Instrumentation fittings and valves for laboratory
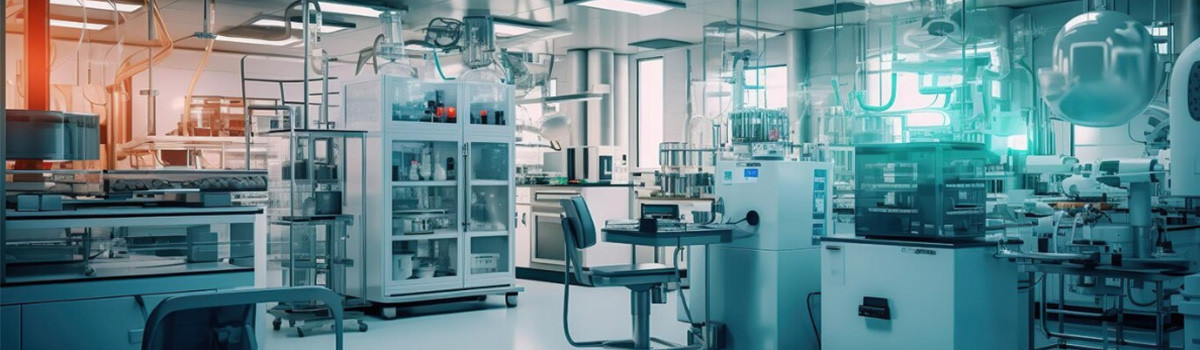
Why instrumentation fittings and valves for laboratory Is Essential for Optimized Laboratory Operations.
Imagine yourself as a laboratory technician. As you perform your intended testing or analysis, you approach a point of use for a particular gas. You activate a mechanism to obtain the gas you need—but flow and pressure are lower than they are supposed to be.
This is a problem, potentially for multiple reasons:
*The accuracy of the test you are performing can’t necessarily be relied upon, and you may not be able to move forward with it at all
*Troubleshooting to find the source of the problem will take time and money, and it’s hard to say how much
*If a leak is causing these flow issues, there could also be a related safety issue, making this a top priority to fix
No matter where your lab is located—within a research facility, a chemical refinery, or some other industrial plant—these rippling consequences can have a significant impact on local operations. They also showcase the importance of maintaining consistent and reliable gas delivery to critical points of use.
All Gases Pose a Potential Risk
Certain gases carry more risk potential than others. Poisonous or noxious gases—ammonia, sulfur dioxide, and hydrogen chloride for examples—pose an immediate risk to laboratory safety in the event of a leak. Direct exposure to any of these gases is highly dangerous and should clearly be avoided.
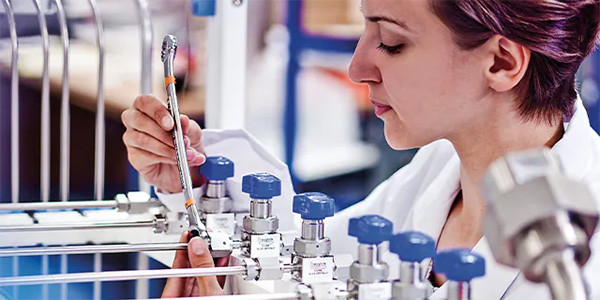
High-purity gas valve fittings are also widely used in laboratories, mainly involving the following aspects:
1. Laboratory gas cylinders: High-purity gas valve fittings are used to connect gas cylinders and experimental equipment to ensure the high purity and safety of the gas. These valve fittings need to have high sealing, corrosion resistance and high pressure resistance to ensure the purity and safety of the gas.
2. Gas pipeline system: The gas pipeline system in the laboratory is an important part of the experimental equipment. High-purity gas valve fittings are mainly used to control the flow of gas, such as gas cylinders, pressure reducing valves, flow meters, etc. These valve fittings need to have high purity, high sealing, corrosion resistance and other characteristics to ensure the normal progress of the experiment and the purity of the gas.
3. Special gas treatment: In the laboratory, some special gases need special treatment, such as chlorine, ammonia, etc. High-purity gas valve fittings are used to treat these special gases. They need to have excellent corrosion resistance and high purity characteristics to prevent the entry of pollutants and ensure the purity and quality of the gas.
4. Vacuum system: In the laboratory, the vacuum system is used for the operation and control of experimental equipment. High-purity gas valve fittings are used to control the gas flow and pressure of the vacuum system. They need to have high sealing and corrosion resistance to ensure the normal operation and stability of the system.
In general, high-purity gas valve fittings are widely used in laboratories and can meet the requirements of experimental equipment for high purity and high safety of gas. In specific applications, it is necessary to select suitable high-purity gas valve fittings according to the requirements of experimental equipment and processes, and ensure that they have the characteristics of corrosion resistance, high pressure resistance, and good sealing.
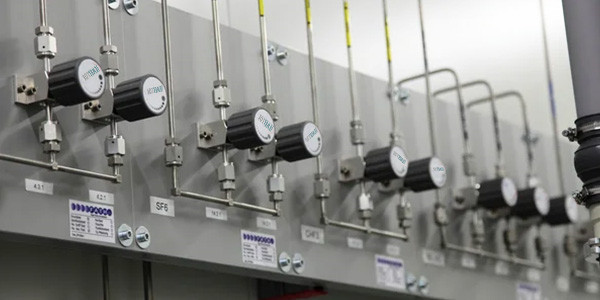
Interested in learning more about how to enhance your system or how a professional evaluation can bring benefits to your laboratory? Get in touch with our gas distribution specialists to discuss your challenges and to gain insights on how to build reliable gas delivery systems.
It is important to remember, though, that all gases have the potential to create a safety risk if they escape your distribution system. Oxygen or hydrogen, for example, can become highly combustible if enough of it enters your lab or plant atmosphere. Nitrogen escaping from a system can displace atmospheric oxygen levels, creating a potentially hazardous environment in a closed space. Heavier gases like propane and butane can drop into and collect within lower-level cavities and enclosures, creating explosion risks.
Because gases like oxygen, hydrogen, and nitrogen are not always treated with the same levels of caution as noxious gases, it is possible for a lab to be experiencing small leaks without operators even realizing they are occurring. This poses a safety hazard, first and foremost. But escaping gas is also wasted gas and can come at a significant monetary cost.
How do you ensure all gases are treated with the appropriate level of caution in your facility? A professional evaluation is an effective way to identify unknown leaks, as well as to uncover distribution system design strategies that can help maximize safety. And the most important point is make sure the fittings and valves for laboratory gas working well.
Pressure and Flow: Critical for Your Productivity
While not always indicative of a safety hazard, improper laboratory gas pressure and flow levels can impact your ability to perform lab tasks as efficiently and accurately as possible. For example, lower levels of pressure and flow may limit the number of tests you are able to complete in a given timeframe. They may also compromise the functionality of your testing equipment.
Often, suboptimal pressure and flow levels are rooted in system design inefficiencies. One classic example is system overdesign, where an excessive number of valves or regulators are included to throttle pressure as it travels from the source to the point of use. Sound gas distribution system design incorporates as few valves and regulators as are necessary to meet user demands at the point of use. Remember that “more” does not equate to “better” in all cases.
In the case of overdesign, it is also common for the cost of extra valves or regulators to be offset by selecting smaller gas transfer lines. A combination of extra valves and smaller lines can severely limit the maximum available pressure and flow at the point of use—thereby limiting testing productivity in the lab. In addition, selecting smaller lines upfront will limit the maximum flow of the system, potentially causing problems if your needs change.
Once again, a professional evaluation can be beneficial here. Gas distribution specialists can help identify areas for design improvement, helping you achieve your desired point-of-use requirements without artificially limiting pressure and flow if you need higher levels in the future.