Blog
Jewellok is a professional pressure regulator and valve manufacturer and supplier.
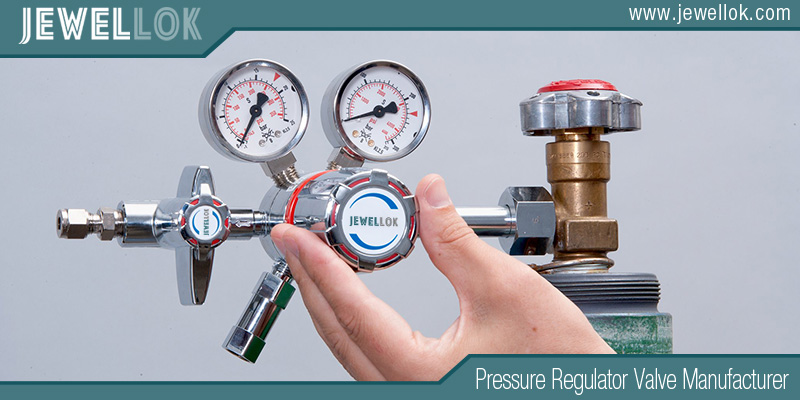
Needle Valve And Ball Valve Difference Analysis: How To Choose The Right Valve According To The Needs?
- Pressure Regulator Valve Manufacturer
- 1 1 2 gas pressure regulator, 1 2 gas regulator, 1 2 propane regulator, 1/2 gas pressure regulator, 12v electric valve, 2 electric valve, 6mm compression union, adjustable propane pressure regulator, argon gas pressure regulator, Diaphragm Valve Manufacturers, electric water valve, gas cylinder, gas manifold system, gas regulator, gas used in semiconductor chip manufacturing, high pressure argon regulator, high pressure flexible hose pipe, high purity regulator, how a regulator works, how a solenoid works, industrial regulators, lab fittings exporter, needle valves and ball valves, needle valves and ball valves manufacturer, needle valves and ball valves supplier, oxygen regulator gauge, pressure regulator, pressure safety valve vs relief valve, propane pressure regulator valve, relief valve and safety valve difference, safety valve and relief valve difference, safety valve vs relief valve, semiconductor gas, valve manifold box, water valve timer, what is a flame arrestor
- No Comments
Needle Valve And Ball Valve Difference Analysis: How To Choose The Right Valve According To The Needs?
Valves are critical components in industrial systems, controlling the flow, pressure, and direction of fluids (liquids or gases) in applications ranging from oil and gas pipelines to pharmaceutical processing and hydrogen energy systems. Among the many valve types, needle valves and ball valves are widely used due to their versatility, reliability, and distinct functionalities. While both serve to regulate fluid flow, their designs, operational characteristics, and applications differ significantly, making them suited to specific scenarios. Choosing the right valve requires a thorough understanding of these differences and how they align with the system’s requirements, such as flow control precision, pressure ratings, fluid type, and maintenance needs. An incorrect choice can lead to inefficiencies, safety hazards, or costly downtime. This article provides a detailed analysis of the differences between needle valves and ball valves, exploring their designs, performance, applications, and key considerations, and offers a step-by-step guide to selecting the right valve for your needs.
Understanding Needle Valves and Ball Valves
Needle Valves
A needle valve is a precision control valve designed for fine flow regulation, particularly in low-flow, high-pressure systems. It features a long, tapered needle-like plunger that fits into a conical seat, allowing gradual and precise adjustments to flow.
Design:
- Components: Includes a threaded stem, needle plunger, seat, body, bonnet, and handle or actuator. The needle’s fine threading allows incremental movement.
- Operation: Turning the handle moves the needle in or out of the seat, adjusting the orifice size to control flow. The valve provides a linear flow characteristic.
- Materials: Typically made from stainless steel (e.g., 316L), brass, or alloys like Hastelloy for corrosion resistance.
Key Characteristics:
- Precise flow control, ideal for throttling and fine adjustments.
- High-pressure capability (e.g., up to 10,000 psi in some designs).
- Slow opening/closing to prevent pressure surges.
- Compact design, suitable for instrumentation and confined spaces.
Ball Valves
A ball valve is a shut-off valve designed for quick, on/off flow control. It uses a spherical ball with a central bore (port) that rotates to allow or block flow.
Design:
- Components: Includes a ball with a bore, stem, seats, body, and handle or actuator. The ball rotates 90 degrees to open or close.
- Operation: Turning the handle aligns the bore with the flow path (open) or perpendicular to it (closed), providing a binary on/off function. Some designs allow throttling.
- Materials: Available in stainless steel, brass, carbon steel, or plastics (e.g., PVC) for various applications.
Key Characteristics:
- Fast, quarter-turn operation for quick shut-off.
- Low pressure drop when fully open, ideal for high-flow systems.
- Durable, with minimal leakage due to tight sealing.
- Versatile, handling a wide range of pressures and temperatures.
Core Difference: Needle valves excel in precise flow regulation for low-flow, high-pressure systems, while ball valves are designed for quick, reliable on/off control in high-flow applications.
Detailed Comparison: Needle Valves vs. Ball Valves
To choose the right valve, it’s essential to compare needle valves and ball valves across key parameters: design, functionality, performance, applications, and maintenance.
- Design and Operation
Needle Valves:
- Mechanism: The needle plunger’s fine threading allows precise control over the orifice size, enabling incremental flow adjustments. Multiple handle turns are required to fully open or close.
- Flow Path: Narrow, restricted flow path due to the small orifice, suitable for low-flow systems.
- Sealing: Relies on metal-to-metal or soft seals (e.g., PTFE) between the needle and seat, ensuring leak-tight performance at high pressures.
- Size: Compact, ideal for instrumentation panels or tight spaces.
Ball Valves:
- Mechanism: The ball rotates 90 degrees via a single handle turn, providing rapid on/off control. Some designs (e.g., V-port ball valves) allow throttling but with less precision.
- Flow Path: Full-bore designs offer minimal flow restriction, while reduced-bore designs have a smaller port, slightly increasing pressure drop.
- Sealing: Uses soft seats (e.g., PTFE, PEEK) or metal seats for high-temperature applications, ensuring tight shut-off.
- Size: Larger than needle valves, especially for high-flow pipelines.
- Key Difference: Needle valves offer precise, multi-turn flow control with a restricted flow path, while ball valves provide quick, quarter-turn on/off control with minimal flow restriction.
- Flow Control and Precision
Needle Valves:
- Precision: Exceptional for fine flow adjustments, with linear flow characteristics that allow throttling at low flow rates (e.g., 0.1–10 L/min).
- Throttling: Designed for continuous flow regulation, minimizing pressure surges or cavitation.
- Applications: Ideal for metering, sampling, or controlling gas flow in analytical instruments or hydraulic systems.
Ball Valves:
- Precision: Limited throttling capability; best for fully open or closed positions. Throttling can cause seat wear or cavitation in partially open states.
- Throttling: Not recommended for precise flow control, though V-port or characterized ball valves offer some modulation.
- Applications: Suited for isolation or shut-off in pipelines, pumps, or tanks.
- Key Difference: Needle valves are superior for precise flow control and throttling, while ball valves are optimized for on/off isolation with minimal flow control.
- Pressure and Temperature Ratings
Needle Valves:
- Pressure: Handle high pressures (e.g., 6,000–10,000 psi), making them suitable for high-pressure gas systems (e.g., hydrogen at 700 bar).
- Temperature: Operate in a wide range (e.g., -40°C to 200°C for stainless steel), with limitations based on seal materials (e.g., PTFE up to 200°C).
- Limitations: Smaller orifice limits flow capacity, unsuitable for high-flow systems.
Ball Valves:
- Pressure: Available for low to high pressures (e.g., 150–2500 psi), with high-pressure designs for oil and gas or hydrogen applications.
- Temperature: Broad range (e.g., -50°C to 400°C for metal-seated valves), with soft seats limiting high-temperature use (e.g., PTFE up to 200°C).
- Limitations: Less effective for ultra-high-pressure systems compared to needle valves.
- Key Difference: Needle valves excel in high-pressure, low-flow systems, while ball valves are versatile for a wider range of pressures and higher flow rates.
- Fluid Compatibility
Needle Valves:
- Compatibility: Suitable for gases (e.g., nitrogen, hydrogen) and liquids (e.g., water, oils). Stainless steel or Hastelloy versions handle corrosive fluids (e.g., ammonia, chlorine).
- UHP Applications: Used in ultra-high-purity (UHP) systems (e.g., semiconductors) due to precise control and leak-tight sealing.
- Limitations: Not ideal for slurries or viscous fluids, which can clog the small orifice.
Ball Valves:
- Compatibility: Handle a broad range of fluids, including gases, liquids, and some slurries, depending on seat materials (e.g., PTFE for chemicals, PEEK for oils).
- Hygienic Applications: Sanitary ball valves with polished stainless steel are used in pharmaceuticals and food processing.
- Limitations: Less suitable for UHP systems requiring fine control or highly corrosive fluids without specialized materials.
- Key Difference: Needle valves are preferred for UHP and corrosive gas systems requiring precision, while ball valves are versatile for diverse fluids, including hygienic applications.
- Maintenance and Durability
Needle Valves:
- Maintenance: Require periodic inspection of the needle and seat for wear, especially in high-pressure or corrosive systems. Packing (e.g., PTFE) may need replacement.
- Durability: Robust for high-pressure applications but susceptible to damage from over-tightening or debris in the fluid.
- Lifespan: Long-lasting in clean, low-flow systems with proper maintenance.
Ball Valves:
- Maintenance: Low maintenance due to simple design and durable seats. Seat wear from throttling or abrasive fluids may require replacement.
- Durability: Highly durable, with minimal leakage even after thousands of cycles. Floating or trunnion-mounted designs enhance longevity in high-flow systems.
- Lifespan: Extended lifespan, especially in on/off applications with clean fluids.
- Key Difference: Ball valves require less maintenance and are more durable for high-flow, on/off applications, while needle valves need careful maintenance for precision control.
Applications of Needle Valves and Ball Valves
Needle Valves
- Instrumentation: Controlling flow in pressure gauges, flow meters, or analytical instruments (e.g., gas chromatography).
- Oil and Gas: Regulating pressure in wellhead control systems or sampling lines.
- Hydrogen Energy: Metering high-pressure hydrogen in fuel cells or refueling stations.
- Chemical Processing: Handling corrosive gases (e.g., ammonia) in reactors or pilot plants.
- Aerospace: Precise control of hydraulic or pneumatic systems in aircraft.
- Example: A needle valve regulates nitrogen flow in a semiconductor fab, ensuring UHP delivery without contamination.
Ball Valves
- Oil and Gas: Isolating flow in pipelines, storage tanks, or refineries.
- Pharmaceuticals: Shut-off in sterile water or clean-in-place (CIP) systems.
- Water Treatment: Controlling water flow in distribution or treatment plants.
- Power Generation: Isolating steam or cooling water in boiler systems.
- HVAC: Managing refrigerant or air flow in chillers.
- Example: A ball valve isolates crude oil flow in a pipeline, ensuring quick shut-off during maintenance.
How to Choose the Right Valve: A Step-by-Step Guide
Selecting the right valve involves aligning its characteristics with the application’s needs. Follow these steps to make an informed choice:
Step 1: Define Application Requirements
- Fluid Type: Identify the fluid (e.g., gas, liquid, corrosive, hygienic) and its properties (e.g., viscosity, temperature).
- Flow Control Needs: Determine if precise throttling (needle valve) or on/off isolation (ball valve) is required.
- Pressure and Temperature: Specify operating and maximum pressure/temperature (e.g., 700 bar for hydrogen, 200°C for steam).
- Application Context: Note the industry and specific use (e.g., UHP semiconductor, high-flow pipeline).
- Action: Create a fluid and system profile to guide valve selection.
Step 2: Select the Valve Type
- Needle Valve: Choose for low-flow, high-pressure systems requiring precise control (e.g., instrumentation, UHP gas delivery).
- Ball Valve: Select for high-flow, on/off applications or systems needing quick shut-off (e.g., pipelines, isolation).
- Action: Match the valve type to the flow control and operational needs (e.g., needle for throttling, ball for isolation).
Step 3: Choose Materials and Seals
- Body Materials:
- Needle Valves: 316L stainless steel or Hastelloy for corrosive or UHP systems; brass for non-corrosive gases.
- Ball Valves: Stainless steel for corrosive or hygienic applications; carbon steel or brass for non-corrosive fluids.
Seal Materials:
- Needle Valves: PTFE or graphite for high-pressure sealing; PEEK for chemical resistance.
- Ball Valves: PTFE for chemicals; Viton for oils; metal seats for high temperatures.
- Action: Ensure material compatibility with the fluid and operating conditions, prioritizing stainless steel for corrosive or hygienic systems.
Step 4: Consider Pressure and Flow Specifications
- Pressure Rating: Select a valve rated above the system’s MAWP (e.g., 10,000 psi for needle valves in hydrogen systems, 2500 psi for ball valves in oil pipelines).
- Flow Capacity: Choose needle valves for low flow (e.g., Cv < 1.0) and ball valves for high flow (e.g., Cv > 10.0).
- Cracking Pressure: Ensure the valve’s cracking pressure suits the system (e.g., low for needle valves in low-pressure systems).
- Action: Verify pressure and flow ratings match system requirements, using manufacturer Cv data for flow capacity.
Step 5: Evaluate Environmental and Installation Factors
- Environmental Conditions:
- Corrosive Atmospheres: Use 316 stainless steel for coastal or chemical plant settings.
- Temperature Extremes: Ensure seals and materials withstand ambient and fluid temperatures.
- Vibration: Use robust designs (e.g., trunnion ball valves) for vibrating systems.
Installation:
- Space: Needle valves for compact instrumentation; ball valves for larger pipelines.
- Orientation: Ensure proper alignment (e.g., vertical for needle valves, any orientation for ball valves).
- Actuation: Manual for most applications; pneumatic/electric for automated systems.
- Action: Specify materials and designs for environmental resilience and follow installation guidelines.
Step 6: Ensure Regulatory and Safety Compliance
Standards:
- ASME B16.34: Valve design and testing for industrial applications.
- API 6D: Pipeline valves, including ball valves.
- ISO 17292: Metal ball valves.
- CGA G-4.1: Cleaning for UHP systems (needle valves).
- FDA/3-A: Hygienic standards for pharmaceuticals and food.
Safety Features:
- Needle Valves: Bellows-sealed designs for toxic gases.
- Ball Valves: Locking handles or fire-safe designs for hazardous systems.
- Action: Verify compliance with standards and select valves with safety features for hazardous applications.
Step 7: Assess Maintenance and Total Cost of Ownership (TCO)
Maintenance:
- Needle Valves: Require periodic packing and seat inspection.
- Ball Valves: Low maintenance, with occasional seat replacement.
TCO:
- Needle Valves: Higher cost for precision but lower for brass models.
- Ball Valves: Cost-effective for high-flow systems, with durable designs reducing replacement frequency.
- Action: Calculate TCO, factoring in purchase price, maintenance, and lifespan, prioritizing durability for critical systems.
Challenges and Solutions
- Challenge: Over-specifying valves, increasing costs.
- Solution: Match valve type to needs (e.g., brass ball valves for non-corrosive fluids vs. stainless steel needle valves for UHP).
- Challenge: Leakage in high-pressure systems.
- Solution: Use bellows-sealed needle valves or trunnion ball valves for tight sealing.
Challenge: Regulatory compliance.
- Solution: Work with suppliers to ensure valves meet standards like ASME or FDA.
Challenge: Misapplication of valve type.
- Solution: Consult fluid and flow requirements to choose needle for precision or ball for isolation.
Emerging Trends
- Smart Valves: IoT-enabled needle and ball valves with sensors for flow, pressure, and leak detection.
- Sustainable Materials: Eco-friendly manufacturing and recyclable stainless steel.
- Compact Designs: Miniaturized needle valves for instrumentation and ball valves for portable systems.
- Advanced Seals: Ceramic or graphene-based seals for extreme conditions.
- Impact: These trends enhance precision, sustainability, and automation, supporting modern industrial needs.
Conclusion
Needle valves and ball valves serve distinct roles in industrial systems, with needle valves excelling in precise flow control for low-flow, high-pressure applications and ball valves providing quick, reliable on/off isolation for high-flow systems. Their differences in design, functionality, pressure ratings, fluid compatibility, and maintenance requirements necessitate careful selection based on application needs. By defining fluid and system requirements, choosing appropriate materials, ensuring compliance with standards, and evaluating TCO, organizations can select the right valve to optimize performance, safety, and efficiency. Emerging trends like smart valves and sustainable materials further enhance their value, supporting innovation in industries like hydrogen energy, semiconductors, and pharmaceuticals. By following the step-by-step guide outlined in this article, stakeholders can confidently choose between needle and ball valves, ensuring reliable fluid control and operational success in critical applications.
For more about needle valve and ball valve difference analysis: how to choose the right valve according to the needs, you can pay a visit to Jewellok at https://www.jewellok.com/ for more info.
Recent Posts
What is a Gas Pressure Relief Valve?
Gas Pressure Regulator: How It Works
What is VMB Valve Manifold Box
Tags
Recommended Products
-
Fully Automated Gas Cabinet For Precise UHP Gas Delivery And High Purity Gas Delivery Systems JW-300-GC
-
High Purity High Pressure Stainless Steel Needle Valve Natural Gas Flow Control Valve JNV Series
-
Ultra High Purity Gas Delivery Systems And Liquid Chemical Delivery Systems JW-300-LDS
-
770L Female Elbow | Stainless Steel High Purity Weld Fittings Female Micro Elbow Fittings
-
Single Stage Wall And Cabinet Mounting Pressure Control Panels JSP-2E Series For High Purity Gases
-
High Purity Semi-Auto Stainless Steel Changeover Manifold System, Nitrogen High Pressure Control Panel With Semiconductor Valve Manifold Box Diaphragm Valves
-
764LR Stainless Steel 316 Reducing Tee UHP Fitting Automatic Buttweld Reducing Tee
-
764L Stainless Steel Union Tee High Purity Fitting Union Tee Reducing Tubing Connection