Blog
Jewellok is a professional pressure regulator and valve manufacturer and supplier.
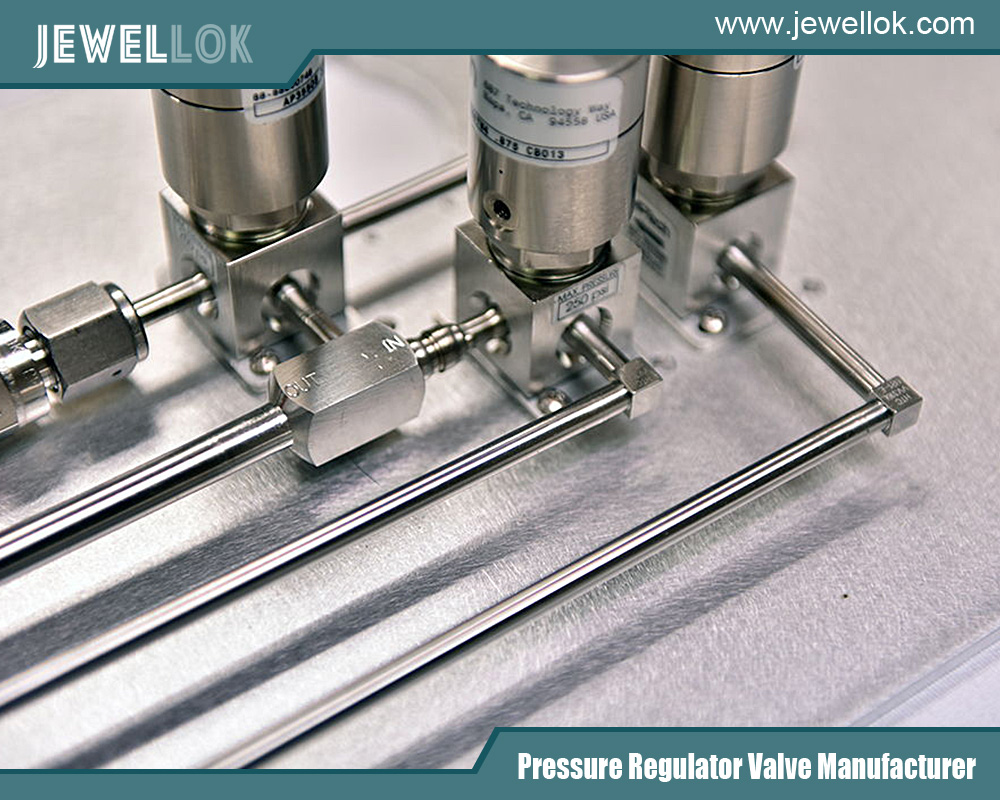
Key Applications of Ultra High Purity Diaphragm Valves in Liquid Crystal Display (LCD) Panel Manufacturing
- Pressure Regulator Valve Manufacturer
- 1 1 2 gas pressure regulator, 1 2 gas regulator, 1 2 propane regulator, 1/2 gas pressure regulator, 12v electric valve, 2 electric valve, 6mm compression union, adjustable air pressure regulator, adjustable hydraulic pressure regulator, Adjustable Pressure Regulators, adjustable propane pressure regulator, air compressor pressure regulator, air pressure regulator diagram, air pressure regulator electronic control, air pressure regulator valve with gauge, air pressure regulator with gauge, air pressure regulator with relief valve, air pressure regulator with water separator, electric water valve, gas regulator, gas used in semiconductor chip manufacturing, high pressure argon regulator, high pressure flexible hose pipe, high purity regulator, how a regulator works, lab fittings exporter, pressure regulator, pressure safety valve vs relief valve, propane pressure regulator valve, relief valve and safety valve difference, safety valve vs relief valve, semiconductor gas, Ultra High Purity Diaphragm Valves, ultra high purity diaphragm valves manufacturer, ultra high purity diaphragm valves supplier, valve manifold box, water valve timer, what is a flame arrestor
- No Comments
Key Applications of Ultra High Purity Diaphragm Valves in Liquid Crystal Display (LCD) Panel Manufacturing
In the complex and precision-intensive field of liquid crystal display (LCD) panel manufacturing, ultra high purity diaphragm valves play a pivotal role as crucial components for fluid control. LCD panel manufacturing involves a variety of high-purity and highly corrosive chemical fluids, along with stringent process requirements. Ultra high purity diaphragm valves, with their outstanding performance features such as high purity, corrosion resistance, zero leakage, and precise flow control, have become core components that ensure the smooth progress of the production process and the quality of the final products. This article will delve into the specific applications, working principles, performance requirements, and future development trends of ultra high purity diaphragm valves in the main process steps of LCD panel manufacturing.
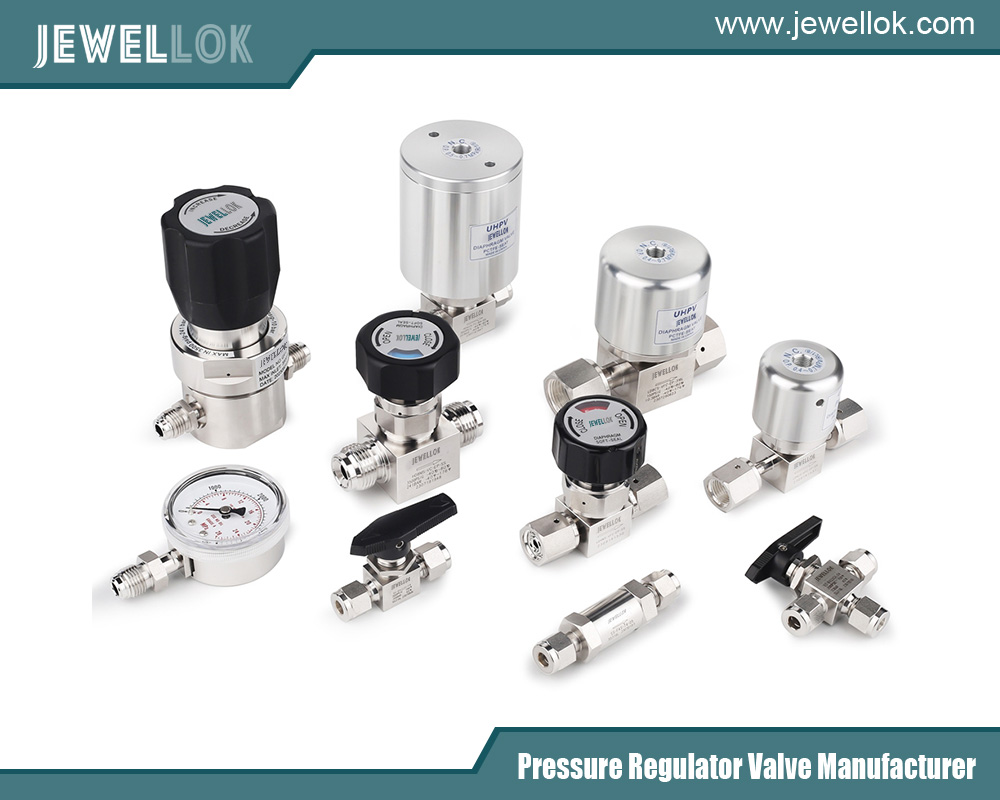
Working Principles and Characteristics of Ultra High Purity Diaphragm Valves
Working Principles
The operation of an ultra high purity diaphragm valve is based on the movement of the diaphragm to control the flow of fluids. When the valve stem rises, the diaphragm is lifted, opening the fluid passage and allowing the fluid to pass through. When the valve stem descends, the diaphragm closely adheres to the valve seat, blocking the flow of the fluid and achieving valve closure. The diaphragm, as a key component, completely isolates the fluid from other parts of the valve, effectively preventing the corrosion and contamination of the internal structure of the valve by the fluid.
Characteristics
- High Purity: Special manufacturing materials and processes, such as high-purity PFA (Perfluoroalkoxy alkanes), are used to ensure that no impurities are released into the fluid during use, meeting the strict requirements for high purity of fluids in LCD panel manufacturing.
- Corrosion Resistance: It can withstand a variety of corrosive chemical fluids, such as hydrochloric acid, nitric acid, hydrofluoric acid, DMSO (Dimethyl sulfoxide), NMP (N-Methyl-2-pyrrolidone), etc., and maintain stable performance in various chemical treatment processes of LCD panel manufacturing.
- Zero Leakage: The tight sealing design between the diaphragm and the valve seat ensures that the valve has almost zero leakage in the closed state, preventing the spillage of fluids and cross-contamination. This is of vital importance for the high-value and high-purity manufacturing processes of LCD panels.
- Precise Flow Control: By integrating with the automation control system, it can achieve precise adjustment of the fluid flow rate, meeting the requirements for subtle changes in fluid flow in different process steps, which helps to improve production efficiency and the consistency of product quality.
Application Process Steps of Ultra High Purity Diaphragm Valves in LCD Panel Manufacturing
Photolithography Process
Photolithography is a key process in LCD panel manufacturing for defining pixel and circuit patterns. During the coating and development of photoresist, ultra high purity diaphragm valves are used to control the delivery of photoresist and developer. Photoresist is a material extremely sensitive to impurities. The high-purity characteristic of ultra high purity diaphragm valves ensures that the photoresist will not be contaminated during the delivery process, avoiding pattern defects in photolithography caused by impurities. In the delivery of the developer, the precise flow control of the diaphragm valve ensures the uniformity and stability of the development process, thus improving the resolution and accuracy of the photolithography pattern.
Etching Process
The etching process is used to remove unwanted semiconductor materials to form precise circuit structures. In the etching process, various strongly corrosive etching gases and liquids, such as chlorine gas and hydrofluoric acid, are required. The corrosion resistance of ultra high purity diaphragm valves enables them to safely and reliably control the flow of these corrosive fluids. At the same time, its fast switching response and precise flow control capabilities ensure the accuracy and consistency of the etching process, avoiding problems such as over-etching or under-etching, which plays a key role in improving the performance and yield rate of LCD panels.
Cleaning Process
The cleaning process runs through multiple stages of LCD panel manufacturing, aiming to remove contaminants such as particles, organic substances, and metal impurities generated during the production process. Ultra high purity diaphragm valves are used to control the delivery of ultra-pure water and various cleaning chemical reagents. The high-purity requirement of ultra-pure water makes ultra high purity diaphragm valves an ideal control component, as they can ensure that the purity of ultra-pure water is not affected during the delivery process. For cleaning chemical reagents, the corrosion resistance and precise flow control characteristics of the diaphragm valve ensure the effectiveness and safety of the cleaning process, avoiding problems such as incomplete cleaning or panel damage caused by reagent residues or uneven flow rates.
Cell Assembly Process
In the cell assembly process of LCD panels, liquid crystal materials need to be injected. Ultra high purity diaphragm valves are used to control the precise injection amount of liquid crystal materials. The injection amount of liquid crystal materials directly affects the display performance of LCD panels, such as contrast ratio, viewing angle, and response time. The high-precision flow control capability of ultra high purity diaphragm valves enables the liquid crystal materials to be accurately injected into the designated area, ensuring the display quality and consistency of LCD panels.
Thin Film Deposition Process
The thin film deposition process is used to deposit various functional thin films on the substrate, such as transparent conductive films and insulating films. During the thin film deposition process, precise control of the flow rates of various gases and vapors is required to ensure the quality and performance of the thin films. Ultra high purity diaphragm valves play an important role in the gas delivery system. Their precise flow control and fast response speed can meet the strict requirements for gas flow rates in the thin film deposition process, helping to improve the uniformity and compactness of the thin films.
Performance Requirements of Ultra High Purity Diaphragm Valves in LCD Panel Manufacturing
Flow Control Precision
In each process step of LCD panel manufacturing, the requirements for fluid flow rates vary greatly, ranging from the tiny dropping of photoresist to the relatively large flow of etching gas delivery. Ultra high purity diaphragm valves need to have a high-precision flow control capability, being able to achieve stable and accurate flow regulation within different flow ranges. Usually, the flow control precision is required to reach ±1% or even higher.
Corrosion Resistance
Due to the involvement of a variety of strongly corrosive chemical fluids in the LCD panel manufacturing process, ultra high purity diaphragm valves must have excellent corrosion resistance. The diaphragm and valve body materials need to be able to resist the erosion of various chemical substances, and not deform, corrode, or degrade during long-term use, so as to ensure the performance and reliability of the valve.
Sealing Performance
Good sealing performance is one of the key performance indicators of ultra high purity diaphragm valves. In LCD panel manufacturing, any leakage of fluids may lead to product contamination, production interruption, or safety accidents. Ultra high purity diaphragm valves need to meet extremely high sealing standards. Usually, the leakage rate in the closed state is required to be lower than 10⁻⁹ mbar·L/s to ensure the safety and stability of the production process.
Cleanliness
The cleanliness of ultra high purity diaphragm valves themselves is of great importance. Their internal structure should be designed to have no dead corners and be easy to clean to prevent the accumulation of particles and impurities. During the manufacturing and assembly processes, strict cleaning processes and inspection methods need to be adopted to ensure that the valves reach an extremely high cleanliness standard before use, avoiding contamination of the LCD panel manufacturing process.
Reliability and Service Life
LCD panel manufacturing equipment usually needs to operate continuously for a long time. As a key component, ultra high purity diaphragm valves must have high reliability and a long service life. They need to be able to operate stably under frequent switching operations and harsh working environments, reducing the frequency of maintenance and replacement, so as to lower production costs and improve production efficiency.
Selection and Maintenance of Ultra High Purity Diaphragm Valves
Key Points for Selection
- Select appropriate materials according to process requirements: For occasions where strongly corrosive chemical fluids are in contact, a diaphragm valve made of PFA material with better corrosion resistance should be selected. For high-temperature processes, valve body and diaphragm materials with high temperature resistance need to be chosen.
- Select appropriate specifications according to flow rate and pressure requirements: Accurately calculate the fluid flow rate and pressure range required by the process, and select the valve size and pressure rating that can meet these requirements. At the same time, consider a certain margin to deal with possible process changes.
- Consider automation control requirements: If the production process requires automation control, an ultra high purity diaphragm valve equipped with a suitable actuator (such as a pneumatic or electric actuator) should be selected, and ensure that it can be compatible with the existing control system.
Key Points for Maintenance
- Regular Inspection: Regularly inspect the appearance, sealing performance, and operation flexibility of the valve, and check for any signs of corrosion, leakage, or damage.
- Cleaning and Maintenance: Regularly clean the valve to remove surface dust and impurities. For the internal structure, it can be disassembled and cleaned as needed, but be careful to avoid damaging the valve during the cleaning process.
- Replacement of Vulnerable Parts: The diaphragm is a vulnerable part of the ultra high purity diaphragm valve and should be replaced regularly according to the usage situation. At the same time, check the wear condition of sealing parts, valve stems, and other components, and replace the severely worn parts in a timely manner.
- Calibration and Testing: Regularly calibrate the flow control precision of the valve to ensure that its performance meets the process requirements. At the same time, conduct a sealing performance test to check whether the sealing performance of the valve is good.
Development Trends of Ultra High Purity Diaphragm Valves in LCD Panel Manufacturing
Intelligence and Automation
With the continuous development of industrial automation and intelligent manufacturing technologies, ultra high purity diaphragm valves will increasingly integrate intelligent sensors and automation control functions. Through connection with the factory automation system, functions such as remote monitoring, fault diagnosis, automatic adjustment, and preventive maintenance can be achieved, improving the intelligent level and efficiency of the production process.
Higher Performance Requirements
With the continuous advancement of LCD panel manufacturing technologies, the performance requirements for ultra high purity diaphragm valves will be further enhanced. Future ultra high purity diaphragm valves will need to have higher flow control precision, better corrosion resistance, lower leakage rates, and longer service lives to meet the evolving needs of LCD panel manufacturing processes.
Miniaturization and Lightweight
To adapt to the development trend of miniaturization and integration of LCD panel manufacturing equipment, ultra high purity diaphragm valves will develop in the direction of miniaturization and lightweight. By optimizing the design and using new materials, while ensuring performance, the volume and weight of the valves can be reduced, lowering the space occupation and cost of the equipment.
Green and Environmental Protection
Against the backdrop of increasing environmental awareness, the design and manufacturing of ultra high purity diaphragm valves will pay more attention to environmental protection. The use of environmentally friendly materials, optimization of the manufacturing process to reduce energy consumption and waste emissions, and improvement of the recyclability and reusability of the valves will be emphasized.
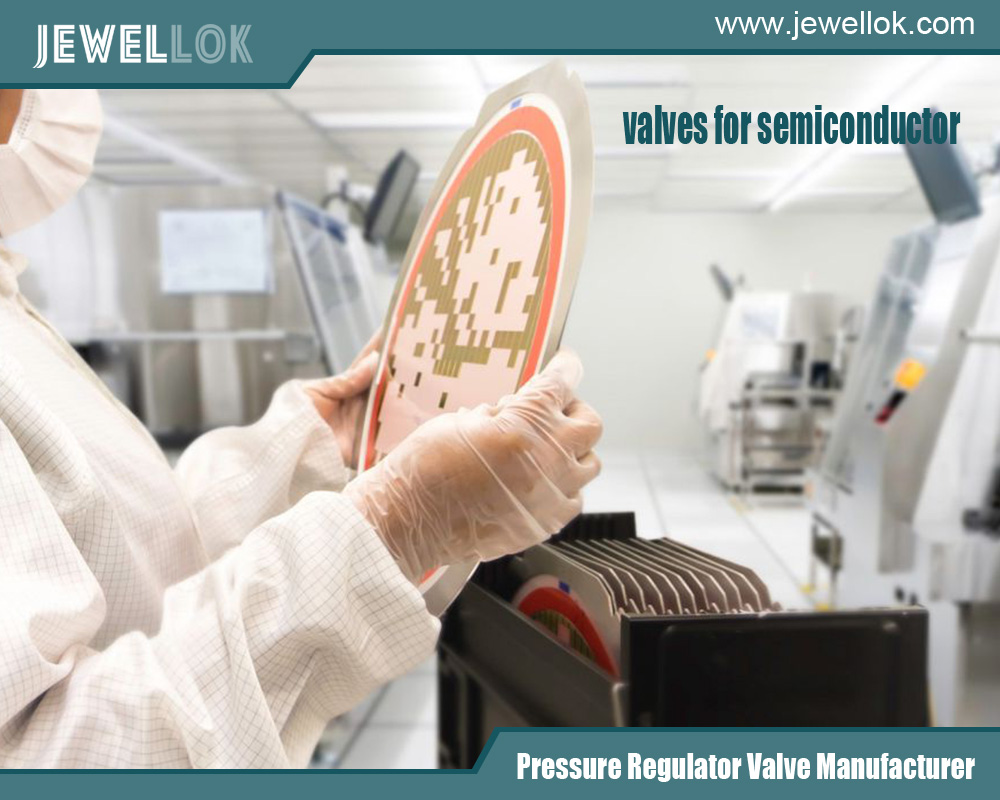
Conclusion
Ultra high purity diaphragm valves play an indispensable role in LCD panel manufacturing. Their applications in key process steps such as photolithography, etching, cleaning, cell assembly, and thin film deposition directly affect the quality and performance of LCD panels. With the continuous progress of LCD panel manufacturing technologies, ultra high purity diaphragm valves are also constantly evolving and innovating to meet higher performance requirements. In the future of the LCD panel manufacturing field, ultra high purity diaphragm valves will continue to develop in the directions of intelligence, high performance, miniaturization, and green environmental protection, providing solid support for the sustainable development of the LCD panel industry.
For more about key applications of ultra high purity diaphragm valves in liquid crystal display (LCD) panel manufacturing, you can pay a visit to Jewellok at https://www.jewellok.com/ for more info.
Recent Posts
Pneumatic Pressure Control Valve Manufacturers in the UK
How To Choose The Right Stainless Steel Needle Valve
Tags
Recommended Products
-
Single Stage Wall And Cabinet Mounting Pressure Control Panels JSP-2E Series For High Purity Gases
-
Stainless Steel Single Stage Semiconductor Grade Pressure Control Module Pressure Control Panels JSP-6A Series
-
Stainless Steel Ultra High Purity Mini Butt Weld Mini Tee Reducer MTRW Series Fittings
-
766L High Purity Female Connector UHP Fitting Female Connector
-
High Purity High Pressure 316 Stainless Steel Ball Valves JBV1 Series From High Pressure Ball Valve Manufacturer And Supplier In China
-
Long Gland LG Series For Ultra High Purity Gas And Chemical Delivery Systems
-
Manual Gas Rack High Purity Gas Delivery Systems JW-100-GR
-
7108L Cylinder Cap Connectors For Ultra High Purity Gases