Blog
Jewellok is a professional pressure regulator and valve manufacturer and supplier.
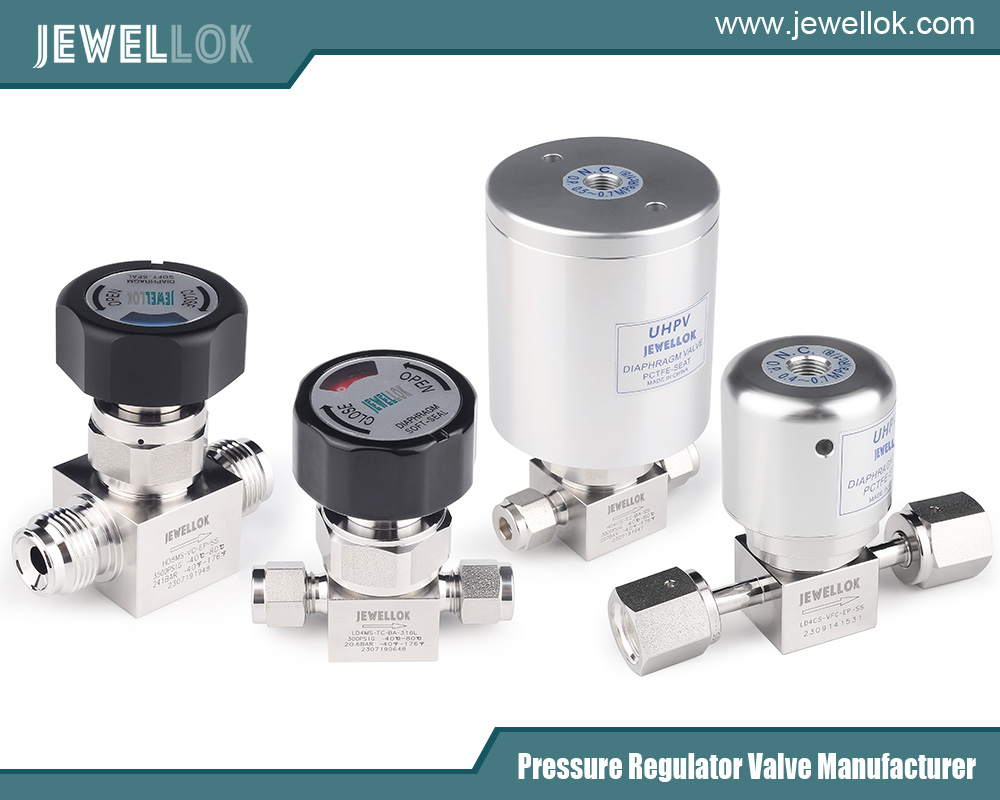
Questions About Special Gas Diaphragm Valves: A Comprehensive Guide
- Pressure Regulator Valve Manufacturer
- China Diaphragm Valve Manufacturers, China Diaphragm Valve Suppliers, diaphragm valve manufacturers in china, GC Special Gas Cabinet, High pressure manual diaphragm valve, High pressure pneumatic diaphragm valve, High Purity Pressure Reducing Valve, Low pressure manual diaphragm valve, Low pressure pneumatic diaphragm valve, Semiconductor equipment prefabricated valve parts, Special gas diaphragm valve, special gas diaphragm valves china, special gas diaphragm valves manufacturer, special gas diaphragm valves suppliers, Special gas pressure reducing valve, Top diaphragm valve manufacturers in china, VMB shunt cabinet
- No Comments
Questions About Special Gas Diaphragm Valves: A Comprehensive Guide
Special gas diaphragm valves are critical components in industries requiring precise control of gases with unique properties, such as high purity, corrosiveness, or toxicity. These valves are designed to ensure safety, maintain gas purity, and provide reliable performance in demanding applications. This 2000-word article addresses common questions about special gas diaphragm valves, exploring their design, applications, materials, maintenance, and more. Whether you’re an engineer, technician, or simply curious about these specialized valves, this guide provides detailed answers to help you understand their role and functionality.
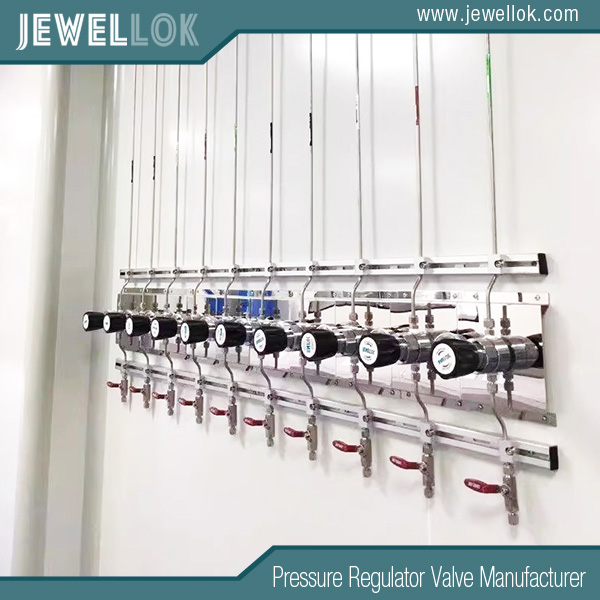
1. What is a Special Gas Diaphragm Valve?
A special gas diaphragm valve is a type of valve engineered to regulate the flow of gases that have unique or challenging properties. These may include corrosive gases like chlorine, high-purity gases used in semiconductor manufacturing, or toxic gases requiring strict containment. The defining feature of a diaphragm valve is its flexible diaphragm, which creates a seal to isolate the gas from the valve’s actuating mechanism. This design ensures that the gas only contacts the valve body and diaphragm, reducing the risk of contamination, leakage, or corrosion.
Diaphragm valves are favored for special gas applications due to their excellent leak tightness, ability to operate across a wide range of pressures and temperatures, and availability in materials compatible with various gases. The diaphragm itself can be made from elastomers such as PTFE, EPDM, or Viton for flexibility and chemical resistance, or from metals like stainless steel or Hastelloy for high-pressure or high-temperature conditions.
2. Why Are Diaphragm Valves Preferred for Special Gases?
Diaphragm valves stand out for special gas applications due to several key advantages:
Leak Tightness: The diaphragm forms a robust seal, preventing gas leakage—a critical factor for safety and purity.
Contamination Prevention: By limiting gas contact to the valve body and diaphragm, the risk of contamination from internal components is minimized.
Corrosion Resistance: Materials can be selected to withstand corrosive gases, extending the valve’s lifespan.
Versatility: These valves can manage a broad spectrum of gases, from inert to highly reactive, under varying conditions.
Ease of Maintenance: The diaphragm can be replaced without removing the valve from the pipeline, reducing downtime.
These qualities make diaphragm valves the go-to choice for industries where gas integrity and operational reliability are non-negotiable.
3. What Materials Are Used in Special Gas Diaphragm Valves?
The materials in special gas diaphragm valves are chosen based on the gas type and operating environment:
Valve Body: Stainless steel (e.g., 316L) is common for its corrosion resistance, while alloys like Hastelloy or Monel are used for harsher conditions. For less demanding applications, brass or PVC may suffice.
Diaphragm: Elastomers like PTFE, EPDM, Viton, or silicone offer flexibility and chemical compatibility. Metal diaphragms, such as stainless steel or Hastelloy, are used for extreme conditions.
Seals and Gaskets: Materials like PTFE, Kalrez, or metal seals ensure compatibility and durability.
Material selection is crucial to prevent reactions, degradation, or contamination, ensuring the valve performs reliably over time.
4. What Are the Typical Applications of These Valves?
Special gas diaphragm valves are essential in industries requiring precise gas control and purity:
Semiconductor Manufacturing: Managing high-purity gases like silane or nitrogen in wafer fabrication.
Pharmaceutical Industry: Handling sterile gases in drug production.
Chemical Processing: Controlling reactive or corrosive gases like ammonia or hydrogen chloride.
Aerospace: Used in fuel systems or environmental controls where reliability is paramount.
Laboratories: Supporting research with specialty gases in analytical equipment.
Their ability to maintain gas purity and prevent leaks makes them indispensable in these high-stakes environments.
5. How Do You Select the Right Valve for a Specific Gas?
Choosing the correct special gas diaphragm valve involves a systematic approach:
Gas Properties: Assess the gas’s corrosiveness, toxicity, and purity needs.
Operating Conditions: Evaluate pressure, temperature, and flow rate requirements.
Material Compatibility: Ensure the valve body and diaphragm materials won’t react with the gas.
Valve Size and Type: Match the valve size to flow needs and choose between weir-type or straight-through designs.
Actuation Method: Decide on manual, pneumatic, or electric actuation based on control preferences.
Standards Compliance: Verify the valve meets industry standards (e.g., SEMI, ISO).
Consulting with manufacturers or specialists can refine this process, ensuring optimal valve selection.
6. What Are the Maintenance Requirements for These Valves?
Maintaining special gas diaphragm valves ensures their longevity and performance:
Regular Inspection: Look for wear, leaks, or damage to the diaphragm and components.
Diaphragm Replacement: Replace the diaphragm periodically, as it’s a wear item, based on usage and conditions.
Cleaning: Keep the valve free of contaminants, especially in high-purity systems.
Lubrication: Apply lubrication to moving parts if needed, avoiding contamination.
Testing: Conduct leak and functional tests to confirm proper operation.
Following manufacturer guidelines is key to minimizing downtime and maintaining efficiency.
7. What Are Common Problems and How to Troubleshoot Them?
Common issues with these valves include:
Leakage: Caused by a worn diaphragm or improper installation. Fix: Replace the diaphragm and check bolt torque.
Sticking/Jamming: Due to contamination or lack of lubrication. Fix: Clean the valve and lubricate appropriately.
Reduced Flow: Resulting from blockages or a partially closed valve. Fix: Inspect for obstructions and adjust the valve position.
Corrosion: Indicates material incompatibility. Fix: Switch to a compatible valve material.
Diaphragm Failure: From overpressure or chemical attack. Fix: Replace the diaphragm and verify operating conditions.
Start troubleshooting with a visual inspection and refer to the valve’s manual for specific guidance.
8. Are There Any Standards or Regulations That Apply to These Valves?
Yes, depending on the application, valves may need to meet:
SEMI Standards: For semiconductor equipment.
ISO Standards: For quality and product specifications.
ASME BPE: For pharmaceutical bioprocessing equipment.
FDA Regulations: For food and drug applications.
ATEX Directives: For explosive atmospheres.
Compliance ensures safety and performance, so verify applicable standards for your use case.
9. How Do These Valves Compare to Other Types for Gas Applications?
Compared to ball, gate, or needle valves, diaphragm valves offer:
Superior Sealing: Reducing leak risks more effectively.
Lower Contamination: Limiting gas exposure to fewer components.
Easier Maintenance: Allowing diaphragm replacement without line removal.
However, they may have lower pressure/temperature limits and higher upfront costs. Their reliability often justifies the investment in critical gas applications.
10. What Are the Latest Advancements in Special Gas Diaphragm Valve Technology?
Recent innovations include:
Advanced Materials: New elastomers and metals for enhanced durability and resistance.
Optimized Designs: Improved flow paths for better efficiency.
Smart Technology: Sensors for monitoring and predictive maintenance.
Miniaturization: Compact valves for tight spaces.
Automation: Greater use of actuators for precise control.
These advancements improve performance and adaptability in modern applications.
11. How Does the Design of a Diaphragm Valve Work?
A diaphragm valve comprises a valve body, a flexible diaphragm, and an actuating mechanism (manual, pneumatic, or electric). The diaphragm is clamped between the body and a bonnet or compressor. When open, the diaphragm lifts from the seat, allowing gas flow; when closed, it seals against the seat to stop flow. This isolates the gas from the actuator, maintaining purity and preventing contamination—a critical feature for special gases.
12. What Are the Different Types of Diaphragm Valves for Special Gases?
Two primary types exist:
Weir-Type: Features a raised weir for sealing, suitable for on/off and throttling.
Straight-Through: Offers a straight flow path with less resistance, ideal for on/off service.
Variations also depend on diaphragm material (elastomer or metal) and actuation type.
13. Can These Valves Be Used for Both On/Off and Throttling Applications?
Yes, diaphragm valves are versatile. Weir-type valves excel in throttling due to their linear flow control, while straight-through designs are better for on/off applications due to minimal pressure drop. For ultra-precise throttling, needle valves might be a better alternative.
14. What Are the Installation Considerations for Special Gas Diaphragm Valves?
Key factors include:
Orientation: Most work in any position, but confirm with the manufacturer.
Piping Support: Avoid stress on the valve with proper support.
Accessibility: Ensure maintenance access.
Cleanliness: Maintain a contaminant-free environment for high-purity uses.
Torque Specs: Adhere to manufacturer guidelines for assembly.
Proper installation enhances performance and longevity.
15. How Do You Ensure Gas Purity When Using These Valves?
To maintain purity:
Material Choice: Use non-reactive, non-outgassing materials.
Surface Finish: Opt for smooth or electropolished surfaces to reduce particles.
Cleaning: Follow strict cleaning and purging protocols.
Leak Testing: Use helium leak tests for verification.
Minimize Dead Volume: Select designs reducing stagnant gas zones.
These steps ensure the gas remains uncontaminated throughout its journey.
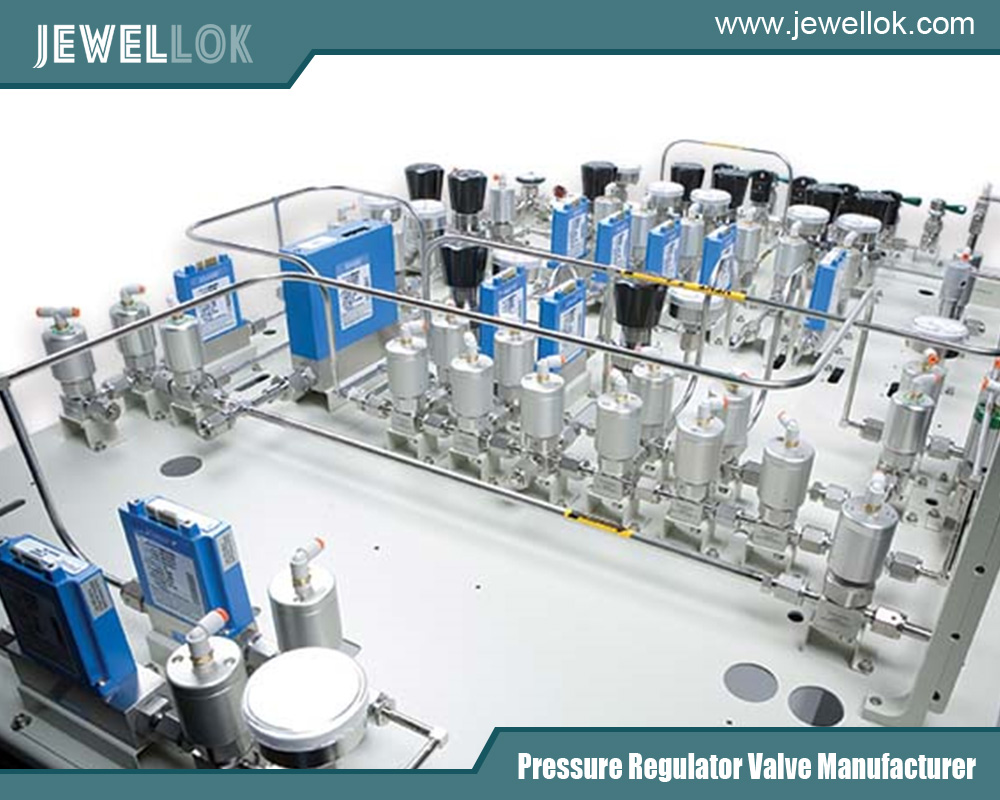
Conclusion
Special gas diaphragm valves are vital for managing gases in industries where precision, safety, and purity are paramount. From their unique design to their wide-ranging applications, these valves address complex challenges with reliability and efficiency. By understanding their features, maintenance needs, and selection criteria, users can optimize their performance in critical systems. Whether you’re dealing with corrosive chemicals, high-purity semiconductors, or aerospace fuels, this guide answers the key questions about special gas diaphragm valves, equipping you with the knowledge to make informed decisions.
For more about questions about special gas diaphragm valves: a comprehensive guide, you can pay a visit to Jewellok at https://www.jewellok.com/product-category/ultra-high-purity-diaphragm-valves/ for more info.
Recent Posts
What is a Gas Pressure Relief Valve?
Gas Pressure Regulator: How It Works
What is VMB Valve Manifold Box
Tags
Recommended Products
-
Stainless Steel Ultra High Purity (UHP) High Pressure Manual Diaphragm Valve
-
Semi Automatic And Automatic Switching Speicialty Gas Changeover Manifold Panel With Semiconductor Valve Manifold Box Gas Pressure Regulators
-
DPR1 Ultra High Purity Two Stage Dual Stage Pressure Reducing Regulator Semiconductor Grade Regulators
-
High Purity High Pressure Specialty Gas Pressure Regulators Specialty Gases Pipeline Engineering Equipments Manufacturer And Supplier
-
High Purity High Pressure Gas Cylinder Pressure Regulators Pressure Reducing Valve JSR-1E Series
-
Hydrogen Manifold Argon Gas Manifold System Oxygen Manifold Propane Gas Manifold With Valves In Gas Manifold Changeover System
-
Semiconductor High Purity High Pressure Specialty Gas Bottle Gas Cylinder Storage Cabinet And Gas Pressure Regulating Cabinet
-
Scrubber Gas Cabinet Scrubber Tail Gas Treatment Cabinet Vent Gas Scrubber System Heat-Filter Burn Box Gas Scrubber/Abatement System