Blog
Jewellok is a professional pressure regulator and valve manufacturer and supplier.
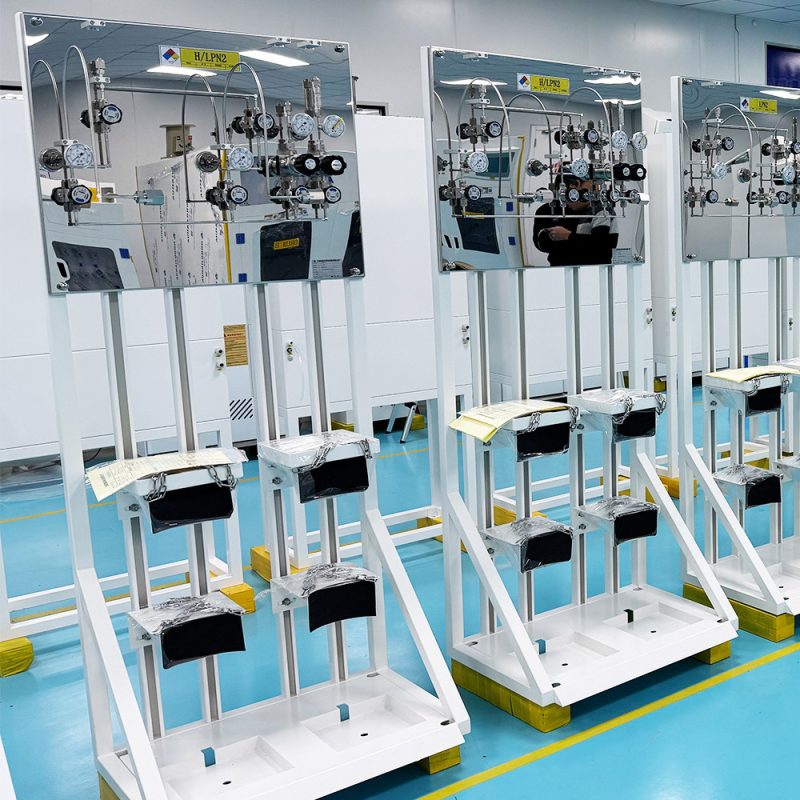
What Is Specialty Gas Semi-automatic Changeover Manifold Systems?
- Pressure Regulator Valve Manufacturer
- gas valve manifold box, High Purity Changeover Manifold, High Purity Changeover Manifold India, High Purity Changeover Manifold Manufacturer, High purity changeover manifolds, High purity changeover manifolds india, High Purity Semi Automatic Changeover Manifold, High Purity Semi-Auto Stainless Steel Changeover Manifolds, Oxygen Nitrogen Helium Argon Gas Changeover Manifold, Semi Automatic and Manual Manifold Systems, semi-automatic changeover manifold system, Semi-automatic Changeover Manifold Systems, Semi-Automatic Manifold Systems, Semi-Automatic Switchover Manifold, semiconductor valve manifold box diaphragm valves, semiconductor valve manifold box gas pressure regulators, Specialty Gas Automatic Changeover Manifolds, Specialty Gas Semi-automatic Changeover Manifold Systems, Stainless Steel Semi-automatic Changeover Gas Manifold, ultra high purity manifolds, valve manifold panels, vmb valve manifold box
- No Comments
What Is Specialty Gas Semi-automatic Changeover Manifold Systems?
Specialty gas semi-automatic changeover manifold systems are critical tools in industries that depend on a continuous and reliable supply of high-purity gases. These systems are designed to ensure uninterrupted gas flow by automatically switching from a depleted gas cylinder to a reserve one, making them invaluable in applications where downtime or gas supply interruptions could have significant consequences. This article provides an in-depth exploration of what specialty gas semi-automatic changeover manifold systems are, how they work, their components, applications, advantages, and how they compare to other types of manifold systems. By the end, readers will have a comprehensive understanding of these systems and their importance in various industries.
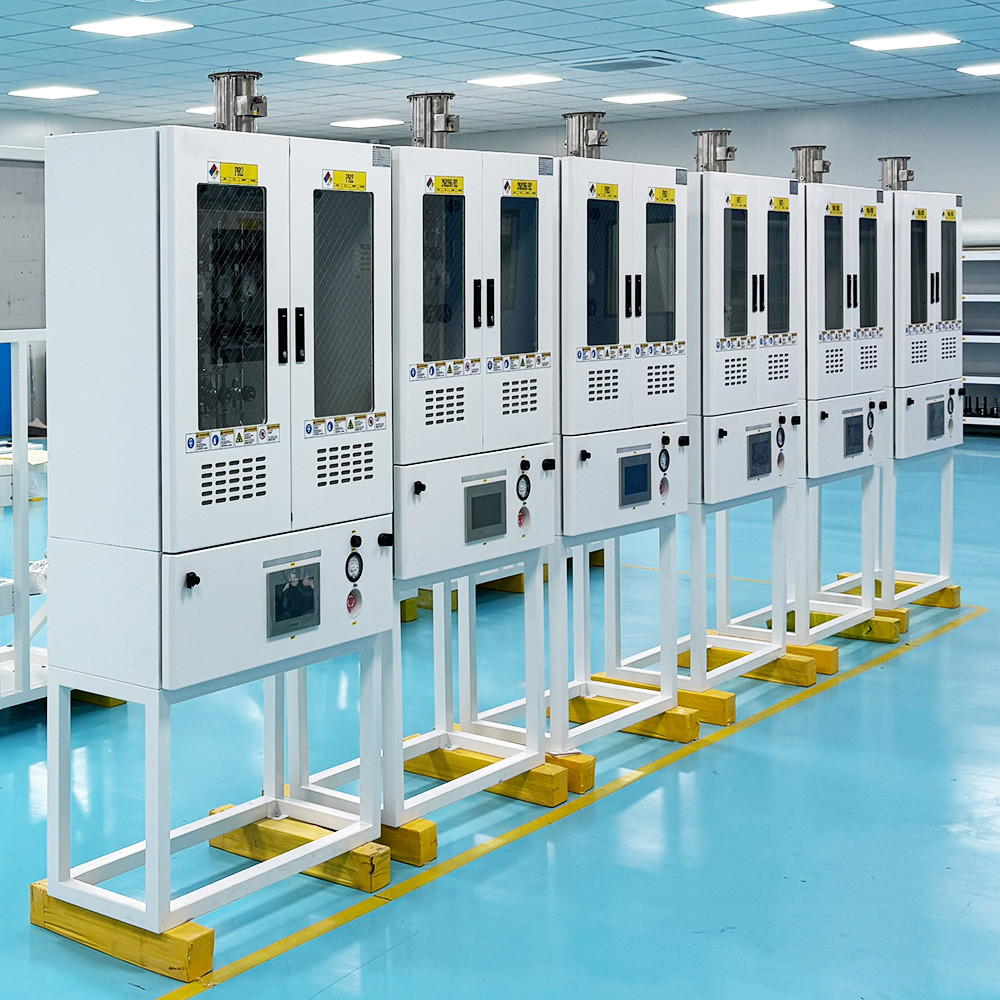
Understanding Specialty Gases
To grasp the significance of semi-automatic changeover manifold systems, it’s essential to first understand what specialty gases are. Specialty gases are high-purity gases tailored for specific applications where precision, consistency, and cleanliness are paramount. Unlike industrial gases used in bulk for general purposes, specialty gases are often produced to exacting standards, with purity levels exceeding 99.99% in many cases. These gases serve a variety of industries, including:
Analytical Chemistry: Calibration gases like helium or nitrogen are used to ensure the accuracy of instruments such as gas chromatographs and mass spectrometers.
Semiconductor Manufacturing: Ultra-high purity gases like argon or silane are critical for processes such as chemical vapor deposition and etching.
Healthcare: Medical gases, including oxygen and nitrous oxide, must meet strict purity and safety standards for patient care.
Research and Development: Laboratories rely on gases like hydrogen or carbon dioxide for experiments where even trace impurities could skew results.
The high stakes of these applications mean that the delivery systems for specialty gases must maintain gas integrity from the cylinder to the point of use. Any contamination or interruption in supply could compromise processes, damage equipment, or pose safety risks. This is where semi-automatic changeover manifold systems come into play.
The Purpose of Changeover Manifold Systems
Changeover manifold systems are engineered to provide a seamless transition between gas cylinders, ensuring a continuous supply of gas without manual intervention at the moment of depletion. These systems connect multiple gas cylinders—typically organized into a primary bank and a reserve bank—and manage the switchover process when the primary source runs low. This functionality is especially crucial for specialty gases, where interruptions could lead to:
Costly Downtime: In manufacturing, halting production to replace a cylinder can result in significant financial losses.
Compromised Results: In research, a sudden loss of gas could ruin experiments or invalidate data.
Safety Hazards: In healthcare, interruptions in medical gas supply could endanger patients.
There are three primary types of changeover manifold systems:
Manual Systems: Operators must monitor gas levels and physically switch to a reserve cylinder when the primary one is empty. These are simple and affordable but labor-intensive.
Semi-automatic Systems: These automatically switch to a reserve cylinder when the primary one is depleted, though manual action is required to reset the system after refilling. They balance automation and cost.
Fully Automatic Systems: These handle both the switch to the reserve and the return to the primary cylinder automatically, offering maximum convenience but at a higher cost.
Semi-automatic changeover manifold systems are the focus of this article, as they provide a practical middle ground for many industries, combining efficiency with affordability.
How Semi-automatic Changeover Manifold Systems Work
A semi-automatic changeover manifold system is designed to maintain gas flow by switching between cylinder banks with minimal disruption. Here’s a detailed look at how these systems operate:
System Setup
The system typically consists of two banks of cylinders: a primary bank, which is used first, and a reserve bank, which stands ready as a backup. Both banks are connected to the manifold, which regulates the flow of gas to the point of use.
Pressure Monitoring
The manifold is equipped with pressure sensors or regulators that continuously monitor the pressure in the primary bank. These components are calibrated to detect when the gas supply in the primary cylinders drops below a predetermined threshold—usually an indicator that the cylinders are nearly empty.
Automatic Switchover
When the pressure in the primary bank falls below the set level, the system automatically switches to the reserve bank. This switchover is often facilitated by a pressure differential mechanism or a solenoid valve, which redirects gas flow without interrupting the supply. This automation ensures that critical processes can continue seamlessly.
Manual Reset
After the depleted primary cylinders are replaced or refilled, an operator must manually reset the system to prioritize the primary bank again. This step ensures that the reserve bank remains available for future switchovers, maintaining the system’s backup capability. In some designs, an alarm or indicator light alerts operators when the switchover occurs, prompting them to address the depleted cylinders.
This combination of automatic switchover and manual reset distinguishes semi-automatic systems from their fully manual and fully automatic counterparts, offering a practical solution for many users.
Key Components of Semi-automatic Changeover Manifold Systems
The effectiveness of a semi-automatic changeover manifold system relies on its components, each of which plays a vital role in ensuring reliable operation. These include:
Regulators: These devices control the output pressure of the gas, ensuring it remains consistent regardless of cylinder pressure. In semi-automatic systems, regulators also help determine the switchover point.
Valves: Isolation valves allow individual cylinders or banks to be shut off for maintenance, while check valves prevent gas backflow, protecting the system from contamination.
Pressure Gauges: These provide real-time readings of cylinder pressure, enabling operators to monitor gas levels and verify system performance.
Pigtails: Flexible hoses connect the cylinders to the manifold. Material selection (e.g., stainless steel for corrosive gases, brass for inert gases) is critical to prevent reactions with the gas.
Purge Valves: These allow the system to be flushed with an inert gas to remove contaminants or residual gas before switching cylinders, preserving gas purity.
Alarms or Indicators: Optional features like audible alarms or LED lights notify operators when a switchover occurs or when maintenance is needed.
The choice of materials for these components is tailored to the specific gas being handled. For instance, corrosive gases like chlorine require stainless steel, while oxygen systems may need grease-free components to prevent combustion risks. This customization ensures that the system maintains the purity and safety of specialty gases.
Applications of Semi-automatic Changeover Manifold Systems
Semi-automatic changeover manifold systems are widely used across industries where a consistent supply of specialty gases is non-negotiable. Some key applications include:
Healthcare
Hospitals rely on these systems to deliver medical gases like oxygen and nitrous oxide to operating rooms, intensive care units, and patient wards. An interruption in supply could be life-threatening, making the automatic switchover feature critical.
Laboratories
Research and analytical labs use specialty gases for experiments and instrument calibration. A sudden loss of gas could damage equipment or invalidate results, so semi-automatic manifolds provide peace of mind.
Semiconductor Manufacturing
The production of microchips requires ultra-high purity gases delivered with precision. Semi-automatic systems ensure that gas flow remains steady during processes like etching and deposition, where interruptions could ruin entire batches.
Industrial Manufacturing
Industries such as welding, chemical processing, and food packaging use specialty gases for various applications. Semi-automatic manifolds minimize downtime, keeping production lines running smoothly.
In each case, the ability to switch to a reserve cylinder without halting operations enhances efficiency and safety, making these systems indispensable.
Advantages of Semi-automatic Changeover Manifold Systems
Semi-automatic changeover manifold systems offer several benefits that make them a popular choice for handling specialty gases:
Cost-Effectiveness: They are less expensive than fully automatic systems, both in terms of initial purchase and ongoing maintenance, while still providing automation benefits.
Uninterrupted Supply: The automatic switchover eliminates downtime, protecting processes that rely on continuous gas flow.
User-Friendly Operation: With minimal manual intervention required—only for resetting or cylinder replacement—these systems are easy to manage.
Enhanced Safety: By reducing the risk of supply failure and incorporating features like purge valves and alarms, they improve safety for operators and processes.
Versatility: These systems can be adapted to handle a wide range of specialty gases and cylinder configurations, meeting diverse industry needs.
These advantages make semi-automatic systems an attractive option for organizations seeking reliability without the complexity or cost of full automation.
Comparing Semi-automatic Systems to Alternatives
To fully understand the value of semi-automatic changeover manifold systems, it’s helpful to compare them with manual and fully automatic systems:
Manual Changeover Systems
Pros: Low cost, straightforward design.
Cons: Requires constant monitoring, higher risk of human error and downtime.
Ideal For: Small operations with non-critical gas needs and limited budgets.
Semi-automatic Changeover Systems
Pros: Automatic switchover, reduced oversight, affordable compared to full automation.
Cons: Manual reset required after cylinder replacement.
Ideal For: Medium to large operations where downtime is costly but full automation isn’t justified.
Fully Automatic Changeover Systems
Pros: Hands-free operation, automatic switchover and reset.
Cons: Higher cost, more complex maintenance.
Ideal For: Large-scale or high-stakes applications where minimal human involvement is critical.
For many users, semi-automatic systems strike the perfect balance, offering significant automation benefits at a reasonable price point.
Installation and Maintenance Considerations
The performance and safety of semi-automatic changeover manifold systems depend on proper installation and regular maintenance.
Installation
Professional Setup: Systems should be installed by trained technicians to ensure leak-tight connections and correct configuration for the gas type.
Safety Measures: Cylinders must be securely restrained, and additional precautions (e.g., ventilation for flammable gases) may be needed.
Customization: The system must be tailored to the specific gas and application, with appropriate materials and pressure settings.
Maintenance
Leak Checks: Regular inspections prevent gas loss and safety hazards.
Component Care: Regulators, valves, and gauges should be serviced periodically to maintain functionality.
Operator Training: Staff should be educated on system operation and troubleshooting to address issues promptly.
Adhering to these practices ensures that the system operates reliably over its lifespan, protecting both the gas supply and the personnel who rely on it.
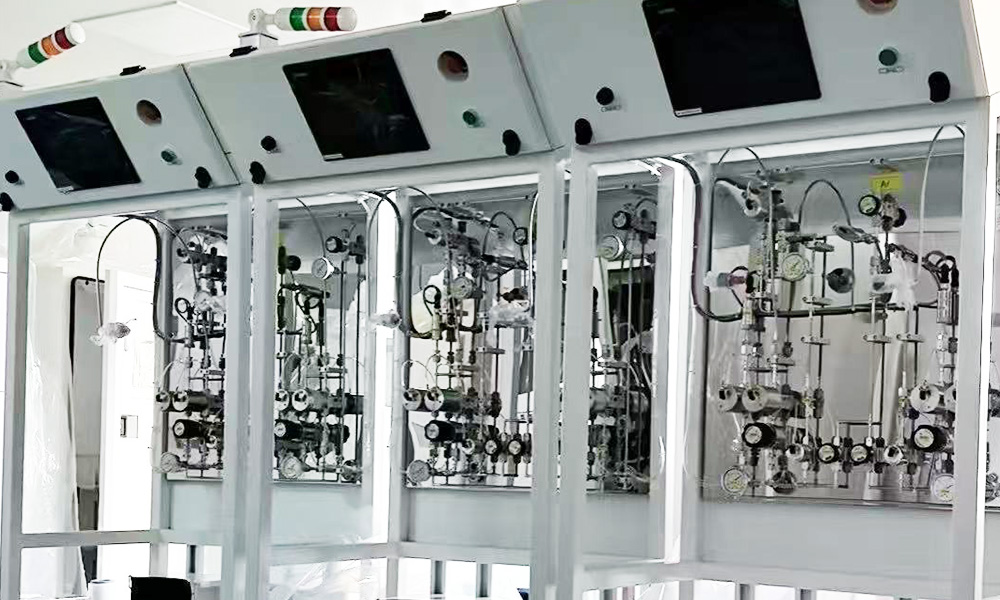
Conclusion
Specialty gas semi-automatic changeover manifold systems are essential for industries that require a steady, high-purity gas supply. By automatically switching to a reserve cylinder when the primary one runs low, these systems prevent interruptions that could disrupt critical processes, compromise safety, or incur significant costs. While they require some manual oversight, their blend of automation, affordability, and versatility makes them a practical choice for applications ranging from healthcare to semiconductor manufacturing.
As industries continue to depend on specialty gases for innovation and productivity, semi-automatic changeover manifold systems will remain a cornerstone of gas delivery infrastructure. By understanding their functionality, components, and benefits, organizations can make informed decisions about integrating these systems into their operations, ensuring both efficiency and reliability in their gas management practices.
For more about what is specialty gas semi-automatic changeover manifold systems, you can pay a visit to Jewellok at https://www.jewellok.com/best-top-10-high-purity-semi-auto-stainless-steel-changeover-manifolds-manufacturers-in-india/ for more info.
Recent Posts
High-Pressure Hydraulic Needle Valve
Pneumatic Actuated Ball Valve
Industrial Diaphragm Valve
Needle Valve 10000 psi Manufacturers
Tags
Recommended Products
-
High Pressure High-Purity Welded Check Valves And Low Cracking Pressure Check Valve JCV1 Series
-
Stainless Steel Ultra High Purity (UHP) High Pressure Manual Diaphragm Valve
-
775L Bulkhead Reducing Union | Stainless Steel High Purity Double Ferrule Bulkhead Reducing Unions
-
VMB Valve Manifold Panels And Boxes High Purity Configurable Systems JW-200-VMB & JW-100-VMB
-
764LR Stainless Steel 316 Reducing Tee UHP Fitting Automatic Buttweld Reducing Tee
-
Stainless Steel 316L Single Stage Regulator Pressure Control Panels JSP-1E Series For Semiconductor Fluid Control
-
Line And Panel Mounting Adjustable Low Pressure Propane And Nitrogen Pressure Regulator JSR-3L & JSR-3LP Series
-
7108L Cylinder Cap Connectors For Ultra High Purity Gases