Blog
Jewellok is a professional pressure regulator and valve manufacturer and supplier.
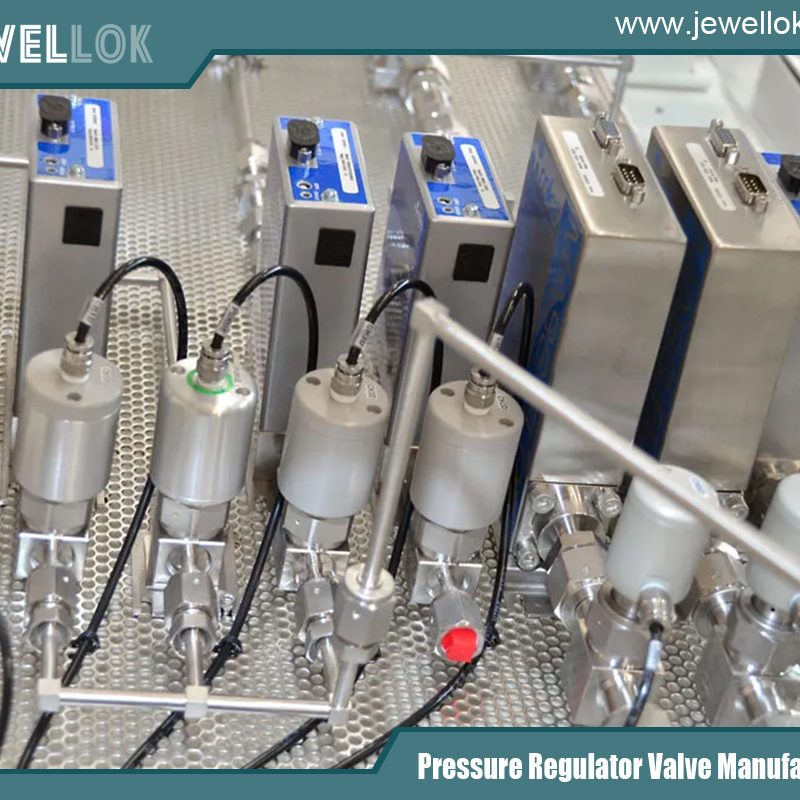
Valves for Ammonia Gas: Design, Selection, and Applications
- Pressure Regulator Valve Manufacturer
- 1 1 2 gas pressure regulator, 1 2 gas regulator, 1 2 propane regulator, 1/2 gas pressure regulator, 12v electric valve, 2 electric valve, adjustable propane pressure regulator, adjusting propane regulator, bcf connector, best Valves for ammonia gas, best Valves for ammonia gas systems, block & bleed valve, chinese propane gas cylinder, diaphram valve, double block & bleed, double block and bleed valve, double block bleed valve, electric water valve, excess flow valve, gas cylinder, gas regulator, gas used in semiconductor chip manufacturing, high pressure argon regulator, high purity regulator, how a regulator works, how a solenoid valve works, hydraulic regulator, lab fittings exporter, o ring face seal fittings, pressure gauge fitting - 3/8 qc, pressure regulator, pressure relief valve vs safety relief valve, pressure safety valve vs relief valve, propane pressure regulator valve, quick connect, quick connect valve, relief valve and safety valve difference, ultra high purity, Valves for ammonia gas, Valves for ammonia gas systems, water solenoid valve 24v, what is a flame arrestor
- No Comments
Valves for Ammonia Gas: Design, Selection, and Applications
Ammonia gas (NH₃) is a versatile compound widely used in industries such as refrigeration, agriculture, and chemical manufacturing. Its unique properties—high heat absorption, corrosiveness, and toxicity—place stringent demands on the equipment used to handle it, particularly valves. Valves for ammonia gas systems are critical components that control flow, ensure safety, and maintain system efficiency. Selecting the right valve involves understanding ammonia’s chemical behavior, operational conditions, and regulatory requirements. This article explores the types of valves suitable for ammonia gas, their design considerations, material compatibility, safety standards, and applications across industries. By examining these factors, we aim to provide a comprehensive guide for engineers, technicians, and industry professionals tasked with specifying or maintaining valves in ammonia gas systems. Proper valve selection not only enhances operational reliability but also mitigates risks associated with ammonia’s hazardous nature.
Properties of Ammonia Gas and Their Impact on Valve Selection
Ammonia gas is a colorless, pungent compound with a low boiling point (-33.34°C at standard pressure), making it ideal for refrigeration systems. However, its corrosive nature, especially in the presence of moisture, and its toxicity necessitate specialized valve designs. Ammonia can react with certain metals, such as copper and brass, leading to corrosion and system failure. Additionally, its high solubility in water can form ammonium hydroxide, which further complicates material selection.
Valves for ammonia must withstand high pressures, low temperatures, and potential chemical reactions. They must also ensure tight sealing to prevent leaks, as even small ammonia leaks can pose health risks, including respiratory irritation or, in extreme cases, fatalities. The valves must operate reliably under varying conditions, such as high-pressure refrigeration cycles or low-pressure storage systems. These properties dictate the use of robust materials and designs that prioritize safety, durability, and leak prevention.
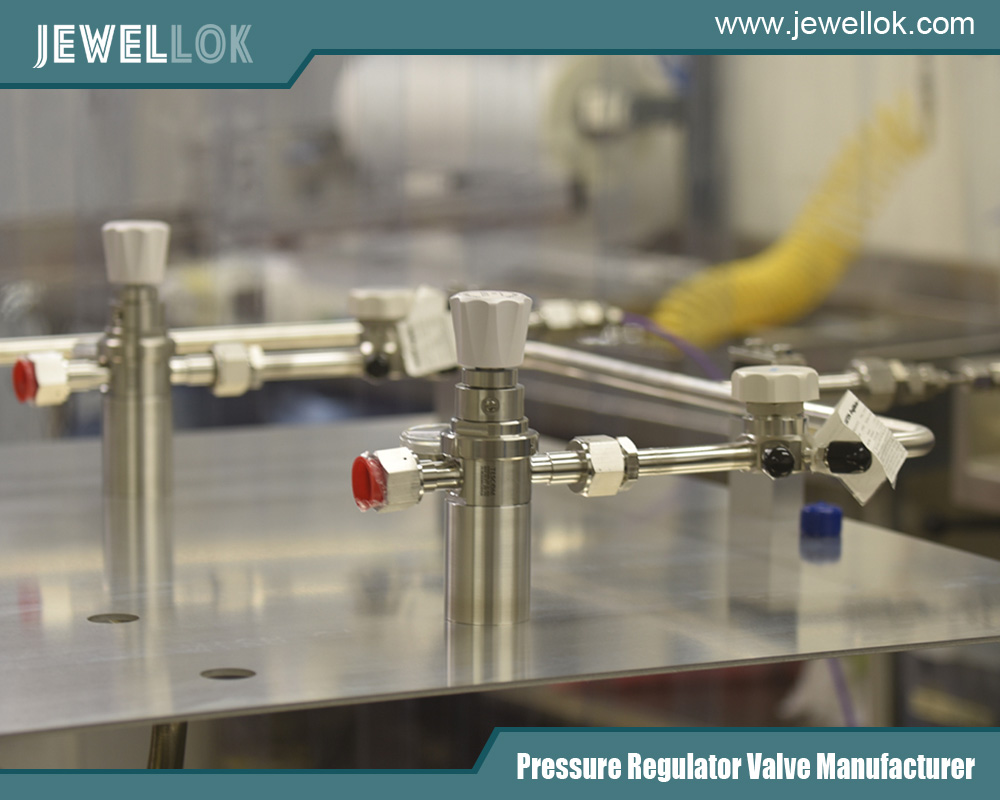
Types of Valves for Ammonia Gas
Several valve types are suitable for ammonia gas systems, each designed for specific functions within the system. Below are the most common types:
- Globe Valves: Globe valves are widely used in ammonia systems due to their excellent throttling capabilities. They provide precise flow control, making them ideal for regulating ammonia flow in refrigeration systems. Their design, however, introduces higher pressure drops, which must be considered in system design.
- Ball Valves: Ball valves offer low pressure drop and quick shut-off, making them suitable for on/off applications in ammonia pipelines. Their simple design ensures reliability, but they are less effective for throttling due to potential wear on the ball and seat.
- Gate Valves: Gate valves are used for isolation in ammonia systems. They provide minimal flow resistance when fully open but are not suitable for throttling due to potential damage to the gate under partial flow conditions.
- Check Valves: Check valves prevent backflow in ammonia systems, protecting pumps and compressors. Swing or spring-loaded check valves are common, with designs ensuring tight sealing to avoid ammonia leakage.
- Pressure Relief Valves: These safety-critical valves protect ammonia systems from overpressure. They automatically release excess pressure to prevent equipment failure or explosions, adhering to standards like ASME and IIAR.
- Solenoid Valves: Used in automated ammonia systems, solenoid valves control flow remotely. They are common in refrigeration systems for precise control of ammonia flow into evaporators or condensers.
Each valve type must be selected based on the system’s pressure, temperature, flow rate, and operational requirements. For instance, high-pressure ammonia systems may favor globe or ball valves, while low-pressure storage systems may use gate valves for isolation.
Material Selection for Ammonia Valves
Material compatibility is critical when selecting valves for ammonia gas. Ammonia is highly corrosive to copper, brass, and certain alloys, especially in moist environments. Therefore, valve materials must resist corrosion and maintain integrity under extreme conditions.
- Steel and Stainless Steel: Carbon steel and stainless steel (e.g., 316 SS) are preferred for ammonia valves due to their corrosion resistance and strength. Stainless steel is particularly suited for high-pressure systems or environments with trace moisture.
- Ductile Iron: Ductile iron is used in some ammonia valves for its durability and cost-effectiveness. It is suitable for low- to medium-pressure applications but requires coatings to prevent corrosion in moist conditions.
- Seals and Gaskets: Non-metallic components, such as seals and gaskets, must also be ammonia-compatible. Polytetrafluoroethylene (PTFE) and neoprene are commonly used due to their chemical inertness and ability to maintain flexibility at low temperatures.
- Avoiding Incompatible Materials: Copper, brass, and zinc should be avoided, as ammonia causes rapid degradation of these materials. Even trace amounts of these metals in alloys can lead to failure over time.
Material selection also depends on the operating environment. For example, valves in outdoor ammonia systems must resist environmental corrosion, while those in refrigeration systems must withstand low temperatures without embrittlement. Manufacturers often provide material compatibility charts to guide selection, ensuring compliance with standards like those from the International Institute of Ammonia Refrigeration (IIAR).
Design Considerations for Ammonia Valves
Designing valves for ammonia gas involves balancing performance, safety, and durability. Key considerations include:
- Leak Prevention: Ammonia’s toxicity demands zero-leak designs. Valves must feature robust sealing mechanisms, such as double O-rings or bellows seals, to prevent fugitive emissions.
- Low-Temperature Performance: Ammonia refrigeration systems often operate below -30°C. Valves must use materials and lubricants that remain functional at these temperatures to avoid seizing or cracking.
- Pressure Ratings: Ammonia systems can operate at pressures ranging from 50 to 300 psig or higher. Valves must be rated for the system’s maximum allowable working pressure (MAWP) to ensure safety.
- Ease of Maintenance: Valves should allow for easy inspection and repair, as ammonia systems require regular maintenance to comply with safety regulations. Designs with replaceable seats or packings reduce downtime.
- Corrosion Resistance: As ammonia can corrode certain materials, valve designs must incorporate corrosion-resistant coatings or materials, especially for components exposed to gas or moisture.
- Actuation: In automated systems, valves may require pneumatic, electric, or hydraulic actuators. These must be compatible with ammonia and capable of operating in harsh environments.
Manufacturers often design valves to meet standards like ASME B31.5 (Refrigeration Piping) and IIAR-2 (Safe Design of Ammonia Refrigeration Systems). These standards ensure valves can handle ammonia’s unique challenges while maintaining system integrity.
Safety Standards and Regulations
Safety is paramount when handling ammonia gas, and valves must comply with stringent regulations. Key standards include:
- IIAR Standards: The International Institute of Ammonia Refrigeration provides guidelines for valve design, installation, and maintenance in ammonia refrigeration systems. IIAR-2 outlines requirements for pressure relief valves and system safety.
- ASME Standards: ASME B31.5 and ASME Section VIII govern the design of piping and pressure vessels, including valves, in ammonia systems. These standards ensure valves can withstand system pressures and temperatures.
- OSHA and EPA Regulations: In the United States, the Occupational Safety and Health Administration (OSHA) and Environmental Protection Agency (EPA) regulate ammonia handling under the Process Safety Management (PSM) and Risk Management Program (RMP) frameworks. Valves must be designed to prevent leaks and ensure safe operation.
- ISO and EN Standards: In Europe and globally, standards like ISO 5149 and EN 378 specify requirements for refrigeration systems, including ammonia-compatible valves.
Compliance with these standards ensures that valves minimize risks of leaks, overpressure, or system failure. Regular inspections and testing, such as hydrostatic or pneumatic tests, are also required to verify valve performance.
Applications of Ammonia Valves
Valves for ammonia gas are used across various industries, including:
- Refrigeration: Ammonia is a preferred refrigerant in industrial systems, such as cold storage, food processing, and ice rinks. Valves control ammonia flow through evaporators, condensers, and compressors.
- Agriculture: Ammonia is used in fertilizer production and as a direct-application fertilizer. Valves regulate ammonia flow in storage tanks and distribution systems.
- Chemical Manufacturing: Ammonia is a key raw material in producing chemicals like nitric acid and urea. Valves ensure precise control in high-pressure reactors and pipelines.
- HVAC Systems: Large-scale HVAC systems may use ammonia for cooling. Valves manage flow and pressure in these systems, ensuring efficiency and safety.
Each application requires valves tailored to specific pressures, temperatures, and flow rates. For example, refrigeration systems prioritize low-temperature performance, while chemical plants demand high-pressure capabilities.
Challenges and Future Trends
Handling ammonia gas presents challenges, including corrosion, leak prevention, and compliance with evolving regulations. Valves must be designed to address these issues while maintaining cost-effectiveness. Advances in materials, such as corrosion-resistant alloys and advanced polymers, are improving valve durability. Additionally, smart valves with sensors for real-time monitoring are gaining traction, enabling predictive maintenance and leak detection.
Sustainability is also driving innovation. As industries adopt greener practices, ammonia’s role as an environmentally friendly refrigerant is expanding. This increases the demand for high-efficiency valves that minimize energy losses and emissions. Manufacturers are developing compact, low-pressure-drop designs to enhance system efficiency.
Digitalization is another trend, with automated valves integrated into IoT platforms for remote monitoring and control. These advancements improve safety and reduce operational costs in ammonia systems.
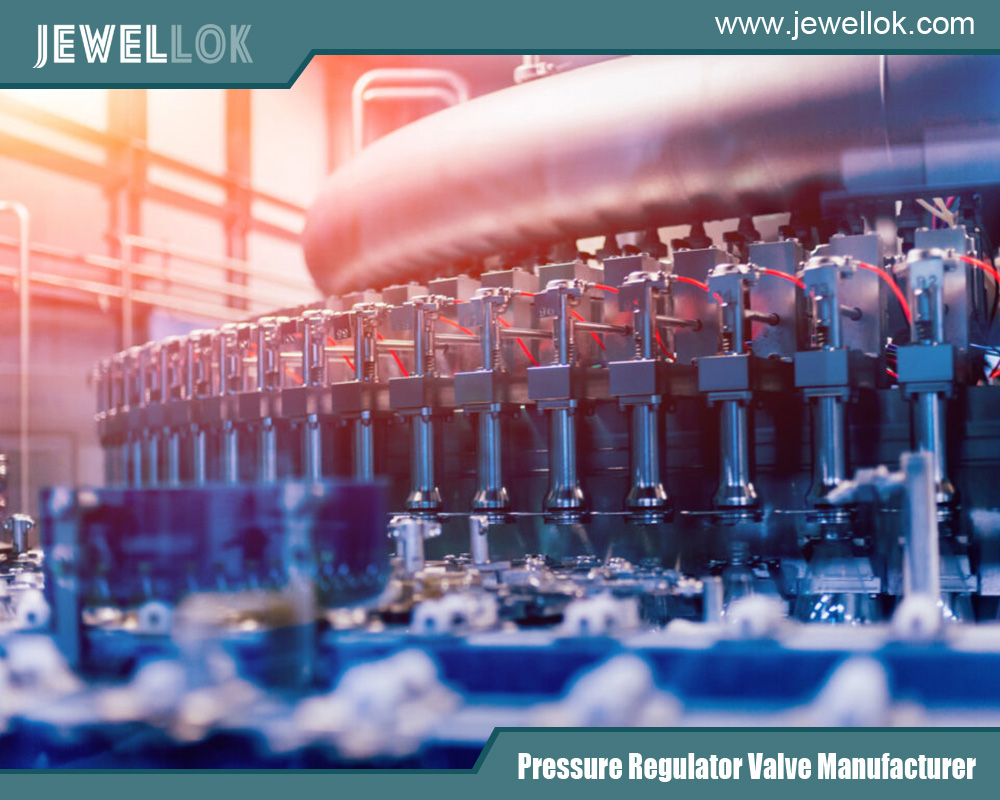
Conclusion
Valves for ammonia gas are critical components in ensuring the safety, efficiency, and reliability of systems across industries like refrigeration, agriculture, and chemical manufacturing. Their design and material selection must account for ammonia’s corrosive and toxic properties, as well as the operational demands of high pressures and low temperatures. By choosing the appropriate valve type—whether globe, ball, gate, or relief—and adhering to safety standards like IIAR and ASME, engineers can mitigate risks and optimize performance. As industries prioritize sustainability and digitalization, innovations in valve technology will continue to evolve, offering improved durability, efficiency, and safety. For professionals working with ammonia systems, understanding valve selection and maintenance is essential to achieving operational excellence and regulatory compliance. With careful planning and adherence to best practices, valves can ensure the safe and efficient handling of ammonia gas for years to come.
For more about tank pressure vs regulated pressure: understanding the differences and their impact, you can pay a visit to Jewellok at https://www.jewellok.com/ for more info.
Recent Posts
Pressure Control Valve Manufacturers
High Flow Needle Valves manufacturers
High-Pressure Hydraulic Needle Valve
Pneumatic Actuated Ball Valve
Tags
Recommended Products
-
7102L Stainless Steel 316L SS Union Cross Ultra High Purity Long Arm Union Elbow Tee Cross Butt Weld Fittings
-
775L Bulkhead Reducing Union | Stainless Steel High Purity Double Ferrule Bulkhead Reducing Unions
-
765LR Reducing Tee | Stainless Steel 316 High Purity Butt Weld Fittings Metal Face Seal For Welding Pipe Fitting Reducing Tee
-
Ultra High Purity Gas Delivery Systems And Liquid Chemical Delivery Systems JW-300-LDS
-
High Purity High Pressure Gas Cylinder Pressure Regulators Pressure Reducing Valve JSR-1E Series
-
765L Stainless Steel Union Elbow Reducing High Purity Fitting Tubing Extension Tubing Connection
-
772L Male Branch Tee | Stainless Steel High-Purity Tube Fitting Male Branch Tee
-
774L Stainless Steel UHP Fittings Butt Weld Bulkhead Union For High Flow Special Gas Fluid