Blog
Jewellok is a professional pressure regulator and valve manufacturer and supplier.
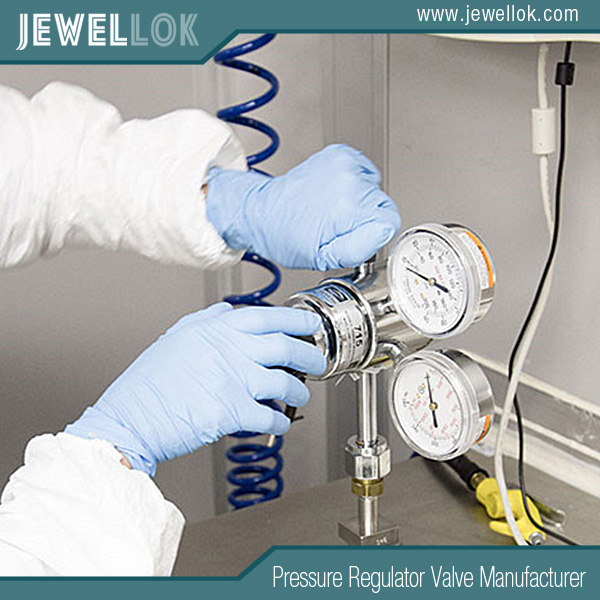
Analysis of Materials for Ultra High Purity Diaphragm Valves: Meeting the Requirements of High Purity Medium Transportation and Stringent Industry Standards
- Pressure Regulator Valve Manufacturer
- adjusting propane regulator, argon hose fitting, bcf connector, block & bleed valve, characteristics of pressure, chinese propane gas cylinder, diaphram valve, double block & bleed, double block and bleed valve, double block bleed valve, excess flow valve, fusible plug, gas regulator, gas used in semiconductor manufacturing, high pressure flexible hose, how a solenoid valve works, hydraulic regulator, industrial grade purity, o ring face seal fittings, pressure gauge fitting - 3/8 qc, pressure gauge manufacturers, pressure relief valve vs safety relief valve, quick connect, quick connect valve, safety relief valve vs pressure relief valve, solenoid valve for ammonia gas 1 inch pipe, solenoid water valve, ultra high purity, ultra high purity diaphragm valve, ultra high purity diaphragm valve factory, ultra high purity diaphragm valve hotsale, ultra high purity diaphragm valve manufacturer, ultra high purity diaphragm valve OEM, ultra high purity diaphragm valve wholesale, water solenoid valve 24v
- No Comments
Analysis of Materials for Ultra High Purity Diaphragm Valves: Meeting the Requirements of High Purity Medium Transportation and Stringent Industry Standards
In many fields of modern industry, such as food, pharmaceuticals, semiconductors, etc., the accurate transportation and processing of high-purity media are of vital importance. The ultra high purity diaphragm valve, as a key device, the selection of its materials plays a decisive role in ensuring the valve’s performance in these applications. It not only needs to have excellent corrosion resistance to withstand the erosion of various chemical substances but also meet the requirement of extremely low extractability to avoid contaminating the high-purity medium, thus meeting the ultra-high purity requirements of various industries.
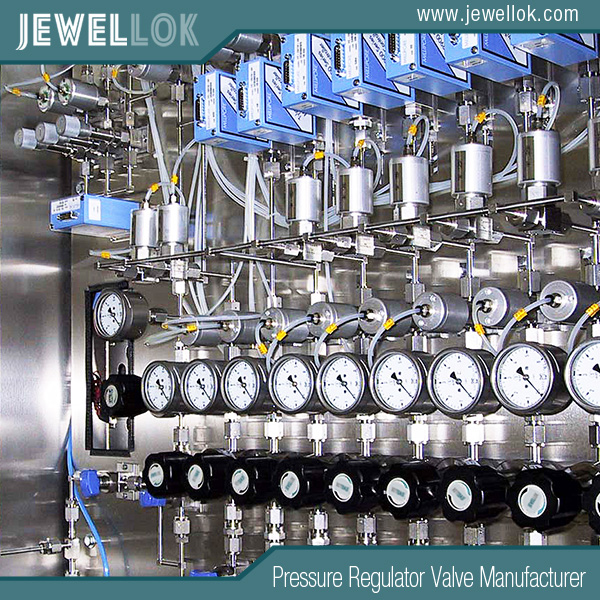
Special Materials Commonly Used in Ultra High Purity Diaphragm Valves
Valve Body Materials
- 316L VIM – VAR Stainless Steel: In ultra high purity diaphragm valves, 316L VIM – VAR (Vacuum Induction Melting – Vacuum Arc Remelting) stainless steel is a commonly used material for the valve body. It has an extremely low impurity content, especially harmful elements such as sulfur and phosphorus, which greatly improves the purity of the material. Its excellent corrosion resistance enables it to work stably in a variety of corrosive environments. In food processing, when dealing with food raw materials containing acids or alkalis, and in the pharmaceutical industry when in contact with various chemical reagents and drug solutions, it can effectively prevent the valve body from being corroded. Its good mechanical properties ensure the structural stability of the valve under different working pressures and temperatures. Even in extreme working conditions of high pressure and high temperature, it can ensure the normal operation of the valve without deformation or damage.
- Special Alloys: In addition to 316L VIM – VAR stainless steel, some special alloys are also applied to the valve bodies of ultra high purity diaphragm valves. These alloys are usually developed for specific highly corrosive or high-temperature environments. By adding specific elements such as nickel, chromium, molybdenum, etc., the corrosion resistance and high-temperature resistance of the alloys are enhanced. Some alloys can still maintain good strength and toughness at high temperatures and are suitable for high-temperature process steps in semiconductor manufacturing. At the same time, they have excellent resistance to some strongly corrosive gases such as chlorine gas and hydrogen fluoride.
Diaphragm Materials
- Fluoropolymers: Fluoropolymers such as polytetrafluoroethylene (PTFE), perfluoroethylene propylene (FEP), and soluble polytetrafluoroethylene (PFA) are common diaphragm materials. PTFE has extremely excellent chemical stability and hardly reacts with any chemical substances. It can withstand various corrosive media such as strong acids, strong alkalis, and strong oxidants. Its extremely low friction coefficient and good self-lubricating property enable the diaphragm to move smoothly during the opening and closing process of the valve, reducing wear and extending the service life. FEP, on the basis of maintaining the excellent chemical properties of PTFE, improves the flexibility and impact resistance of the material, making it more suitable for use in some working conditions that require frequent opening and closing. In addition to having similar chemical stability to PTFE, PFA also has better molding and processing performance, and can be used to manufacture diaphragms with high precision and complex shapes to meet the needs of different valve designs.
- Metal Materials: In some occasions where extremely high requirements are placed on sealing performance and corrosion resistance, metal materials are used as diaphragms. For example, cobalt-based superalloys have high strength and excellent corrosion resistance, and can still maintain stable performance in high-temperature and highly corrosive environments. In the atomic layer deposition (ALD) process of semiconductor manufacturing, the cobalt-based superalloy diaphragm can withstand the erosion of high-temperature and high-concentration precursor gases, ensuring the sealing performance and reliability of the valve, thus guaranteeing the precision and quality of the chip manufacturing process.
Valve Seat Materials
- Fluoroplastics: Fluoroplastics, especially PFA, are ideal materials for the valve seats of ultra high purity diaphragm valves. PFA has good chemical stability and can resist the corrosion of a variety of chemical substances. It has good compatibility with the fluoropolymer materials of the diaphragm, effectively reducing the wear and adhesion between the two. Its excellent resistance to expansion and anti-pollution performance enable it to maintain stable sealing performance during long-term use, and will not expand and deform due to the erosion of the medium or temperature changes, thus ensuring the sealing performance of the valve and preventing the leakage of the medium and the intrusion of external impurities.
- Ceramic Materials: In some special applications, ceramic materials are also used for valve seats. Ceramics have extremely high hardness and wear resistance and can withstand the erosion of high-velocity media and are not easily worn. Their chemical stability is also very good, and they have strong resistance to most chemical substances. In semiconductor manufacturing, when transporting high-purity gases containing particles, the ceramic valve seat can effectively resist the impact and wear of particles, ensuring the sealing performance and service life of the valve.
How the Materials Meet the High Standard Purity Requirements of the Industry
Food Industry
- Stringent Hygiene Standards: The food industry has extremely high requirements for product hygiene and safety. Any contamination by impurities may lead to food safety problems. The materials of ultra high purity diaphragm valves must comply with relevant hygiene standards, such as FDA (Food and Drug Administration) certification. The surface of the 316L VIM – VAR stainless steel valve body is processed by high-precision polishing, with an extremely low roughness. There are no gaps, welds, or grooves where bacteria and impurities can adhere, fundamentally eliminating the risk of contamination. The diaphragm made of food-grade rubber or polytetrafluoroethylene will not chemically react with food media, ensuring the purity and safety of food during transportation. The food-grade rubber diaphragm has good elastic recovery ability and can adapt to frequent opening and closing operations and the erosion of food fluids under different pressure and temperature conditions; the polytetrafluoroethylene diaphragm, with its excellent chemical stability and low friction coefficient, can still maintain stable and reliable sealing performance under complex working conditions.
- Low Extractability: To ensure the quality and safety of food, the extractables of valve materials must be controlled at an extremely low level. Under normal working conditions, these materials will hardly release any harmful substances into the food medium, ensuring the purity of the food and that its taste is not affected. Even under extreme conditions such as high temperature and high pressure, these materials can remain stable and will not decompose or release impurities.
Pharmaceutical Industry
- GMP Compliance: The pharmaceutical industry follows strict Good Manufacturing Practice (GMP) for pharmaceuticals. The design and material selection of ultra high purity diaphragm valves must meet GMP requirements. The valve materials not only need to have good corrosion resistance to adapt to the erosion of various drug solutions and chemical reagents but also be easy to clean and disinfect to ensure that no impurities or microorganisms are introduced during the pharmaceutical manufacturing process. The 316L stainless steel valve body and fluoropolymer diaphragm and valve seat can withstand the corrosion of common disinfectants and cleaning agents. At the same time, their smooth surfaces are convenient for in-line cleaning (CIP) and in-place sterilization (SIP) operations, meeting the strict requirements of the pharmaceutical industry for equipment cleaning and disinfection.
- Prevention of Cross-Contamination: In the pharmaceutical manufacturing process, preventing cross-contamination between different drugs is of great importance. The diaphragm of the ultra high purity diaphragm valve completely isolates the inside of the valve body from the outside world, avoiding the contact between the medium and the external environment, thus preventing the occurrence of cross-contamination. At the same time, the valve materials will not adsorb or retain drugs, and can be thoroughly cleaned after each use to ensure that the new drug will not be contaminated during the next use.
Semiconductor Industry
- Requirements for Ultra-Clean Environments: Semiconductor manufacturing needs to be carried out in an ultra-clean environment, and the requirements for the purity of gases and liquids are extremely high. Any tiny impurity may affect the performance and quality of the chip. The materials of ultra high purity diaphragm valves have an extremely low particle release rate, which can effectively reduce the particles generated during the opening and closing process of the valve and avoid these particles from entering the semiconductor manufacturing process and contaminating the chip. The cobalt-based superalloy diaphragm and 316L VIM – VAR stainless steel valve body, through special processing and treatment processes, can ensure that no particles are generated or released during the transportation of high-purity gases and liquids, meeting the strict requirements of the semiconductor industry for ultra-clean environments.
- Chemical Compatibility: A variety of chemical substances are used in the semiconductor manufacturing process, such as strongly corrosive etchants and high-purity gases. The materials of ultra high purity diaphragm valves must have good compatibility with these chemical substances and will not undergo chemical reactions or be corroded. The fluoropolymer diaphragm and PFA valve seat can withstand the erosion of various strongly corrosive chemical substances, ensuring the stability and reliability of the valve in the semiconductor manufacturing process and guaranteeing the smooth progress of the chip manufacturing process.
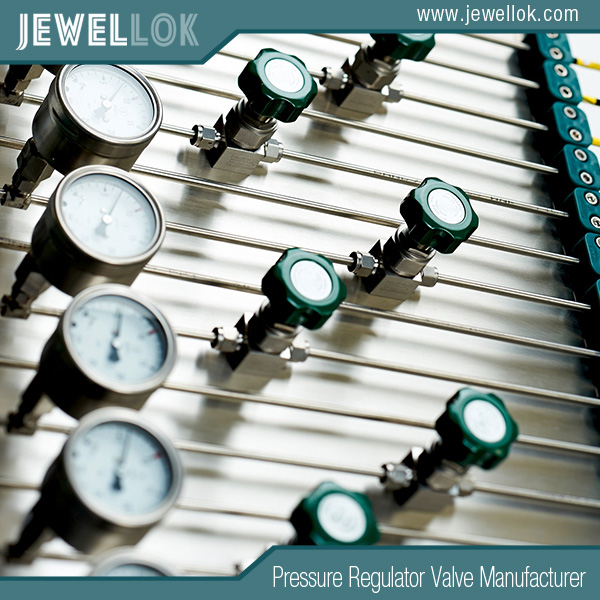
Ultra high purity diaphragm valves meet the strict requirements of the food, pharmaceutical, semiconductor, and other industries for the transportation of high-purity media by selecting special valve body, diaphragm, and valve seat materials. These materials not only have excellent corrosion resistance and low extractability but also, in their respective application fields, ensure the safety, stability, and high quality of the industry production process by meeting hygiene standards, preventing cross-contamination, and adapting to ultra-clean environments. With the continuous progress of technology and the increasing demands of the industry, the materials of ultra high purity diaphragm valves will also be continuously innovated and optimized to better serve the development of various industries.
For more about analysis of materials for ultra high purity diaphragm valves: meeting the requirements of high purity medium transportation and stringent industry standards, you can pay a visit to Jewellok at https://www.jewellok.com/ for more info.
Recent Posts
What Is A High Purity Gas Regulator?
What Is An Integrated Gas Supply System?
Stainless Steel Diaphragm Valve Manufacturer
Tags
Recommended Products
-
Stainless Steel Single Stage Semiconductor Grade Pressure Control Module Pressure Control Panels JSP-6A Series
-
High Purity Bulk Specialty Gas Pressure Control And Filtration Bulk Gas Skid Systems JW-300-BSGS
-
771LF Female Run Tee | Stainless Steel Tube Fitting Compression Fittings 1/4 In 3-Way Tee Female Run Tee
-
Ultra High Purity Pressure Gauge For Laboratory And Semiconductor JR Series
-
JF Series In-Line Gas Filters | High Purity High Precision High Flow Semiconductor Gas Filter Gas Filtration & Purification
-
771L Male Run Tee | Stainless Steel High Quality High Purity Male Run Tee Branch Tee Pipe Fittings
-
DPR1 Ultra High Purity Two Stage Dual Stage Pressure Reducing Regulator Semiconductor Grade Regulators
-
Single Stage Wall And Cabinet Mounting Pressure Control Panels JSP-2E Series For High Purity Gases