Blog
Jewellok is a professional pressure regulator and valve manufacturer and supplier.
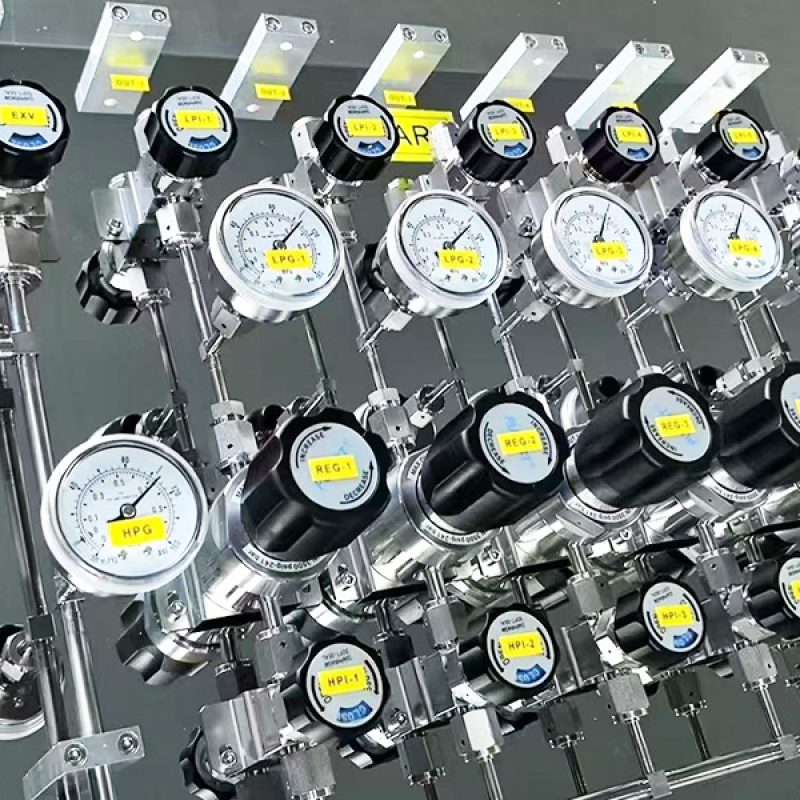
Nitrogen Manifold Panel for Individual Gas Cabinet and Valve Manifold Box
- Pressure Regulator Valve Manufacturer
- 200 Bar Changeover Manifold, 200bar Semi-automatic Switchover Manifold, Double Cylinder Manifold For Nitrogen, Gas Distribution Manifold Systems, Gas manifold systems with automatic switch-over, Gas Valve Manifold Boxes, Nitrogen Control Panel Regulator, Nitrogen Gas Control Panel, Nitrogen Gas Cylinders Manifold And Control panel, Nitrogen Gas Manual Manifold Systems, nitrogen manifold panel, nitrogen manifold panel for individual gas cabinet and valve manifold box, Nitrogen Manifold System, Nitrogen Manifold w/pressure, semi-automatic switching manifold, Stainless Steel Changeover Nitrogen Gas Panel, Valve Manifold Boxes And Panels, Valve Manifold Panels and Boxes, VMB Cabinet Gas Valve Manifold Box
- No Comments
Nitrogen Manifold Panel for Individual Gas Cabinet and Valve Manifold Box
In industries where precision, safety, and reliability are non-negotiable, the management of gases like nitrogen plays a pivotal role. Nitrogen, an inert gas constituting approximately 78% of Earth’s atmosphere, is widely utilized for purging, inerting, and as a carrier gas across various applications. To ensure its continuous and safe delivery, specialized equipment such as gas cabinets, nitrogen manifold panels, and valve manifold boxes (VMBs) are employed. This article provides a comprehensive exploration of nitrogen manifold panels within individual gas cabinets and their integration with valve manifold boxes, emphasizing their design, functionality, safety features, and maintenance requirements in industrial gas delivery systems. Spanning approximately 2000 words, this discussion aims to equip professionals with a thorough understanding of these critical components.
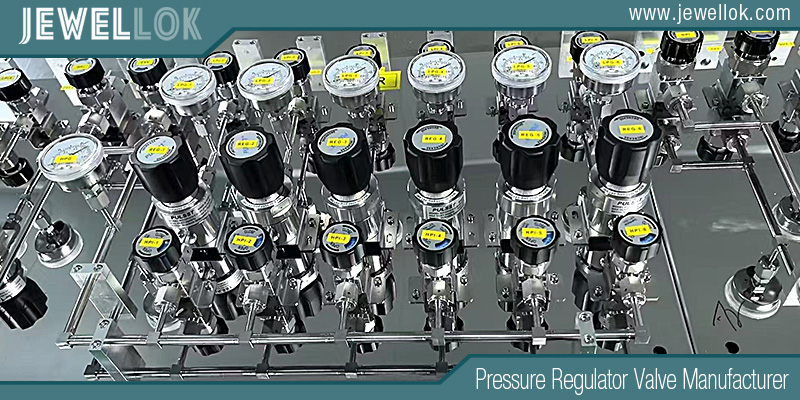
Introduction
Effective gas management is essential in industries such as semiconductor manufacturing, pharmaceuticals, food processing, and metal fabrication, where nitrogen’s inert properties are harnessed to enhance safety and efficiency. Nitrogen manifold panels within individual gas cabinets and valve manifold boxes are engineered systems designed to store, regulate, and distribute nitrogen gas seamlessly. This article delves into their roles, how they integrate into a cohesive gas delivery system, and the considerations that ensure their optimal performance. By examining their applications, design principles, safety mechanisms, and operational best practices, we highlight their significance in maintaining controlled and reliable gas supply chains.
Nitrogen in Industrial Applications
Nitrogen’s prominence in industrial settings stems from its inert, non-reactive nature, making it ideal for environments where oxidation or combustion must be prevented. Comprising a colorless and odorless gas, nitrogen serves multiple purposes:
– Purging: It displaces oxygen or other reactive gases from pipelines, vessels, or systems to prevent unwanted chemical reactions or degradation.
– Inerting: Nitrogen creates an oxygen-free atmosphere in storage tanks or reactors, safeguarding sensitive or flammable materials.
– Carrier Gas: In processes like gas chromatography or chemical synthesis, nitrogen transports substances without interfering chemically.
In the semiconductor industry, nitrogen is indispensable for maintaining cleanroom conditions and preventing contamination during wafer fabrication. In food packaging, it extends shelf life by replacing oxygen in sealed containers, while in metal fabrication, it acts as an assist gas in laser cutting. Its versatility and safety profile make nitrogen a cornerstone of modern industrial processes.
Gas Cabinets: The Foundation of Safe Storage
A gas cabinet is a ventilated, enclosed structure designed to house gas cylinders securely, particularly for hazardous or high-purity gases. While nitrogen itself is non-toxic and non-flammable, gas cabinets provide critical benefits even for this inert gas:
– Containment: They protect cylinders from physical damage and environmental exposure.
– Organization: Cylinders are kept orderly and accessible for maintenance or replacement.
– Contamination Prevention: Enclosures shield the gas supply from dust or impurities.
An individual gas cabinet is typically dedicated to a single gas type—nitrogen, in this case—to avoid cross-contamination and simplify system management. Key features include:
– Ventilation Systems: Exhaust fans remove any leaked gas, maintaining a safe environment.
– Fire Suppression: Sprinklers or gas-based systems mitigate risks, especially if co-located with flammable gases.
– Access Control: Lockable doors restrict entry to trained personnel.
– Monitoring: Sensors detect leaks or pressure anomalies, enhancing safety.
Constructed from robust materials like steel, gas cabinets are engineered to withstand operational stresses while adhering to stringent safety standards.
Nitrogen Manifold Panels: Ensuring Continuous Supply
Within the gas cabinet, the nitrogen manifold panel is the heart of the system, connecting multiple gas cylinders to a single output line. This configuration ensures uninterrupted nitrogen supply, a necessity for processes intolerant of downtime. For nitrogen, cylinders typically use a CGA 580 connection, requiring compatible fittings on the manifold. Key components include:
– Inlet Connections: Flexible pigtails or hoses (often stainless steel or Teflon-lined) link cylinders to the manifold.
– Isolation Valves: Each cylinder has a dedicated valve to control gas flow.
– Pressure Regulators: These maintain consistent output pressure, tailored to downstream needs.
– Gauges: Monitor cylinder and output pressures for operational oversight.
– Purge Systems: Remove air or residual gases during cylinder changes to preserve nitrogen purity.
The manifold’s design supports redundancy: when one cylinder depletes, the system can switch—manually or automatically—to a full reserve cylinder. Advanced panels incorporate pressure sensors and automatic switchover mechanisms, alerting operators via alarms or indicators. This ensures a steady supply, critical in applications like semiconductor processing, where even brief interruptions can compromise product quality.
Valve Manifold Boxes (VMBs): Precision Distribution
The valve manifold box (VMB) extends the gas delivery system by distributing nitrogen from the gas cabinet to multiple points of use. Acting as a centralized hub, the VMB offers flexibility and control over gas allocation. Its components include:
– Inlet Port: Connects to the manifold panel’s output line.
– Distribution Manifold: A header with multiple outlets for gas routing.
– Valves: Manual or automated valves per outlet enable individual flow control.
– Pressure Regulators: Adjust pressure for specific applications.
– Flow Meters: Monitor usage, ranging from simple rotameters to precise mass flow controllers (MFCs).
In high-precision settings like semiconductor fabrication, MFCs ensure accurate flow rates, often integrated with digital controls for remote monitoring. For less demanding uses, variable area flow meters suffice. Safety features, such as excess flow valves, halt gas flow if a downstream leak occurs, protecting both equipment and personnel. The VMB’s modular design allows customization based on the number of outlets and operational requirements.
Integration of Components: A Unified System
The synergy between the nitrogen manifold panel and VMB creates an efficient gas delivery system:
- Storage: Nitrogen cylinders reside in the individual gas cabinet, secured and monitored.
2. Regulation: The manifold panel connects these cylinders, regulating pressure and providing a single output.
3. Distribution: The VMB receives this output and allocates nitrogen to various endpoints.
This integration ensures continuity and precision. For example, in a laboratory, nitrogen might supply gas chromatography units, mass spectrometry equipment, and glove boxes simultaneously. The manifold panel guarantees availability, while the VMB tailors delivery to each instrument’s needs. Centralized control minimizes complexity, enabling operators to manage the system from a single interface, often enhanced by automation like programmable logic controllers (PLCs).
Design Considerations: Building for Performance
Designing these systems demands attention to several factors:
– Material Compatibility: Components must resist corrosion and maintain nitrogen purity. Stainless steel, brass, and high-purity seals (e.g., Viton or Teflon) are standard.
– Flow Rates: The system must accommodate peak demand. For instance, five points of use at 10 SLPM each require a minimum capacity of 50 SLPM, with a buffer (e.g., 75 SLPM) for scalability.
– Pressure Management: Regulators and piping must minimize pressure drops, especially over long runs.
– Safety Compliance: Adherence to standards like OSHA, NFPA, or SEMI ensures regulatory alignment.
– Accessibility: Layouts should facilitate cylinder changes and maintenance.
Nitrogen’s relatively low pressure simplifies some aspects, but high-purity applications may require electropolished stainless steel to prevent contamination. Redundancy—such as dual regulators—enhances reliability in critical operations.
Safety Features: Mitigating Risks
While nitrogen is inert, its use involves risks, notably asphyxiation in confined spaces where leaks can displace oxygen. Safety features include:
– Leak Detection: Gas sensors trigger alarms if nitrogen levels rise unexpectedly.
– Pressure Relief Valves: Prevent over-pressurization of cylinders or lines.
– Emergency Shut-off Valves: Isolate the system during incidents.
– Ventilation: Removes leaked gas from cabinets or work areas.
– Oxygen Monitors: Essential in enclosed spaces, alerting when oxygen falls below 19.5% (OSHA’s safe threshold).
Training is equally vital, ensuring personnel recognize asphyxiation symptoms and follow emergency protocols. Proper labeling and maintenance further reduce hazards.
Maintenance and Operation: Sustaining Reliability
Regular upkeep ensures system longevity and safety. Best practices include:
– Leak Testing: Use soap solutions or electronic detectors to identify breaches.
– Valve Checks: Verify smooth operation and proper sealing.
– Regulator Calibration: Confirm accurate pressure settings.
– Cylinder Handling: Secure and transport cylinders safely, adhering to protocols.
– Purge Procedures: Prevent contamination during cylinder swaps.
A maintenance checklist might cover visual inspections for corrosion, functional tests of valves and alarms, and calibration of gauges and flow meters. Automation, such as PLCs for switchover or remote monitoring, enhances operational efficiency and reduces human error.
Environmental and Cost Benefits
Nitrogen’s environmental impact is minimal due to its abundance and inertness. Efficient systems, like those with automatic switchover, minimize residual gas waste, reducing cylinder replacement frequency. Centralized VMB distribution lowers installation and maintenance costs compared to separate lines, while reduced downtime boosts productivity.
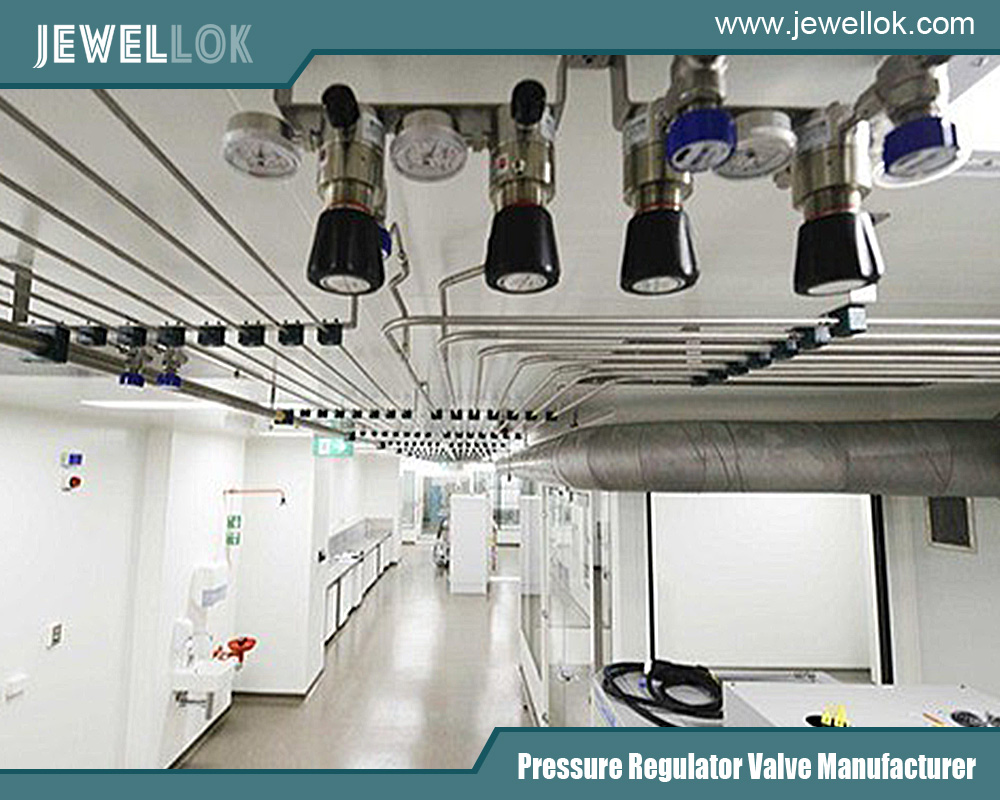
Conclusion
Nitrogen manifold panels within individual gas cabinets and valve manifold boxes form the backbone of industrial gas delivery systems. They ensure a safe, continuous, and efficient nitrogen supply, supporting critical processes across diverse sectors. By mastering their design, integration, safety, and maintenance, operators can optimize performance while safeguarding personnel and facilities. As reliance on nitrogen grows, these systems remain indispensable for advancing industrial excellence.
For more about nitrogen manifold panel for individual gas cabinet and valve manifold box, you can pay a visit to Jewellok at https://www.jewellok.com/product-category/gas-cabinet/ for more info.
Recent Posts
Pressure Relief Valve vs Safety Valve
How a Gas Pressure Regulator Works
Adjustable Low Pressure Propane Regulator
Tags
Recommended Products
-
767LT Reducer Pressure Reducing Valve Adjustment High purity Pressure Reducing Union Fittings And Tubing
-
Line And Panel Mounting Adjustable Low Pressure Propane And Nitrogen Pressure Regulator JSR-3L & JSR-3LP Series
-
770L Female Elbow | Stainless Steel High Purity Weld Fittings Female Micro Elbow Fittings
-
High Purity And Industria Gas Stick Assemblies Precise Pressure Control Gas Systems JSR-1ETG-BV Series
-
Manual Gas Rack High Purity Gas Delivery Systems JW-100-GR
-
Stainless Steel Low Pressure Seal Pneumatic Diaphragm Control Valve For For HP & UHP Gases
-
7108L Cylinder Cap Connectors For Ultra High Purity Gases
-
Stainless Steel High Purity High Temperature Pneumatic Actuated Ball Valves JBV2 Series