Blog
Jewellok is a professional pressure regulator and valve manufacturer and supplier.
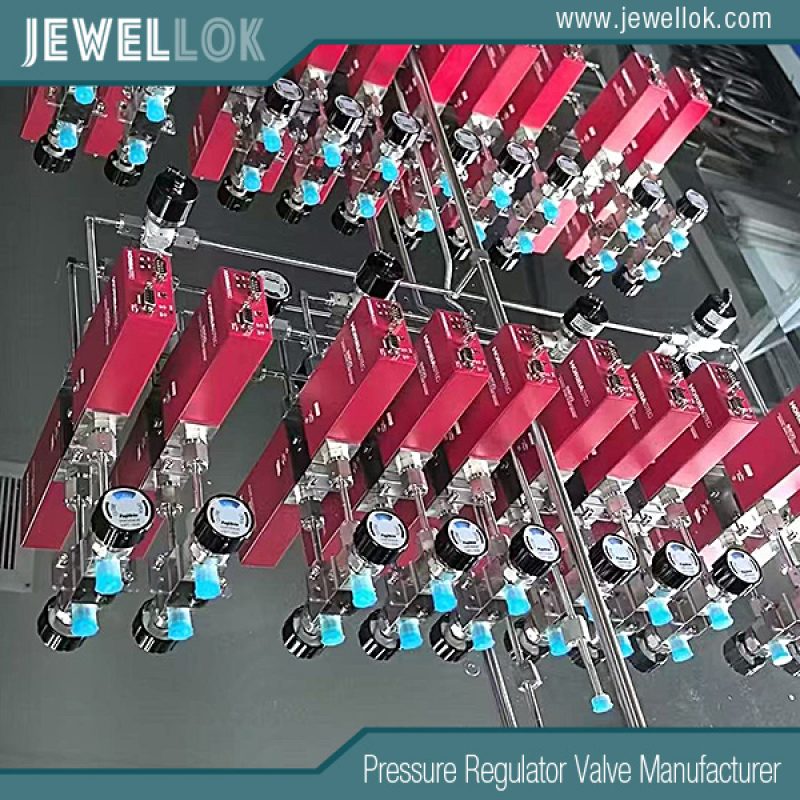
Safety or Relief Valves: Essential Guardians of Pressure Systems
- Pressure Regulator Valve Manufacturer
- 1/2 gas pressure regulator, 2 inch irrigation solenoid valve, adjustable propane regulator, adjusting propane regulator, argon gas pressure regulator, argon hose fitting, characteristics of pressure, chinese propane gas cylinder, Diaphragm Valve Manufacturers, fusible plug, gas filter, gas manifold system, gas regulator, gas used in semiconductor manufacturing, high pressure flexible hose, how a solenoid valve works, how does pressure regulator work, hydraulic regulator, industrial grade purity, industrial regulators, low pressure regulator, oxygen regulator gauge, pressure gauge manufacturers, pressure relief valve vs safety relief valve, quick connect valve, relief vs safety valve, Safety and Relief Valves, safety or relief valves, safety or relief valves factory, safety or relief valves manufacturer, safety or relief valves market, safety or relief valves supplier, safety or relief valves systems, safety relief valve vs pressure relief valve, safety valve and relief valve difference, safety valve vs relief valve, solenoid valve for ammonia gas 1 inch pipe, solenoid water valve, stainless pressure regulator, water solenoid valve 24v
- No Comments
Safety or Relief Valves: Essential Guardians of Pressure Systems
In industries where pressure systems are a cornerstone—such as oil and gas, chemical processing, power generation, and manufacturing—safety and relief valves stand as critical safeguards against catastrophic overpressure events. These valves are engineered to automatically release excess pressure from vessels, pipelines, or other pressurized systems when it surpasses a predetermined threshold. By doing so, they protect equipment, the environment, and, most crucially, human lives.
Though the terms “safety valve” and “relief valve” are often used interchangeably, they serve distinct purposes. Safety valves are typically designed for gas, vapor, or steam services and feature a rapid, full-opening action—often called “pop” action—to provide swift pressure relief. Relief valves, conversely, are used in liquid services and open gradually in proportion to the pressure increase, offering a more controlled release. Together, these devices ensure that pressure systems operate within safe limits, preventing explosions, equipment damage, and potential loss of life.
This article explores the workings of safety and relief valves, their various types, and their wide-ranging applications across industries. We’ll also examine key design considerations, best practices for installation and maintenance, relevant regulatory standards, common troubleshooting techniques, and emerging trends in valve technology.
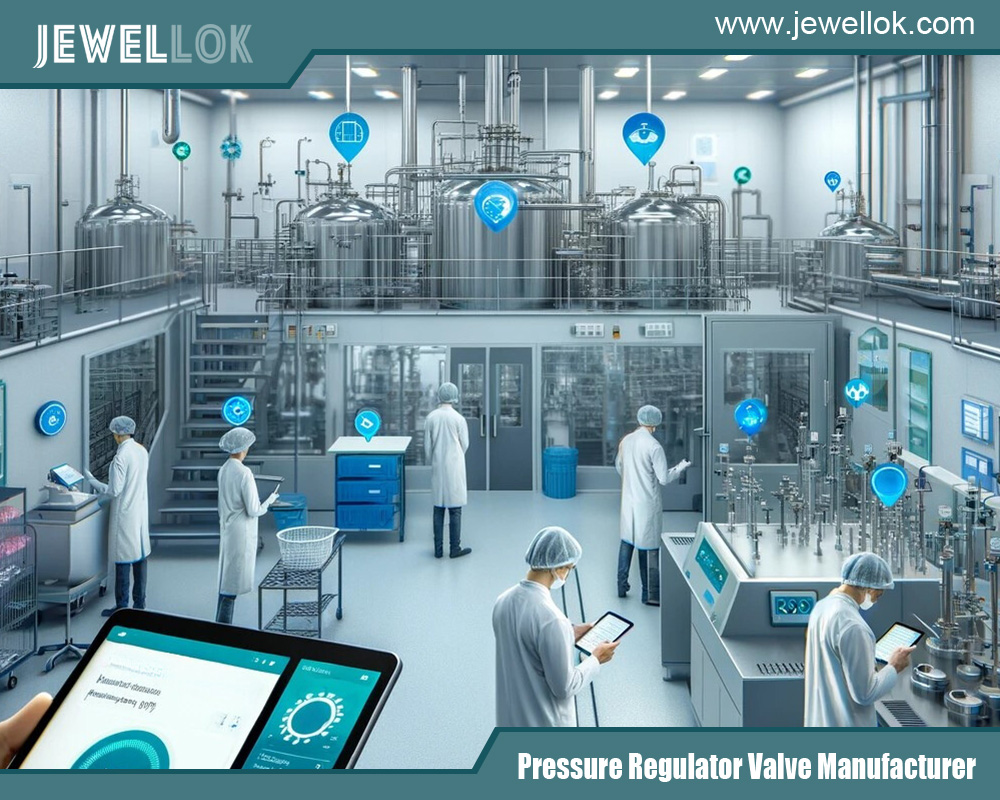
How Safety and Relief Valves Work
Safety and relief valves function by balancing forces to manage pressure. Their primary components include a valve seat, disc, spring, and adjustment mechanism, though designs may vary based on application.
In a spring-loaded safety or relief valve, the disc is pressed against the seat by a spring calibrated to exert a force corresponding to the desired set pressure. When the system pressure exceeds this set point, the fluid’s force overcomes the spring, lifting the disc and allowing fluid to escape through the outlet. This release reduces the system pressure to safe levels.
- Safety valves, used for compressible fluids like steam or gas, open fully and rapidly when triggered. They remain open until the pressure drops to a predefined level—known as the blowdown pressure—then close quickly.
- Relief valves, designed for incompressible fluids like liquids, open gradually as pressure rises, with the flow rate proportional to the pressure increase, ensuring controlled relief.
More advanced designs, such as pilot-operated safety relief valves, use a smaller pilot valve to control the main valve’s operation. These are ideal for applications requiring precise control or high flow rates.
Key Components:
- Nozzle: The inlet where fluid enters.
- Disc: Seals against the nozzle to prevent flow.
- Spring: Holds the disc in place until the set pressure is reached.
- Adjustment Screw: Sets the spring tension to the desired pressure.
- Bonnet: Encloses the spring and adjustment mechanism.
In safety valves, a huddling chamber may enhance the lifting force once the valve begins to open, ensuring full pop action. Relief valves, however, are designed for proportional opening, often with a different disc and seat configuration.
Types of Safety and Relief Valves
Safety and relief valves come in various types, each tailored to specific fluids, pressures, and applications:
- Spring-Loaded Safety Valves:
- Common in steam, gas, and vapor systems.
- Feature rapid pop action for quick relief.
- Available in conventional or balanced bellows designs (to handle backpressure).
2. Spring-Loaded Relief Valves:
- Used for liquid systems.
- Open gradually based on pressure increase.
- Typically have lower capacity than safety valves.
3. Pilot-Operated Safety Relief Valves:
- Combine a main valve and a pilot valve.
- Offer precise control and high capacity.
- Suitable for both gas and liquid services.
4. Dead-Weight Safety Valves:
- Use weights instead of springs for closing force.
- Ideal for low-pressure applications like storage tanks.
- Simple but limited in scope.
5. Rupture Discs:
- Non-reclosing devices that burst at a set pressure.
- Require replacement after activation.
6. Vacuum Relief Valves:
- Prevent vacuum conditions by allowing air or gas into tanks when internal pressure drops.
7. Temperature and Pressure (T&P) Relief Valves:
- Respond to both pressure and temperature.
- Common in water heaters.
The choice of valve depends on factors like fluid type, operating conditions, and regulatory requirements. For instance, a steam boiler might use a spring-loaded safety valve, while a hydraulic system would rely on a relief valve.
Applications of Safety and Relief Valves
Safety and relief valves are vital across numerous industries:
- Boilers and Pressure Vessels: Protect power plants and industrial steam systems from overpressure.
- Oil and Gas: Safeguard pipelines, refineries, and offshore platforms handling hydrocarbons.
- Chemical and Petrochemical Plants: Manage pressure in reactors, distillation columns, and hazardous chemical storage.
- Pharmaceutical and Food Processing: Ensure safety in pressure cookers and autoclaves.
- HVAC Systems: Relief valves prevent excessive pressure in refrigeration units.
- Water Heaters: T&P valves guard against overpressure and overheating.
- Aerospace and Defense: Used in hydraulic and pneumatic systems.
- Marine Industry: Critical for shipboard pressure systems.
In these applications, valves must be carefully sized and selected to match the system’s maximum pressure and flow requirements, often with redundant valves for added safety.
Design Considerations for Safety and Relief Valves
Selecting and designing a valve involves several key factors:
- Set Pressure: The point at which the valve opens, set below the system’s maximum allowable working pressure (MAWP).
- Capacity: Must handle the required flow rate to prevent pressure buildup.
- Blowdown: The pressure drop needed for the valve to close (typically 3-5% of set pressure for safety valves).
- Overpressure: The allowable pressure increase during discharge (often 10% above set pressure).
- Temperature: Influences material choice and valve performance.
- Backpressure: Downstream pressure that can affect operation, mitigated by balanced designs.
- Fluid Properties: Dictates material compatibility (e.g., corrosive fluids require special alloys).
- Installation Location: Must be accessible for maintenance.
- Discharge Piping: Ensures safe fluid venting.
- Regulatory Compliance: Must meet standards like ASME or API.
Engineers use formulas from codes like ASME Section I (for boilers) or Section VIII (for pressure vessels) to size valves, ensuring they meet safety and performance needs.
Installation and Maintenance Best Practices
Proper installation and maintenance are essential for valve reliability:
Installation:
- Mount vertically for optimal performance.
- Minimize inlet piping length to reduce pressure drop.
- Direct discharge piping to safe locations, away from personnel.
- Use drip pans or drains for steam systems.
- Ensure accessibility for inspection.
Maintenance:
- Test regularly to verify set pressure accuracy.
- Inspect for corrosion, leakage, or wear.
- Check springs for fatigue and seats for damage.
- For pilot-operated valves, test the pilot assembly separately.
- Follow manufacturer maintenance schedules (often annually).
Detailed records of tests and maintenance are crucial for compliance and tracking valve performance over time.
Regulatory Standards and Codes
Safety and relief valves are governed by strict standards:
ASME Boiler and Pressure Vessel Code:
- Section I: Safety valves for boilers.
- Section VIII: Relief devices for pressure vessels.
API Standards:
- API 520: Sizing and selection guidelines.
- API 526: Flanged steel valve specifications.
- API 527: Seat tightness requirements.
- ISO 4126: Safety devices for pressure protection.
- National Board Inspection Code (NBIC): Installation and repair guidelines.
- European Pressure Equipment Directive (PED): CE marking for EU compliance.
These standards ensure valves are designed, tested, and certified to perform reliably under specified conditions.
Common Issues and Troubleshooting
Valves can encounter issues that impair their function:
- Leakage: From damaged seats or debris.
- Chattering: Rapid opening/closing due to poor sizing or installation.
- Failure to Open: Caused by corrosion or sticking components.
- Premature Opening: Resulting from spring fatigue.
- Inadequate Capacity: Unable to handle required flow.
Troubleshooting Steps:
- Inspect for physical damage or blockages.
- Test to confirm set pressure.
- Verify installation and sizing accuracy.
- Replace worn parts as needed.
- Complex issues may require expert consultation to ensure safety.
Advancements and Future Trends
Valve technology is advancing to meet modern needs:
- Smart Valves: IoT integration for real-time monitoring and predictive maintenance.
- Advanced Materials: Corrosion-resistant alloys for harsh conditions.
- 3D Printing: Precision manufacturing of complex parts.
- Enhanced Sealing: Designs to reduce leakage.
- Eco-Friendly Valves: Minimize emissions for environmental compliance.
- System Integration: Coordination with plant control systems.
These innovations enhance reliability, safety, and efficiency in pressure management.
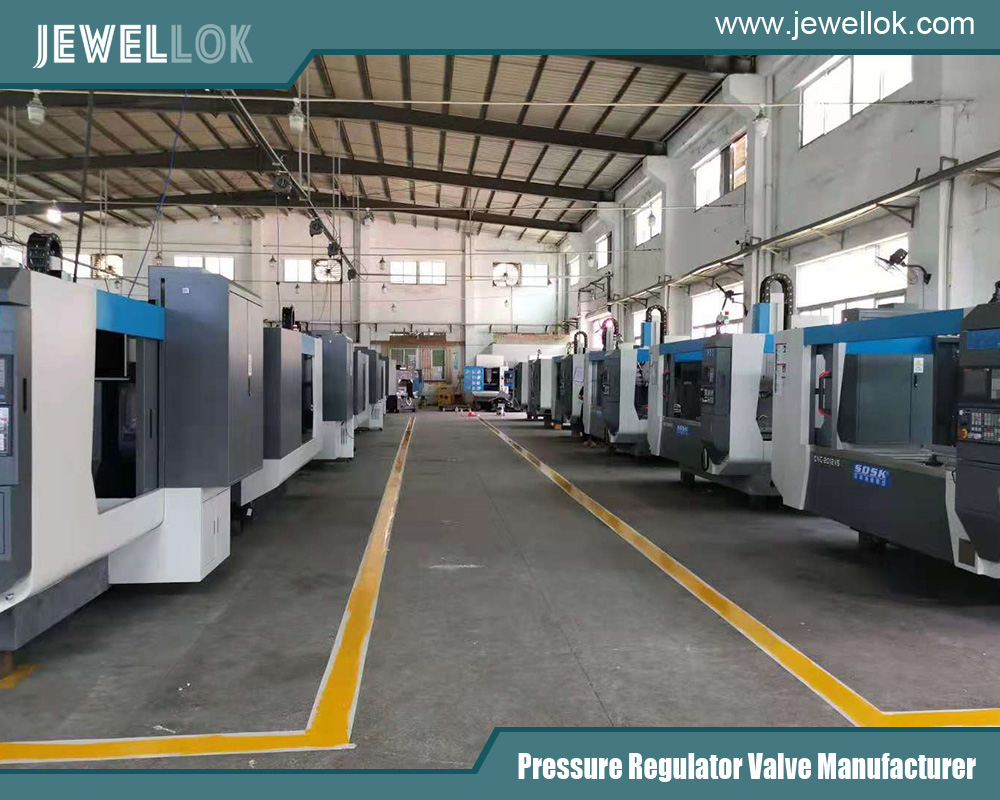
Conclusion
Safety and relief valves are indispensable for maintaining the integrity of pressure systems across industries. By understanding their operation, types, and maintenance requirements, operators can ensure these devices perform when needed most. Compliance with standards and adoption of new technologies will further strengthen their role as guardians of industrial safety, protecting lives and assets in an ever-evolving world.
For more about the safety or relief valves: essential guardians of pressure systems, you can pay a visit to Jewellok at https://www.jewellok.com/ for more info.
Recent Posts
Adjustable Low Pressure Propane Regulator
Pressure Control Valve Manufacturers
High Flow Needle Valves manufacturers
Tags
Recommended Products
-
UHP Metal Gasket Face Seal Fittings Vacuum Coupling Metal Face Seal Join Long Gland And Short Gland
-
Ultra High Purity Gas Delivery Systems And Liquid Chemical Delivery Systems JW-300-LDS
-
Low Pressure High Flow Line Pressure Regulators And Control Valves JSR-4L Series For Laboratory Pressure Control
-
739LF High Purity Female Adapter Tube To Pipe Fittings And Connectors
-
7102L Stainless Steel 316L SS Union Cross Ultra High Purity Long Arm Union Elbow Tee Cross Butt Weld Fittings
-
Flow Control Stainless Steel Low Pressure Manual Diaphragm Valve For High Purity And Ultra High Purity Gases
-
Stainless Steel Single Stage Semiconductor Grade Pressure Control Module Pressure Control Panels JSP-6A Series
-
316L Stainless Steel Tube Butt Weld Reducing Fittings Union Reducer RW Series Ultrahigh Purity Process