Blog
Jewellok is a professional pressure regulator and valve manufacturer and supplier.
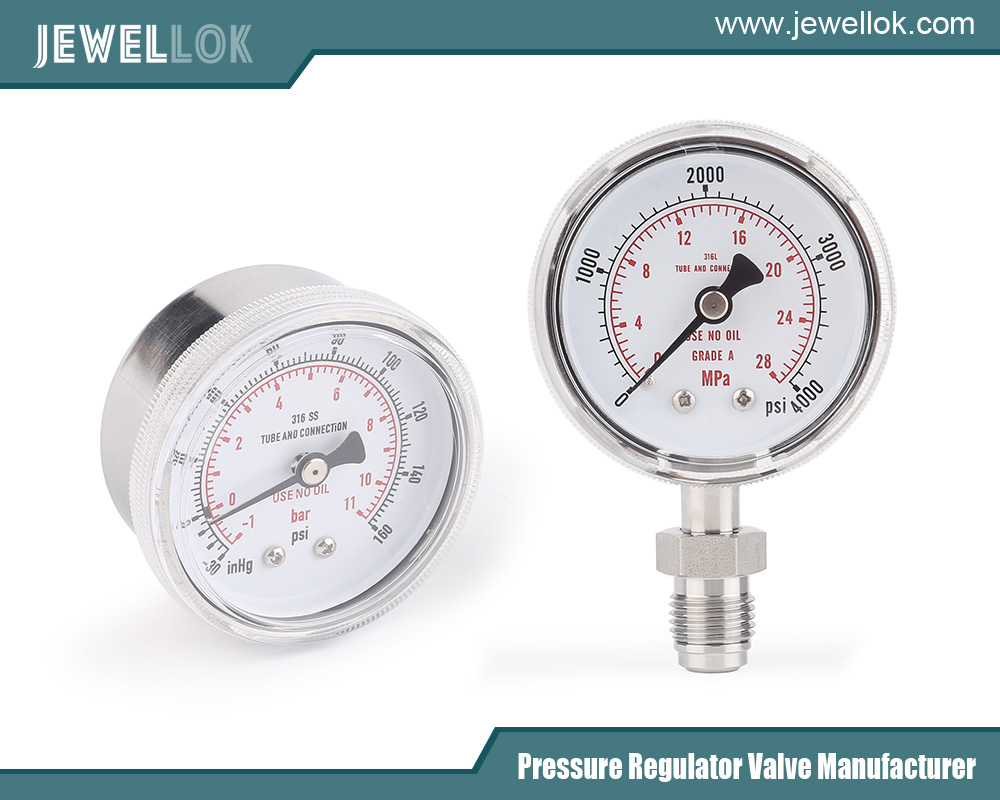
High Flow Needle Valves manufacturers
- Pressure Regulator Valve Manufacturer
- 1 1 2 gas pressure regulator, 1 2 gas regulator, 1 2 propane regulator, 1/2 gas pressure regulator, 12v electric valve, 2 electric valve, adjustable propane pressure regulator, argon gas pressure regulator, best high flow needle valves manufacturers, electric water valve, gas regulator, high flow co2 regulator, high flow needle valves factory, high flow needle valves manufacturer, high flow needle valves manufacturers, high flow needle valves market, high flow needle valves supplier, high pressure argon regulator, high purity regulator, how a solenoid works, how does a gas pressure regulator work, how does a needle valve work, industrial regulators, low pressure gas regulator, pressure regulator, pressure safety valve vs relief valve, propane pressure regulator valve, relief valve and safety valve difference, safety valve and relief valve, safety valve vs relief valve, semiconductor gas, solenoid valve working
- No Comments
High Flow Needle Valves manufacturers
In industries where precise fluid control is paramount, high flow needle valves stand out as critical components. These specialized valves combine the fine-tuned adjustability of traditional needle valves with enhanced flow capacity, making them indispensable in applications ranging from oil and gas to aerospace and chemical processing. Unlike standard needle valves, high flow variants are engineered to handle higher volumes of liquids or gases while maintaining pinpoint accuracy. This article explores the design, functionality, applications, and advantages of high flow needle valves, shedding light on why they are a preferred choice in high-stakes environments. We will also discuss material considerations, operational challenges, and emerging trends in valve technology. By understanding the unique features of high flow needle valves, engineers and professionals can make informed decisions to optimize system performance and reliability.
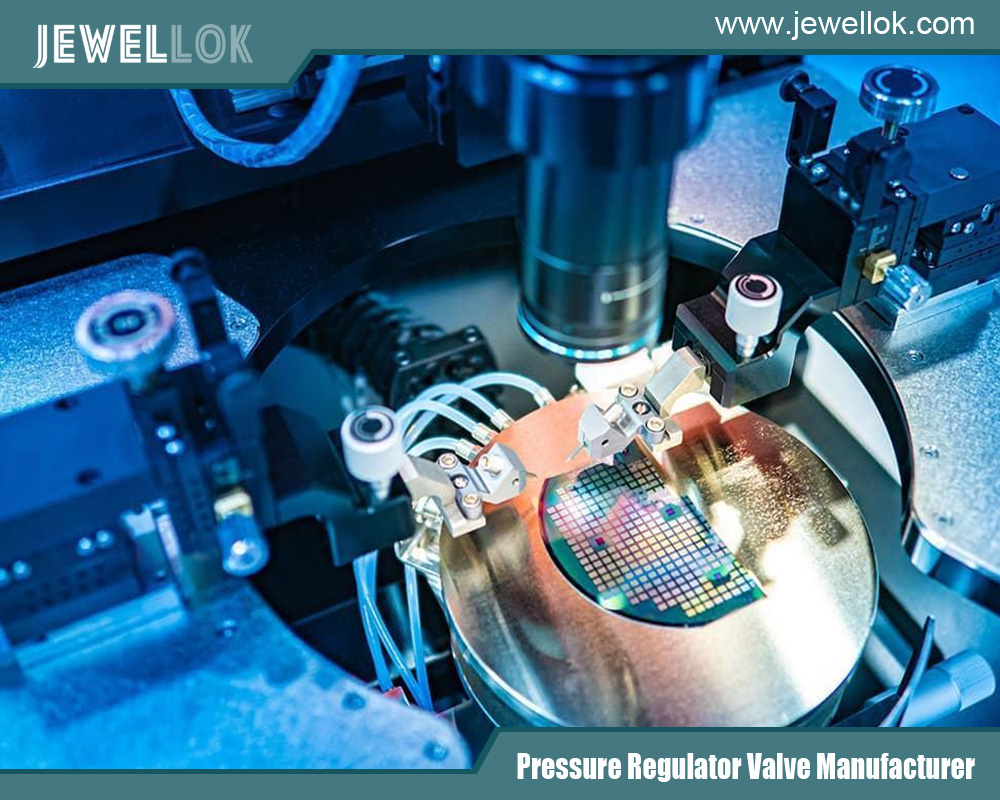
What is a High Flow Needle Valve?
A high flow needle valve is a precision-engineered device used to regulate the flow of fluids—liquids or gases—in a system. It features a long, tapered needle-like stem that fits into a conical seat, allowing for gradual and precise flow adjustments. Unlike standard needle valves, which are typically designed for low to moderate flow rates, high flow needle valves are optimized to accommodate higher flow capacities without sacrificing control accuracy.
The valve’s design includes a larger orifice and optimized internal geometry to reduce flow resistance, enabling it to handle increased volumes. Despite the higher flow, the needle’s fine threading ensures micro-adjustments, making these valves ideal for applications requiring both high throughput and precision. High flow needle valves are typically constructed from durable materials like stainless steel, brass, or exotic alloys to withstand harsh conditions, including high pressures and corrosive fluids. Their versatility and reliability make them essential in industries where fluid dynamics are critical to operational success.
Design and Working Principle
The design of a high flow needle valve is a balance of precision and capacity. At its core, the valve consists of a body, a needle stem, a seat, a bonnet, and a handle or actuator. The needle stem, which is threaded, moves in and out of the seat when the handle is turned, adjusting the size of the flow path. The tapered needle allows for gradual changes in flow, providing exceptional control even at high volumes.
In high flow models, the orifice size is larger, and the internal flow path is streamlined to minimize turbulence and pressure drop. This is achieved through computational fluid dynamics (CFD) modeling during the design phase, ensuring optimal performance. The valve may also feature a multi-turn handle for fine adjustments or a quick-acting mechanism for rapid response in dynamic systems.
High flow needle valves often incorporate advanced sealing technologies, such as PTFE or graphite packing, to prevent leaks under high pressure or temperature. Some designs include a rising stem for visual indication of valve position, while others use non-rising stems for compact installations. Automated versions with electric or pneumatic actuators are also available for integration into modern control systems.
Key Features and Benefits
High flow needle valves offer several advantages that make them suitable for demanding applications:
- Enhanced Flow Capacity: Unlike traditional needle valves, high flow models can handle significantly higher flow rates, making them ideal for systems requiring both volume and precision.
- Precision Control: The fine-threaded needle allows for minute flow adjustments, ensuring accurate regulation even in high-pressure environments.
- Durability: Constructed from robust materials like 316 stainless steel or Hastelloy, these valves resist corrosion, erosion, and wear, extending service life in harsh conditions.
- Versatility: High flow needle valves are compatible with a wide range of fluids, including gases, oils, water, and aggressive chemicals, making them adaptable to various industries.
- Low Pressure Drop: Optimized internal geometry minimizes flow resistance, reducing energy losses and improving system efficiency.
- Safety and Reliability: Leak-tight seals and robust construction ensure safe operation under extreme pressures and temperatures.
These features translate into tangible benefits, such as reduced maintenance costs, improved process control, and enhanced system uptime. For engineers, the ability to achieve precise flow regulation without compromising on throughput is a game-changer in optimizing system performance.
Applications of High Flow Needle Valves
High flow needle valves are used across a wide range of industries due to their ability to manage high flow rates with precision. Key applications include:
- Oil and Gas: In upstream, midstream, and downstream operations, high flow needle valves regulate the flow of crude oil, natural gas, and refined products. They are used in wellhead control, pipeline sampling, and pressure regulation systems.
- Chemical Processing: These valves handle aggressive chemicals and slurries, ensuring precise dosing and flow control in reactors, distillation columns, and mixing systems.
- Aerospace and Defense: High flow needle valves are critical in hydraulic and pneumatic systems for aircraft and military vehicles, where they control fuel, lubricants, and compressed gases under extreme conditions.
- Power Generation: In nuclear, fossil fuel, and renewable energy plants, these valves manage steam, cooling water, and fuel flows, contributing to efficient and safe operations.
- Pharmaceuticals: High flow needle valves ensure accurate fluid delivery in bioprocessing and drug manufacturing, where sterility and precision are paramount.
- Water Treatment: They regulate chemical dosing and water flow in treatment plants, ensuring compliance with environmental standards.
In each application, the valve’s ability to deliver high flow with fine control is critical. For example, in oil and gas pipelines, a high flow needle valve can throttle gas flow to prevent surges, while in pharmaceuticals, it ensures precise delivery of active ingredients during production.
Material Selection and Environmental Considerations
The performance of a high flow needle valve depends heavily on its material composition. Common materials include:
- Stainless Steel (316/304): Offers excellent corrosion resistance and strength, ideal for general-purpose and harsh environments.
- Brass: Cost-effective for low-pressure, non-corrosive applications like water or air systems.
- Exotic Alloys (Monel, Hastelloy, Inconel): Used in extreme conditions, such as high-temperature steam or highly corrosive fluids.
- Polymers (PTFE, PEEK): Employed for seals and seats to ensure leak-tight performance and chemical compatibility.
Material selection is guided by factors like fluid type, pressure, temperature, and environmental conditions. For instance, in offshore oil platforms, stainless steel or Hastelloy valves are preferred due to exposure to saltwater and high pressures. In contrast, brass may suffice for indoor HVAC systems.
Environmental considerations also play a role. Manufacturers are increasingly adopting sustainable practices, such as using recyclable materials and reducing waste during production. Additionally, high flow needle valves with low leakage rates contribute to environmental compliance by minimizing fugitive emissions in chemical and gas systems.
Operational Challenges and Solutions
While high flow needle valves are robust, they face challenges in demanding applications:
- Cavitation and Erosion: High flow rates can cause cavitation in liquid systems, leading to erosion of the needle and seat. Solution: Use hardened materials like tungsten carbide or ceramic coatings.
- Clogging: Particulate matter in fluids can obstruct the small orifice. Solution: Install upstream filters or choose valves with self-cleaning designs.
- High-Pressure Leakage: Extreme pressures can compromise seals. Solution: Use high-performance packing materials and regular maintenance checks.
- Thermal Expansion: Temperature fluctuations can affect valve performance. Solution: Select materials with compatible thermal expansion coefficients.
Proactive maintenance, such as periodic cleaning, lubrication, and inspection, can mitigate these issues. Additionally, choosing a valve with the right specifications—such as pressure rating, material, and flow coefficient (Cv)—ensures optimal performance and longevity.
Emerging Trends in High Flow Needle Valve Technology
The high flow needle valve market is evolving with advancements in materials, design, and automation. Key trends include:
- Smart Valves: Integration with IoT and sensors allows real-time monitoring of flow, pressure, and valve position, enabling predictive maintenance and remote control.
- Additive Manufacturing: 3D printing enables complex internal geometries, improving flow efficiency and reducing production costs.
- Eco-Friendly Designs: Manufacturers are developing low-emission valves to meet stringent environmental regulations, particularly in oil and gas.
- Compact Designs: Miniaturized high flow needle valves are gaining traction in space-constrained applications like aerospace and medical devices.
These innovations are expanding the capabilities of high flow needle valves, making them more efficient, reliable, and adaptable to modern industrial needs.
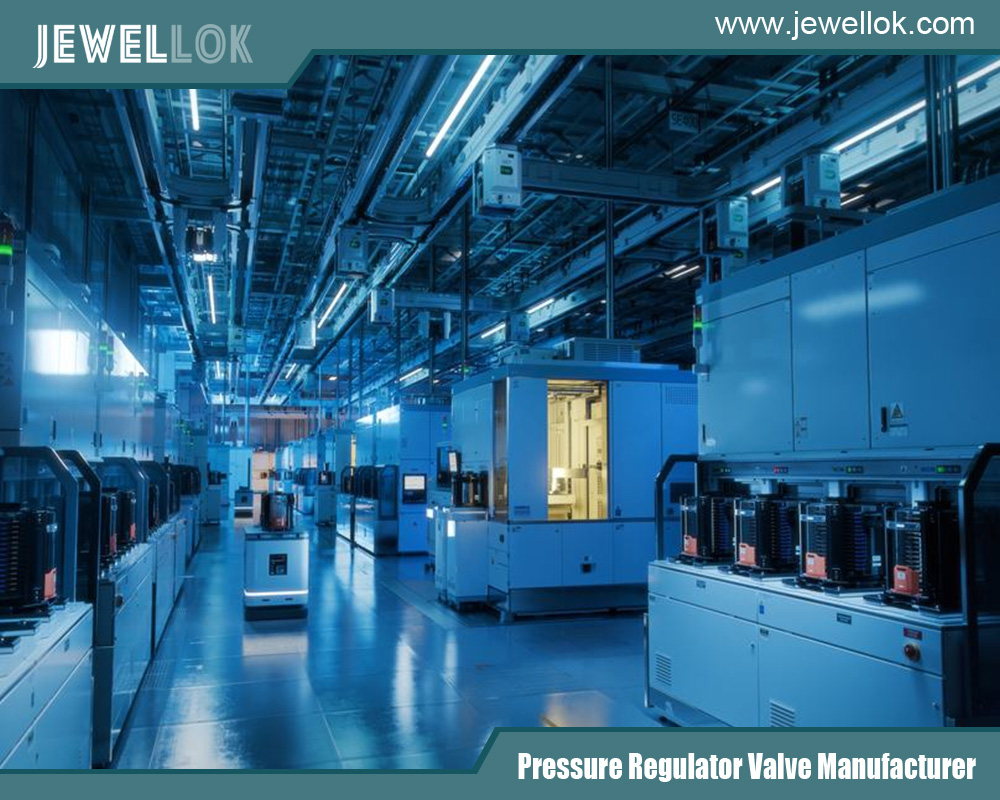
Conclusion
High flow needle valves are a cornerstone of fluid control in industries requiring both high throughput and precision. Their robust design, versatility, and ability to handle demanding conditions make them invaluable in applications from oil and gas to pharmaceuticals. By selecting the right materials, addressing operational challenges, and leveraging emerging technologies, engineers can maximize the performance of these valves. As industries evolve, high flow needle valves will continue to play a critical role in ensuring efficiency, safety, and reliability in fluid management systems, solidifying their place as a vital component in modern engineering.
For more about the best high flow needle valves manufacturers, you can pay a visit to Jewellok at https://www.jewellok.com/ for more info.
Recent Posts
Pressure Control Valve Manufacturers
High Flow Needle Valves manufacturers
High-Pressure Hydraulic Needle Valve
Pneumatic Actuated Ball Valve
Tags
Recommended Products
-
Low Pressure High Flow Line Pressure Regulators And Control Valves JSR-4L Series For Laboratory Pressure Control
-
764LR Stainless Steel 316 Reducing Tee UHP Fitting Automatic Buttweld Reducing Tee
-
Line And Panel Mounting Adjustable Low Pressure Propane And Nitrogen Pressure Regulator JSR-3L & JSR-3LP Series
-
Pressure Control Panels For High Purity Gas Control System JSP-3AE Series From Pressure Control Panels Suppliers And Manufacturer
-
Ultra High Purity Pressure Gauge For Laboratory And Semiconductor JR Series
-
High Purity Stainless Steel Mini Tube Butt Weld Fittings For Semiconductor
-
Fully Automated Gas Cabinet For Precise UHP Gas Delivery And High Purity Gas Delivery Systems JW-300-GC
-
Fully Automated Gas Cabinet Gas Rack Gas Delivery Systems JW-300-GR