Blog
Jewellok is a professional pressure regulator and valve manufacturer and supplier.
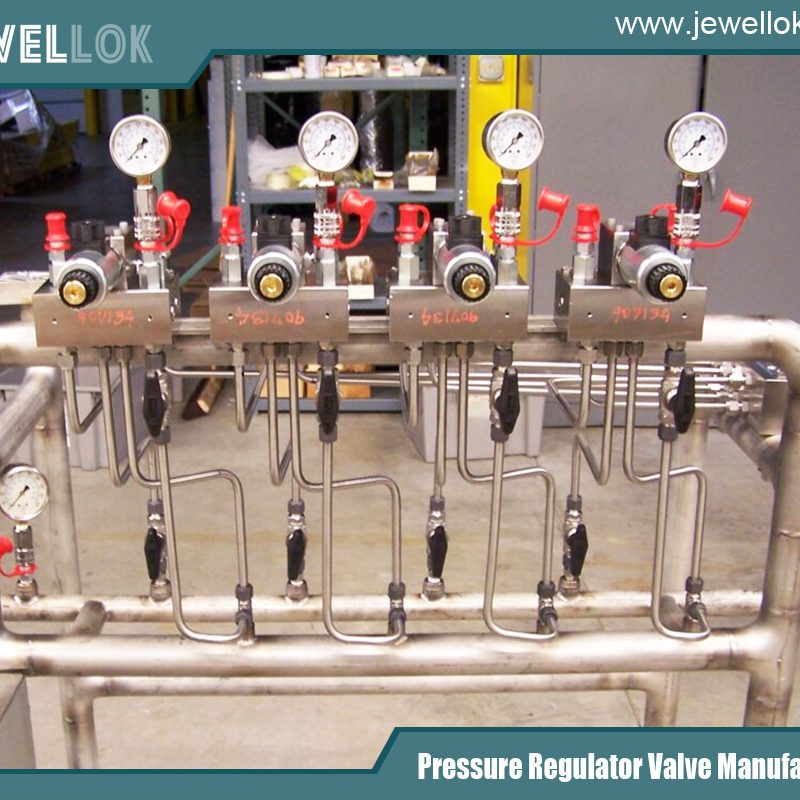
How a Gas Pressure Regulator Works
- Pressure Regulator Valve Manufacturer
- 1 1 2 gas pressure regulator, 1/2 gas pressure regulator, adjustable low pressure propane regulator, air compressor non return valve, application of ultra-high purity gas pressure regulator, argon gas pressure regulator, argon gas pressure regulator manufacturer, argon gas pressure regulator supplier, argon gas pressure regulator supplier factory, argon gas pressure regulator supplier hotsale, argon gas pressure regulator supplier OEM, argon gas pressure regulator supplier wholesale, BA Grade High Purity Gas Pressure Regulators, China Customized Back Gas Pressure Regulator Manufacturers, China Customized Gas Pressure Regulator Manufacturers, China Natural Gas Pressure Regulator, China Single Stage Gas Pressure Regulator Manufacturers, China Suppliers Instrument Gas Pressure Regulator, China Wholesale Nitrogen Gas Pressure Regulator, fire arrestor, gas pressure regulator, Gas Pressure Regulator Companies in Russia, gas pressure regulator factory, Gas pressure regulator for hydrogen, how a pressure regulator works, humming propane regulator, pressure relief valve vs safety valve, propane manifold with valves, safety relief valve vs safety valve, safety valve vs pressure relief valve, second stage propaneregulator, timer water valve
- No Comments
How a Gas Pressure Regulator Works
Imagine a scenario where the gas flowing to your stove or heater is uncontrolled, with pressure levels fluctuating wildly. Such a situation could lead to inefficient operation, equipment damage, or even catastrophic accidents. Fortunately, gas pressure regulators exist to prevent these issues by precisely controlling gas pressure. These devices are the unsung heroes of gas systems, ensuring that the right amount of gas is delivered at the right pressure, every time.
Gas pressure regulators are used in a wide range of settings, from residential gas grills and water heaters to industrial manufacturing processes and medical equipment. Understanding how they work is crucial for anyone involved in the installation, maintenance, or use of gas systems. This article provides a detailed exploration of gas pressure regulators, breaking down their components, explaining their operating principles, and highlighting their importance in various applications.
What is a Gas Pressure Regulator?
A gas pressure regulator is a mechanical device designed to reduce and control the pressure of gas as it flows from a high-pressure source to a lower-pressure application. The high-pressure source could be a gas cylinder, a storage tank, or a pipeline, where gas is stored or transported at pressures much higher than what is safe or practical for end-use devices. For example, the pressure in a propane tank can reach up to 200 psi, while a typical gas grill requires only about 0.5 psi. The regulator steps down this pressure to a safe and usable level.
Beyond simply reducing pressure, regulators maintain a constant output pressure despite variations in the input pressure or changes in gas flow demand. This stability is critical because fluctuations in pressure can affect the performance of gas-powered equipment, potentially leading to inefficiencies or safety hazards.

Components of a Gas Pressure Regulator
A typical gas pressure regulator consists of three main components: the loading mechanism, the sensing element, and the control element. Each plays a vital role in the regulation process.
- Loading Mechanism: This is usually a spring that applies a constant force to the sensing element. The spring’s tension determines the desired output pressure and can often be adjusted to set different pressure levels.
- Sensing Element: Typically a diaphragm, this flexible membrane responds to changes in gas pressure. The diaphragm moves based on the balance between the force of the spring and the pressure of the gas.
- Control Element: This is a valve that adjusts the flow of gas through the regulator. Connected to the diaphragm, it opens or closes based on the diaphragm’s movement to maintain the desired pressure.
These components work together in a feedback loop to ensure that the output pressure remains stable, even when there are changes in the input pressure or gas flow rate.
How Does a Gas Pressure Regulator Work?
The operation of a gas pressure regulator relies on a simple yet effective principle: balancing forces to maintain equilibrium. Here’s a step-by-step explanation of how it functions:
- Initial State: When the regulator is installed, the spring pushes down on the diaphragm, which in turn opens the valve. This allows gas to flow from the high-pressure inlet to the low-pressure outlet.
- Pressure Build-Up: As gas flows into the outlet side, the pressure begins to rise. This increasing pressure exerts an upward force on the diaphragm, counteracting the downward force of the spring.
- Equilibrium: When the outlet pressure reaches the desired level (set by the spring tension), the upward force from the gas pressure equals the downward force from the spring. The diaphragm stabilizes, and the valve adjusts to a position where it allows just enough gas to flow to maintain the set pressure.
Response to Changes:
- If the outlet pressure drops (e.g., due to increased demand from an appliance), the spring force exceeds the gas pressure force, pushing the diaphragm down and opening the valve further to allow more gas through.
- If the outlet pressure rises (e.g., due to decreased demand), the gas pressure force surpasses the spring force, pushing the diaphragm up and closing the valve to reduce gas flow.
- This continuous adjustment ensures that the output pressure remains constant, regardless of fluctuations in the input pressure or changes in gas consumption.
To illustrate this, consider a thermostat in a heating system. The thermostat maintains a set temperature by turning the heater on when the room cools and off when it warms. Similarly, the regulator maintains a set pressure by opening the valve when pressure drops and closing it when pressure rises.
Types of Gas Pressure Regulators
Gas pressure regulators come in various types, each suited to specific applications and requirements. They can be categorized based on the number of stages and the method of operation.
Based on Stages
- Single-Stage Regulators:
- These reduce pressure from the source to the desired level in one step.
- They are simpler and less expensive but may not provide precise control if the inlet pressure varies significantly.
- Commonly used in applications with stable inlet pressure, such as residential gas systems
2. Two-Stage Regulators:
- These reduce pressure in two steps, offering more accurate and stable output pressure.
- The first stage lowers the inlet pressure to an intermediate level, and the second stage fine-tunes it to the desired output pressure.
- Ideal for applications with fluctuating inlet pressure or where precision is critical, such as laboratories or industrial processes.
Based on Operation
- Direct-Operated Regulators:
- Also called self-operated regulators, these use the system’s own pressure to operate the valve.
- They are simple, reliable, and suitable for low to moderate flow rates, often found in residential and light commercial applications.
2. Pilot-Operated Regulators:
- These use a small pilot valve to control the main valve, providing precise pressure control and higher flow capacities.
- Typically used in high-flow applications, such as industrial gas distribution or large commercial systems.
Selecting the appropriate type depends on factors like required precision, flow rate, inlet pressure variability, and the specific application.
Safety Features
Safety is paramount in gas systems, and pressure regulators include various features to prevent accidents and ensure reliable operation:
- Overpressure Protection: Many regulators have a relief valve that opens if the output pressure exceeds a safe level, venting excess gas to prevent damage or hazards.
- Shut-Off Mechanisms: Some feature automatic shut-off valves that close if pressure exceeds a critical limit or if a sudden pressure loss indicates a leak.
- Vent Holes: These prevent pressure build-up in the diaphragm housing if the diaphragm fails, avoiding uncontrolled gas release.
- Filters: Inlet filters keep debris from entering the regulator, reducing the risk of malfunctions.
These features protect both the system and its users.
Installation and Maintenance
Proper installation and regular maintenance are vital for safe and effective regulator operation.
Installation Tips
- Orientation: Install the regulator as specified (e.g., vent hole downward) to ensure proper function and prevent moisture ingress.
- Sizing: Match the regulator to the application’s flow and pressure needs.
- Connections: Use appropriate fittings and ensure tight seals to avoid leaks.
- Ventilation: Keep vents unobstructed and directed away from ignition sources.
Maintenance Guidelines
- Inspections: Check for wear, corrosion, or damage, especially on the diaphragm and valve seat.
- Leak Testing: Use a soap solution or gas detector to test for leaks periodically.
- Spring Tension: Verify it matches the desired output pressure.
- Cleaning: Remove debris from the vent and inlet areas.
These practices enhance safety and longevity.
Applications of Gas Pressure Regulators
Gas pressure regulators are used across industries, including:
- Residential: Gas stoves, ovens, and heaters.
- Commercial: Restaurant kitchens and heating systems.
- Industrial: Metal cutting, welding, and chemical production.
- Medical: Oxygen therapy and anesthesia machines.
- Energy: Natural gas pipelines.
- Aerospace: Rocket propulsion systems.
Each application requires a regulator tailored to its specific needs.
Technical Specifications
Key specifications for selecting a regulator include:
- Pressure Ranges: Must handle the maximum inlet and deliver the desired outlet pressure.
- Flow Capacity: Measured in CFH or BTU/h, indicating maximum gas flow without pressure drop.
- Accuracy: Ability to maintain set pressure under varying conditions.
- Lock-Up Pressure: Pressure at which the regulator shuts off when demand ceases.
- Temperature Range: Operating limits affecting performance.
These ensure the regulator meets application demands.
Materials Used
Materials depend on the gas and conditions:
- Body: Brass, aluminum, or stainless steel for durability.
- Diaphragm: Rubber (nitrile, neoprene) or metal (stainless steel).
- Valve Seat: Teflon or nylon for sealing.
- Springs: Stainless steel for corrosion resistance.
For oxygen, hydrocarbon-free materials prevent combustion.
Troubleshooting Common Issues
Common problems and solutions include:
- High Output Pressure:
- Cause: Excessive spring tension or damaged diaphragm.
- Solution: Adjust tension or replace diaphragm.
2. Low Output Pressure:
- Cause: Low spring tension, blocked inlet, or worn valve seat.
- Solution: Adjust spring, clean inlet, or replace seat.
3. Gas Leak:
- Cause: Loose connections or damaged seals.
- Solution: Tighten connections or replace seals.
4. Chattering:
- Cause: Oversized regulator.
- Solution: Use a properly sized unit.
Consult a professional if issues persist.
Regulatory Standards
Regulators must meet standards from:
- ANSI: Gas appliance standards.
- ISO: Global pressure regulator standards.
- UL: Safety certifications.
- CSA: Canadian gas equipment standards.
Compliance ensures safety and performance.
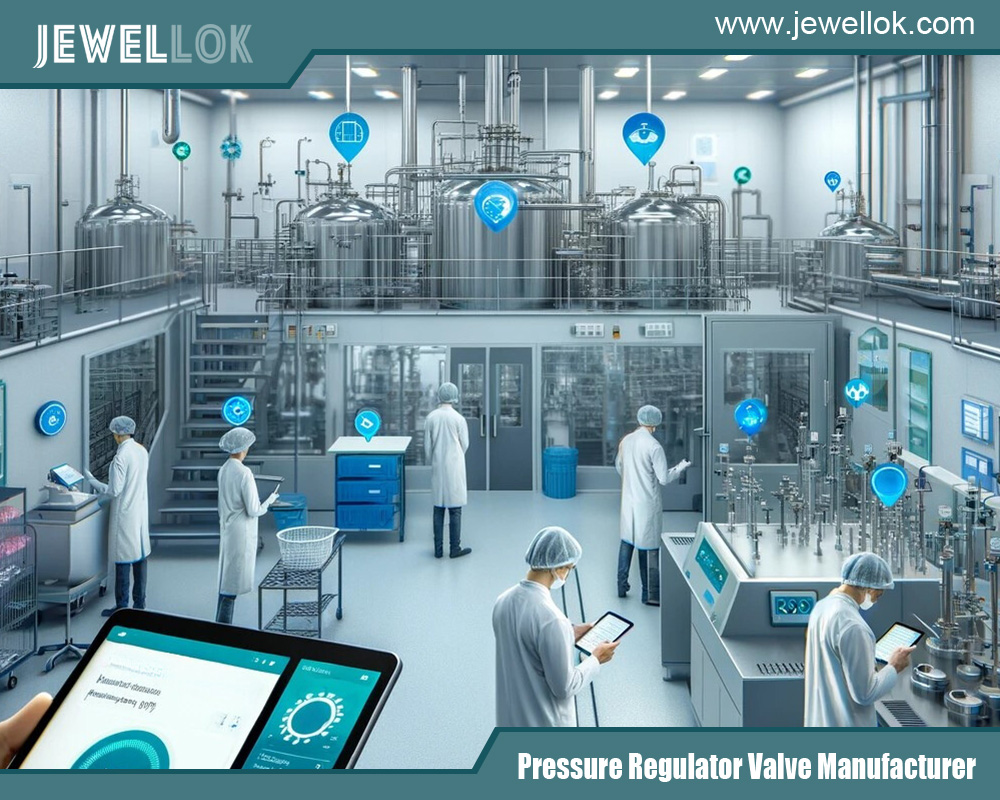
Conclusion
Gas pressure regulators are vital for controlling pressure in gas systems, ensuring safety and efficiency. By understanding their components, principles, and types, users can select and maintain the right regulator for their needs. As technology advances, these devices continue to improve, playing a key role in diverse applications from homes to industries.
For more about how a gas pressure regulator works, you can pay a visit to Jewellok at https://www.jewellok.com/ for more info.
Recent Posts
How a Gas Pressure Regulator Works
Adjustable Low Pressure Propane Regulator
Pressure Control Valve Manufacturers
High Flow Needle Valves manufacturers
Tags
Recommended Products
-
Manual Gas Rack High Purity Gas Delivery Systems JW-100-GR
-
Stainless Steel High Purity High Temperature Pneumatic Actuated Ball Valves JBV2 Series
-
FT-BOX JW-FTB-C Valve Manifold Panels And Boxes With High Purity Configurable Systems
-
High Purity And Industria Gas Stick Assemblies Precise Pressure Control Gas Systems JSR-1ETG-BV Series
-
Stainless Steel Low Pressure Seal Pneumatic Diaphragm Control Valve For For HP & UHP Gases
-
VMB Valve Manifold Panels And Boxes High Purity Configurable Systems JW-200-VMB & JW-100-VMB
-
Fully Automated Gas Cabinet For Precise UHP Gas Delivery And High Purity Gas Delivery Systems JW-300-GC
-
765LR Reducing Tee | Stainless Steel 316 High Purity Butt Weld Fittings Metal Face Seal For Welding Pipe Fitting Reducing Tee