Blog
Jewellok is a professional pressure regulator and valve manufacturer and supplier.
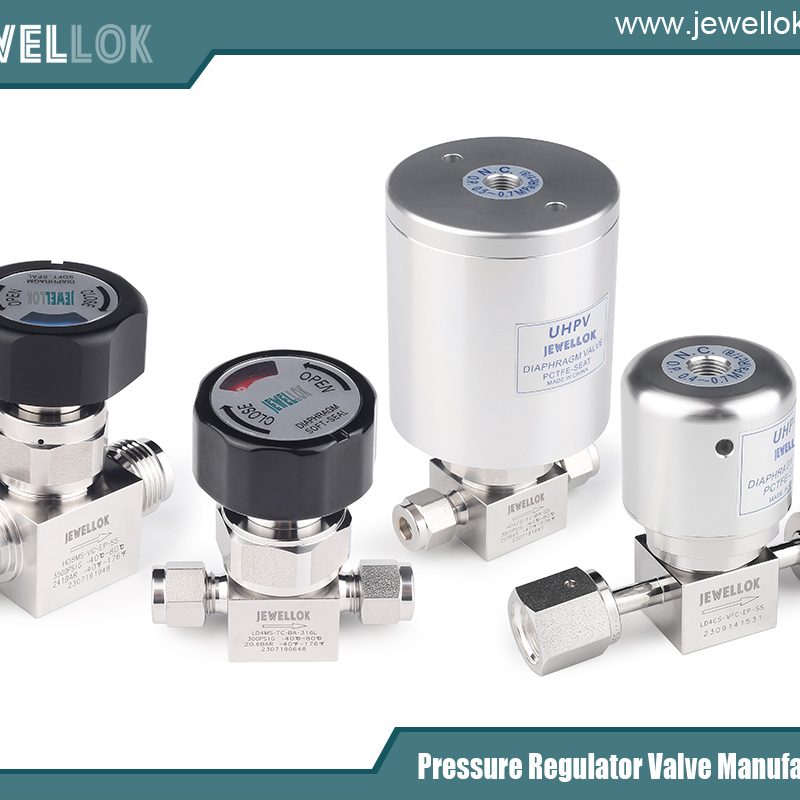
What Types of Gases Are Typically Used in Ultra High Purity Gas Delivery Systems?
- Pressure Regulator Valve Manufacturer
- China High Purity Gas System Manufacturer, gas delivery system in semiconductor, Gas delivery system Manufacturer in China, High Purity Gas Delivery Equipment, High Purity Gas Pipeline Manufacturer and Supplier in China, High purity specialty gas supply equipment, Malaysia Ultra High Purity Gas Delivery Systems, UHP Gas Distribution Panel, ultra high purity gas delivery system manufacturers in china, ultra high purity gas delivery systems in brazil, ultra high purity gas delivery systems in thailand, Ultra High Purity Gas Delivery Systems in USA, Ultra High Purity Gas Delivery Systems Malaysia, ultra high purity gas delivery systems vietnam, Ultra High Purity Gas Distribution Systems, Ultra-High-Purity Gas Delivery Systems
- No Comments
What Types of Gases Are Typically Used in Ultra High Purity Gas Delivery Systems?
Ultra High Purity (UHP) gas delivery systems are engineered to supply gases with impurity levels as low as parts per billion (ppb) or even parts per trillion (ppt). These systems are indispensable in industries where contamination can compromise product quality, process efficiency, or safety. Semiconductor manufacturing, pharmaceuticals, biotechnology, and advanced research laboratories are prime examples of fields that rely on UHP gases. This article explores the types of gases typically used in these systems, categorized by their properties and applications, and underscores why purity is a non-negotiable requirement. From inert gases that stabilize environments to reactive gases that drive chemical processes, and specialty gases tailored for niche uses, each type plays a critical role in modern technology and science.
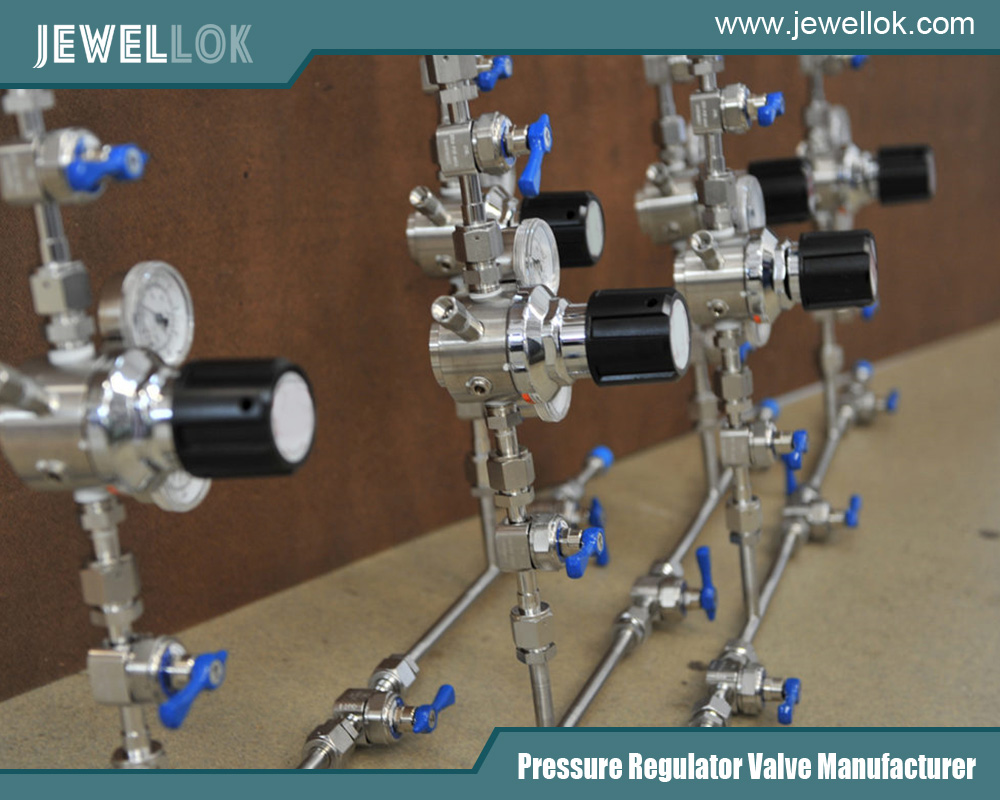
Introduction to UHP Gas Delivery Systems
UHP gas delivery systems are sophisticated setups designed to transport gases from their source to the point of use without introducing contaminants. Constructed with materials like electropolished stainless steel and equipped with high-purity valves and filters, these systems maintain gas integrity under stringent conditions. The importance of UHP gases lies in their applications: in semiconductor fabrication, impurities can render microchips defective; in pharmaceuticals, they can affect drug safety and efficacy. This article categorizes the gases into inert, reactive, specialty, and gas mixtures, detailing their uses and the critical need for purity in each case.
1. Inert Gases
Inert gases are prized for their chemical stability, making them ideal for applications requiring non-reactive environments. Below are the most common inert gases in UHP systems, their uses, and why purity is essential.
Nitrogen (N₂)
Nitrogen is the most widely used inert gas in UHP systems, owing to its abundance and versatility. In semiconductor manufacturing, UHP nitrogen purges vacuum chambers and maintains inert atmospheres during wafer processing, preventing oxidation that could introduce defects. In the food industry, it displaces oxygen in packaging to extend shelf life by inhibiting spoilage. Analytical labs use UHP nitrogen as a carrier gas in gas chromatography, where even trace impurities like oxygen or moisture can skew results. Purity levels must often be 99.9999% or higher to ensure process reliability.
Argon (Ar)
Argon’s density and inertness make it a staple in UHP applications. In metal fabrication, it serves as a shielding gas in welding, preventing oxidation of the weld pool for strong, defect-free joints. In analytical chemistry, UHP argon powers inductively coupled plasma (ICP) spectrometry, generating plasma to detect trace elements—impurities can destabilize this plasma, leading to errors. In semiconductors, argon is used in sputtering to deposit thin films, where its purity ensures film quality. Contaminants as low as a few ppb can compromise these processes.
Helium (He)
Helium’s unique properties—low density, high thermal conductivity, and a low boiling point—make it invaluable. In cryogenics, UHP helium cools superconducting magnets to near absolute zero, where impurities could reduce efficiency or damage equipment. As a carrier gas in gas chromatography, it ensures precise compound separation, and in leak detection, its small atomic size reveals minute flaws. Purity is critical to maintain performance, with impurity tolerances often in the ppt range.
Why Purity Matters: For inert gases, purity prevents unwanted reactions or contamination. Trace impurities can degrade product quality, reduce yields, or interfere with measurements, making UHP delivery a necessity.
2. Reactive Gases
Reactive gases participate in chemical reactions, requiring UHP delivery to ensure only intended outcomes occur. Here are key examples and their roles.
Oxygen (O₂)
Oxygen is a cornerstone reactive gas in UHP systems. In semiconductor manufacturing, UHP oxygen grows silicon dioxide layers on wafers, forming insulating films for transistors—impurities like moisture or hydrocarbons can introduce defects. In medical applications, it supports respiratory therapies and surgeries, where contaminants pose health risks. Oxygen also aids combustion processes and certain welding techniques, demanding purity for consistency and safety. Levels of 99.999% purity are typical to meet these needs.
Hydrogen (H₂)
Hydrogen’s reactivity suits it for high-precision tasks. In semiconductors, UHP hydrogen anneals silicon wafers to repair crystal defects, boosting electrical performance. As a reducing agent, it prevents oxidation in metal manufacturing, and in chemical synthesis, it drives hydrogenation reactions for pharmaceuticals and fine chemicals—purity affects yield and quality. Hydrogen also powers fuel cells, where UHP delivery ensures efficiency. Impurities can disrupt these processes, necessitating rigorous purity standards.
Chlorine (Cl₂) and Fluorine (F₂)
Chlorine and fluorine, reactive halogens, are vital in semiconductor fabrication. In dry etching, UHP chlorine and fluorine remove material from wafers to create microchip patterns—chlorine reacts with silicon, while fluorine etches silicon dioxide. Impurities can cause uneven etching or contamination, and their corrosiveness demands specialized delivery systems. Purity ensures precision and safety, with tolerances often below 1 ppb for critical applications.
Why Purity Matters: Impurities in reactive gases can alter reactions, introduce defects, or create hazards. UHP delivery ensures process control and product integrity.
3. Specialty Gases
Specialty gases serve niche, high-stakes roles, often requiring extreme purity due to their unique properties or hazards. Below are prominent examples.
Silane (SiH₄)
Silane, a pyrophoric gas that ignites in air, is used in chemical vapor deposition (CVD) to deposit silicon layers in semiconductors. Its purity is critical—oxygen or water vapor can introduce lattice defects, reducing device performance. Silane’s flammability requires UHP systems with safety features like gas cabinets, ensuring both purity and accident prevention.
Phosphine (PH₃) and Arsine (AsH₃)
Phosphine and arsine, toxic hydrides, dope semiconductors with phosphorus or arsenic to create n-type materials for transistors. Their extreme toxicity—lethal at ppm levels—demands UHP delivery with stringent safety measures. Purity ensures doping uniformity, as contaminants can affect device reliability. These gases exemplify the dual focus on purity and safety in UHP systems.
Ammonia (NH₃)
Ammonia deposits nitride films in semiconductor manufacturing, enhancing material properties, and supports chemical production like fertilizers. In UHP form, it prevents moisture or contaminants from compromising film quality or process efficiency. Its corrosiveness requires careful handling, with purity levels critical for performance.
Why Purity Matters: Specialty gases’ specific roles mean impurities can ruin outcomes—structural flaws, safety risks, or reduced yields—making UHP delivery essential.
4. Gas Mixtures
Gas mixtures, though less common, are vital in UHP systems for precision applications.
Examples and Applications
Calibration gases (e.g., helium-nitrogen) standardize instruments like mass spectrometers, requiring purity for accuracy. In semiconductors, blends like nitrogen-hydrogen support specific process steps, needing UHP delivery to maintain ratios. Medical mixtures like oxygen-helium (heliox) aid respiratory care, where purity ensures safety. These mixtures demand exact composition and freedom from contaminants.
Why Purity Matters: Impurities can shift mixture balances or introduce variability, undermining their function. UHP systems guarantee precision.
Challenges in Handling UHP Gases
Handling UHP gases requires specialized equipment—electropolished stainless steel prevents outgassing, while filters remove trace contaminants. Safety features address toxic or flammable gases, and system design minimizes dead spaces where contamination could occur. These challenges highlight the complexity of maintaining purity from source to use.
Standards and Certifications
UHP gases adhere to strict standards, such as SEMI F112 for semiconductors or ISO guidelines, defining allowable impurity levels. Suppliers provide certificates of analysis (CoA) to verify compliance, ensuring reliability and consistency across industries.
Sources and Purification
Inert gases like nitrogen are extracted from air via cryogenic distillation, while reactive and specialty gases like hydrogen or silane come from chemical synthesis. Purification methods—pressure swing adsorption, membrane separation—remove impurities, achieving UHP standards.
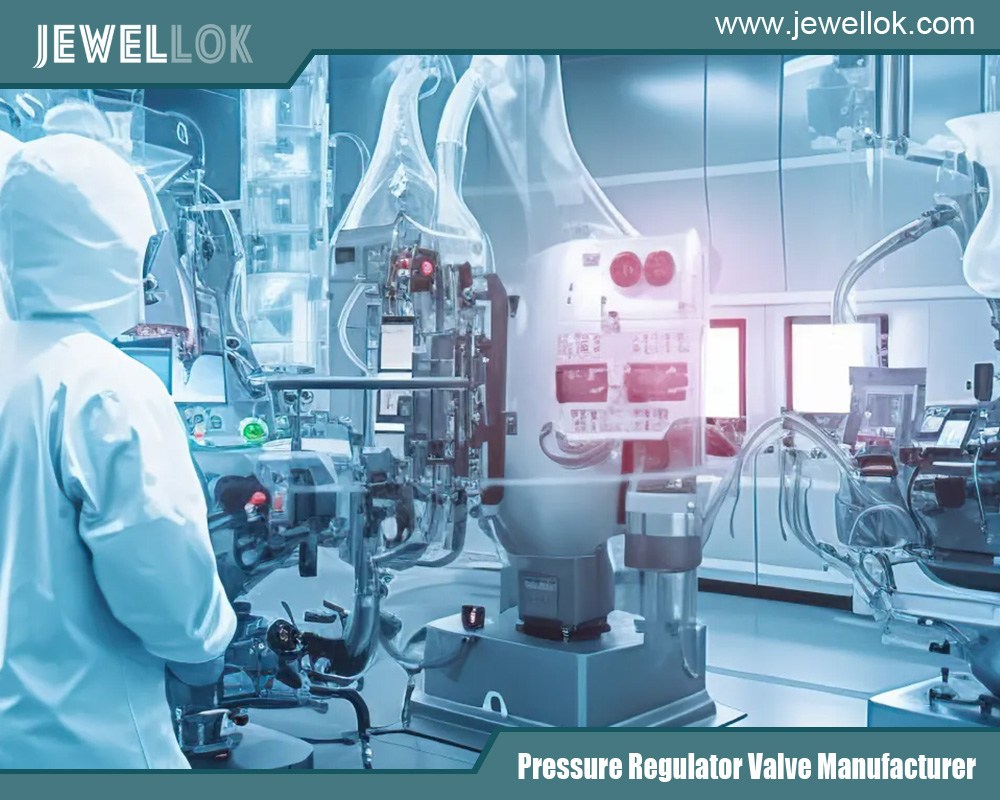
Conclusion
UHP gas delivery systems rely on inert gases (nitrogen, argon, helium), reactive gases (oxygen, hydrogen, chlorine, fluorine), specialty gases (silane, phosphine, arsine, ammonia), and gas mixtures. Each serves unique purposes—stabilizing environments, driving reactions, or enabling advanced processes—united by the need for exceptional purity. As industries like semiconductors and pharmaceuticals evolve, UHP gases and their delivery systems will remain pivotal, blending precision, safety, and innovation.
For more about what types of gases are typically used in ultra high purity gas delivery systems, you can pay a visit to Jewellok at https://www.jewellok.com/ for more info.
Recent Posts
Pneumatic Actuated Ball Valve
Industrial Diaphragm Valve
Needle Valve 10000 psi Manufacturers
Best High-Pressure Gas Regulators For Industrial Use
Tags
Recommended Products
-
High Purity Chemical Dispense System & Packing System For Semiconductors JW-200L-CDM & JW-1000L-CDM
-
767LT Reducer Pressure Reducing Valve Adjustment High purity Pressure Reducing Union Fittings And Tubing
-
JF Series In-Line Gas Filters | High Purity High Precision High Flow Semiconductor Gas Filter Gas Filtration & Purification
-
7121L Plug High Purity Plug Fitting And Blanking Plug
-
Ultra High Purity Pressure Gauge For Laboratory And Semiconductor JR Series
-
DPR1 Ultra High Purity Two Stage Dual Stage Pressure Reducing Regulator Semiconductor Grade Regulators
-
FT-BOX JW-FTB-C Valve Manifold Panels And Boxes With High Purity Configurable Systems
-
Stainless Steel High-Purity High Temperature Metal Seated Ball Valves JBV3 Series