Blog
Jewellok is a professional pressure regulator and valve manufacturer and supplier.
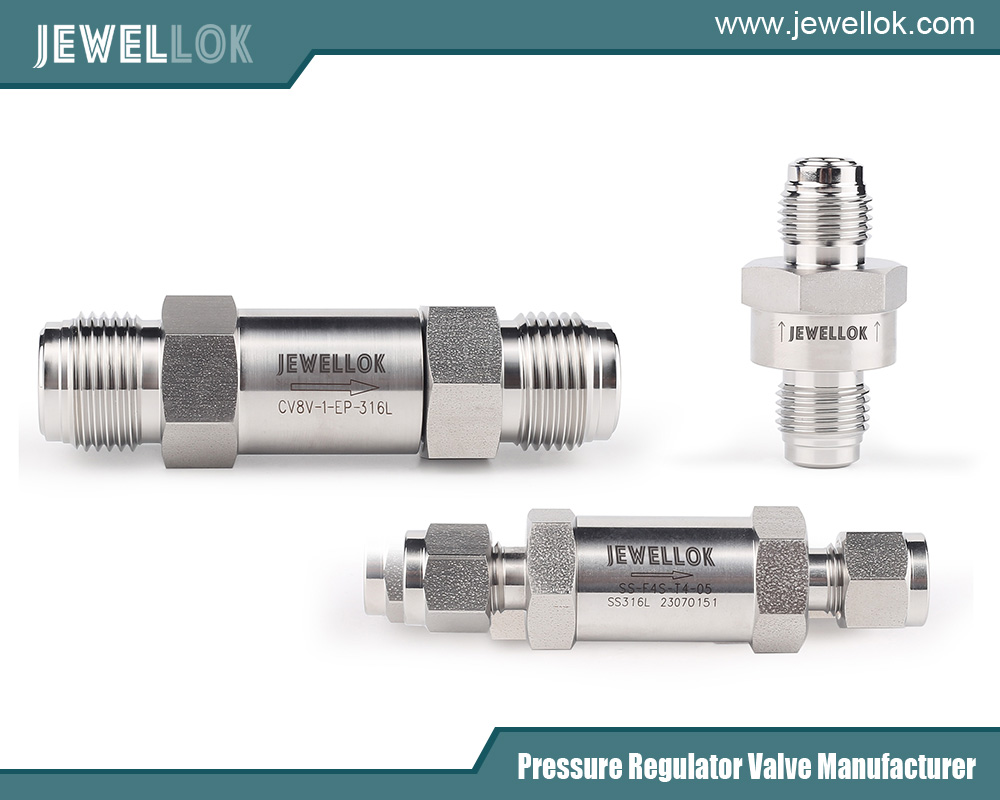
Anti-clogging Design and Maintenance Technology of Pressure Reducing Valves in Large-flow Media with Impurities
- Pressure Regulator Valve Manufacturer
- 2 inch irrigation valve, adjustable low pressure propane regulator, air compressor non return valve, argon hose connector, argon hose fittings, gas semiconductor, high purity pressure reducing valves manufacturer, high purity regulators, high-flow pressure reducing valves, high-flow pressure reducing valves factory, high-flow pressure reducing valves manufacturer, how a gas pressure regulator works, how a pressure regulator works, humming propane regulator, Hydraulic Pressure Reducing Valves, large-flow single-gauge pressure reducing valves, pressure reducing valves, pressure reducing valves factory, pressure reducing valves manufacturer, pressure regulator valve leaking, pressure relief valve vs safety valve, propane adjustable pressure regulator, propane manifold with valves, safety or relief valves, safety relief valve vs safety valve, safety valve vs pressure relief valve, second stage propaneregulator, single-gauge pressure reducing valves, timer water valve, two stage pressure regulator
- No Comments
Anti-clogging Design and Maintenance Technology of Pressure Reducing Valves in Large-flow Media with Impurities
In industrial fields such as petrochemical, water supply and drainage, and metallurgy, the media during large-flow transportation often contain impurities or particles. As a key pressure regulating device, once the pressure reducing valve is clogged by impurities, it will not only affect its pressure reducing performance but also may lead to out-of-control system pressure, equipment damage and even safety accidents. Therefore, it is of great practical significance to study the anti-clogging design and maintenance technology of pressure reducing valves in large-flow media with impurities.
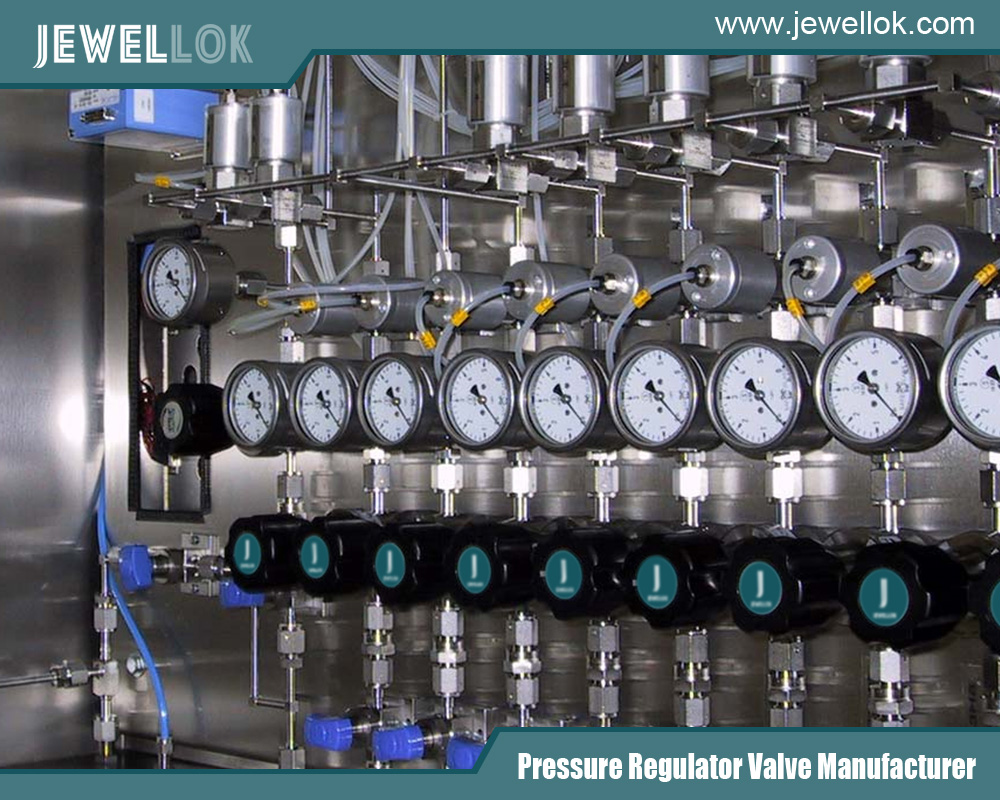
Analysis of the Main Causes of Pressure Reducing Valve Blockage
1. Influence of Medium Characteristics
Media containing impurities such as sediment, rust, suspended substances and crystallites are likely to have particles accumulate in narrow passages, throttling ports, sealing surfaces and other parts inside the valve when passing through the pressure reducing valve. Under large-flow working conditions, although the medium flow rate is relatively high, when the flow rate distribution is uneven or local vortices occur, impurities may still deposit.
2. Structural Design Defects
If the structural design of key components such as the valve core and valve seat of the traditional pressure reducing valve is unreasonable, for example, the shape of the throttling port is not conducive to the passage of impurities, or there are right angles or sharp corners in the flow channel, which will lead to poor fluid flow, and it is easy to form impurity retention areas. In addition, if the gap between the sealing surfaces is too small, fine particles may be embedded, resulting in sealing failure and blockage.
3. Influence of Working Condition Changes
During the operation of the system, if the pressure and flow rate fluctuate violently, it may cause the change of the movement state of impurities inside the pressure reducing valve, increasing the risk of their deposition and blockage. For example, during the start-up, shutdown or switching process of the system, the sudden change of the flow rate may cause the originally suspended impurities to settle.
Anti-clogging Design Technology
1. Optimize the Internal Flow Channel Structure
- Streamlined Flow Channel Design: Adopt a smooth streamlined inner cavity of the valve body, reduce right-angle bends and sudden expansion and contraction structures, make the medium flow smoothly, and reduce the probability of impurity deposition. For example, a gradually changing flow channel design similar to a Venturi tube can be adopted to ensure a uniform change in the medium flow rate.
- Large-diameter Throttling Port: Appropriately increase the size of the throttling port, reduce the local resistance when the medium passes through, and at the same time enable larger particle impurities to pass through smoothly. However, it should be noted that increasing the size of the throttling port may have a certain impact on the pressure reducing accuracy, and reasonable structural optimization and control strategies are required for compensation.
- Inclined Valve Seat: Design the valve seat at an inclined angle, and use the flow power of the medium itself to make the impurities deposited on the valve seat be automatically discharged under the action of the fluid to prevent accumulation.
2. Use Special Materials and Surface Treatment
- Wear-resistant and Corrosion-resistant Materials: Select materials with good wear resistance and corrosion resistance, such as cemented carbide, ceramics, etc., to manufacture key components such as the valve core and valve seat. These materials can not only resist the erosion and wear of impurity particles but also prevent the further blockage of the internal passages of the valve due to rust slag generated by corrosion.
- Surface Coating Treatment: Coat the inner surface of the valve with a coating with anti-friction and self-lubricating properties, such as polytetrafluoroethylene (PTFE) coating. The coating can reduce the adhesion between impurities and the inner surface of the valve, making it easier for impurities to be discharged with the medium flow.
3. Install a Filter Device
- Pre-filter: Install a suitable filter on the inlet pipeline of the pressure reducing valve to intercept larger particle impurities and reduce the blockage risk of the pressure reducing valve. The selection of the filter needs to be determined according to the medium characteristics and the requirements of the pressure reducing valve, such as the pore size of the filter screen and the filtration accuracy. For media containing more large particle impurities, a basket filter can be used; for occasions with high requirements for filtration accuracy, a bag filter or a precision filter can be selected.
- Built-in Filter Structure: Design a built-in filter element, such as a filter cartridge or a filter screen, inside the pressure reducing valve. These built-in filter structures can further filter the fine impurities in the medium without affecting the normal operation of the pressure reducing valve. At the same time, the built-in filter structure should be easy to disassemble and clean to ensure its continuous and effective filtration performance.
4. Intelligent Control and Monitoring Technology
- Pressure and Flow Monitoring: Install pressure sensors and flow sensors to monitor the pressure and flow changes at the inlet and outlet of the pressure reducing valve in real-time. When abnormal pressure fluctuations or a decrease in flow rate are detected, the system can determine that there may be a blockage situation and send out an alarm signal in a timely manner.
- Automatic Flushing Function: Set an automatic flushing device on the pressure reducing valve. When signs of blockage are detected or after a certain operating time, the flushing program is automatically started. Use high-pressure fluid to flush the internal passages of the valve to discharge the deposited impurities. The flushing program can be flexibly set according to the actual working conditions, such as flushing time, flushing pressure and other parameters.
Maintenance Technology
1. Regular Inspection and Cleaning
- External Inspection: Regularly check the appearance of the pressure reducing valve to see if there are any signs of leakage, corrosion, deformation, etc. Check whether the connecting pipelines are firm and whether there are any looseness or damage.
- Internal Cleaning: According to the medium characteristics and operating conditions, formulate a reasonable internal cleaning cycle. Disassemble the pressure reducing valve, and thoroughly clean the valve core, valve seat, flow channel and other parts to remove the deposited impurities and dirt. During the cleaning process, special cleaning agents and tools can be used to avoid damaging the inner surface of the valve. For stubborn impurities that are difficult to clean, methods such as ultrasonic cleaning can be used.
- Maintenance of the Filter Device: Regularly check the pre-filter and the built-in filter element, and replace the clogged filter screen or filter cartridge in a timely manner. At the same time, clean and check the shell of the filter to ensure its good sealing performance.
2. Inspection and Replacement of Key Components
- Sealing Component Inspection: Check the sealing components of the pressure reducing valve, such as sealing rings, sealing gaskets, etc., to see if there are any signs of wear, aging or damage. Once the sealing component fails, it should be replaced in a timely manner to ensure the sealing performance of the pressure reducing valve, prevent medium leakage and the entry of impurities.
- Wear Detection of the Valve Core and Valve Seat: Use professional detection tools, such as calipers, dial indicators, etc., to measure the size and shape of the valve core and valve seat, and judge their wear degree. When the wear exceeds the specified range, repair or replacement should be carried out to ensure the pressure reducing accuracy and normal working performance of the pressure reducing valve.
3. Performance Testing and Debugging
- Pressure Regulation Performance Test: After maintenance, conduct a pressure regulation performance test on the pressure reducing valve. By changing the inlet pressure and flow rate, check whether the outlet pressure of the pressure reducing valve can be stably maintained within the set range and whether the regulation accuracy meets the requirements.
- Flow Characteristics Test: Test the working performance of the pressure reducing valve under different flow rates and draw the flow characteristics curve. By comparing with the design curve, judge whether the flow characteristics of the pressure reducing valve have changed and whether there are blockages or other faults affecting its flow regulation ability.
- Sealing Performance Test: Conduct a sealing performance test on the pressure reducing valve to check whether there is any leakage phenomenon under the specified pressure. The air pressure test or water pressure test method can be used to ensure that the sealing performance of the pressure reducing valve meets the requirements.
4. Establish a Maintenance File
Establish a detailed maintenance file for each pressure reducing valve, recording information such as its installation time, operating parameters, maintenance situation, and fault handling records. Through the analysis and summary of the maintenance file, the operation rules and performance change trends of the pressure reducing valve can be mastered, providing a basis for formulating a reasonable maintenance plan and predictive maintenance, and improving the reliability and service life of the pressure reducing valve.
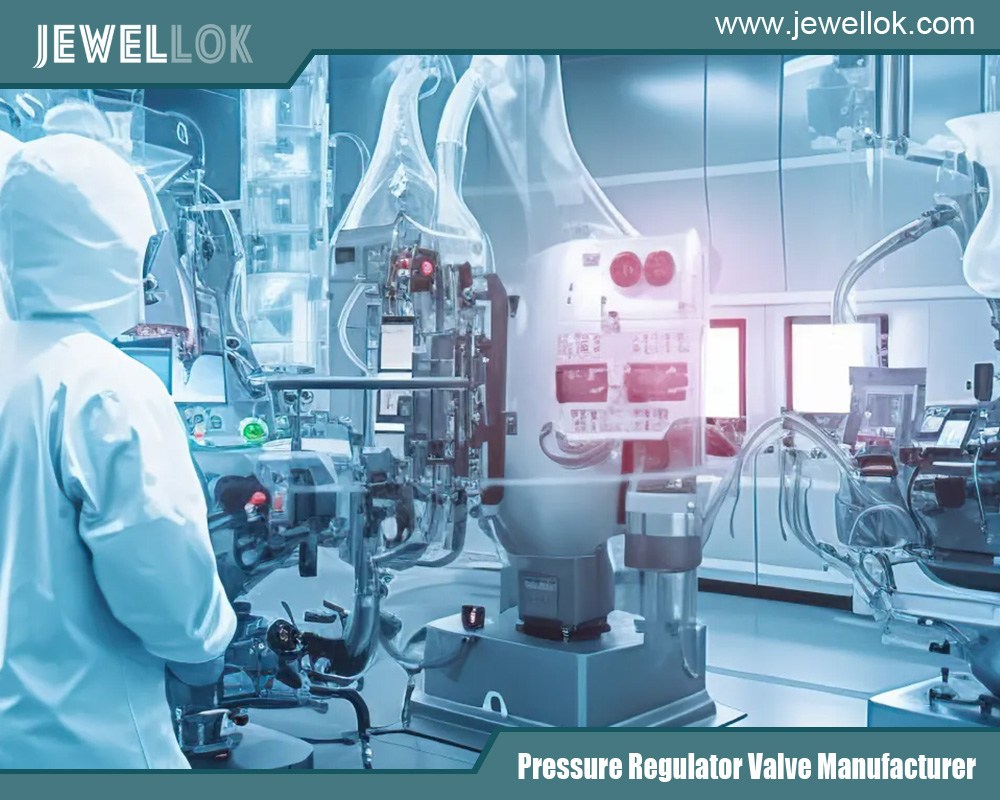
Conclusion
In large-flow media containing impurities or particles, by means of anti-clogging design measures such as optimizing the internal flow channel structure of the pressure reducing valve, using special materials and surface treatment, installing a filter device, and applying intelligent control and monitoring technology, the blockage risk of the pressure reducing valve can be effectively reduced. At the same time, scientific and reasonable maintenance technology, including regular inspection and cleaning, inspection and replacement of key components, performance testing and debugging, and establishing a maintenance file, plays an important role in ensuring the normal operation and extending the service life of the pressure reducing valve. In practical applications, according to the specific working conditions and medium characteristics, these anti-clogging design and maintenance technologies should be comprehensively applied to ensure the reliable and stable operation of the large-flow single-gauge pressure reducing valve.
For more about anti-clogging design and maintenance technology of pressure reducing valves in large-flow media with impurities, you can pay a visit to Jewellok at https://www.jewellok.com/ for more info.
Recent Posts
High-Pressure Hydraulic Needle Valve
Pneumatic Actuated Ball Valve
Industrial Diaphragm Valve
Needle Valve 10000 psi Manufacturers
Tags
Recommended Products
-
775L Bulkhead Reducing Union | Stainless Steel High Purity Double Ferrule Bulkhead Reducing Unions
-
772L Male Branch Tee | Stainless Steel High-Purity Tube Fitting Male Branch Tee
-
Stainless Steel Single Stage Semiconductor Grade Pressure Control Module Pressure Control Panels JSP-6A Series
-
High Purity Chemical Dispense System & Packing System For Semiconductors JW-200L-CDM & JW-1000L-CDM
-
Ultra High Purity Gas Delivery Systems And Liquid Chemical Delivery Systems JW-300-LDS
-
Line And Panel Mounting Adjustable Low Pressure Propane And Nitrogen Pressure Regulator JSR-3L & JSR-3LP Series
-
739LF High Purity Female Adapter Tube To Pipe Fittings And Connectors
-
UHP Metal Gasket Face Seal Fittings Vacuum Coupling Metal Face Seal Join Long Gland And Short Gland