Blog
Jewellok is a professional pressure regulator and valve manufacturer and supplier.
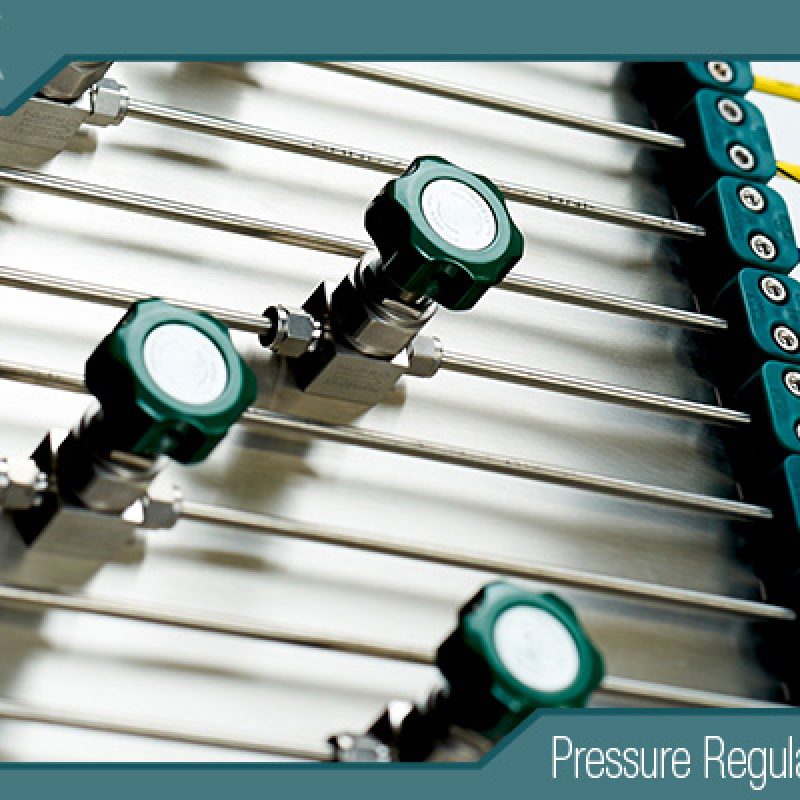
How to Choose the Right Stainless Steel Pressure Gauge for Your Use?
- Pressure Regulator Valve Manufacturer
- adjusting propane regulator, bcf connector, block & bleed valve, characteristics of pressure, China Stainless Steel Pressure Regulator, chinese propane gas cylinder, diaphram valve, double block & bleed, double block and bleed valve, double block bleed valve, excess flow valve, fusible plug, gas regulator, gas used in semiconductor manufacturing, high grade stainless steel pressure regulator, High Pressure Co2 Stainless Steel Pressure Regulator, high pressure flexible hose, high pressure regulator, High Pressure Stainless Steel Pressure Regulator, how a solenoid valve works, hydraulic regulator, industrial grade purity, o ring face seal fittings, pressure gauge fitting - 3/8 qc, pressure relief valve vs safety relief valve, quick connect, quick connect valve, relief valve and safety valve difference, safety relief valve vs pressure relief valve, solenoid valve for ammonia gas 1 inch pipe, Stainless Pressure Gauge, Stainless Steel Pressure Gauge, Stainless Steel Pressure Regulator, ultra high purity, water solenoid valve 24v
- No Comments
How to Choose the Right Stainless Steel Pressure Gauge for Your Use?
Pressure gauges are indispensable instruments in industries such as oil and gas, chemical processing, hydrogen energy, pharmaceuticals, water treatment, and food and beverage, where they monitor and control system pressure to ensure safety, efficiency, and compliance. Stainless steel pressure gauges, known for their durability, corrosion resistance, and versatility, are widely used in demanding environments where harsh fluids, high pressures, or stringent hygiene standards are present. However, choosing the right stainless steel pressure gauge requires careful consideration of factors like application requirements, pressure range, accuracy, environmental conditions, material compatibility, and regulatory standards. An incorrect choice can lead to inaccurate readings, equipment damage, safety hazards, or regulatory non-compliance. This article provides a step-by-step guide to selecting the right stainless steel pressure gauge, exploring key criteria, practical considerations, and emerging trends to help organizations optimize performance and reliability in their pressure measurement systems.
Understanding Stainless Steel Pressure Gauges
A pressure gauge measures the pressure of a gas or liquid in a system, typically displayed on a dial with a needle or digitally. Stainless steel pressure gauges are constructed with stainless steel (e.g., 304 or 316) for critical components like the case, wetted parts (bourdon tube, socket), or both, making them ideal for corrosive, high-pressure, or hygienic applications. They are available in various types, including:
- Bourdon Tube Gauges: Use a curved tube that straightens under pressure, moving a needle (most common, ±0.5–2% accuracy).
- Diaphragm Gauges: Employ a flexible diaphragm for low-pressure or corrosive fluids (±1–2% accuracy).
- Capsule Gauges: Measure very low pressures using two diaphragms (±1–3% accuracy).
- Digital Gauges: Provide precise, electronic readings (±0.1–0.5% accuracy).
Choosing the right gauge involves aligning its specifications with the application’s needs. Below, we outline a structured approach to guide this process.
Step 1: Define Application Requirements
The first step is to understand the specific requirements of your application, as these dictate the gauge’s design, materials, and performance.
1.1 Fluid Type and Compatibility
The fluid being measured (gas or liquid) determines the gauge’s material and construction:
- Corrosive Fluids: Chemicals like ammonia, chlorine, or acids require 316L stainless steel wetted parts for superior corrosion resistance compared to 304 stainless steel.
- Non-Corrosive Fluids: Water, air, or nitrogen may allow 304 stainless steel, which is less expensive but less resistant to pitting corrosion.
- Viscous or Slurry Fluids: Diaphragm gauges with a seal prevent clogging, unlike bourdon tube gauges.
- Hazardous Gases: Flammable (e.g., hydrogen) or toxic (e.g., arsine) gases require gauges with leak-tight seals and safety features like blowout backs.
- Action: Create a fluid profile specifying composition, corrosiveness, and state (gas/liquid), and ensure wetted parts are compatible (e.g., 316L for corrosive media).
1.2 Pressure Range and Operating Conditions
The gauge must handle the system’s pressure range and operating conditions:
- Pressure Range: Select a gauge with a full-scale range approximately twice the normal operating pressure to avoid over-pressurization damage. For example, a system operating at 100 bar should use a gauge with a 0–200 bar range.
- Pressure Type: Choose gauges for gauge pressure (relative to atmospheric), absolute pressure (relative to vacuum), or differential pressure (between two points).
- Temperature: Ensure the gauge withstands fluid and ambient temperatures (e.g., -40°C to 150°C for 316 stainless steel). Use liquid-filled gauges or remote seals for extreme temperatures.
- Pulsation/Vibration: Pulsating or vibrating systems (e.g., near pumps) require liquid-filled gauges or snubbers to dampen needle movement.
- Action: Compile a datasheet with maximum and normal operating pressures, temperature range, and dynamic conditions (pulsation/vibration).
1.3 Application Context
Consider the industry and specific use case:
- Oil and Gas: Requires gauges with high-pressure ratings (e.g., 1000 bar) and corrosion resistance for crude oil or sour gas.
- Pharmaceuticals: Demands hygienic gauges with polished 316L stainless steel and clean-in-place (CIP) compatibility.
- Hydrogen Energy: Needs gauges for ultra-high-pressure hydrogen (e.g., 700 bar) with materials resistant to embrittlement.
- Food and Beverage: Requires sanitary gauges meeting 3-A or FDA standards.
- Water Treatment: Uses gauges for moderate pressures and corrosion resistance against chlorinated water.
- Action: Define the industry, application (e.g., process monitoring, custody transfer), and any regulatory or hygienic requirements.
Step 2: Select the Appropriate Gauge Specifications
Once application requirements are clear, choose a gauge with specifications that ensure accuracy, durability, and safety.
2.1 Accuracy and Resolution
Accuracy is critical for precise pressure measurement:
- Accuracy Classes: Gauges are rated by accuracy (e.g., ±0.5% full scale [FS], ±1% FS). High-precision applications (e.g., pharmaceuticals) require ±0.25–0.5% FS, while general industrial use may tolerate ±1–2% FS.
- Dial Size: Larger dials (e.g., 100–150 mm) improve readability and resolution, ideal for critical systems. Smaller dials (e.g., 50 mm) suit compact installations.
- Digital vs. Analog: Digital gauges offer higher accuracy (±0.1–0.5%) and data logging, while analog gauges are simpler and more cost-effective.
- Action: Select an accuracy class based on application needs (e.g., ±0.5% for custody transfer) and choose a dial size or digital display for clear readability.
2.2 Material Selection
Stainless steel grade and component materials impact performance:
- Case Material: 304 stainless steel for general environments; 316 stainless steel for corrosive or marine settings.
- Wetted Parts: 316L stainless steel for corrosive fluids; Monel or Hastelloy for extreme conditions (e.g., chlorine gas).
- Lens: Polycarbonate for impact resistance; laminated safety glass for high-pressure or hazardous applications.
- Seals/Gaskets: PTFE or Viton for chemical compatibility; silicone for food-grade applications.
- Action: Specify 316L stainless steel for wetted parts in corrosive systems and ensure seals match fluid compatibility.
2.3 Gauge Type and Features
Choose the gauge type and features based on system requirements:
- Bourdon Tube Gauges: Versatile for high-pressure gases or liquids (e.g., oil pipelines).
- Diaphragm Gauges: Ideal for low-pressure or corrosive fluids (e.g., wastewater).
- Liquid-Filled Gauges: Dampen vibration and pulsation, extending lifespan in dynamic systems (e.g., pump discharge).
- Safety Features: Blowout backs, solid-front cases, or restrictor screws enhance safety for hazardous applications.
- Mounting Options: Bottom, back, or panel mounts suit different installation needs.
- Output Signals: 4–20 mA or digital outputs (e.g., HART, Modbus) for integration with control systems.
- Action: Select the gauge type (e.g., liquid-filled bourdon for vibrating systems) and features (e.g., 4–20 mA output for SCADA integration) based on operational needs.
Step 3: Consider Environmental and Installation Factors
Environmental conditions and installation practices significantly affect gauge performance and longevity.
3.1 Environmental Conditions
- Corrosive Atmospheres: Coastal or chemical plant environments require 316 stainless steel cases to resist salt or acid exposure.
- Temperature Extremes: Use gauges with temperature compensation or remote seals for cryogenic (e.g., -196°C for liquid nitrogen) or high-temperature (e.g., 200°C for steam) systems.
- Ingress Protection: IP65 or IP67 ratings protect against dust and water in outdoor or washdown environments (e.g., food processing).
- Vibration/Shock: Liquid-filled gauges or shock-resistant designs prevent needle drift in high-vibration areas (e.g., near compressors).
- Action: Specify IP ratings and stainless steel grades to match environmental conditions, and use dampening accessories for vibration-prone areas.
3.2 Installation Considerations
Proper installation ensures accurate readings and gauge durability:
- Location: Install gauges away from extreme heat sources or direct sunlight to prevent thermal drift.
- Orientation: Vertical mounting is standard; angled mounts improve readability in awkward locations.
- Piping: Use impulse dampeners, snubbers, or pigtail siphons to protect gauges from pressure spikes or steam.
- Accessibility: Ensure gauges are easily accessible for reading, calibration, and maintenance.
- Action: Follow manufacturer installation guidelines, using accessories like snubbers or siphons to protect the gauge.
Step 4: Ensure Regulatory and Safety Compliance
Compliance with industry standards and safety requirements is critical, especially in regulated industries.
4.1 Key Standards
- ASME B40.100: Specifies performance, accuracy, and safety for pressure gauges, including stainless steel models.
- EN 837: European standard for pressure gauges, defining accuracy classes and testing requirements.
- API 520/526: Governs pressure measurement in oil and gas, emphasizing safety and reliability.
- FDA/3-A: Require hygienic designs for food and pharmaceutical gauges, including polished 316L stainless steel.
- NFPA 56: Mandates safe materials and designs for hydrogen systems, including embrittlement-resistant gauges.
- ATEX/IECEx: Ensure gauges are intrinsically safe for explosive atmospheres (e.g., hydrogen refueling stations).
4.2 Safety Features
- Blowout Back: Releases pressure in case of failure, protecting operators.
- Solid-Front Design: Prevents case rupture in high-pressure systems.
- Over-Pressure Protection: Limits damage from pressure spikes (e.g., 130% of full scale).
- Action: Verify compliance with relevant standards (e.g., ASME, FDA) and select gauges with safety features for hazardous applications.
Step 5: Evaluate Performance and Maintenance Needs
The gauge’s performance and maintenance requirements impact long-term reliability and cost.
5.1 Performance Criteria
- Accuracy Stability: High-quality gauges maintain accuracy over time, reducing calibration frequency.
- Response Time: Fast response is critical for dynamic systems (e.g., hydraulic presses).
- Repeatability: Ensures consistent readings under identical conditions, vital for process control.
- Action: Request performance data (e.g., accuracy, repeatability) from suppliers and choose gauges with proven stability.
5.2 Maintenance and Calibration
- Calibration Frequency: High-precision gauges (e.g., ±0.5% FS) may require annual calibration, while general-purpose gauges (e.g., ±2% FS) can be calibrated every 2–3 years.
- Ease of Maintenance: Liquid-filled or sealed gauges reduce maintenance needs; digital gauges offer self-diagnostic features.
- Spare Parts: Ensure availability of replacement lenses, seals, or bourdon tubes.
- Action: Establish a calibration schedule based on application criticality and manufacturer recommendations, and maintain spare parts for quick repairs.
5.3 Total Cost of Ownership (TCO)
- Upfront Cost: Stainless steel gauges cost more than brass or plastic but offer durability.
- Maintenance Costs: Liquid-filled or digital gauges reduce maintenance compared to dry analog gauges.
- Lifespan: 316 stainless steel gauges last longer in corrosive environments, reducing replacement frequency.
- Action: Calculate TCO by factoring in purchase price, maintenance, calibration, and lifespan, prioritizing quality for critical systems.
Step 6: Partner with Reliable Suppliers
The supplier’s expertise, quality, and support are crucial for selecting the right gauge.
6.1 Supplier Evaluation
- Reputation: Choose suppliers with a track record in your industry (e.g., WIKA, Ashcroft, or Omega for industrial gauges).
- Certifications: Ensure gauges meet ISO 9001, ASME, or industry-specific standards.
- Customization: Select suppliers offering tailored solutions (e.g., specific pressure ranges, materials, or outputs).
6.2 Support Services
- Technical Support: Access to engineers for selection and troubleshooting.
- Calibration Services: On-site or lab calibration to maintain accuracy.
- Warranty: Look for warranties covering defects or performance issues (e.g., 1–5 years).
- Action: Request supplier references, certifications, and service details, and negotiate terms for support and warranties.
Challenges and Solutions
- Challenge: Over-specifying gauges, increasing costs.
- Solution: Match gauge specifications to application needs (e.g., ±1% FS for general use vs. ±0.5% for precision).
- Challenge: Environmental damage to gauges
- Solution: Use 316 stainless steel, IP67-rated, or liquid-filled gauges for harsh conditions.
- Challenge: Regulatory compliance.
- Solution: Work with suppliers to ensure gauges meet standards like ASME or FDA.
- Challenge: Calibration downtime.
- Solution: Use digital gauges with remote calibration or maintain spare gauges.
Emerging Trends
Innovations are enhancing stainless steel pressure gauges:
- Digital Gauges: Offer high accuracy, data logging, and wireless connectivity for IoT integration.
- Smart Diagnostics: AI-driven gauges predict calibration drift or failures, reducing maintenance.
- Sustainable Materials: Eco-friendly manufacturing and recyclable stainless steel align with green goals.
- Miniaturization: Compact gauges support portable or space-constrained systems (e.g., medical devices).
- Impact: These trends improve accuracy, usability, and sustainability, supporting modern industrial needs.
Case Studies
- Oil Refinery (USA): A refinery selected 316L stainless steel bourdon tube gauges with ±0.5% FS accuracy for sour gas monitoring, ensuring API 520 compliance and reducing failures by 70%.
- Pharmaceutical Plant (Germany): Polished 316L diaphragm gauges with 3-A certification were used for sterile water systems, meeting FDA standards and improving hygiene.
- Hydrogen Station (Japan): Digital 316 stainless steel gauges with ATEX certification handled 700-bar hydrogen, integrating with SCADA for real-time monitoring.
Conclusion
Choosing the right stainless steel pressure gauge requires a systematic approach, considering fluid compatibility, pressure range, accuracy, environmental conditions, regulatory compliance, and maintenance needs. By defining application requirements, selecting appropriate specifications, ensuring proper installation, and partnering with reliable suppliers, organizations can optimize gauge performance, enhance safety, and reduce costs. Stainless steel gauges, particularly those made from 316L, offer unmatched durability and corrosion resistance, making them ideal for demanding industries like oil and gas, pharmaceuticals, and hydrogen energy. Emerging trends like digital gauges and smart diagnostics further enhance their value, supporting precision and efficiency in modern systems. By following the steps outlined in this article, stakeholders can confidently select the right stainless steel pressure gauge, ensuring reliable pressure measurement and operational success in critical applications.
For more about how to choose the right stainless steel pressure gauge for your use, you can pay a visit to Jewellok at https://www.jewellok.com/ for more info.
Recent Posts
Pneumatic Actuated Ball Valve
Industrial Diaphragm Valve
Needle Valve 10000 psi Manufacturers
Best High-Pressure Gas Regulators For Industrial Use
Tags
Recommended Products
-
316L Stainless Steel Tube Butt Weld Reducing Fittings Union Reducer RW Series Ultrahigh Purity Process
-
764LR Stainless Steel 316 Reducing Tee UHP Fitting Automatic Buttweld Reducing Tee
-
775L Bulkhead Reducing Union | Stainless Steel High Purity Double Ferrule Bulkhead Reducing Unions
-
High Pressure High-Purity Welded Check Valves And Low Cracking Pressure Check Valve JCV1 Series
-
Ultra High Purity Oxygen Pressure Gauge For Semiconductor Gases JG Series Pressure Instruments For Semiconductor Manufacturing
-
UHP Metal Gasket Face Seal Fittings Vacuum Coupling Metal Face Seal Join Long Gland And Short Gland
-
Line And Panel Mounting Adjustable Low Pressure Propane And Nitrogen Pressure Regulator JSR-3L & JSR-3LP Series
-
High Purity High Pressure Gas Cylinder Pressure Regulators Pressure Reducing Valve JSR-1E Series