Blog
Jewellok is a professional pressure regulator and valve manufacturer and supplier.
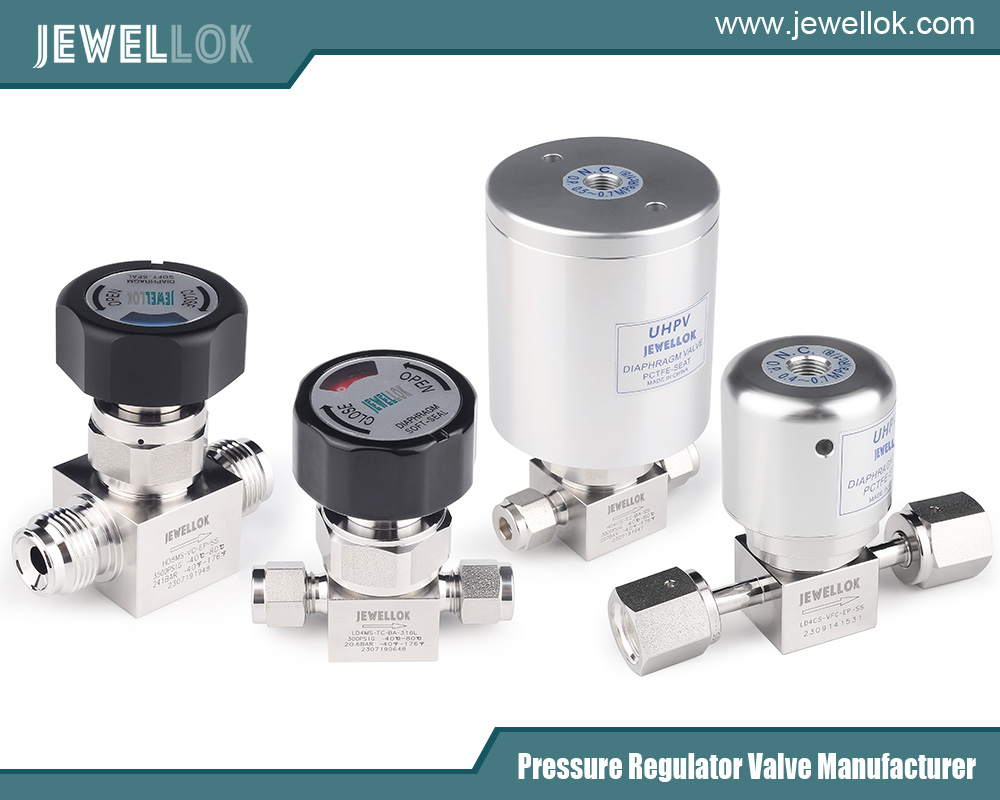
What is the difference between AP, MP, BP, and EP grade stainless steel pressure regulators?
- Pressure Regulator Valve Manufacturer
- BA grade high purity ball valves, BA Grade High Purity Gas Pressure Regulators, ba grade high purity pressure regulator, ba grade stainless steel pressure regulator, ba series high pressure valve, BA Series high purity ball valves, High Pressure Co2 Stainless Steel Pressure Regulator, high purity BA Grade pressure reducing regulator, High purity pressure gauge BA grade, OEM High Precision Ba Finishing Gas Regulator, Stainless Steel High Purity Line Pressure Regs, Stainless Steel In-Line Pressure Regulator, Stainless Steel Pressure Regulator
- No Comments
What is the difference between AP, MP, BP, and EP grade stainless steel pressure regulators?
Stainless steel pressure regulators are indispensable devices across a wide range of industries, tasked with maintaining precise control over the pressure of gases or liquids in various systems. These regulators are employed in applications as diverse as industrial manufacturing, semiconductor production, pharmaceutical processing, and food and beverage preparation. While their primary function—regulating pressure—remains consistent, the material properties of the stainless steel used in their construction, particularly the surface finish, can significantly influence their performance, durability, and suitability for specific tasks.
In this context, the terms AP, MP, BP, and EP are often interpreted as designations related to the quality or characteristics of stainless steel pressure regulators. However, there is some ambiguity in their exact meaning, as these abbreviations can have different interpretations depending on the industry or context. After careful consideration, it’s most plausible that in the context of stainless steel pressure regulators, AP, MP, BA (Bright Annealing), and EP refer to surface treatment methods applied to the stainless steel components, while BP likely stands for Back-Pressure, a specific type of regulator rather than a surface finish grade. This article will explore these interpretations, focusing primarily on how surface treatments (AP, MP, BA, and EP) affect pressure regulators, while addressing BP as a distinct regulator type, to provide a comprehensive understanding of their differences.
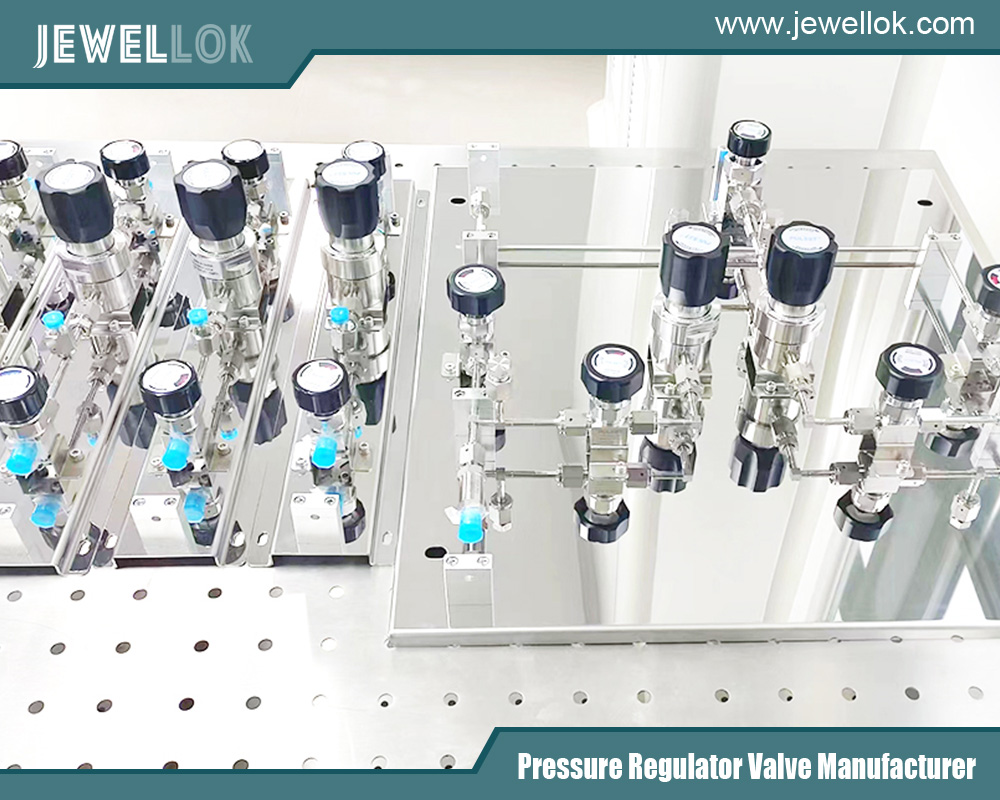
Understanding Pressure Regulators and Surface Treatments
Pressure regulators are devices designed to maintain a constant output pressure regardless of variations in the input pressure or flow demand. Made from stainless steel, they offer excellent corrosion resistance, durability, and compatibility with a wide range of media, making them ideal for both harsh industrial environments and high-purity applications.
The surface finish of the stainless steel components within a pressure regulator is a critical factor influencing its performance. The internal surfaces, which come into contact with the regulated media, can affect:
Cleanliness: Rough surfaces can trap contaminants, posing challenges in sterile or high-purity environments.
Corrosion Resistance: A smoother, passivated surface enhances stainless steel’s natural resistance to corrosion.
Flow Dynamics: Surface roughness influences how smoothly the media flows through the regulator.
Longevity: Certain treatments reduce wear and extend the regulator’s lifespan.
The designations AP (Acid Pickling), MP (Mechanical Polishing), BA (Bright Annealing), and EP (Electrolytic Polishing) refer to distinct surface treatment processes applied to stainless steel. These processes alter the surface properties, making them suitable for different applications. Meanwhile, BP is most commonly understood in the pressure regulator context as Back-Pressure, indicating a regulator type rather than a surface finish. Let’s explore each in detail.
AP (Acid Pickling) Grade Pressure Regulators
Process
Acid pickling involves immersing stainless steel components in an acidic solution, typically a blend of nitric and hydrofluoric acids. This process removes surface oxides, scale, and impurities that form during manufacturing, while also passivating the steel by promoting the formation of a protective chromium oxide layer.
Characteristics
Surface Finish: The surface is relatively rough compared to other treatments, with microscopic peaks and valleys that may remain after pickling.
Corrosion Resistance: Enhanced by passivation, though the rougher surface may be more susceptible to localized corrosion in aggressive conditions.
Cost: An economical process, making AP grade components cost-effective.
Implications for Pressure Regulators
Pressure regulators with AP-treated stainless steel components are robust and suitable for general-purpose applications where extreme cleanliness or smoothness isn’t required. The rougher surface, while clean, may trap particles or contaminants over time, limiting its use in high-purity settings.
Applications
Industrial gas systems
Water treatment facilities
General manufacturing processes
Limitations
The surface roughness can be a disadvantage in environments requiring high cleanliness, such as food processing or pharmaceuticals, where contaminants or bacteria could accumulate.
MP (Mechanical Polishing) Grade Pressure Regulators
Process
Mechanical polishing employs abrasive tools—such as polishing wheels, belts, or pads—to physically smooth the stainless steel surface. The degree of smoothness depends on the abrasive grit size and the number of polishing stages.
Characteristics
Surface Finish: Smoother than AP, with a bright, reflective appearance, though minor scratches or grooves may persist.
Corrosion Resistance: Can be compromised if the polishing disrupts the passive layer, unless followed by chemical passivation.
Cost: More labor-intensive and thus costlier than acid pickling.
Implications for Pressure Regulators
MP grade regulators offer improved aesthetics and moderate cleanliness, making them a step up from AP grade. However, the potential for residual polishing compounds or reduced corrosion resistance (without passivation) must be considered.
Applications
Food and beverage processing (non-critical areas)
Pharmaceutical intermediate stages
Decorative industrial applications
Limitations
The surface isn’t as smooth as BA or EP grades, and corrosion resistance may be lower unless additional passivation is applied, limiting its use in highly corrosive or ultra-clean environments.
BA (Bright Annealing) Grade Pressure Regulators
Process
Bright annealing heats stainless steel in a controlled, oxygen-free atmosphere (e.g., hydrogen or vacuum) and cools it rapidly. This prevents oxidation and produces a smooth, bright surface without additional mechanical or chemical treatment.
Characteristics
Surface Finish: Very smooth and reflective, free from scale or oxidation, with a mirror-like quality.
Corrosion Resistance: Excellent, as the process preserves and enhances the passive layer.
Cost: Higher due to the specialized equipment and controlled conditions required.
Implications for Pressure Regulators
BA grade regulators are well-suited for applications requiring high cleanliness and minimal particle generation. The smooth, oxide-free surface reduces contamination risks and supports consistent performance in sensitive systems.
Applications
Semiconductor manufacturing (e.g., gas delivery)
Biotechnology and pharmaceutical production
High-purity chemical processing
Limitations
While smoother than AP and MP, BA surfaces may still have minor roughness compared to EP, making it less ideal for ultra-high purity needs.
EP (Electrolytic Polishing) Grade Pressure Regulators
Process
Electrolytic polishing, or electropolishing, is an electrochemical process that removes a thin layer of material from the stainless steel surface using an electric current and electrolyte solution. This smooths the surface and enhances passivation.
Characteristics
Surface Finish: Ultra-smooth and highly reflective, minimizing roughness and particle adhesion.
Corrosion Resistance: Superior, due to the removal of impurities and the formation of a thick, uniform passive layer.
Cost: The most expensive, reflecting the precision and time involved.
Implications for Pressure Regulators
EP grade regulators offer the highest level of surface quality, making them ideal for ultra-high purity or corrosive environments where cleanliness and durability are paramount.
Applications
Semiconductor fabrication (ultra-pure gas systems)
Aerospace and defense
Medical device manufacturing
Aggressive chemical processing
Limitations
The high cost may not be justified for applications where such extreme surface quality isn’t necessary.
BP (Back-Pressure) Regulators: A Different Category
Definition
Unlike AP, MP, BA, and EP, which describe surface treatments, BP in the context of pressure regulators typically stands for Back-Pressure. A back-pressure regulator maintains a constant upstream pressure by releasing excess pressure downstream, contrasting with forward-pressure regulators that control downstream pressure.
Characteristics
Function: Controls pressure on the inlet side, venting excess to maintain system stability.
Surface Finish: Can be constructed with AP, MP, BA, or EP treated stainless steel, depending on the application’s needs.
Cost: Varies based on design complexity and material treatment.
Implications for Pressure Regulators
BP regulators serve a distinct purpose compared to standard pressure regulators. Their stainless steel components could be finished with any of the above treatments (AP, MP, BA, EP), depending on the required cleanliness or corrosion resistance.
Applications
Overpressure protection in pipelines
Gas chromatography systems
Industrial exhaust systems
Clarification
While the query lists BP as a “grade” alongside AP, MP, and EP, it’s more likely a type of regulator rather than a surface finish designation. However, a BP regulator’s performance could still be influenced by its surface treatment, aligning it with the discussion of AP, MP, BA, and EP grades.
Comparison of AP, MP, BA, and EP Grades
Here’s a detailed comparison of the surface treatment grades, excluding BP as it pertains to regulator type:
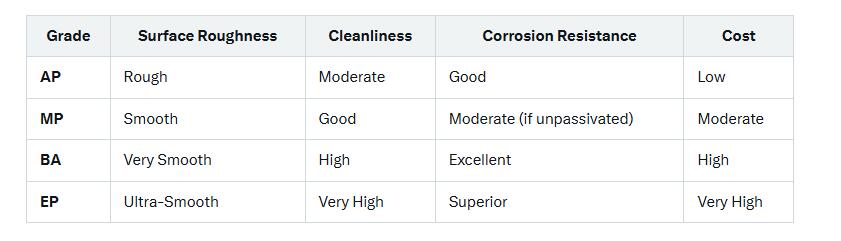
Surface Roughness: EP > BA > MP > AP (smoothest to roughest)
Cleanliness: EP > BA > MP > AP
Corrosion Resistance: EP > BA > AP > MP (assuming MP isn’t passivated)
Cost: EP > BA > MP > AP
For BP regulators, their surface finish could match any of these grades, affecting their performance similarly to standard regulators.
Applications and Selection Considerations
Choosing the right stainless steel pressure regulator depends on the application’s demands:
AP Grade: Cost-effective for general industrial use (e.g., air compressors, water systems).
MP Grade: Balances cost and cleanliness for food processing or non-critical pharmaceutical stages.
BA Grade: High-purity needs in semiconductors or biotech, where contamination must be minimized.
EP Grade: Ultra-high purity or corrosive environments, such as semiconductor gas delivery or aerospace.
BP Regulators: Used for back-pressure control, with surface finish (AP, MP, BA, or EP) chosen based on the media and environment.
Industry standards, media type, and budget also influence the decision.
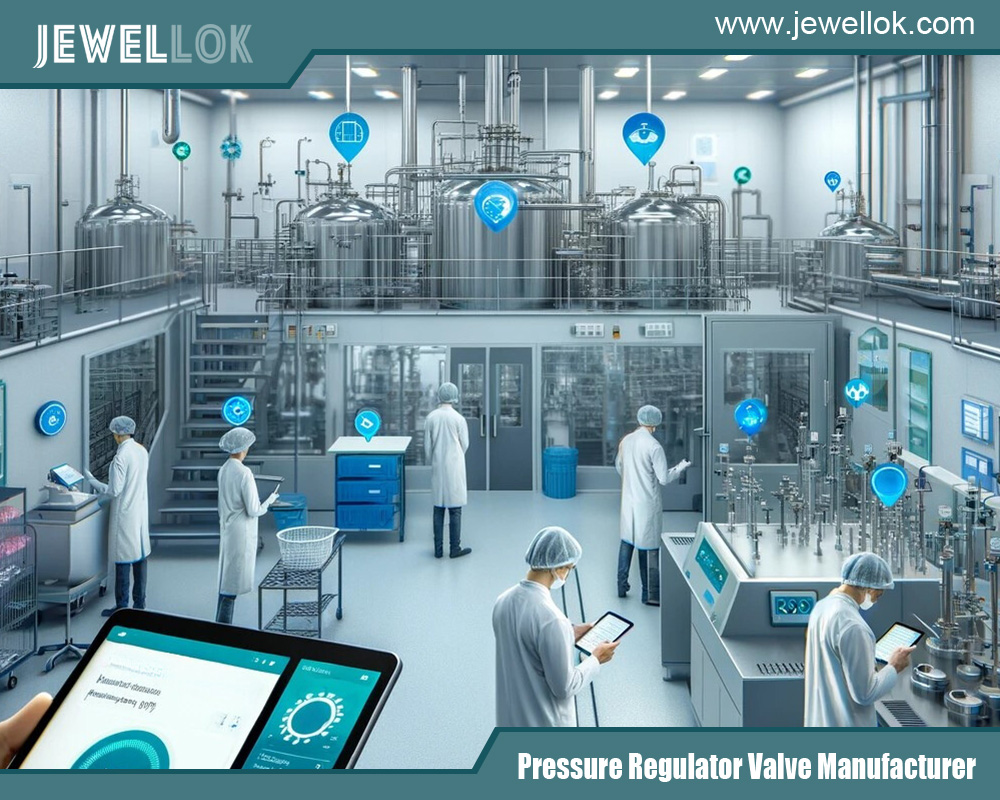
Conclusion
The differences between AP, MP, BA (not BP), and EP grade stainless steel pressure regulators stem from the surface treatments applied to their components, affecting cleanliness, corrosion resistance, and cost. AP offers an economical, rough finish for general use; MP provides a smoother, brighter surface for moderate cleanliness; BA delivers high-purity performance with a smooth, oxide-free finish; and EP excels in ultra-high purity and corrosive settings with its superior smoothness and passivation. Meanwhile, BP refers to back-pressure regulators, a functional category rather than a grade, though its components could feature any of these surface finishes.
Understanding these distinctions enables informed selection, ensuring optimal performance and reliability tailored to specific industrial or high-purity needs. Whether prioritizing cost, cleanliness, or durability, the right choice enhances system efficiency and longevity.
For more about what is the difference between AP, MP, BP, and EP grade stainless steel pressure regulators, you can pay a visit to Jewellok at https://www.jewellok.com/la/product/stainless-steel-316l-single-stage-regulator-pressure-control-panels-jsp-1e-series-for-semiconductor-fluid-control/ for more info.
Recent Posts
The Applications, Principles and Types of Water Solenoid Valve
Medical Oxygen Regulator Manufacturers in France
How Does a Bulk Specialty Gas Delivery System (BSGS) Work?
Tags
Recommended Products
-
Pressure Control Panels For High Purity Gas Control System JSP-3AE Series From Pressure Control Panels Suppliers And Manufacturer
-
Semi Automatic Gas Changeover Manifold System Manual Changeover Manifold Panel Single Stage Automatic Switchover Board
-
Semiconductor High Purity High Pressure Specialty Gas Bottle Gas Cylinder Storage Cabinet And Gas Pressure Regulating Cabinet
-
763L Stainless Steel High Purity Pressure Reducing Union Fittings And Tubing Pressure Reducing Valve Adjustment
-
764LR Stainless Steel 316 Reducing Tee UHP Fitting Automatic Buttweld Reducing Tee
-
High Purity Semi-Auto Stainless Steel Changeover Manifold System, Nitrogen High Pressure Control Panel With Semiconductor Valve Manifold Box Diaphragm Valves
-
7102L Stainless Steel 316L SS Union Cross Ultra High Purity Long Arm Union Elbow Tee Cross Butt Weld Fittings
-
Ultra High Purity Gas Delivery Systems And Liquid Chemical Delivery Systems JW-300-LDS