Blog
Jewellok is a professional pressure regulator and valve manufacturer and supplier.
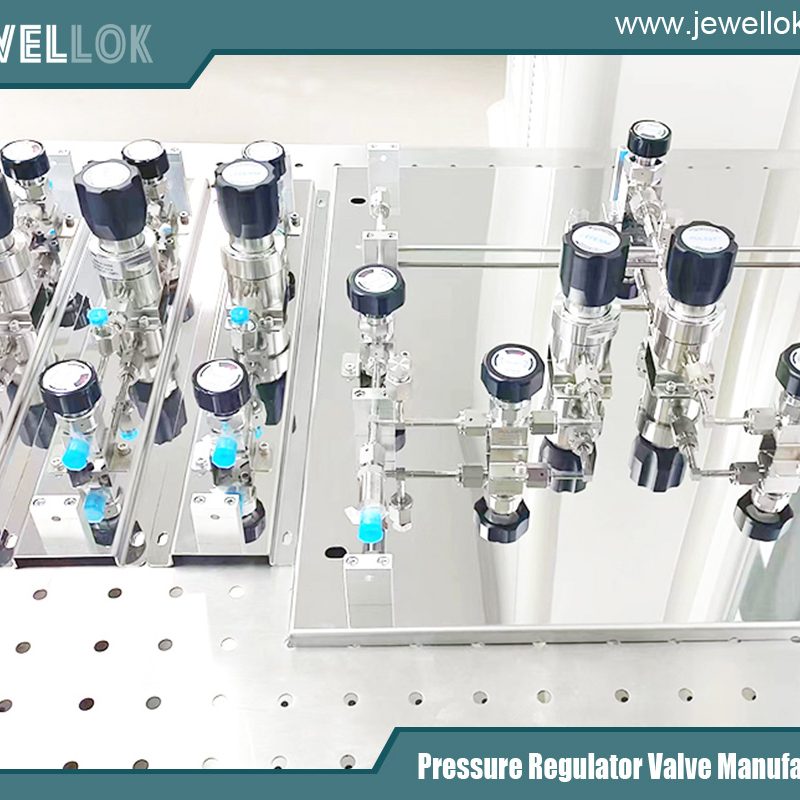
Pressure Relief Valve vs Safety Valve
- Pressure Regulator Valve Manufacturer
- 1 1 2 gas pressure regulator, 1 2 gas regulator, 1/2 gas pressure regulator, 12v electric valve, 2 electric valve, 6mm compression union, adjustable propane pressure regulator, best high purity valves, best high purity valves manufacturers, diaphragm suppliersrelief vs safety valve, electric water valve, gas used in semiconductor chip manufacturing, high pressure argon regulator, high pressure flexible hose pipe, high purity regulator, high purity valve, high purity valves supplier, how a regulator works, how a solenoid works, hydraulic pressure relief valve manufacturers, industrial regulators, lab fittings exporter, pressure regulator, pressure relief valve manufacturer, pressure relief valve vs safety valve, propane pressure regulator valve, relief valve and safety valve difference, relief valve safety valve difference, relief vs safety valve, safety relief valve vs safety valve, safety valve, safety valve and pressure relief valve, safety valve and relief valve, safety valve manufacturer, safety valve vs pressure relief valve, safety valve vs relief valve, semiconductor gas, valve manifold box, water valve timer, what is a flame arrestor
- No Comments
Pressure Relief Valve vs Safety Valve
In any system where pressure plays a critical role—be it a household water heater, an industrial steam boiler, or a complex hydraulic system—maintaining control over that pressure is vital for safety and operational efficiency. Excessive pressure can lead to equipment damage, leaks, or even catastrophic events like explosions. To prevent such outcomes, engineers rely on specialized devices known as pressure relief valves and safety valves. While both are designed to protect systems by releasing excess pressure, they differ in their design, operation, and applications. This article provides a detailed comparison of pressure relief valves and safety valves, exploring their definitions, mechanisms, uses, and the factors that guide their selection and maintenance. By the end, readers will have a clear understanding of how these valves function and when each should be employed.
Definitions and Terminology
To compare pressure relief valves and safety valves effectively, we must first establish clear definitions for each, as terminology can vary across industries and regions.
A pressure relief valve is a device primarily used in systems containing liquids. It is designed to open gradually as the pressure exceeds a predetermined set point, releasing fluid in proportion to the pressure increase. This controlled release reduces the system pressure to a safe level, and the valve closes once the pressure drops below the set point. Pressure relief valves are versatile and widely used in applications such as hydraulic systems, water pipelines, and liquid storage tanks.
In contrast, a safety valve is typically employed in systems handling gases, vapors, or steam. It operates differently by opening fully and rapidly—often with a distinctive “pop” action—when the pressure reaches the set point. This sudden, complete opening allows for a quick discharge of gas or vapor, swiftly reducing pressure to prevent hazards like explosions. Safety valves are essential in applications such as steam boilers, compressed air systems, and gas pipelines.
Adding to the complexity, there’s a hybrid type known as the safety relief valve, which can function as either a safety valve or a relief valve depending on the application. These valves are adaptable, suitable for systems where both liquids and gases may be present or where fluid conditions vary.
For clarity in this article, we’ll use “pressure relief valve” to refer to valves primarily for liquids with proportional opening, and “safety valve” for those designed for gases with rapid, full opening. However, it’s worth noting that in some contexts, “pressure relief valve” is a broader term encompassing both types, a nuance we’ll address as needed.
Design and Operation
Understanding the operational differences between pressure relief valves and safety valves requires examining their internal mechanisms and how they respond to pressure.
Pressure Relief Valve
A typical pressure relief valve consists of a valve seat, a disc or poppet, and a spring. Under normal conditions, the spring presses the disc against the seat, preventing fluid flow. When the system pressure exceeds the spring’s force, the disc lifts, allowing fluid to escape through an outlet. The key feature here is that the lift is proportional to the pressure increase—higher pressure results in a greater opening, but not necessarily a full one. This gradual release stabilizes the system without excessive discharge. As the pressure decreases, the spring reseats the disc, closing the valve.
Safety Valve
Safety valves share a similar basic structure but are engineered for rapid action. They often include a huddling chamber or an additional lifting area. When the pressure reaches the set point and the disc begins to lift, this chamber amplifies the lifting force, causing the valve to “pop” open fully. This design ensures a large volume of gas or vapor escapes quickly, reducing pressure almost instantly. Once the pressure falls to a safe level, the valve closes abruptly. This pop action is critical in gas systems where delayed response could be dangerous.
For example, in a steam boiler, a safety valve might pop open to release excess steam if the pressure climbs too high, preventing a rupture. Conversely, a pressure relief valve on a hydraulic system would open just enough to relieve excess liquid pressure, maintaining system stability.
Applications
The choice between a pressure relief valve and a safety valve hinges on the system’s fluid type and the risks involved.
Pressure Relief Valve Applications
Pressure relief valves excel in liquid-based systems where a controlled release suffices. Common uses include:
- Hydraulic Systems: In machinery, they prevent damage from pressure spikes.
- Water Supply Lines: They protect pipes from bursting due to thermal expansion.
- Liquid Storage Tanks: They maintain safe pressure levels in chemical or fuel storage.
- Hot Water Heaters: They release excess pressure from heated water.
Safety Valve Applications
Safety valves are indispensable in gas or vapor systems requiring rapid pressure reduction. Typical applications include:
- Steam Boilers: In power plants, they prevent explosions by releasing steam.
- Compressed Air Systems: In manufacturing, they ensure safe operation of pneumatic tools.
- Gas Pipelines: They protect against over pressurization in transport systems.
- Refrigeration Systems: They manage vapor pressure in cooling units.
Safety Relief Valve Applications
Safety relief valves bridge the gap, used in mixed or variable systems. For instance, in a chemical plant, they might handle both liquid reactants and gaseous byproducts, adapting to the process stage.
Selection Criteria
Choosing the appropriate valve involves evaluating several factors to ensure safety and efficiency:
- Fluid Type: Liquids call for pressure relief valves, gases for safety valves, and mixed systems may need safety relief valves.
- Set Pressure: The valve must open at a pressure below the system’s maximum allowable limit.
- Discharge Capacity: It should handle the maximum expected flow rate during overpressure.
- Temperature: Materials must withstand the system’s operating temperature.
- Back Pressure: Downstream pressure can affect valve performance, especially in safety valves.
- Regulatory Compliance: Standards like ASME or ISO dictate design and use.
Incorrect selection can lead to inadequate protection or system inefficiency, underscoring the need for careful analysis.
Standards and Regulations
Both valve types are governed by strict standards to ensure reliability. In the United States, the ASME Boiler and Pressure Vessel Code (Section VIII) outlines requirements for design, testing, and installation. The American Petroleum Institute (API) provides standards like API 520 for oil and gas applications. Internationally, ISO 4126 specifies performance criteria for safety valves. Compliance is often legally mandated and ensures that valves perform as expected under pressure, protecting both people and property.
Maintenance and Testing
Regular maintenance is essential to keep these valves operational. Over time, corrosion, debris, or spring fatigue can impair performance. Best practices include:
- Visual Inspections: Check for wear, leaks, or damage.
- Functional Testing: Verify opening at the set pressure, often using a test bench.
- Cleaning/Replacement: Remove buildup or replace worn parts.
- Documentation: Log maintenance for audits and compliance.
Testing frequency varies—annual checks are common, but critical systems may require more frequent inspection per regulations or manufacturer guidelines.
Case Studies
Real-world examples illustrate the stakes involved:
- Boiler Failure (2015): A manufacturing plant suffered a boiler explosion when a neglected safety valve, untested for years, corroded and failed to open. The incident highlighted the need for regular maintenance.
- Hydraulic Success: In an automotive factory, a pressure relief valve on a hydraulic press released excess pressure from a pump malfunction, preventing a rupture and maintaining production—a testament to proper valve selection.
- These cases emphasize that effective valve use can prevent disasters or save resources.
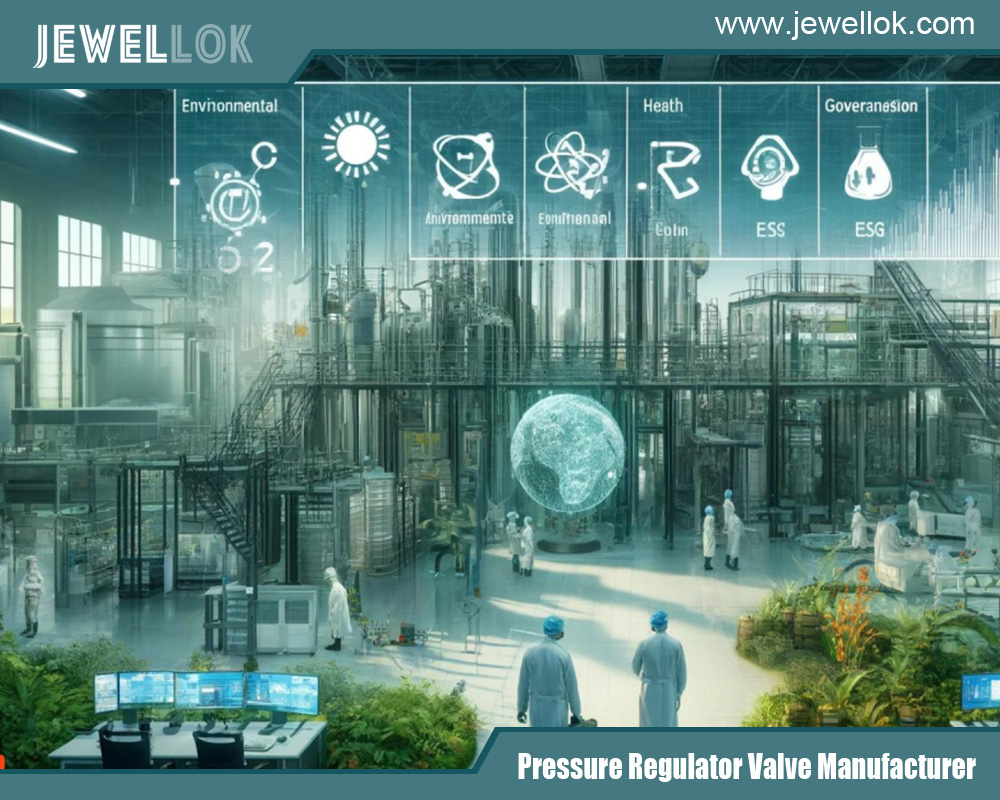
Conclusion
Pressure relief valves and safety valves, while sharing the goal of overpressure protection, serve distinct purposes. Pressure relief valves manage liquid systems with gradual, proportional relief, while safety valves handle gases with rapid, full discharge. The hybrid safety relief valve offers flexibility for mixed applications. Selecting the right valve requires understanding fluid types, system demands, and regulatory standards, followed by diligent maintenance to ensure performance.
These devices are more than engineering components—they’re safeguards for lives, equipment, and operations. By mastering their differences and applications, engineers and operators can enhance system safety and reliability, preventing the costly consequences of overpressure.
For more about the pressure relief valve vs safety valve, you can pay a visit to Jewellok at https://www.jewellok.com/ for more info.
Recent Posts
Pressure Relief Valve vs Safety Valve
How a Gas Pressure Regulator Works
Adjustable Low Pressure Propane Regulator
Tags
Recommended Products
-
High Purity High Pressure Stainless Steel Needle Valve Natural Gas Flow Control Valve JNV Series
-
Ultra High Purity Pressure Gauge For Laboratory And Semiconductor JR Series
-
316L Stainless Steel Tube Butt Weld Reducing Fittings Union Reducer RW Series Ultrahigh Purity Process
-
765L Stainless Steel Union Elbow Reducing High Purity Fitting Tubing Extension Tubing Connection
-
7102L Stainless Steel 316L SS Union Cross Ultra High Purity Long Arm Union Elbow Tee Cross Butt Weld Fittings
-
739LF High Purity Female Adapter Tube To Pipe Fittings And Connectors
-
Semi Automatic Gas Cabinet Gas Panels High Purity Gas Delivery Systems JW-200-GC
-
7108L Cylinder Cap Connectors For Ultra High Purity Gases