Blog
Jewellok is a professional pressure regulator and valve manufacturer and supplier.
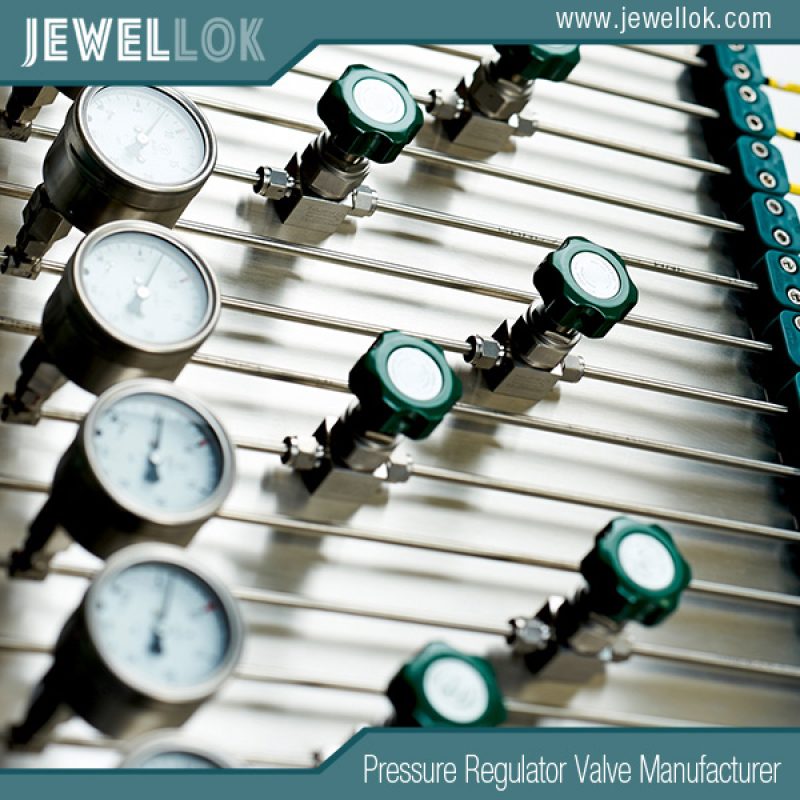
High Pressure Needle Valve : Precision Engineering for Demanding Applications
- Pressure Regulator Valve Manufacturer
- 2 inch irrigation solenoid valve, adjustable propane regulator, adjusting propane regulator, argon hose fitting, best high pressure needle valve, characteristics of pressure, china high pressure needle valve manufacturer, China High Pressure Needle Valve Suppliers, china stainless steel high pressure needle valve, china stainless steel high pressure needle valve manufacturer, China Top 10 High Pressure Needle Valve, chinese propane gas cylinder, gas used in semiconductor manufacturing, high pressure needle valve, high pressure needle valve factory, high pressure needle valve manufacturer, high pressure needle valve manufacturer in china, High Pressure Needle Valve Manufacturer in India, high pressure needle valve manufacturers, High Pressure Needle Valve Stainless Steel, High Pressure Needle Valve Stainless Steel China, high pressure needle valve supplier, High Pressure Needle Valves, High Pressure Needle Valves China, High Pressure Needle Valves Manufacturer, low pressure regulator, pressure gauge manufacturers, pressure relief valve vs safety relief valve, quick connect valve, relief vs safety valve, safety relief valve vs pressure relief valve, solenoid water valve, stainless pressure regulator, Ultra High Pressure Needle Valve, what is a gas pressure regulator
- No Comments
High Pressure Needle Valve : Precision Engineering for Demanding Applications
In the complex world of industrial fluid control, high-pressure needle valves are unsung heroes, ensuring safety and efficiency under some of the most extreme conditions imaginable. These specialized valves are engineered to regulate the flow of liquids and gases in systems where pressures can exceed 10,000 pounds per square inch (psi). From oil rigs deep beneath the ocean to chemical plants processing volatile substances, high-pressure needle valves are vital components that keep operations running smoothly. This article explores the intricate process of manufacturing these valves, delving into the precision engineering, materials, applications, challenges, and innovations that define this critical industry. By understanding the expertise behind high-pressure needle valve production, we gain insight into the craftsmanship that supports some of the world’s most demanding applications.
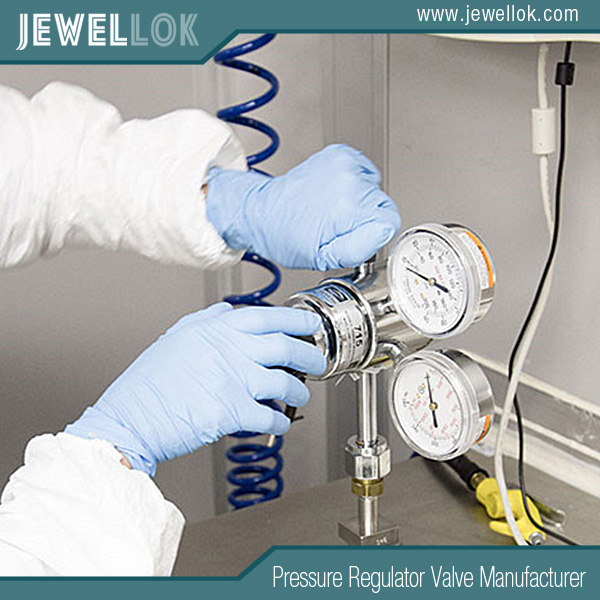
Introduction to High-Pressure Needle Valves
Valves are essential to industrial systems, acting as gatekeepers that control the movement of fluids with precision and reliability. Among the many types of valves, high-pressure needle valves stand out for their ability to thrive in environments where others would fail. Characterized by a small port and a threaded, needle-like plunger, these valves allow for fine-tuned adjustments to flow rates, making them ideal for applications requiring exact control.
The significance of high-pressure needle valves lies in their role as guardians of safety and performance. In industries where a single failure could lead to catastrophic consequences—think oil and gas exploration or hydraulic machinery—these valves prevent over-pressurization, isolate system sections for maintenance, and ensure consistent operation. As industrial processes push the boundaries of pressure and temperature, the demand for reliable, high-quality needle valves continues to rise, placing manufacturers at the heart of this essential supply chain.
The Manufacturing Process: Precision at Every Step
Creating a high-pressure needle valve is a feat of precision engineering, requiring meticulous attention to detail at every stage. The journey begins with design, where engineers leverage advanced software to model the valve’s performance under extreme conditions. This step is crucial for optimizing flow characteristics and ensuring the valve meets the specific needs of its intended application—whether it’s regulating gas in a laboratory or managing hydraulic fluid in an industrial press.
Once the design is perfected, the process shifts to machining, where raw materials are transformed into finely crafted components. High-pressure needle valves demand tolerances measured in microns to guarantee a perfect seal and seamless operation. Manufacturers often employ Computer Numerical Control (CNC) machines, which deliver the precision and consistency required for large production runs. Every curve of the needle, every thread in the body, must be exact—there’s no room for error when pressures reach the tens of thousands of psi.
After machining, the valves face rigorous testing. Pressure tests subject them to forces well beyond their rated capacity, simulating the harshest real-world scenarios. Leak tests follow, ensuring no fluid escapes under pressure—a critical factor for safety and efficiency. Only after passing these trials does a valve earn its place in a high-stakes system, a testament to the manufacturer’s commitment to quality.
Materials: The Backbone of Durability
The materials used in high-pressure needle valves are the foundation of their performance, chosen for their ability to withstand punishing conditions. Stainless steel, particularly grades like 316, is a cornerstone material. Its strength, coupled with excellent corrosion resistance, makes it ideal for harsh environments like offshore oil platforms or chemical processing plants. The alloy’s resistance to pitting and crevice corrosion ensures the valve remains reliable over years of service.
For less demanding applications, brass offers a cost-effective alternative. While it provides decent corrosion resistance and machinability, it lacks the robustness of stainless steel, limiting its use in extreme conditions. In cases where fluids are highly corrosive or temperatures soar, manufacturers turn to exotic alloys like Monel, Inconel, or Hastelloy. These materials excel in resisting wear and chemical attack, making them perfect for specialized applications, though their cost reflects their superior properties.
Material selection isn’t just about durability—it also affects functionality. The coefficient of thermal expansion, for instance, must be considered to ensure the valve maintains its seal across temperature swings. Manufacturers balance these factors carefully, tailoring material choices to the valve’s specific role, whether it’s enduring the salty spray of a marine environment or the acidic conditions of a chemical reactor.
Applications: Where Precision Meets Performance
High-pressure needle valves are versatile workhorses, serving a wide range of industries with unique demands. In the oil and gas sector, they’re indispensable. During exploration and drilling, they regulate the pressure of drilling fluids at the wellhead, preventing blowouts. In pipelines and refineries, they manage the flow of crude oil and natural gas, ensuring safe transport and processing under immense pressure.
Chemical processing plants also rely heavily on these valves. They control the flow of aggressive reactants in reactors, maintaining precise conditions for product quality. In distribution systems, they handle volatile chemicals safely, protecting both workers and equipment. The ability to fine-tune flow makes them invaluable in these high-stakes settings.
In hydraulic systems, high-pressure needle valves shine. Found in industrial machinery like hydraulic presses, they regulate fluid flow to control speed and force with pinpoint accuracy. In aerospace, they’re critical to hydraulic systems powering landing gear and flight controls, where reliability can be a matter of life and death.
Even medical equipment benefits from these valves. Anesthesia machines and laboratory instruments use them to control gas or liquid flow with precision, ensuring patient safety and experimental accuracy. From deep-sea rigs to hospital operating rooms, high-pressure needle valves prove their worth wherever precision and reliability are paramount.
Challenges in Manufacturing: Meeting the Demands of Excellence
Manufacturing high-pressure needle valves is no easy task—it’s a field rife with challenges that test a manufacturer’s skill and resilience. Industry standards, such as those from the American Petroleum Institute (API) or the American Society of Mechanical Engineers (ASME), set a high bar. Compliance requires robust quality control, meticulous documentation, and often third-party certification, adding layers of complexity to production.
The cost of materials and processes is another hurdle. Exotic alloys and precision machining drive up expenses, and manufacturers must balance these costs while remaining competitive. In a global market, this can mean razor-thin margins, pushing companies to optimize every step of their operation.
Customization adds further complexity. Many clients need valves tailored to specific dimensions, materials, or performance specs—think a unique thread size for a bespoke hydraulic system or a corrosion-resistant alloy for a chemical plant. This demands flexibility in design and production, often extending lead times and requiring specialized expertise.
Supply chain disruptions—like those seen during the COVID-19 pandemic—can also derail production. Securing high-quality materials on time is critical, and delays can ripple through the process, affecting delivery schedules. Manufacturers must build resilient supply chains and contingency plans to stay ahead of these risks.
Innovations: Pushing the Boundaries of Technology
Despite these challenges, the high-pressure needle valve industry is a hotbed of innovation, driven by the need for better performance and efficiency. Materials science is leading the charge, with new alloys and composites offering enhanced strength, corrosion resistance, and thermal stability. These advancements enable valves to tackle even tougher conditions, from deeper wells to hotter reactors.
Design improvements are also transforming the field. Engineers are refining the needle and seat geometry to enhance flow control and reduce wear over time. Tools like computational fluid dynamics (CFD) allow manufacturers to simulate performance digitally, perfecting designs before cutting metal. This reduces waste and accelerates development.
Smart technology is another frontier. Some valves now feature integrated sensors that monitor pressure, temperature, and flow in real-time. These “smart valves” feed data to operators, enabling predictive maintenance and minimizing downtime. In a factory setting, this could mean catching a leak before it becomes a failure, saving time and money.
Automation in manufacturing is boosting precision and scalability too. Robotic assembly lines and advanced CNC systems ensure consistency, even as demand grows. Together, these innovations are pushing high-pressure needle valves into a new era of reliability and sophistication.
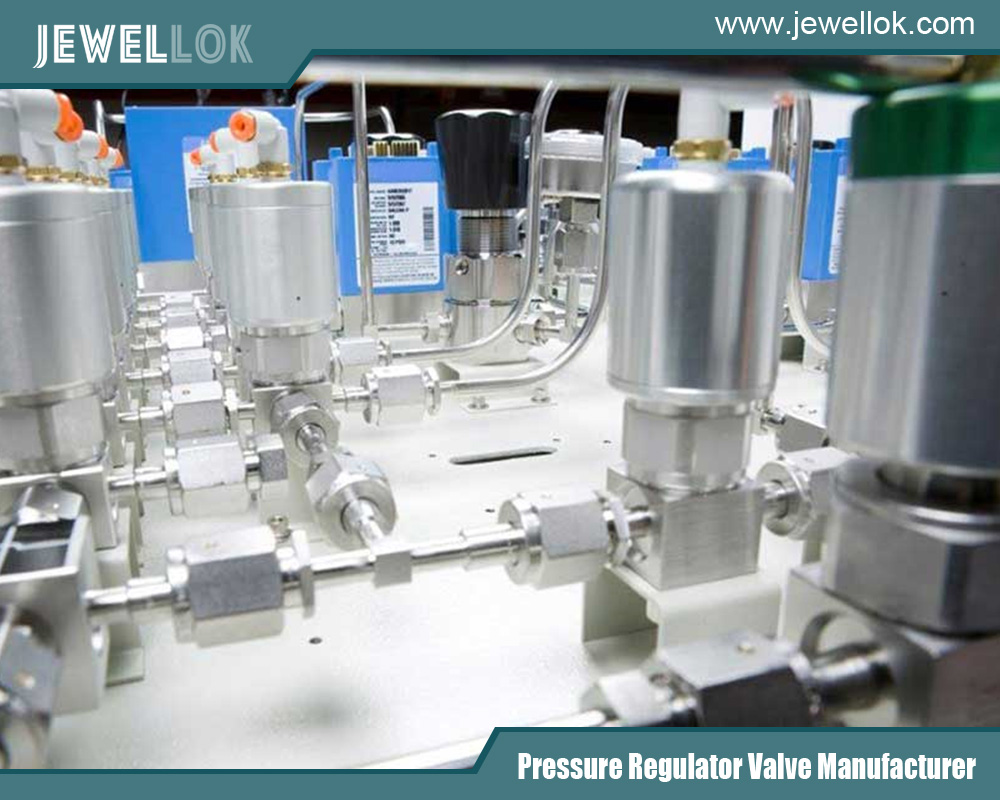
Conclusion: The Future of High-Pressure Needle Valves
High-pressure needle valves are more than mere components—they’re the product of extraordinary engineering, blending precision, durability, and innovation. As industries like oil and gas, chemical processing, and aerospace continue to push the limits of what’s possible, the need for these valves will only grow. Manufacturers who master this craft, delivering products that meet the highest standards, will remain linchpins in the industrial world.
For businesses operating in high-stakes environments, choosing a reputable manufacturer is non-negotiable. A well-made valve ensures system reliability, protects workers, and drives efficiency—cornerstones of success in any field. Looking ahead, advancements in materials, design, and technology promise to elevate high-pressure needle valves further, cementing their role as indispensable tools in the ever-evolving landscape of modern industry.
For more about the best high pressure needle valve : precision engineering for demanding applications, you can pay a visit to Jewellok at https://www.jewellok.com/ for more info.
Recent Posts
High-Pressure Hydraulic Needle Valve
Pneumatic Actuated Ball Valve
Industrial Diaphragm Valve
Needle Valve 10000 psi Manufacturers
Tags
Recommended Products
-
774L Stainless Steel UHP Fittings Butt Weld Bulkhead Union For High Flow Special Gas Fluid
-
764LR Stainless Steel 316 Reducing Tee UHP Fitting Automatic Buttweld Reducing Tee
-
High Purity Bulk Specialty Gas Pressure Control And Filtration Bulk Gas Skid Systems JW-300-BSGS
-
High Purity High Pressure Gas Cylinder Pressure Regulators Pressure Reducing Valve JSR-1E Series
-
Flow Control Stainless Steel Low Pressure Manual Diaphragm Valve For High Purity And Ultra High Purity Gases
-
Semi Automatic Gas Cabinet Gas Panels High Purity Gas Delivery Systems JW-200-GC
-
UHP Metal Gasket Face Seal Fittings Vacuum Coupling Metal Face Seal Join Long Gland And Short Gland
-
JF Series In-Line Gas Filters | High Purity High Precision High Flow Semiconductor Gas Filter Gas Filtration & Purification