Blog
Jewellok is a professional pressure regulator and valve manufacturer and supplier.
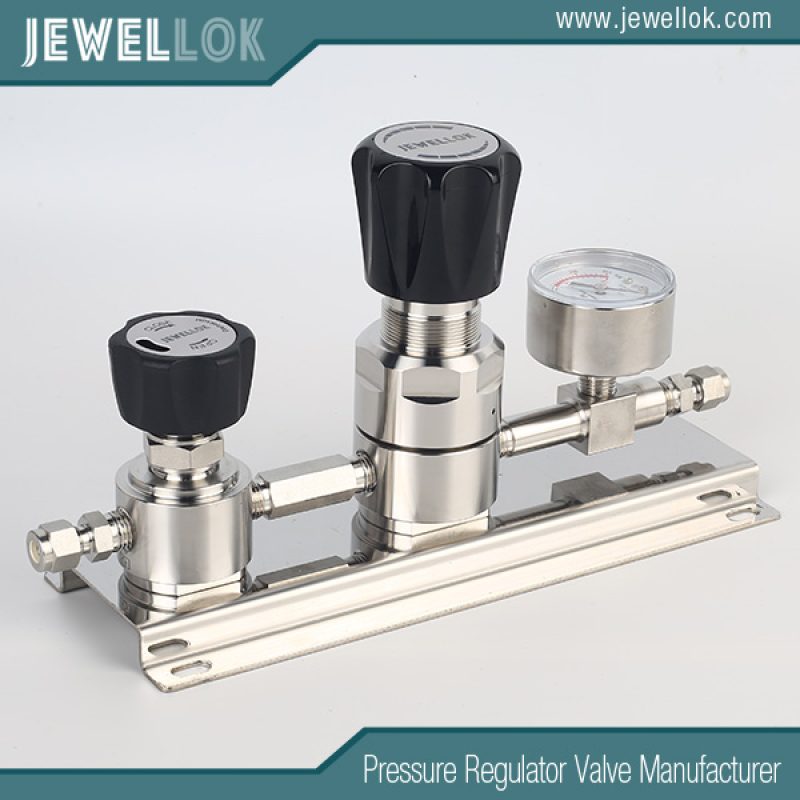
Why Is Nickel-Plated Brass Better Than Brass for Cylinder Couplings?
- Pressure Regulator Valve Manufacturer
- 1 1 2 gas pressure regulator, 1/2 gas pressure regulator, adjustable air pressure regulator, Adjustable Pressure Regulators, adjusting propane regulator, air compressor pressure regulator, Air Pressure Regulator Manufacturer, air pressure regulator with gauge, air pressure regulator with relief valve, bcf connector, block & bleed valve, chinese propane gas cylinder, cylinder coupling, cylinder coupling factory, cylinder coupling manufacturer, cylinder coupling supplier, cylinder couplings, diaphram valve, double block & bleed, double block and bleed valve, double block bleed valve, excess flow valve, fusible plug, gas regulator, high pressure flexible hose, hydraulic regulator, o ring face seal fittings, pressure gauge fitting - 3/8 qc, pressure regulator, pressure relief valve vs safety relief valve, pressure relief valve vs safety valve, pressure relief valves, pressure safety valve vs relief valve, quick connect, quick connect valve, relief valve, relief valve safety valve difference, ultra high purity, water solenoid valve 24v
- No Comments
Why Is Nickel-Plated Brass Better Than Brass for Cylinder Couplings?
Cylinder couplings are essential components in gas delivery systems, connecting gas cylinders to regulators, pipelines, or equipment to ensure safe and efficient gas flow. These couplings are used in industries such as semiconductors, hydrogen energy, chemical processing, medical gas delivery, and manufacturing, where precision, safety, and reliability are paramount. The choice of material for cylinder couplings significantly impacts their performance, durability, and compatibility with specific gases. Two common materials are brass and nickel-plated brass, with the latter gaining prominence due to its superior properties. This article examines why nickel-plated brass is better than plain brass for cylinder couplings, exploring their material characteristics, performance advantages, applications, cost considerations, regulatory compliance, and emerging trends. By understanding these differences, organizations can make informed decisions to optimize gas delivery systems and enhance operational safety and efficiency.

Understanding Cylinder Couplings and Material Requirements
Cylinder couplings, also known as cylinder valves or fittings, are mechanical connectors that interface gas cylinders with downstream systems. They must withstand high pressures, resist corrosion, ensure leak-tight seals, and maintain compatibility with a wide range of gases, from inert (e.g., nitrogen, helium) to reactive (e.g., chlorine, hydrogen). Common standards, such as CGA (Compressed Gas Association) or DIN (Deutsches Institut für Normung), specify coupling designs to ensure compatibility and safety.
The material for cylinder couplings must meet several requirements:
- Corrosion Resistance: To withstand exposure to reactive gases or humid environments.
- Mechanical Strength: To handle high pressures (e.g., up to 700 bar in hydrogen systems).
- Gas Compatibility: To prevent reactions with gases that could cause contamination or degradation.
- Durability: To ensure long-term performance under frequent use or harsh conditions.
- Sealing Integrity: To maintain leak-tight connections, critical for hazardous or ultra-high-purity (UHP) gases.
Brass, an alloy of copper and zinc, has long been a standard material for cylinder couplings due to its affordability, machinability, and corrosion resistance. However, nickel-plated brass, which adds a thin layer of nickel over the brass substrate, offers enhanced properties that make it a superior choice in many applications. Below, we compare the two materials and explore why nickel-plated brass outperforms plain brass.
Material Properties: Brass vs. Nickel-Plated Brass
Brass
Brass is a versatile alloy with the following properties:
- Composition: Typically 60–70% copper and 30–40% zinc, with trace elements like lead for machinability.
- Corrosion Resistance: Good resistance to corrosion in non-aggressive environments, but susceptible to dezincification (zinc leaching) in humid or acidic conditions.
- Mechanical Strength: Moderate strength, suitable for pressures up to 200–300 bar, depending on alloy composition.
- Machinability: Excellent, allowing precise threading and shaping for couplings.
- Gas Compatibility: Compatible with many inert and non-corrosive gases (e.g., nitrogen, helium, oxygen), but less suitable for reactive or corrosive gases (e.g., ammonia, chlorine).
- Cost: Relatively low, making it an economical choice for general-purpose applications.
- Limitations: Brass is prone to tarnishing, dezincification, and pitting corrosion in harsh environments, which can compromise sealing integrity and longevity. It also has limited resistance to high-pressure or reactive gases, restricting its use in demanding applications.
Nickel-Plated Brass
Nickel-plated brass consists of a brass substrate coated with a thin layer of nickel (typically 5–20 microns) via electroplating or electroless plating. Its properties include:
- Enhanced Corrosion Resistance: The nickel layer acts as a protective barrier, significantly improving resistance to corrosion, dezincification, and tarnishing, even in humid, acidic, or saline environments.
- Improved Surface Hardness: Nickel is harder than brass, increasing wear resistance and durability under frequent use.
- Superior Gas Compatibility: Nickel’s inert nature enhances compatibility with reactive, corrosive, or UHP gases, reducing the risk of contamination or degradation.
- Maintained Machinability: The brass substrate retains its machinability, while the nickel layer adds surface smoothness for better sealing.
- Aesthetic and Cleanability: Nickel plating provides a shiny, tarnish-resistant finish, improving aesthetics and ease of cleaning, critical for medical or UHP applications.
- Cost: Higher than plain brass due to the plating process, but still cost-effective compared to stainless steel or exotic alloys.
- Advantages: The nickel layer addresses brass’s limitations, offering superior corrosion resistance, durability, and gas compatibility while maintaining affordability .
Performance Advantages of Nickel-Plated Brass
Nickel-plated brass outperforms plain brass in several key areas, making it the preferred choice for cylinder couplings in demanding applications.
- Superior Corrosion Resistance
Corrosion is a major concern for cylinder couplings, especially in environments with high humidity, coastal conditions, or reactive gases. Plain brass is susceptible to:
- Dezincification: Zinc leaches out in acidic or saline conditions, weakening the alloy and causing leaks.
- Pitting Corrosion: Localized damage from exposure to corrosive gases like chlorine or ammonia.
- Tarnishing: Surface oxidation reduces aesthetics and can affect sealing surfaces.
Nickel-plated brass mitigates these issues:
- The nickel layer forms a durable, non-porous barrier that resists corrosion from moisture, acids, and salts.
- It prevents dezincification by shielding the brass substrate, ensuring long-term structural integrity.
- Nickel’s resistance to tarnishing maintains a clean, polished surface, reducing the risk of contamination in UHP systems.
Example: In a semiconductor fab using ammonia for nitride deposition, nickel-plated brass couplings resist corrosion better than plain brass, extending service life and maintaining purity.
- Enhanced Durability and Wear Resistance
Cylinder couplings undergo frequent connection/disconnection cycles, which can wear threading or sealing surfaces. Nickel’s higher hardness (Vickers hardness ~150–400 vs. brass’s ~80–120) improves:
- Wear Resistance: Reduces abrasion on threads and seats during repeated use, ensuring consistent sealing.
- Scratch Resistance: Protects surfaces from damage during handling or installation, critical for leak-tight performance.
- Fatigue Resistance: Enhances durability under high-pressure or cyclic loading, common in hydrogen refueling systems.
Plain brass, while durable for low-cycle applications, is softer and more prone to wear, leading to leaks or thread damage over time.
Example: In medical gas delivery systems, nickel-plated brass couplings withstand frequent cylinder changes, maintaining reliability over thousands of cycles.
- Improved Gas Compatibility
Gas compatibility is critical to prevent reactions that could contaminate the gas, degrade the coupling, or compromise safety. Plain brass is suitable for inert gases but struggles with:
- Reactive Gases: Ammonia, chlorine, or hydrogen sulfide can corrode brass, forming compounds that contaminate the gas stream.
- UHP Requirements: Brass’s surface porosity and potential for outgassing (release of trapped gases) can introduce impurities in semiconductor or medical applications.
- High-Pressure Gases: Brass may not withstand the mechanical stresses of ultra-high-pressure gases like hydrogen at 700 bar.
Nickel-plated brass excels in these scenarios:
- Nickel’s chemical inertness ensures compatibility with reactive or corrosive gases, reducing contamination risks.
- The smooth, non-porous nickel surface minimizes outgassing and particle generation, meeting UHP standards (e.g., <10 ppb impurities).
- Nickel’s strength supports high-pressure applications, maintaining integrity under extreme conditions.
Example: In hydrogen refueling stations, nickel-plated brass couplings handle high-pressure hydrogen without embrittlement or corrosion, ensuring safety and purity.
- Better Sealing and Leak-Tight Performance
Leak-tightness is critical for cylinder couplings, especially for hazardous or UHP gases. Nickel-plated brass offers:
- Smoother Surface Finish: The nickel layer reduces surface roughness (e.g., Ra < 0.4 µm), improving contact with seals or gaskets for tighter connections.
- Corrosion-Free Sealing Surfaces: Prevents pitting or degradation that could compromise seals, unlike plain brass in corrosive environments.
- Compatibility with Soft Seals: Nickel’s inertness pairs well with elastomers (e.g., PTFE, Viton), enhancing seal longevity.
Plain brass’s susceptibility to corrosion and tarnishing can degrade sealing surfaces, increasing leak risks over time.
Example: In a chemical plant handling chlorine, nickel-plated brass couplings maintain leak-tight seals, preventing toxic gas releases.
- Aesthetic and Hygienic Benefits
In applications like medical gas delivery or food processing, aesthetics and hygiene are important:
- Tarnish Resistance: Nickel-plated brass retains a shiny, polished finish, unlike brass, which tarnishes and appears worn.
- Ease of Cleaning: The smooth nickel surface resists dirt buildup and is easier to sanitize, critical for medical or UHP environments.
- Professional Appearance: Enhances equipment aesthetics, important for customer-facing applications.
Example: In hospital oxygen delivery systems, nickel-plated brass couplings ensure a clean, professional look while meeting hygiene standards.
Applications of Nickel-Plated Brass Couplings
Nickel-plated brass couplings are preferred in industries where performance, safety, and reliability are critical:
**Semiconductors **: Handling UHP gases (e.g., nitrogen, silane) for wafer fabrication, where nickel’s inertness prevents contamination.
Hydrogen Energy: Managing high-pressure hydrogen in fuel cells and refueling stations, requiring corrosion resistance and durability.
Chemical Processing: Delivering reactive gases like ammonia or chlorine, where nickel plating prevents corrosion and ensures safety.
Medical Gas Delivery: Supplying oxygen, nitrous oxide, or medical air, where hygiene and aesthetics are paramount.
Manufacturing: Controlling compressed air or inert gases in pneumatic systems, benefiting from nickel’s wear resistance.
Plain brass couplings remain suitable for less demanding applications, such as low-pressure inert gas systems (e.g., argon for welding) or non-corrosive environments, where cost is a primary concern.
Cost Considerations
While nickel-plated brass offers superior performance, it comes at a higher cost than plain brass:
- Material Cost: Nickel plating adds 10–30% to the cost of brass couplings, depending on plating thickness and process (electroplating vs. electroless).
- Manufacturing Complexity: Plating requires additional steps (surface preparation, plating, quality control), increasing production costs.
- Market Pricing: Nickel-plated brass couplings are priced higher but remain significantly cheaper than alternatives like stainless steel or Monel.
However, the total cost of ownership (TCO) often favors nickel-plated brass:
- Longer Lifespan: Reduced corrosion and wear extend service life, lowering replacement frequency.
- Lower Maintenance: Fewer repairs or leaks due to corrosion resistance and durability.
- Improved Safety: Prevents costly incidents (e.g., gas leaks, contamination) in hazardous or UHP applications.
- Regulatory Compliance: Ensures adherence to standards, avoiding fines or downtime.
Example: In a semiconductor fab, nickel-plated brass couplings for silane delivery cost 20% more than brass but last twice as long, saving $50,000 annually in maintenance and downtime.
Action: Evaluate TCO by comparing upfront costs, maintenance, and replacement intervals, prioritizing nickel-plated brass for high-risk or UHP applications.
Regulatory and Industry Standards
Cylinder couplings must comply with standards to ensure safety and interoperability:
- CGA Standards: Specify coupling designs (e.g., CGA 350 for hydrogen, CGA 580 for nitrogen) and materials for gas compatibility. Nickel-plated brass meets CGA requirements for reactive and UHP gases.
- ISO 5145: Governs cylinder valve outlets globally, recommending corrosion-resistant materials like nickel-plated brass for hazardous gases.
- ASME B31.3: Mandates material compatibility for process piping, favoring nickel-plated brass in corrosive environments.
- NFPA 55: Requires safe materials for compressed gas systems, particularly hydrogen, where nickel plating enhances safety.
- FDA/USP: For medical gas systems, nickel-plated brass’s hygiene and cleanability align with regulatory requirements.
- Action: Verify that couplings meet relevant standards (e.g., CGA, ISO) and maintain compliance documentation for audits.
Challenges and Considerations
While nickel-plated brass is superior, some challenges remain:
- Cost Sensitivity: In low-budget applications, plain brass may be preferred despite its limitations.
- Plating Quality: Poorly applied nickel layers can peel or crack, reducing benefits. Electroless plating offers uniform coverage but is costlier.
- Allergic Reactions: Nickel can cause skin reactions in medical or consumer applications, though this is rare for cylinder couplings.
- Alternative Materials: Stainless steel or exotic alloys (e.g., Hastelloy) may be required for extreme conditions, limiting nickel-plated brass’s use.
Solutions:
- Conduct cost-benefit analyses to justify nickel-plated brass for high-value applications.
- Partner with reputable suppliers to ensure high-quality plating (e.g., ASTM B733 standards).
- Use stainless steel for extreme cases, reserving nickel-plated brass for cost-effective, moderate-to-high-risk scenarios.
Emerging Trends
The gas industry is evolving, influencing material choices for cylinder couplings:
- Smart Couplings: IoT-enabled couplings with sensors monitor pressure, leaks, or corrosion, with nickel-plated brass offering durability for sensor integration.
- Sustainable Materials: Eco-friendly plating processes (e.g., trivalent chromium alternatives) reduce environmental impact while maintaining performance.
- Hydrogen Economy: Rising demand for hydrogen systems drives adoption of nickel-plated brass for its high-pressure compatibility and corrosion resistance.
- Miniaturization: Compact couplings for portable or small-scale systems benefit from nickel’s wear resistance and smooth finish.
- Impact: These trends reinforce nickel-plated brass’s role as a versatile, high-performance material.
Case Studies
- Semiconductor Fab (Taiwan): A fab switched to nickel-plated brass couplings for silane delivery, reducing contamination incidents by 50% and extending coupling life by 3 years compared to plain brass.
- Hydrogen Refueling Station (Germany): Nickel-plated brass couplings handled 700-bar hydrogen, resisting corrosion and ensuring leak-tight performance, saving €20,000 annually in maintenance.
- Medical Gas System (USA): A hospital adopted nickel-plated brass for oxygen couplings, meeting FDA hygiene standards and improving aesthetics, with zero failures over 5 years.
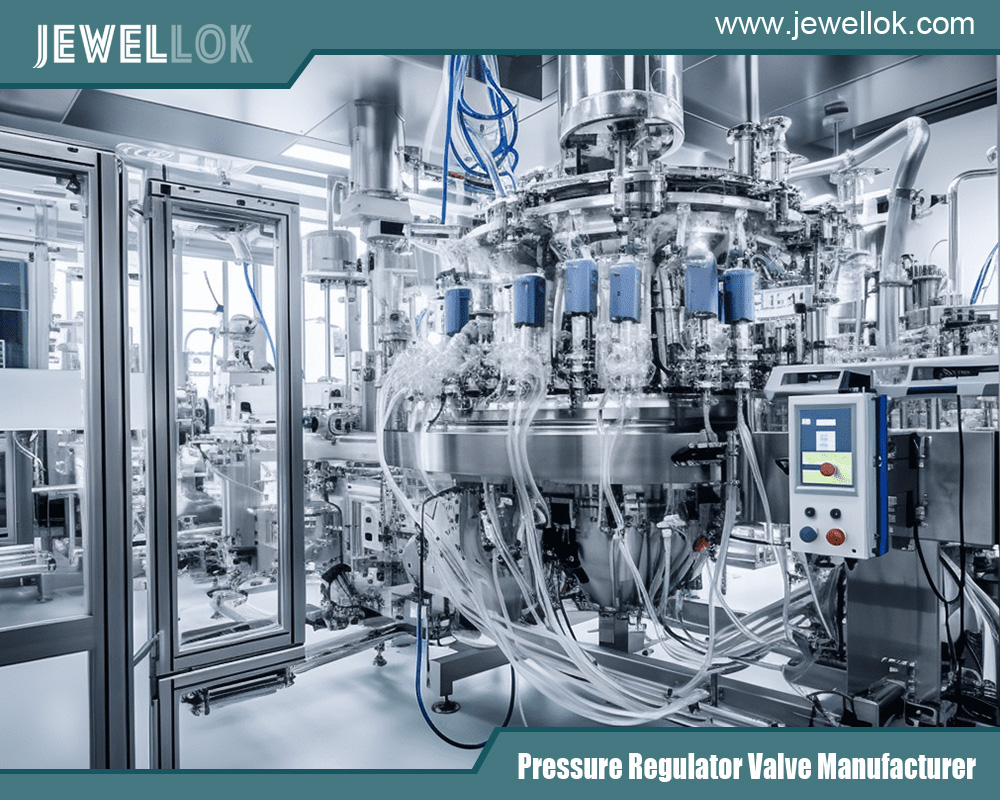
Conclusion
Nickel-plated brass is superior to plain brass for cylinder couplings due to its enhanced corrosion resistance, durability, gas compatibility, sealing performance, and aesthetic benefits. The nickel layer addresses brass’s limitations—dezincification, tarnishing, and reactivity—making it ideal for demanding applications like semiconductors, hydrogen energy, chemical processing, and medical gas delivery. While plain brass remains suitable for low-cost, non-corrosive systems, nickel-plated brass offers a compelling balance of performance and affordability, especially when total cost of ownership is considered. Compliance with standards like CGA, ISO, and NFPA further supports its use in safety-critical systems. As industries embrace trends like the hydrogen economy, smart systems, and sustainability, nickel-plated brass will continue to play a pivotal role in gas delivery systems. By choosing nickel -plated brass for cylinder couplings, organizations can enhance safety, reliability, and efficiency, ensuring robust performance in the most challenging environments.
For more about why is nickel-plated brass better than brass for cylinder couplings?, you can pay a visit to Jewellok at https://www.jewellok.com/ for more info.
Recent Posts
Tags
Recommended Products
-
JR1000 Series UHP Ultra High Purity Single Stage Pressure Reducing Regulator And Low To Intermediate Flow
-
T-BOX JW-TB-C Special Gas Delivery System Gas Valve Manifold Boxes
-
Stainless Steel High-Purity High Temperature Metal Seated Ball Valves JBV3 Series
-
High Purity Bulk Specialty Gas Pressure Control And Filtration Bulk Gas Skid Systems JW-300-BSGS
-
Pressure Control Panels For High Purity Gas Control System JSP-3AE Series From Pressure Control Panels Suppliers And Manufacturer
-
Semi Automatic Oxygen Nitrogen Helium Argon Gas Changeover Manifold Manual Gas Changeover Manifold Panel For Gas Cylinders
-
765L Stainless Steel Union Elbow Reducing High Purity Fitting Tubing Extension Tubing Connection
-
771L Male Run Tee | Stainless Steel High Quality High Purity Male Run Tee Branch Tee Pipe Fittings