Blog
Jewellok is a professional pressure regulator and valve manufacturer and supplier.
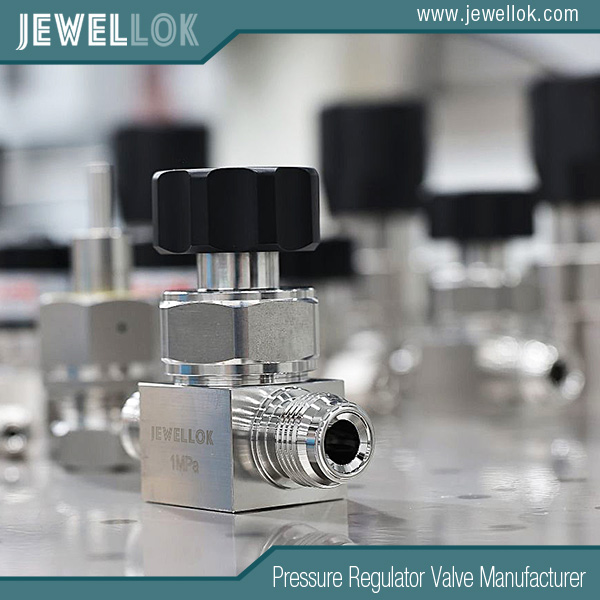
How to Correctly Select CGA Series Cylinder Couplings? – A Comprehensive Guide to Help You Make an Easy Choice
- Pressure Regulator Valve Manufacturer
- 0-10 psi air pressure regulator with gauge, 0-100 PSI Helium Tank Regulator, 0-30 psi propane regulator with gauge, 1 1 2 gas pressure regulator, 1 2 gas regulator, 1 2 propane regulator, 1/2 gas pressure regulator, 1/4 VCR Stainless Steel Ultra High Purity Gas Regulator, 2 stage propane regulator vs single stage, 2-stage propane regulator for home, 3/4 natural gas regulator, 3000PSI Nitrogen Panel Mount Pressure Regulator, adjustable air pressure regulator, adjustable high pressure propane regulator, Argon Gas Flow Gauge Regulator And Valves, BA grade high purity ball valves, BA Series high purity ball valves, Best specialty gas valves manufacturers china, CGA series cylinder couplings, CGA series cylinder couplings manufacturer, China High purity gas valves manufacturers, China High Purity Valves Manufacturer, China High Temperature Ball Valves, China Needle Valves Stainless steel, china semiconductor diaphragm valves manufacturers, China specialty gas valves manufacturers, China Ultra High Purity Gas Cylinder Valves, Control Valves and Pressure Regulators Manufacturer, diaphragm valves, diaphragm valves factory, Diaphragm Valves for Ultra High-Purity Gas Systems, diaphragm valves manufacturer, Diaphragm Valves Manufacturer Mumbai, diaphragm valves supplier, Diaphragm-Sealed Valves, Double Block and Bleed Ball Valves, low pressure propane regulator
- No Comments
How to Correctly Select CGA Series Cylinder Couplings? – A Comprehensive Guide to Help You Make an Easy Choice
Compressed gas cylinders are vital for delivering gases in industries such as oil and gas, semiconductors, pharmaceuticals, welding, hydrogen energy, and medical applications. To ensure safe and efficient gas transfer from cylinders to regulators, transfer lines, or equipment, CGA series cylinder couplings—standardized fittings developed by the Compressed Gas Association (CGA)—are used. These couplings are designed to prevent hazardous misconnections, ensure gas purity, and maintain system integrity under varying pressures and conditions. Selecting the correct CGA coupling is critical to avoid leaks, equipment damage, safety risks, or regulatory non-compliance. The process involves understanding gas properties, pressure requirements, material compatibility, environmental factors, and industry standards. An incorrect choice can lead to catastrophic consequences, such as gas leaks, fires, or contamination in ultra-high-purity (UHP) systems. This comprehensive guide outlines a step-by-step approach to selecting the right CGA series cylinder coupling, exploring key criteria, practical considerations, and best practices to help stakeholders make informed decisions with confidence.
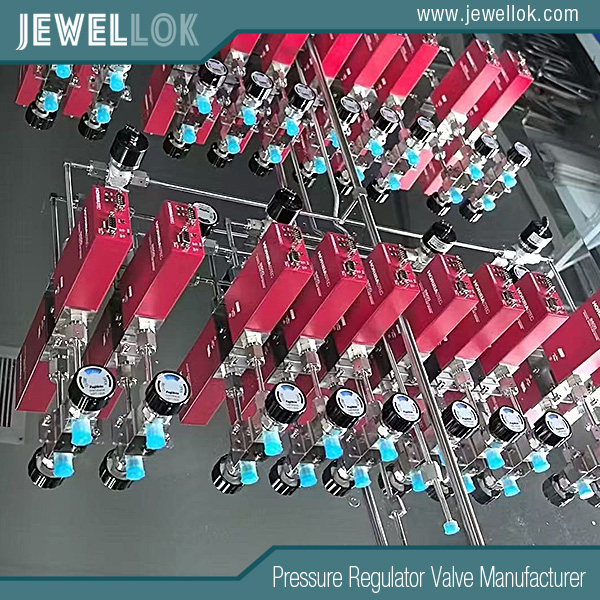
Understanding CGA Series Cylinder Couplings
CGA cylinder couplings are standardized fittings that connect compressed gas cylinders to regulators, hoses, or equipment, ensuring safe and leak-tight gas delivery. The CGA, a leading authority in gas safety standards, assigns unique couplings for specific gases and pressure ranges to minimize the risk of cross-connection and ensure compatibility. Each coupling is designated by a CGA number (e.g., CGA 580, CGA 320) and defined in the CGA V-1 standard, “Standard for Compressed Gas Cylinder Valve Outlet and Inlet Connections,” which includes 129 valve outlet connections for 278 gases and mixtures.
Key Features of CGA Couplings
- Gas-Specific Design: Each coupling is unique to a gas or gas family (e.g., CGA 580 for inert gases like nitrogen, argon; CGA 320 for carbon dioxide) to prevent misconnections.
- Pressure Ratings: Couplings are rated for specific maximum pressures (e.g., 3000 psig for CGA 580, 500 psig for CGA 350), ensuring safe operation.
- Thread Direction: Right-hand (RH) threads are used for non-hazardous gases (e.g., oxygen, nitrogen), while left-hand (LH) threads, marked with a notch, indicate hazardous gases (e.g., flammable or toxic gases like hydrogen, arsine).
- Sealing Mechanism: Couplings use either metal-to-metal seals (bullet-nose, e.g., CGA 580) or gasket seals (e.g., CGA 320), depending on the gas and application.
- Materials: Available in brass, 316L stainless steel, or nickel-plated brass for compatibility with corrosive, UHP, or medical gases.
CGA couplings are critical for applications ranging from welding (e.g., acetylene with CGA 510) to semiconductor manufacturing (e.g., silane with CGA 350) and medical gas delivery (e.g., oxygen with CGA 540). The following steps guide the selection process to ensure safety, compatibility, and performance.
Step 1: Identify the Gas Type and Application
The first step in selecting a CGA coupling is to identify the gas being used and the specific application, as these dictate the coupling’s design and specifications.
1.1 Gas Type
Each gas or gas mixture has a designated CGA coupling to prevent cross-connection. Common examples include:
- Inert Gases: CGA 580 for nitrogen, argon, helium (non-flammable, non-oxidizing).
- Flammable Gases: CGA 350 for hydrogen, carbon monoxide; CGA 510 for acetylene.
- Oxidizing Gases: CGA 540 for oxygen; CGA 326 for nitrous oxide.
- Corrosive/Toxic Gases: CGA 660 for chlorine, ammonia; CGA 330 for carbonyl sulfide.
- Medical Gases: CGA 870 for medical oxygen; CGA 950 for xenon (up to 3000 psi).
- Specialty Gases: CGA 718 for argon at 3500 psi; CGA 677 for argon at 6000 psi.
- Action: Consult the CGA V-1 standard or supplier gas assignment tables (e.g., Airgas, CONCOA) to identify the correct CGA number for the gas. Verify the gas’s chemical properties (e.g., flammability, corrosivity) to ensure compatibility.
1.2 Application Context
The industry and use case influence coupling selection:
- Welding: Requires robust couplings like CGA 510 for acetylene or CGA 540 for oxygen, often in brass for durability.
- Semiconductors: Demands UHP couplings (e.g., CGA 350 for arsine) in electropolished 316L stainless steel to prevent contamination.
- Pharmaceuticals: Needs sanitary couplings for medical gases (e.g., CGA 870 for oxygen) with polished surfaces meeting FDA standards.
- Hydrogen Energy: Requires high-pressure couplings (e.g., CGA 350 for hydrogen at 700 bar) with embrittlement-resistant materials.
- Laboratories: Uses precision couplings for analytical gases (e.g., CGA 580 for helium in gas chromatography).
- Action: Define the industry, application (e.g., welding, UHP gas delivery), and any regulatory or purity requirements.
Step 2: Determine Pressure Requirements
CGA couplings are rated for specific maximum pressures, which must match the cylinder’s service pressure to prevent leaks or regulator failure.
2.1 Cylinder Service Pressure
- Low Pressure (<500 psig): Couplings like CGA 200 (acetylene) or CGA 330 (carbonyl sulfide) are designed for low-pressure gases.
- Moderate Pressure (500–3000 psig): Common couplings like CGA 580 (nitrogen, 3000 psig) or CGA 320 (carbon dioxide, 3000 psig) suit most industrial gases.
- High Pressure (>3000 psig): Couplings like CGA 680 (argon, 3500 psig) or CGA 677 (argon, 6000 psig) are for high-pressure cylinders.
- Risk of Mismatch: Using a coupling rated below the cylinder’s pressure (e.g., CGA 580 on a CGA 680 cylinder) can over-pressurize the regulator, leading to failure or injury.
- Action: Check the cylinder’s service pressure (marked on the cylinder or in documentation) and select a coupling rated at or above this pressure.
2.2 Regulator Compatibility
The regulator must have a matching CGA coupling and pressure rating. For example, a regulator with a CGA 580 fitting is suitable for nitrogen at 3000 psig but not for argon at 6000 psig (CGA 677).
Action: Verify the regulator’s CGA number and pressure rating align with the cylinder’s coupling and service pressure.
Step 3: Select the Appropriate Material
Material selection ensures compatibility with the gas, environmental conditions, and purity requirements.
3.1 Coupling Materials
- Brass: Cost-effective for non-corrosive gases (e.g., oxygen, nitrogen, acetylene) in welding or industrial applications.
- 316L Stainless Steel: Ideal for corrosive gases (e.g., chlorine, ammonia) or UHP applications (e.g., semiconductors) due to corrosion resistance and low particle generation.
- Nickel-Plated Brass: Balances cost and corrosion resistance for moderately corrosive gases (e.g., carbon dioxide).
- Hastelloy/Monel: Used for highly corrosive gases (e.g., hydrogen chloride) in chemical processing.
- Consideration: For metal-to-metal seals (e.g., CGA 580), avoid overtightening, as the harder material (e.g., stainless steel nipple) may damage the softer valve material (e.g., brass).
3.2 Gasket Materials (If Applicable)
Some couplings (e.g., CGA 320 for carbon dioxide) use gaskets for sealing. Common gasket materials include:
- PTFE: Chemical resistance for corrosive gases (e.g., chlorine).
- Nylon: Durable for non-corrosive gases (e.g., carbon dioxide).
- Lead or Fiber: Used for specific low-pressure gases (e.g., acetylene).
- Action: Select coupling and gasket materials based on gas compatibility, purity requirements, and environmental conditions, prioritizing 316L stainless steel for UHP or corrosive applications.
Step 4: Verify Thread Type and Sealing Mechanism
CGA couplings use specific thread types and sealing mechanisms to ensure safety and compatibility.
4.1 Thread Direction
- Right-Hand (RH): Standard for non-hazardous gases (e.g., CGA 580 for nitrogen, CGA 540 for oxygen). Threads are clockwise.
- Left-Hand (LH): Used for hazardous gases (flammable, toxic, or poisonous, e.g., CGA 350 for hydrogen, CGA 660 for chlorine). Threads are counterclockwise, marked with a notch on the nut.
- Safety Note: LH threads alert users to handle hazardous gases with care, reducing the risk of errors. Never modify or interchange RH and LH couplings.
4.2 Sealing Mechanism
- Bullet-Nose (Metal-to-Metal): Couplings like CGA 580 rely on a metal-to-metal seal between the nipple and valve. Proper torque (per CGA recommendations) is critical to avoid leaks without damaging surfaces.
- Gasket-Sealed: Couplings like CGA 320 use a gasket (e.g., PTFE) to form a seal. Replace gaskets regularly to maintain integrity, and avoid using PTFE tape, which can cause leaks by preventing full contact.
- Action: Confirm the coupling’s thread direction (RH or LH) and sealing mechanism (bullet-nose or gasket), and follow CGA torque specifications for installation.
Step 5: Consider Environmental and Installation Factors
Environmental conditions and installation practices affect coupling performance and longevity.
5.1 Environmental Conditions
- Corrosive Atmospheres: Coastal or chemical plant settings require 316L stainless steel couplings to resist salt or acid exposure.
- Temperature Extremes: Ensure materials withstand fluid and ambient temperatures (e.g., -40°C to 60°C for brass, -200°C to 200°C for stainless steel).
- Cleanliness: UHP applications (e.g., semiconductors) require couplings cleaned to CGA G-4.1 standards to prevent contamination.
- Vibration: Secure couplings with proper mounting to prevent loosening in high-vibration areas (e.g., near compressors).
- Action: Specify materials and cleaning standards to match environmental conditions, and use vibration-resistant installation practices.
5.2 Installation Considerations
- Torque: Follow CGA torque recommendations (available from suppliers like Airgas) to achieve a gas-tight seal without damaging the coupling or valve.
- No Tape: Avoid PTFE tape on CGA couplings, as it can cause leaks by preventing full contact in bullet-nose seals or compressing gaskets improperly.
- Compatibility: Ensure the coupling matches the cylinder valve and regulator exactly. Never use adapters or modify couplings, as this can lead to over-pressurization or leaks.
- Inspection: Check couplings for damage (e.g., dents, corrosion) before installation, and replace damaged components.
- Action: Install couplings per CGA guidelines, using correct torque, avoiding tape, and ensuring compatibility.
Step 6: Ensure Regulatory and Safety Compliance
Compliance with industry standards and safety requirements is critical, especially for hazardous or regulated gases.
6.1 Key Standards
- CGA V-1: Defines CGA coupling specifications, including dimensions, pressure ratings, and gas assignments.
- CGA G-4.1: Specifies cleaning procedures for UHP and oxygen systems to prevent contamination or fires.
- ASME B31.3: Governs process piping, including gas delivery systems.
- NFPA 56: Mandates safe handling for hydrogen systems, including coupling compatibility.
- OSHA 1910.101: Outlines compressed gas safety requirements.
- SEMI F19: Defines UHP coupling requirements for semiconductors.
- Action: Verify that couplings meet CGA V-1 and other relevant standards, and request supplier documentation (e.g., certificates of conformance).
6.2 Safety Features
- LH Threads for Hazardous Gases: Ensure LH couplings are used for flammable or toxic gases to alert users.
- Pressure Ratings: Confirm the coupling’s pressure rating exceeds the cylinder’s service pressure to prevent failures.
- Material Compatibility: Use materials that prevent reactions (e.g., stainless steel for chlorine to avoid corrosion).
- No Modifications: Never change or adapt CGA couplings, as this can lead to unsafe conditions (e.g., using a CGA 580 on a CGA 680 cylinder).
- Action: Select couplings with safety features and ensure compliance with OSHA, NFPA, and CGA standards.
Step 7: Evaluate Maintenance and Total Cost of Ownership (TCO)
The coupling’s maintenance needs and TCO impact long-term reliability and cost.
7.1 Maintenance Requirements
- Inspection: Regularly inspect couplings for wear, corrosion, or damage, especially in corrosive or UHP systems.
- Gasket Replacement: For gasket-sealed couplings (e.g., CGA 320), replace gaskets per manufacturer schedules to maintain seals.
- Cleaning: UHP couplings require periodic cleaning to CGA G-4.1 standards to prevent contamination.
- Torque Checks: Verify torque during maintenance to ensure leak-tight connections without over-tightening.
- Action: Establish a maintenance schedule based on application criticality and manufacturer recommendations, and maintain spare gaskets or couplings.
7.2 Total Cost of Ownership
- Upfront Cost: Stainless steel couplings cost more than brass but offer durability in corrosive environments.
- Maintenance Costs: Gasket-sealed couplings require gasket replacements, increasing costs compared to bullet-nose designs.
- Lifespan: High-quality materials (e.g., 316L stainless steel) extend lifespan, reducing replacement frequency.
- Action: Calculate TCO by factoring in purchase price, maintenance, and lifespan, prioritizing quality for critical or hazardous applications.
Step 8: Partner with Reliable Suppliers
The supplier’s expertise, quality, and support are crucial for selecting the right CGA coupling.
8.1 Supplier Evaluation
- Reputation: Choose suppliers with a track record in your industry (e.g., Airgas, CONCOA, Swagelok).
- Certifications: Ensure couplings meet CGA V-1 and ISO 9001 standards.
- Inventory: Select suppliers with a wide range of CGA couplings (e.g., brass, stainless steel) and accessories (e.g., plugs, caps).
8.2 Support Services
- Technical Support: Access to engineers for coupling selection and troubleshooting.
- Charts and Guides: Suppliers like Airgas or CONCOA provide CGA selection charts for reference.
- Customization: Some suppliers (e.g., GasFlo, FTI) offer custom configurations for unique applications.
- Action: Request supplier references, certifications, and selection charts, and negotiate terms for support and warranties.
Challenges and Solutions
- Challenge: Incorrect coupling selection due to gas misidentification.
- Solution: Use CGA V-1 or supplier gas assignment tables to confirm the correct CGA number.
- Challenge: Leaks from improper installation.
- Solution: Follow CGA torque specifications, avoid PTFE tape, and inspect couplings before use.
- Challenge: Regulatory compliance.
- Solution: Work with suppliers to ensure couplings meet CGA, OSHA, or NFPA standards.
- Challenge: Contamination in UHP systems.
- Solution: Use electropolished 316L stainless steel couplings cleaned to CGA G-4.1 standards.
Emerging Trends
- UHP Couplings: Increased demand for electropolished stainless steel couplings in semiconductors and hydrogen energy for purity and safety.
- Smart Monitoring: IoT-enabled regulators with integrated CGA couplings monitor leaks or pressure, enhancing safety.
- Sustainable Materials: Eco-friendly manufacturing and recyclable materials align with green goals.
- International Standards: Harmonization with DIN, JIS, and BSI standards for global compatibility.
- Impact: These trends improve safety, purity, and sustainability, supporting modern industrial needs.
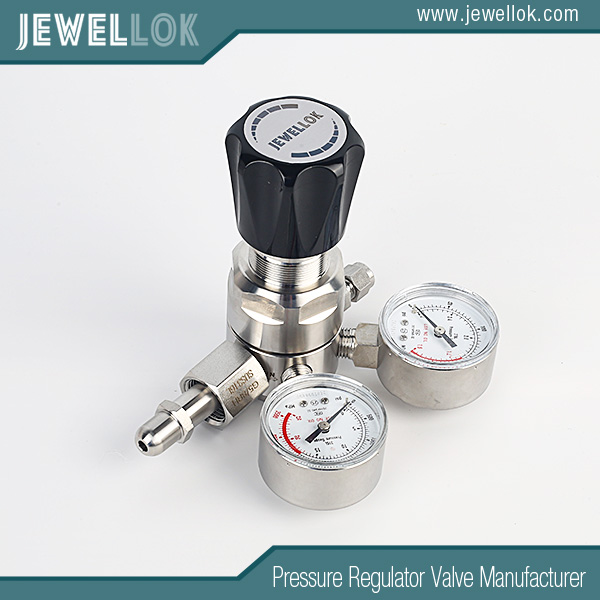
Conclusion
Selecting the right CGA series cylinder coupling is a critical task that ensures safe, efficient, and compliant gas handling in industries like semiconductors, welding, and hydrogen energy. By identifying the gas type, verifying pressure requirements, choosing compatible materials, ensuring proper installation, and adhering to regulatory standards, stakeholders can prevent leaks, contamination, and safety hazards. CGA couplings, standardized under CGA V-1, offer gas-specific, pressure-rated solutions that minimize risks through unique designs, thread directions, and sealing mechanisms. Partnering with reputable suppliers like Airgas or CONCOA, using selection charts, and following best practices (e.g., avoiding PTFE tape, adhering to torque specs) further streamline the process. Emerging trends like UHP couplings and smart monitoring enhance performance, supporting innovation and safety. By following the step-by-step guide outlined in this article, engineers, technicians, and procurement specialists can confidently select the right CGA coupling, ensuring reliable gas delivery and operational success in critical applications.
For more about how to correctly select CGA series cylinder couplings? – a comprehensive guide to help you make an easy choice, you can pay a visit to Jewellok at https://www.jewellok.com/ for more info.
Recent Posts
Types of Specialty Gas Changeover Systems
Top High-Pressure Diaphragm Valve Suppliers in Mexico
Tags
Recommended Products
-
Pressure Control Panels For High Purity Gas Control System JSP-3AE Series From Pressure Control Panels Suppliers And Manufacturer
-
772 LF Female Branch Tee | Stainless Steel Tube Fitting Female Branch Tee 1/2 in. Tube OD x 1/2 in. Tube OD x 3/8 in. Female NPT
-
772L Male Branch Tee | Stainless Steel High-Purity Tube Fitting Male Branch Tee
-
316L Stainless Steel Tube Butt Weld Reducing Fittings Union Reducer RW Series Ultrahigh Purity Process
-
Stainless Steel Single Stage Semiconductor Grade Pressure Control Module Pressure Control Panels JSP-6A Series
-
765LR Reducing Tee | Stainless Steel 316 High Purity Butt Weld Fittings Metal Face Seal For Welding Pipe Fitting Reducing Tee
-
770L Female Elbow | Stainless Steel High Purity Weld Fittings Female Micro Elbow Fittings
-
Stainless Steel Ultra High Purity (UHP) High Pressure Manual Diaphragm Valve