Instrumentation fittings and valves for CNG & LNG
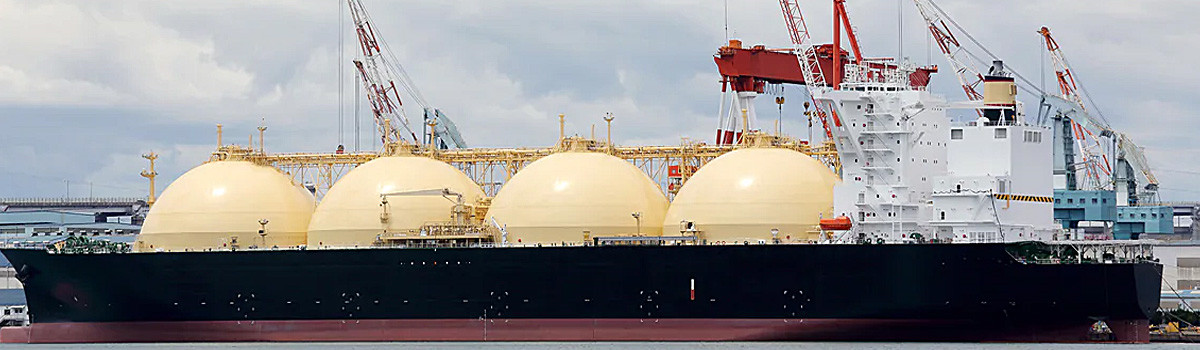
As a leading provider of valve and fitting solutions across a wide range of industries including cryogenics, chemical processing, pharmaceutical and biotechnology semiconductor manufacturing, oil and gas, defense, aerospace, and pharmaceutical and biotechnology.
Compressed natural gas (CNG) is a natural gas that has no color, odor, or corrosion under pressure. It can be used as a transportation fuel in either liquid or gas form, although most vehicles use the gas form compressed to pressures above 3,100 pounds per square inch. Liquified natural gas (LNG) is a natural gas that has been converted to liquid in order to make it easier for storage or transport.
Minimize CNG and LNG Jewellok valves and fittings are used in CNG engines, refueling station, and various systems that demand optimal performance under a variety of conditions and temperature ranges. As an industry leader, Jewellok CNG parts deliver the uncompromised performance your applications demand.
Jewellok’s LNG and CNG product line includes receptacles, ball valves, tee filters, tube fittings, and purge valves, as well as other compressed natural gas components.
These same Jewellok parts are used in dozens of industries and thousands of applications worldwide.
We only provide products that can be safely produced
Whether it is compressed natural gas or liquefied natural gas, they are flammable, explosive, highly corrosive, and have high pressure rating requirements. In order to ensure the safety of transportation, storage and use, Jewellok strongly recommends our basic tube fittings and control valves for the installation and construction of infrastructure. The materials we selected have super corrosion resistance, reasonable structure design, stable performance, convenient installation, good sealing performance and convenient maintenance in the later period, which meet the application requirements of the natural gas industry and can create a safe working environment for the natural gas industry.
Vehicle manufacturers around the world are increasingly pursuing compressed natural gas (CNG) and liquified natural gas (LNG) as viable clean fuel options to comply with strict emissions requirements.
Capitalizing on the vast business potential of CNG and LNG requires the development of high-quality fuel delivery system solutions at every level, from the fuel source to the vehicle. The componentry that makes up those systems, including pre-bent fuel lines, valves, flexible hose, measurement devices, and importantly, tube fittings, should be thoughtfully selected and specified to contribute to safe, long-term system performance.
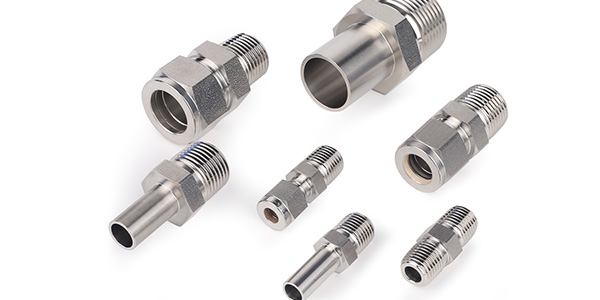
It is important for original equipment manufacturers (OEMs) involved in the assembly of CNG/LNG vehicles and the refueling infrastructure that makes their adoption possible, to select fittings that deliver the specific performance criteria required in these applications. Let’s take a closer look at some of them:
Seal TightnessSeal Tightness
CNG and LNG are stored at pressures that can exceed 275 bar (4000 psi). Any leak can pose significant safety hazards for operators. In particular, refueling stations—where ordinary end-users need to be able to fill their tanks safely and easily—must be fault-free. High-quality componentry is a necessity to make this possible.
To prevent leaks even under challenging conditions, a gas-tight seal is required. Traditional bite type and compression tube fittings, with both single- and two-ferrule designs, are suitable for many general industrial applications but may fall short in more demanding transportation applications. A fitting that creates a gas seal along multiple lines of contact can provide a more robust protection from leaks, contributing to higher levels of safety in both refueling and on-vehicle connections.
Vibration resistanceVibration Resistance
CNG fittings and LNG fittings must be able to withstand continuous vibrations associated with a moving vehicle, virtual pipeline, and compressor station. For this reason, it is important to seek fittings that demonstrate uncompromising vibration resistance.
A tube fitting featuring a two-ferrule design with hinging-colleting action can provide the vibration resistance required in transportation applications. The two-ferrule design creates a twin mechanical grip on tubing, effectively reducing the likelihood of fittings backing off, even when subjected to continuous operational vibration. This design additionally allows for a very small amount of movement in the fitting while maintaining the appropriate levels of grip and force. This movement, called “spring back,” creates robust vibration resistance, ideal for both on-vehicle operation and use within refueling infrastructure.
Thermal PerformanceThermal Performance
CNG and LNG fuel systems are subject to inherent thermodynamic challenges. For example, pressures at which CNG is stored are significantly higher than the pressures at which CNG travels from the dispenser into the on-vehicle fuel tank. As CNG depressurizes during the refueling process, the Joule-Thomson effect causes the gas temperature to drop drastically. This kind of temperature drop can also happen when compressed gas or liquid travels from the vehicle’s storage tank to the engine during operation.
All parts of the system must be able to withstand these sudden temperature changes, especially tube fittings throughout the system. Lower-quality materials may expand and contract due to temperature fluctuations, which can contribute to leaks or other forms of failure.
Corrosion resistanceCorrosion Resistance
CNG and LNG vehicles and fueling infrastructure are subject to a wide variety of environmental conditions that can contribute to corrosion. This means OEMs should seek to proactively prevent corrosion-related failures with high-quality materials of construction for every component in CNG and LNG systems.
For example, traditional carbon steel is quite susceptible to internal rusting. CNG and LNG fuels typically incorporate odorants, which better enable users to smell a leak if one happens. However, such odorants typically contain sulfur, which can contribute to premature corrosion and rusting in fuel systems. Natural gas also has an inherent humidity content that can contribute to higher corrosion levels and can become even more problematic in wetter and warmer climates. And because internal corrosion cannot be easily detected visually during general maintenance inspections, it can become a serious safety risk.
High-quality stainless steel that is formulated with higher nickel and chromium levels can more effectively combat corrosion. Lesser-quality stainless steel formulations with low nickel and chromium content are more susceptible to these kinds of corrosion issues.
Assembly and availabilityAssembly and Availability
As demand for CNG and LNG mobility solutions grows, OEMs should be prepared to quickly deliver reliable products. Constructing high-quality systems quickly and dependably, however, can be a challenge. Consider the potential complexity of a CNG system layout, which can become particularly challenging for technicians who are not highly skilled in making tube fitting connections. Simplified installation is an important characteristic in your choice of tube fitting.
Fittings that have been specifically designed for high-volume fuel line production can help installers make consistent, leak-tight tube connections that resist vibration far more effectively than alternative technologies. Remember also that high-volume production is about more than easy assembly. OEMs aspiring to maintain aggressive production schedules need suppliers that can provide local inventory of components and that take the time to understand and work around OEMs’ production needs. This kind of localized parts availability also provides OEMs with access to safety stock to help manage fluctuations in demand.
CheckmarkAn Ideal Fitting for CNG and LNG Applications
To succeed in the CNG and LNG market, OEMS need tube fitting technology that meets the demanding performance criteria of these fuel systems.
One option developed specifically to meet the requirements of alternative fuel transportation applications is the Swagelok® assembly-by-torque (AbT) fitting. Featuring an advanced-geometry, hinging-colleting back ferrule tube fitting design, the patented fitting allows for assembly by torque, which provides consistent leak-tight performance. In addition, AbT fitting assembly can be accomplished quickly and easily, and the fittings provide excellent gas-tight sealing, tube-gripping action, and vibration fatigue resistance even after repeated reassembly.