Blog
Jewellok is a professional pressure regulator and valve manufacturer and supplier.
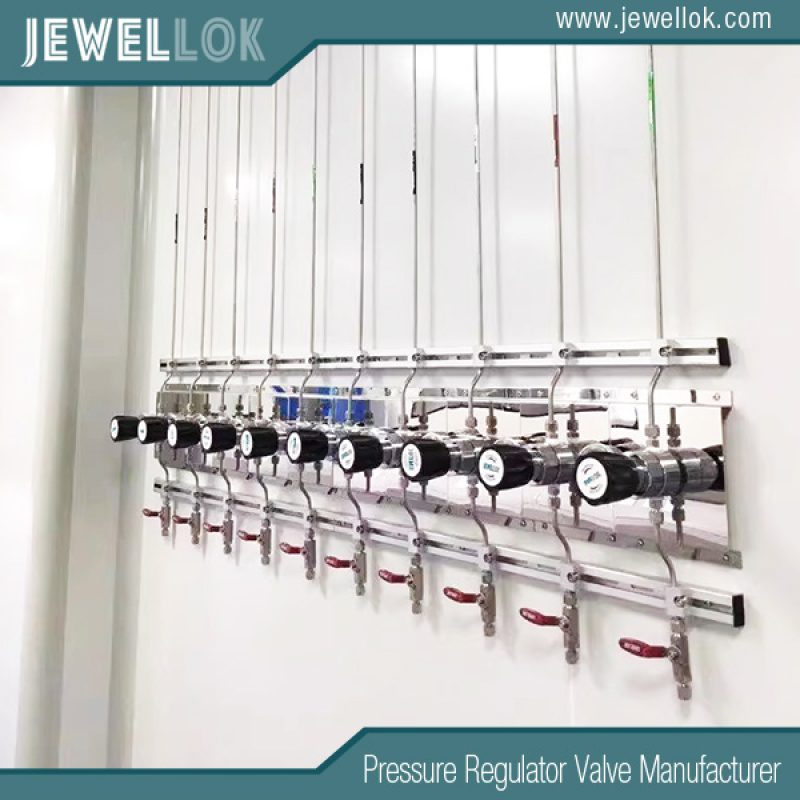
High-Pressure Hydraulic Needle Valve
- Pressure Regulator Valve Manufacturer
- 2 inch irrigation valve, argon hose connector, back pressure regulator manufacturers, best 316 SS ball valves manufacturer, best gas regulator in philippines, Best high purity gas valve manufacturers in china, Best High-Pressure Ball Valve Manufacturer, best high-pressure gas regulators for industrial use, best high-pressure hydraulic needle valve, Best Hydraulic Fitting Manufacturer Supplier China, Best lpg gas regulator manufacturers in india, best needle valve 10000 psi manufacturers, best pneumatic actuated ball valve, best specialty gas cabinet companies in taiwan, Best specialty gas regulator manufacturers, Best specialty gas regulators manufacturer in india, gas pipeline valve, gas semiconductor, high pressure hydraulic needle valve manufacturer, high pressure hydraulic needle valve supplier, high purity regulators, high purity stainless steel gas fittings, high purity valves, high purity valves manufacturers, high purity valves supplier, high-pressure hydraulic needle valve, high-pressure hydraulic needle valve market, laboratory gas valves, low-pressure valve, low-pressure valve manufacturers, regulator valve alibaba international market, relief valve safety valve difference, timed water valve, two stage pressure regulator
- No Comments
High-Pressure Hydraulic Needle Valve
High-pressure hydraulic needle valves are vital components in hydraulic systems, designed to regulate fluid flow with precision under extreme pressure conditions, often exceeding 10,000 pounds per square inch (psi). These valves play a critical role in industries requiring meticulous control over fluid dynamics, such as oil and gas, aerospace, chemical processing, and industrial manufacturing. Unlike standard valves, needle valves feature a small port and a threaded, needle-like plunger, allowing fine adjustments to flow rates, though they are typically suited for low-flow applications.
In high-pressure environments, these valves must not only provide accurate regulation but also endure significant forces without compromising safety or performance. This article explores the world of high-pressure hydraulic needle valve manufacturers, highlighting their importance, key players in the industry, materials and design features, applications, selection criteria, maintenance practices, emerging trends, and challenges. By understanding these aspects, readers can appreciate the engineering excellence behind these components and the expertise of the manufacturers producing them.
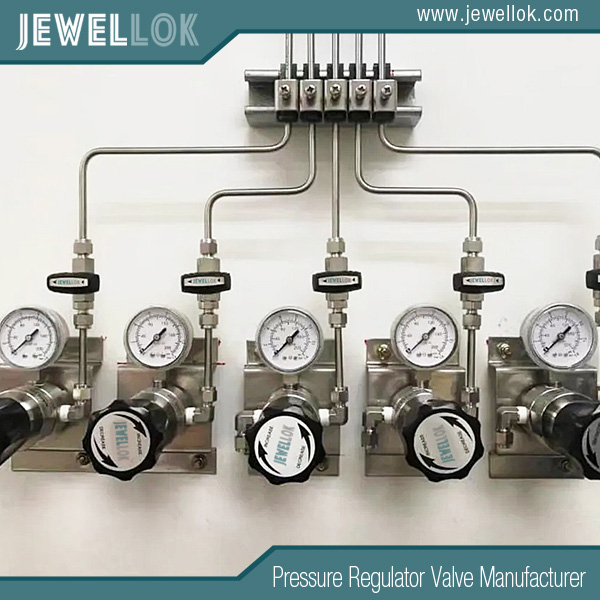
The Role and Importance of High-Pressure Hydraulic Needle Valves
High-pressure hydraulic systems power a wide range of industrial applications, from heavy machinery to energy transmission. Needle valves are indispensable in these systems for several reasons:
- Precision Flow Control: They enable operators to fine-tune fluid flow, critical for controlling the speed and movement of hydraulic actuators.
- Pressure Regulation: By adjusting flow, these valves help maintain or modify system pressure, ensuring operational stability.
- System Isolation: They allow sections of a hydraulic circuit to be isolated for maintenance or safety purposes.
- Enhanced Safety: Accurate flow control prevents over-pressurization, reducing the risk of equipment failure or accidents.
Given their critical functions, the quality of high-pressure hydraulic needle valves directly impacts system efficiency and safety. Reputable manufacturers are essential in delivering products that meet these demanding requirements.
Leading Manufacturers of High-Pressure Hydraulic Needle Valves
The market for high-pressure hydraulic needle valves features several standout manufacturers known for their quality, innovation, and reliability. Below are profiles of some industry leaders:
- Parker Hannifin
- Overview: Founded in 1917, Parker Hannifin is a global leader in motion and control technologies, renowned for its hydraulic components.
- Products: Their needle valves handle pressures up to 15,000 psi, available in stainless steel, brass, and various configurations.
- Quality Standards: Certified to ISO 9001, Parker ensures rigorous testing and compliance with industry benchmarks.
- Global Reach: With facilities and support networks worldwide, Parker excels in customer service and product availability.
- Swagelok
- Overview: Since 1947, Swagelok has been a trusted name in fluid system solutions, emphasizing precision engineering.
- Products: Swagelok offers needle valves rated up to 10,000 psi, crafted from stainless steel and alloys, with manual and actuated options.
- Innovation: Heavy investment in R&D keeps their products at the forefront of technology.
- Support: Extensive technical resources and training enhance customer experience.
- Hy-Lok
- Overview: A South Korean company with a strong global presence, Hy-Lok specializes in fluid control products.
- Products: Their high-pressure needle valves, rated up to 10,000 psi, are made from stainless steel and carbon steel.
- Certifications: ISO 9001 compliance ensures consistent quality and reliability.
- Accessibility: A worldwide distributor network makes Hy-Lok products readily available.
- NOSHOK
- Overview: Based in the U.S., NOSHOK is known for its measurement and control solutions, including valves.
- Products: NOSHOK’s needle valves support pressures up to 10,000 psi, with customizable options.
- Quality Assurance: Backed by a three-year warranty, their products undergo strict quality checks.
- Service: Responsive customer support is a hallmark of NOSHOK’s operations.
These manufacturers exemplify excellence in the field, offering diverse solutions tailored to high-pressure hydraulic needs.
Materials Used in High-Pressure Hydraulic Needle Valves
The durability and performance of these valves hinge on the materials used in their construction. Common materials include:
- Stainless Steel: Preferred for its strength and corrosion resistance, especially grades like 316, ideal for harsh environments.
- Brass: Used in less demanding applications, offering good corrosion resistance at a lower cost, though less robust than steel.
- Carbon Steel: Chosen for high-strength needs, though it requires protection against corrosion.
- Exotic Alloys: Materials like Monel, Inconel, or Hastelloy are used in highly corrosive or extreme conditions.
Material selection depends on the fluid type, temperature, and environmental factors, with manufacturers providing guidance to ensure compatibility.
Design Features of High-Pressure Hydraulic Needle Valves
To perform under extreme conditions, these valves incorporate specialized design elements:
- Reinforced Bodies: Thicker, stronger bodies resist pressure-induced deformation.
- High-Strength Stems: Hardened stems prevent bending or failure during operation.
- Advanced Seals: Metal-to-metal seats or high-performance elastomers ensure leak-free performance.
- Mounting Options: Panel-mount designs facilitate integration into equipment.
- Safety Features: Locking mechanisms prevent unintended adjustments.
- Operation Enhancements: Ergonomic handles or actuators (pneumatic/electric) improve usability and automation.
These features collectively ensure reliability and precision in high-pressure applications.
Applications Across Industries
High-pressure hydraulic needle valves serve diverse industries, each with specific needs:
- Oil and Gas: Used in drilling, pipelines, and refining to control hydraulic fluids under pressure.
- Aerospace: Critical in aircraft hydraulic systems for landing gear, flight controls, and fuel management.
- Chemical Processing: Manage aggressive chemicals in high-pressure reactors and processing units.
- Power Generation: Regulate hydraulic fluids in turbines, cooling systems, and boilers.
- Manufacturing: Essential in hydraulic presses, molding machines, and precision equipment.
Each application demands valves that meet industry-specific standards, such as API or ASME.
Selection Criteria for High-Pressure Hydraulic Needle Valves
Selecting the right valve requires evaluating several factors:
- Pressure Rating: Must exceed the system’s maximum pressure with a safety margin.
- Flow Rate: Match the valve’s flow coefficient (Cv) to application needs, noting low-flow limitations.
- Material Compatibility: Ensure resistance to the fluid’s chemical properties.
- Temperature Range: Verify performance across operating temperatures.
- Connection Type: Options like threaded (NPT, BSP), flanged, or welded must suit the system.
- Manufacturer Reputation: Opt for trusted brands with proven quality and support.
- Certifications: Industry-specific standards may be required.
A thorough assessment ensures the valve meets operational demands effectively.
Maintenance and Servicing
Regular maintenance extends valve life and reliability:
- Inspection: Check for leaks, wear, or corrosion periodically.
- Cleaning: Remove debris that could impair function.
- Lubrication: Apply to moving parts as needed, per manufacturer guidelines.
- Seal Replacement: Replace worn seals with OEM parts to maintain integrity.
- Testing: Verify performance post-maintenance under operating conditions.
Manufacturers often provide detailed manuals or servicing support to guide users.
Trends and Innovations in the Industry
The industry is advancing with technology and market shifts:
- Higher Pressure Capabilities: Valves now handle up to 20,000 psi for extreme applications.
- Enhanced Flow Control: Design improvements offer finer regulation.
- Automation: Pneumatic and electric actuators enable remote operation.
- Smart Technology: Sensors and IoT integration allow monitoring and predictive maintenance.
- Sustainability: Eco-friendly materials and processes are gaining traction.
These trends enhance performance, safety, and efficiency across applications.
Challenges Faced by Manufacturers
Producing these valves involves overcoming significant hurdles:
- Stringent Standards: Compliance with rigorous quality and safety regulations is mandatory.
- Material Challenges: Selecting suitable materials for diverse conditions is complex.
- Competitive Market: Balancing cost, quality, and innovation in a global landscape is demanding.
- Customization Needs: Tailored solutions require additional resources and time.
- Supply Chain: Securing high-quality materials amid disruptions poses risks.
Manufacturers address these through R&D, advanced manufacturing, and strong supply networks.
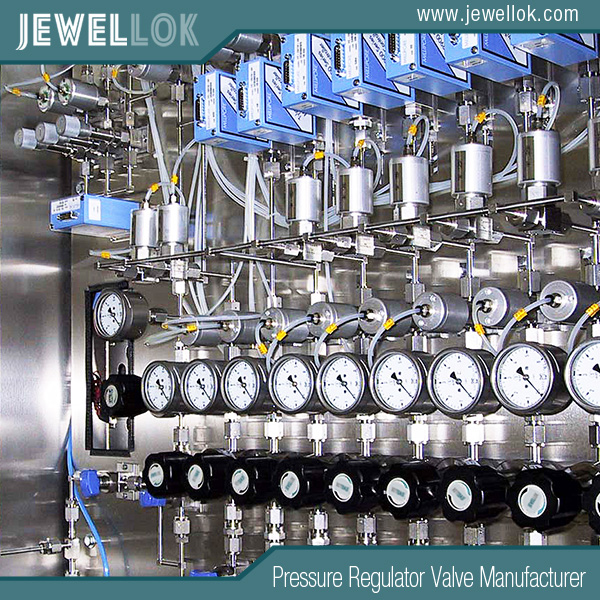
Conclusion
High-pressure hydraulic needle valves are critical for precision and safety in hydraulic systems across multiple industries. Manufacturers like Parker Hannifin, Swagelok, Hy-Lok, and NOSHOK lead the way with high-quality, innovative products supported by robust customer service. By leveraging advanced materials, thoughtful design, and emerging technologies, these companies meet the evolving needs of their clients.
Understanding the valves’ applications, selection criteria, and maintenance needs empowers users to optimize performance. As the industry progresses with higher pressure ratings, automation, and smart features, the role of reputable manufacturers becomes even more vital. Choosing a trusted high-pressure hydraulic needle valve manufacturer ensures reliability, efficiency, and safety in the most demanding environments.
For more about the best high-pressure hydraulic needle valve, you can pay a visit to Jewellok at https://www.jewellok.com/ for more info.
Recent Posts
Pneumatic Actuated Ball Valve
Industrial Diaphragm Valve
Needle Valve 10000 psi Manufacturers
Best High-Pressure Gas Regulators For Industrial Use
Tags
Recommended Products
-
Fully Automated Gas Cabinet For Precise UHP Gas Delivery And High Purity Gas Delivery Systems JW-300-GC
-
775L Bulkhead Reducing Union | Stainless Steel High Purity Double Ferrule Bulkhead Reducing Unions
-
JF Series In-Line Gas Filters | High Purity High Precision High Flow Semiconductor Gas Filter Gas Filtration & Purification
-
FT-BOX JW-FTB-C Valve Manifold Panels And Boxes With High Purity Configurable Systems
-
763L Stainless Steel High Purity Pressure Reducing Union Fittings And Tubing Pressure Reducing Valve Adjustment
-
7121L Plug High Purity Plug Fitting And Blanking Plug
-
Stainless Steel High-Purity High Temperature Metal Seated Ball Valves JBV3 Series
-
High Pressure High Temperature Pneumatic Ultrahigh Purity Stainless Steel Diaphragm Valves