Blog
Jewellok is a professional pressure regulator and valve manufacturer and supplier.
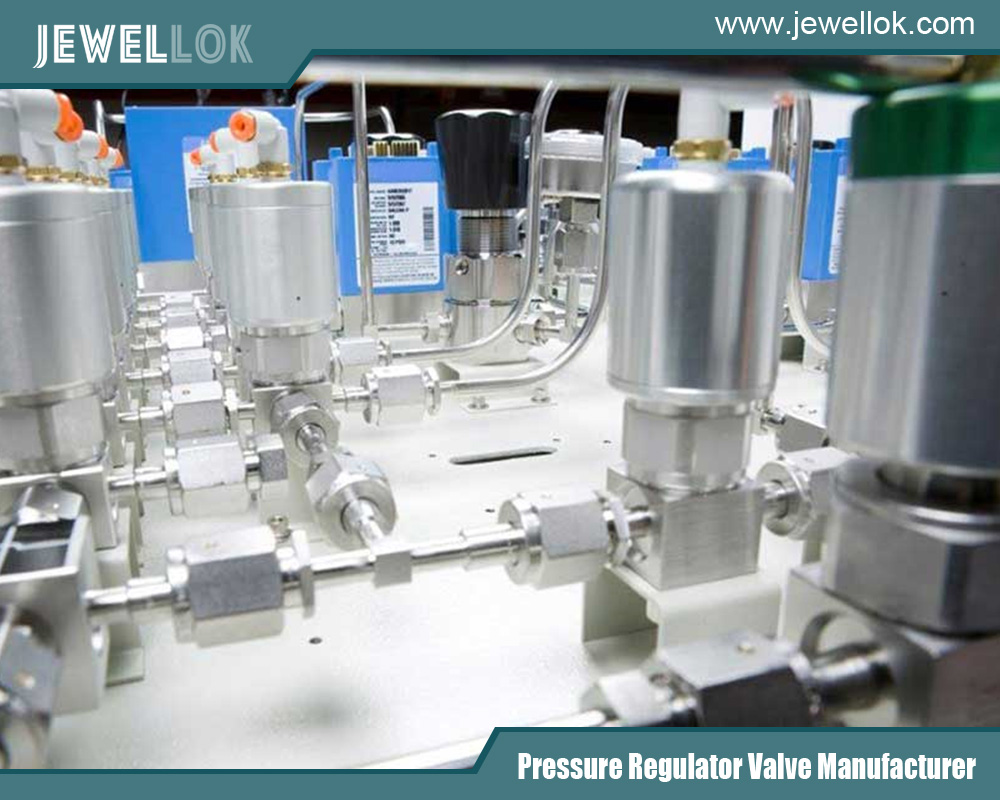
Technical Assurance for Precise Pressure Regulation of Pressure Reducing Valves under High-Flow Conditions
- Pressure Regulator Valve Manufacturer
- adjusting propane regulator, block & bleed valve, diaphram valve, double block and bleed valve, double block bleed valve, excess flow valve, Gas Pressure Reducing Valve, high purity BA Grade pressure reducing regulator, High Purity L-Type Pressure Reducing Valve, High Purity Pressure Reducing Regulators, High Purity Pressure Reducing Valve, high purity pressure reducing valves manufacturer, high purity pressure reducing valves manufacturer in china, High-purity Pressure Reducing Regulator, Hydraulic Pressure Reducing Valves, hydraulic regulator, industrial lng pressure reducing regulator, natural gas pressure reducing valve, o ring face seal fittings, pressure gauge fitting - 3/8 qc, Pressure Reducing Valve, Pressure Reducing Valve China, pressure reducing valves, pressure reducing valves factory, pressure reducing valves manufacturer, pressure reducing valves supplier, pressure relief valve vs safety relief valve, quick connect valve, Reverse Osmosis Pressure Reducing Valve, Special gas pressure reducing valve, ultra high purity, Ultra High Purity Dual Stage Pressure Reducing Regulator, Ultra High Purity Two Stage Pressure Reducing Regulator
- No Comments
Technical Assurance for Precise Pressure Regulation of Pressure Reducing Valves under High-Flow Conditions
In modern industrial production and various engineering applications, high-flow conditions are extremely common. Examples include large pipeline transportation systems in the petrochemical industry, the main pipeline networks of urban water supply, and the steam transmission lines of thermal power plants. In these scenarios, pressure reducing valves play a crucial role. They can accurately and stably regulate the relatively high inlet pressure to the set outlet pressure, ensuring the safe and efficient operation of downstream equipment and systems. However, high-flow conditions pose numerous challenges to pressure reducing valves, such as large flow rate variations, high flow velocities, and severe pressure fluctuations. Thus, how to ensure their stable and precise pressure regulation has become a key research focus.
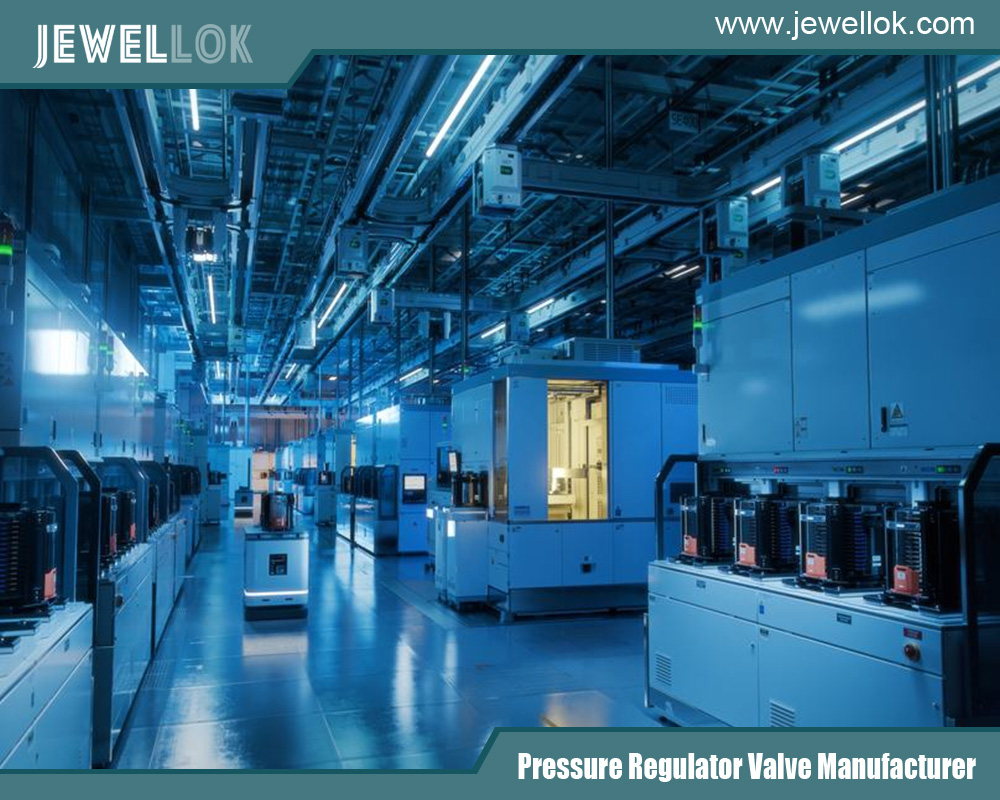
Challenges to the Operation of Pressure Reducing Valves under High-Flow Conditions
Influence of Large Flow Rate Fluctuations
Under high-flow conditions, the flow rate fluctuates widely and changes rapidly. In petrochemical production, with the switching of production processes and the start and stop of equipment, the fluid flow rate may jump from an extremely low value to a very high value within a short period. This will cause a drastic change in the internal flow field of the pressure reducing valve, and the flow velocity will fluctuate significantly. According to Bernoulli’s equation, a large change in flow velocity will lead to frequent conversion between pressure energy and kinetic energy, making the pressure distribution inside the pressure reducing valve extremely unstable, thus affecting the stability of the outlet pressure. Moreover, the rapid change in flow rate requires the regulating mechanism of the pressure reducing valve to respond quickly. In practice, due to factors such as the inertia of mechanical components and the delay in control signal transmission, it is difficult to keep up with the rhythm of flow rate changes in a timely manner, and adjustment lag is likely to occur, resulting in deviations in the outlet pressure.
Problems Caused by High-Velocity Fluids
When the flow rate is high, the fluid will strongly erode the internal components of the pressure reducing valve. Take the technical water supply system of a hydropower station as an example. The high-speed water flow will wear the valve core, valve seat, etc. of the pressure reducing valve over a long period, change the shape and size of the components, and alter the throttling characteristics of the pressure reducing valve, making it impossible to accurately regulate the pressure according to the established rules. High-velocity fluids are also prone to cavitation. When the fluid flows through the narrow parts of the pressure reducing valve, the pressure drops sharply, and the dissolved gas in the liquid precipitates to form bubbles. These bubbles then burst, generating a strong impact force, further damaging the components and interfering with the stability of pressure regulation.
Interference of Pressure Fluctuations
Under high-flow conditions, the upstream pressure fluctuates frequently and with a large amplitude, which may be caused by the instability of the power source, the operation interference of other equipment, etc. For example, in an urban water supply system, there will be obvious fluctuations in the output pressure of the water pump during peak and off-peak water consumption periods. These fluctuations are transmitted to the pressure reducing valve, which will break the original pressure balance inside it, causing uneven forces on the regulating components and resulting in fluctuations in the outlet pressure. Moreover, when the flow rate is high, the pressure transmission speed is fast, and slight pressure disturbances will spread rapidly and be amplified, increasing the difficulty for the pressure reducing valve to stabilize the outlet pressure.
Analysis of the Working Principle of Stable and Precise Pressure Regulation of Pressure Reducing Valves
Basic Pressure Regulation Principle
Pressure reducing valves work based on the principle of pressure balance. By changing the throttling area, the flow velocity and kinetic energy of the fluid are changed, resulting in different pressure losses, thus achieving pressure reduction. For a common spring-type pressure reducing valve, when the inlet pressure acts on the valve core, if the pressure is greater than the set elastic force of the spring, the valve core opens, and the fluid flows out after pressure reduction through the throttling port. The outlet pressure acts on the valve core in a feedback manner and forms a balance with the spring force to maintain the stability of the outlet pressure. When the outlet pressure increases, the valve core moves in the closing direction under the action of the pressure, reducing the throttling area, increasing the pressure loss, and reducing the outlet pressure; conversely, when the outlet pressure decreases, the valve core moves in the opening direction, increasing the throttling area, reducing the pressure loss, and increasing the outlet pressure.
Dynamic Regulation Mechanism
Under high-flow conditions, the pressure reducing valve needs to have good dynamic regulation capabilities. Take the pilot-operated pressure reducing valve as an example. The main valve is responsible for the pressure reduction of the high-flow fluid, and the pilot valve precisely controls the main valve according to the change in the outlet pressure. When there is a slight change in the outlet pressure, the pilot valve responds first, adjusts the pressure in the control cavity by changing its opening degree, and then controls the position of the main valve core to achieve rapid adjustment of the outlet pressure. This two-stage control structure improves the response speed and regulation accuracy of the pressure reducing valve and enables it to better adapt to the pressure fluctuations under high-flow conditions.
Technical Measures to Ensure Stable and Precise Pressure Regulation of Pressure Reducing Valves
Optimization of Valve Structure Design
- Improvement of the Valve Core Structure: Adopt a streamlined valve core design to reduce the resistance and turbulence of the fluid when it flows through. For example, a hyperbolic valve core can make the fluid pass through more smoothly, reducing energy loss and pressure fluctuations. Optimize the matching accuracy between the valve core and the valve seat, reduce the clearance, and prevent fluid leakage and pressure surges. Use elastic sealing materials to ensure the sealing performance and compensate for the clearance changes caused by wear.
- Addition of Buffer Devices: Install a buffer chamber or buffer spring inside the pressure reducing valve. The buffer chamber can store part of the fluid to relieve the sudden changes in flow rate and pressure; the buffer spring can absorb the pressure impact and make the movement of the valve core smoother. In a high-pressure and high-flow pressure reducing valve, by setting up a multi-stage buffer structure, the high-speed fluid is initially buffered through the throttle hole, and then the buffer spring further absorbs the impact energy, effectively reducing the influence of pressure fluctuations on the regulation accuracy.
Selection of Appropriate Control Modes
- Proportional-Integral-Derivative (PID) Control: Use a PID controller to calculate the control signal according to the deviation between the actual value and the set value of the outlet pressure and adjust the opening degree of the pressure reducing valve. In a high-flow steam pipeline pressure reduction system, through PID control, the valve opening can be adjusted in real-time, the pressure change can be responded to quickly, and the outlet pressure can be stabilized near the set value, reducing the fluctuation range.
- Intelligent Control Algorithms: Introduce intelligent algorithms such as neural networks and fuzzy control. Neural networks can learn through a large amount of data to establish a complex relationship model between inputs and outputs, realizing precise control of the pressure reducing valve; fuzzy control can process inaccurate and uncertain pressure information according to fuzzy rules, enabling the pressure reducing valve to still work stably under complex working conditions. In a high-flow gas pressure reduction system in chemical production, the fuzzy PID control algorithm is adopted, which combines the flexibility of fuzzy control and the accuracy of PID control, significantly improving the control performance of the pressure reducing valve.
Enhancement of Manufacturing and Assembly Precision
- High-Precision Machining Processes: Use advanced machining technologies, such as numerical control machining and electrical discharge machining, to ensure the dimensional accuracy and surface quality of the components of the pressure reducing valve. For key components such as the valve core and the valve seat, carry out precision grinding through a numerical control grinding machine to make the surface roughness reach below Ra0.1, improving the sealing performance and throttling accuracy.
- Strict Assembly Requirements: Formulate strict assembly process specifications and control parameters such as assembly clearance and perpendicularity. During the assembly process, use special tooling and testing equipment to ensure that each component is installed in place and reduce leakage and jamming phenomena caused by improper assembly. For the assembly of the pilot valve of the pilot-operated pressure reducing valve, strictly control the flatness and installation tension of the diaphragm to ensure the sensitivity and reliability of the pilot valve.
Application of Auxiliary Technologies
- Installation of Filters: Install a filter in front of the inlet of the pressure reducing valve to filter out impurities and particles in the fluid, prevent them from entering the inside of the pressure reducing valve, damage components such as the valve core and the valve seat, and affect the pressure regulation accuracy. In front of the pressure reducing valve of the urban water supply system, install a Y-type filter with an accuracy of 50μm to effectively intercept impurities such as sand and rust in the water, extend the service life of the pressure reducing valve, and ensure stable pressure regulation.
- Setting up of Surge Tanks: Install a surge tank behind the outlet of the pressure reducing valve and use its ability to store and release fluid to buffer pressure fluctuations. In a fire protection water supply system, the surge tank can stabilize the system pressure at the moment when the fire pump starts or during the peak water consumption period, ensuring that the outlet pressure of the pressure reducing valve meets the fire protection requirements.
Analysis of Practical Cases
A Large Petrochemical Enterprise
The high-flow pressure reducing valve in the crude oil pipeline transportation system of this enterprise had large outlet pressure fluctuations during the initial operation, affecting the stable operation of subsequent processing equipment. By optimizing the structure of the pressure reducing valve, adopting a new type of valve core and a multi-stage buffer device, and introducing an intelligent PID control algorithm, the outlet pressure fluctuation range was reduced from ±0.5MPa to ±0.1MPa, meeting the strict requirements of the production process for pressure stability and improving product quality and production efficiency.
An Urban Water Supply Project
The high-flow pressure reducing valve in the main pipeline of the urban water supply project had a problem of pressure regulation lag during peak water consumption. By enhancing the manufacturing and assembly precision, replacing the valve core and the valve seat with high-precision ones, and installing a high-precision filter and a surge tank, the response speed of the pressure reducing valve was greatly improved, and the outlet pressure could be quickly and stably maintained at the set value, ensuring the safety and stability of urban residents’ water supply.
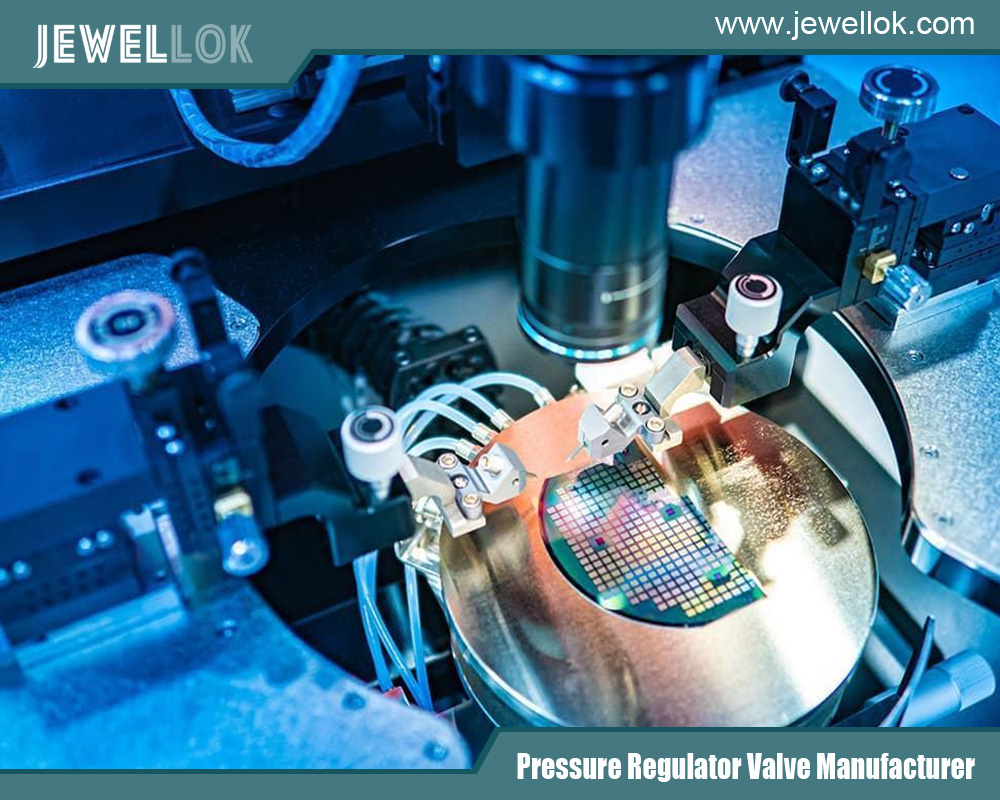
Conclusion
To ensure that the pressure reducing valve can stably and precisely regulate the inlet pressure to the set outlet pressure under high-flow conditions, it is necessary to take comprehensive measures from multiple aspects such as structure design, control mode, manufacturing and assembly precision, and application of auxiliary technologies. By optimizing these key factors and combining the experience summary and improvement of practical cases, the performance of the pressure reducing valve under high-flow conditions can be effectively improved, meeting the requirements for precise pressure regulation in various industrial and engineering fields and providing a solid guarantee for the safe and efficient operation of the system. In the future, with the continuous development of technology, it is necessary to continuously explore new materials, structures, and control methods to further enhance the pressure regulation ability of the pressure reducing valve under complex high-flow conditions.
For more about technical assurance for precise pressure regulation of pressure reducing valves under high-flow conditions, you can pay a visit to Jewellok at https://www.jewellok.com/ for more info.
Recent Posts
Types of Specialty Gas Changeover Systems
Top High-Pressure Diaphragm Valve Suppliers in Mexico
How Does An Automatic Propane Gas Changeover Valve Work?
High Pressure Nitrogen Gas Regulator Companies in the UK
Tags
Recommended Products
-
768L Stainless Steel Male Tube Butt Weld Connector | Clean Weld Fittings And Ultra-High Purity Fittings
-
Low Pressure High Flow Line Pressure Regulators And Control Valves JSR-4L Series For Laboratory Pressure Control
-
Single Stage Wall And Cabinet Mounting Pressure Control Panels JSP-2E Series For High Purity Gases
-
Semi Automatic Oxygen Nitrogen Helium Argon Gas Changeover Manifold Manual Gas Changeover Manifold Panel For Gas Cylinders
-
JR1300 Series Ultra High Purity Single Stage Regulator High Flow Line Regulator For Ultra High Purity Intermediate Flow
-
772 LF Female Branch Tee | Stainless Steel Tube Fitting Female Branch Tee 1/2 in. Tube OD x 1/2 in. Tube OD x 3/8 in. Female NPT
-
High Purity Bulk Specialty Gas Pressure Control And Filtration Bulk Gas Skid Systems JW-300-BSGS
-
High Pressure High Temperature Pneumatic Ultrahigh Purity Stainless Steel Diaphragm Valves