Blog
Jewellok is a professional pressure regulator and valve manufacturer and supplier.
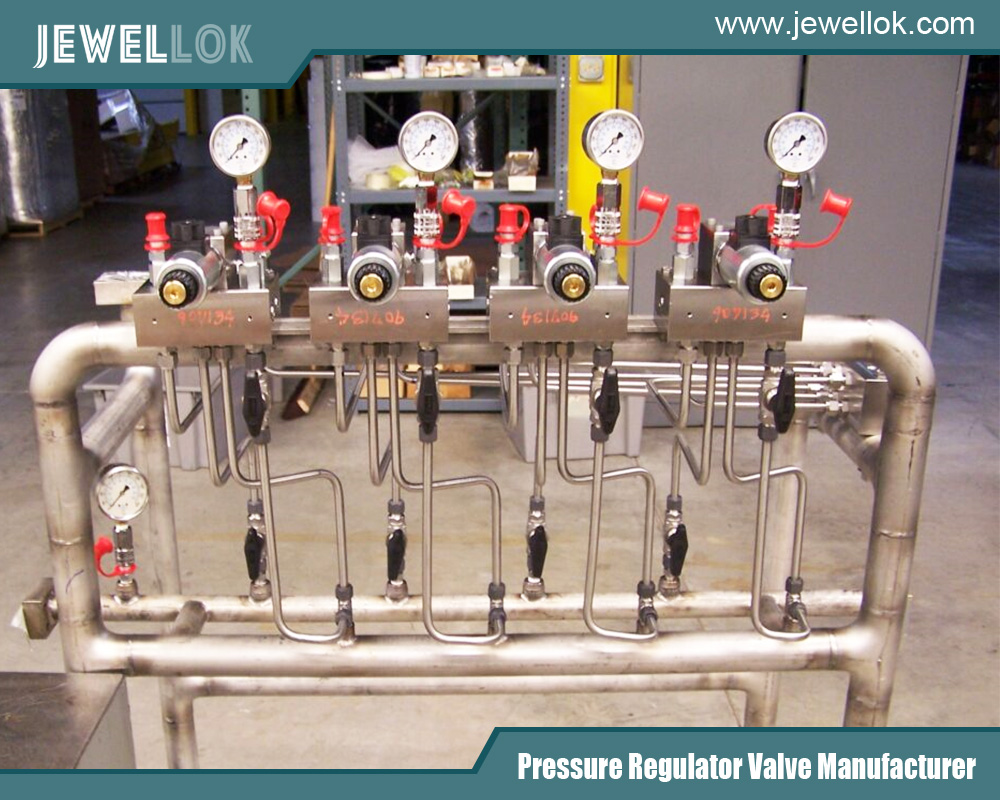
Design and Manufacturing Technologies of Ultra-High Purity Diaphragm Valves to Reduce Particle Generation and Release
- Pressure Regulator Valve Manufacturer
- adjusting propane regulator, argon hose fitting, bcf connector, block & bleed valve, characteristics of pressure, chinese propane gas cylinder, diaphram valve, double block & bleed, double block and bleed valve, double block bleed valve, excess flow valve, fusible plug, gas filter, gas regulator, gas used in semiconductor manufacturing, high pressure flexible hose, how a solenoid valve works, hydraulic regulator, industrial grade purity, low pressure regulator, o ring face seal fittings, pressure gauge fitting - 3/8 qc, pressure gauge manufacturers, pressure relief valve vs safety relief valve, quick connect, quick connect valve, safety relief valve vs pressure relief valve, solenoid valve for ammonia gas 1 inch pipe, solenoid water valve, stainless pressure regulator, ultra high purity, Ultra High Purity Diaphragm Valves, ultra high purity diaphragm valves manufacturer, ultra high purity diaphragm valves supplier, ultra-high purity diaphragm valves factory, water solenoid valve 24v
- No Comments
Design and Manufacturing Technologies of Ultra-High Purity Diaphragm Valves to Reduce Particle Generation and Release
In industries with extremely high requirements for medium purity, such as semiconductor, pharmaceutical, and biotechnology industries, ultra-high purity diaphragm valves are widely used in the conveying systems of ultra-high purity media. The production processes in these industries are extremely sensitive to the purity of the medium. Even a tiny amount of particle contamination may lead to a decline in product quality, a reduction in production efficiency, and even serious safety issues. For example, in semiconductor chip manufacturing, tiny particles may cause short circuits or other performance defects in the chips, significantly increasing the defective product rate. In the pharmaceutical industry, particle contamination may affect the safety and effectiveness of drugs. Therefore, how to effectively reduce the generation and release of particles inside ultra-high purity diaphragm valves has become a key technical issue in the field of valve design and manufacturing.
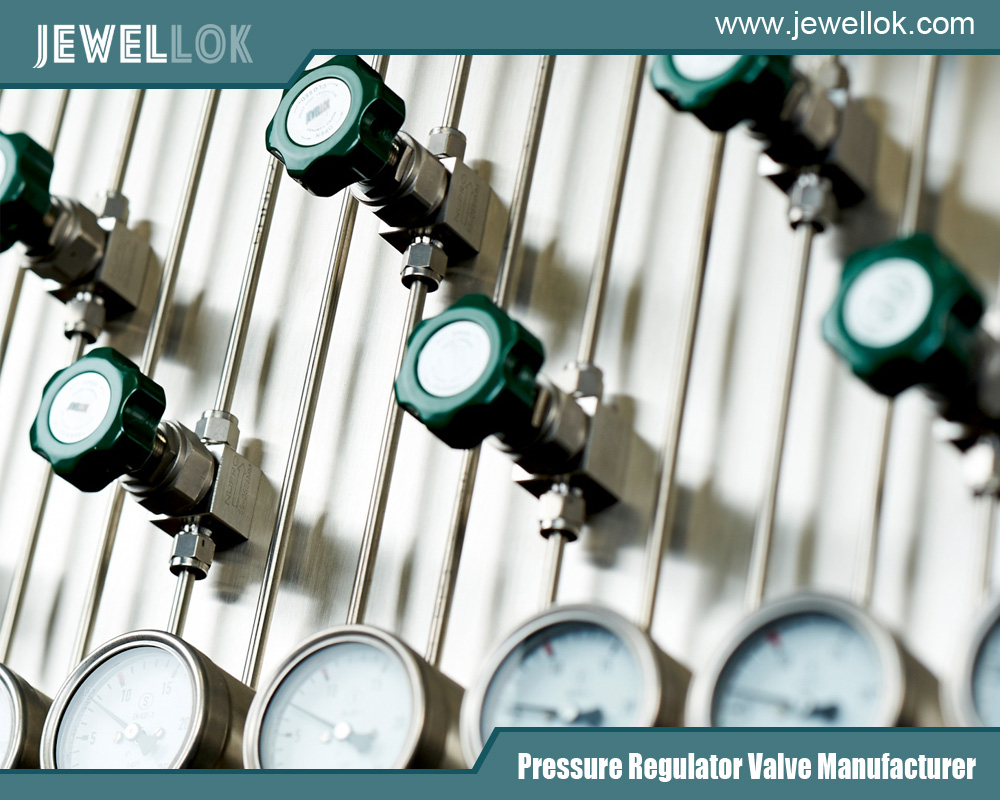
Working Principle and Structural Characteristics of Ultra-High Purity Diaphragm Valves
I. Working Principle
Ultra-high purity diaphragm valves control the flow of fluid through the movement of the diaphragm. When the valve is opened, the diaphragm moves upward or to one side, allowing the fluid to pass through the valve body flow channel. When the valve is closed, the diaphragm closely adheres to the valve seat to prevent the fluid from flowing. As a key component of the valve, the diaphragm not only plays the role of isolating the medium from other components but also directly participates in the fluid control process.
II. Structural Characteristics
- Valve Body: It is usually made of high-quality materials such as 316L VIM-VAR stainless steel, which has good corrosion resistance and high strength and can withstand the pressure and chemical effects of the conveyed medium. The design of the valve body should ensure a smooth flow channel to reduce the resistance of the fluid and the accumulation of particles.
- Diaphragm: It is made of special materials, such as cobalt-based superalloys, fluororubber, polytetrafluoroethylene (PTFE), etc. These materials have excellent corrosion resistance, flexibility, and fatigue resistance, and can effectively isolate the medium from the external environment to prevent impurities from entering.
- Valve Seat: It generally uses fluoride coatings or special plastic materials, such as fluorinated high-purity PFA (perfluoroalkoxy resin), to ensure good sealing performance and chemical compatibility and reduce the generation and release of particles.
- Actuating Mechanism: It includes manual, pneumatic, or electric actuation methods to control the movement of the diaphragm. The design of the actuating mechanism should ensure accurate and smooth operation and avoid the shedding of particles caused by excessive impact or vibration.
Analysis of the Causes of Particle Generation and Release
I. Material Wear
- Friction between the Valve Body and the Diaphragm: During the opening and closing process of the valve, there will be friction between the diaphragm and the valve body. Long-term friction may cause the wear of the diaphragm material and generate tiny particles. For example, when the flexibility of the diaphragm is insufficient or the matching accuracy with the valve body is not enough, the friction will be intensified.
- Contact Wear between the Valve Seat and the Diaphragm: When the valve is closed, the diaphragm is in close contact with the valve seat. During frequent opening and closing operations, the friction between the two may also cause material wear and release particles.
II. Corrosion Effects
- Chemical Corrosion of the Medium: Ultra-high purity media often have strong chemical activity and may cause corrosion to the metal components of the valve. For example, some corrosive gases or liquids may react chemically with the valve body material, causing corrosion pits or peeling on the metal surface and generating particles.
- Electrochemical Corrosion: When there are different metal materials or contact between metal and non-metal materials inside the valve, in the presence of an electrolyte solution (such as a medium containing trace amounts of water), an electrochemical corrosion cell may be formed, accelerating the corrosion of the metal and leading to the generation of particles.
III. Processing and Assembly Defects
- Insufficient Processing Precision: During the processing of components such as the valve body and the diaphragm, if the processing precision is not enough and the surface roughness is large, there may be tiny protrusions, depressions, or burrs. These defects are likely to be washed away by the fluid during the operation of the valve, leading to the shedding of particles.
- Improper Assembly: During the valve assembly process, if the installation gap between components is unreasonable, the connection is not tight, or there is stress concentration, it may cause vibration or displacement during the operation of the valve, resulting in the generation and release of particles. For example, if the diaphragm is installed too tightly, it may cause premature damage during the working process and generate particles.
IV. Fluid Impact
- Scouring of High-Speed Fluid: When the medium flows at a relatively high speed inside the valve, it will have a scouring effect on the internal components of the valve. Especially when the valve opening is small and the flow rate is large, the impact force of the fluid may cause the tiny particles on the material surface to shed.
- Pressure Fluctuation: The pressure fluctuation in the conveying system may also have an impact on the valve. When the pressure changes suddenly, the internal components of the valve will be subjected to an instantaneous impact force, leading to the release of particles. For example, pressure surges may occur when starting and stopping the conveying pump.
Design Measures to Reduce Particle Generation and Release
I. Optimize the Valve Body Design
- Adopt a Streamlined Flow Channel: Design a smooth and dead-angle-free streamlined valve body flow channel to enable the fluid to pass through smoothly, reduce the turbulence of the fluid, and the accumulation of particles. The turning points of the flow channel should use large-radius arc transitions to avoid sharp corners.
- Reduce the Surface Roughness: Through high-precision processing technology, such as precision casting and polishing treatment after machining, the surface roughness of the valve body interior should be reduced to a minimum value. Generally, it is required to reach below Ra0.2μm, or even lower, to reduce the adhesion and shedding of particles.
- Avoid Protrusions in the Internal Structure: Unnecessary supports, ribs, and other protruding structures should be avoided inside the valve body to prevent these structures from becoming accumulation points and sources of particles.
II. Improve the Diaphragm Design
- Select the Appropriate Diaphragm Material: According to the characteristics of the medium and working conditions, select a diaphragm material with excellent wear resistance, corrosion resistance, and flexibility. For example, in the semiconductor industry, cobalt-based superalloy diaphragms are often used. They not only have high strength and good corrosion resistance but also can maintain stable performance under high temperature and high-frequency opening and closing operations, reducing the generation of particles.
- Optimize the Diaphragm Structure: Design a reasonable diaphragm shape and thickness distribution to ensure that the diaphragm is evenly stressed during the opening and closing process of the valve and reduce the wear and damage caused by local stress concentration. For example, adopt a diaphragm design with a gradient thickness, so that the part of the diaphragm in contact with the valve seat has sufficient strength and wear resistance, while maintaining appropriate flexibility in other parts.
- Add Diaphragm Protection Measures: A protective coating or gasket can be set on the surface of the diaphragm in contact with the valve body or valve seat, such as using a PTFE coating or a special rubber gasket to further reduce friction and wear and prevent the generation of particles.
III. Improve the Valve Seat Design
- Adopt a Self-Cleaning Valve Seat Structure: Design a self-cleaning valve seat, such as setting special grooves or protrusions on the valve seat surface. When the valve opens and closes, the movement of the diaphragm can drive the medium to scour the valve seat and remove the possibly accumulated particles.
- Improve the Sealing Performance of the Valve Seat: Optimize the shape of the valve seat and the sealing material to ensure a tight seal between the valve seat and the diaphragm and reduce the leakage of the medium and the intrusion of particles. For example, adopt metal-to-metal sealing or high-performance elastic sealing materials to improve the reliability of the seal.
- Select a Valve Seat Material with Low Particle Release: Similar to the diaphragm, the valve seat material should also be a material with low particle release, such as fluorinated high-purity PFA, etc., to reduce the possibility of particles generated by the valve seat itself.
IV. Optimize the Actuating Mechanism Design
- Adopt a Smooth Actuation Method: Give priority to pneumatic or electric actuation methods and achieve smooth control of the actuation process through the control system to avoid rapid impact and vibration of the actuating mechanism. For example, use a proportional control valve or a servo motor to control the movement speed and force of the actuating mechanism to make the opening and closing process of the diaphragm smoother.
- Reduce the Connection Clearance between the Actuating Mechanism and the Valve Body: Ensure a tight connection between the actuating mechanism and the valve body and reduce the vibration and displacement caused by excessive clearance, thereby reducing the risk of particle generation. High-precision connecting parts and seals can be used to improve the stability of the connection.
- Add a Buffer Device: A buffer device, such as a spring, a rubber pad, etc., should be set between the actuating mechanism and the diaphragm to absorb the impact force during the actuation process, reduce the damage to the diaphragm, and reduce the generation of particles.
Manufacturing Process Measures to Reduce Particle Generation and Release
I. High-Precision Processing Technology
- CNC Processing Technology: Use advanced CNC processing equipment to carry out high-precision processing of components such as the valve body, diaphragm, and valve seat to ensure that the dimensional accuracy and shape accuracy meet strict requirements. CNC processing can achieve the processing of complex shapes and ensure the consistency and repeatability of processing.
- Special Processing Technology: For some high-precision requirements that are difficult to achieve through traditional machining, special processing technologies can be adopted, such as electrical discharge machining (EDM), electrochemical machining (ECM), laser processing, etc. These processes can process materials without generating mechanical cutting force, avoiding burrs and surface damage during the processing and reducing the generation of particles.
- Grinding and Polishing Process: After the components are processed, carry out fine grinding and polishing treatment to further reduce the surface roughness. Adopt processes such as mechanical grinding and chemical mechanical polishing (CMP) to make the surface of the components reach a mirror effect and reduce the adhesion and shedding of particles.
II. Strict Material Quality Control
- Raw Material Inspection: Carry out strict inspection of the purchased raw materials, including chemical composition analysis, physical property testing, metallographic structure inspection, etc., to ensure that the raw materials meet the requirements for the use of ultra-high purity valves. For key materials, such as diaphragm materials and valve body materials, reliable suppliers should be selected and incoming inspection should be carried out.
- Material Purification Treatment: Before use, carry out purification treatment on the raw materials to remove surface impurities and pollutants. For example, carry out degreasing, pickling, passivation, and other treatments on metal materials, and carry out cleaning and drying treatments on plastic materials to reduce the particles carried by the materials themselves.
- Material Compatibility Test: During the design stage, carry out compatibility tests on various materials used in the valve to ensure that there will be no chemical reactions or mutual corrosion between different materials and avoid the generation of particles caused by material compatibility problems.
III. Clean Assembly Environment
- Dust-Free Assembly Workshop: Establish a dust-free assembly workshop and use an air purification system to control the concentration of dust particles in the workshop at an extremely low level. Generally, it is required to reach the cleanliness standard of ISO 4 or higher. Operators should wear clean clothes, gloves, and masks to avoid the particles carried by the human body from contaminating the valve components.
- Special Assembly Tools and Equipment: Use special clean assembly tools and equipment, such as oil-free pneumatic tools, anti-static tweezers, vacuum adsorption devices, etc., to avoid the pollution of the valve components by the tools and equipment themselves. The assembly tools should be regularly cleaned and maintained to ensure the cleanliness of their surfaces.
- Cleaning Measures during the Assembly Process: During the assembly process, carry out strict cleaning and inspection of each component to ensure that there are no impurities and particles attached. Use dust-free wiping cloths, high-purity cleaning agents, etc. to clean the components. At the same time, after the assembly is completed, carry out a comprehensive cleaning and inspection of the entire valve to ensure that the cleanliness inside the valve meets the requirements.
IV. Strict Quality Inspection and Verification
- Particle Counting Detection: Use equipment such as a laser particle counter to detect the number and size of particles inside the valve. After the valve is manufactured and under simulated actual working conditions, conduct tests to ensure that the generation and release amount of particles is lower than the specified standard. Generally, it is required that within a certain test time, the number of particles inside the valve does not exceed a specific value, and the particle size is not larger than the specified size.
- Sealability Detection: Use equipment such as a helium mass spectrometer leak detector to detect the sealing performance of the valve to ensure that there is no leakage under the working pressure. Leakage may cause external impurities to enter the valve, increasing the risk of particle contamination. Therefore, good sealing performance is an important guarantee for reducing the generation and release of particles.
- Life Test: Carry out a life test of the valve under simulated actual working conditions to verify the performance stability of the valve in reducing the generation and release of particles during long-term use. During the life test, regularly carry out particle counting detection and sealability detection on the valve, observe the change of the valve performance, and ensure that the valve can meet the requirements of actual use.
Conclusion
In the field of ultra-high purity medium conveying, reducing the generation and release of particles inside ultra-high purity diaphragm valves is crucial for ensuring product quality and the stability of the production process. Through optimized design, including the reasonable design of the valve body, diaphragm, valve seat, and actuating mechanism, as well as the adoption of advanced manufacturing processes, such as high-precision processing, strict material quality control, clean assembly environment, and strict quality inspection and verification, etc., the generation and release of particles can be effectively reduced, and the performance and reliability of the valve can be improved. With the continuous improvement of the requirements for medium purity in industries such as semiconductor and pharmaceutical, the design and manufacturing technology of ultra-high purity diaphragm valves will also continue to develop and innovate to meet the increasingly strict production requirements. In the future, it is also necessary to further study and explore new materials, new design concepts, and manufacturing processes, and continuously improve the performance of ultra-high purity diaphragm valves in reducing particle generation and release, providing more reliable support for the development of related industries.
For more about design and manufacturing technologies of ultra-high purity diaphragm valves to reduce particle generation and release, you can pay a visit to Jewellok at https://www.jewellok.com/ for more info.
Recent Posts
What Is A High Purity Gas Regulator?
What Is An Integrated Gas Supply System?
Stainless Steel Diaphragm Valve Manufacturer
Tags
Recommended Products
-
764L Stainless Steel Union Tee High Purity Fitting Union Tee Reducing Tubing Connection
-
Stainless Steel High Purity High Temperature Pneumatic Actuated Ball Valves JBV2 Series
-
765L Stainless Steel Union Elbow Reducing High Purity Fitting Tubing Extension Tubing Connection
-
762L Stainless Steel High Purity Union High-Purity Gas System Fittings
-
High Purity High Pressure Stainless Steel Needle Valve Natural Gas Flow Control Valve JNV Series
-
768LN Stainless Steel Male Pipe Tube Butt Weld Connector And Tube Fittings Supplier
-
739 High Purity LMR Male Adapter Tube To Pipe Fittings And Adapters
-
767LT Reducer Pressure Reducing Valve Adjustment High purity Pressure Reducing Union Fittings And Tubing