Blog
Jewellok is a professional pressure regulator and valve manufacturer and supplier.
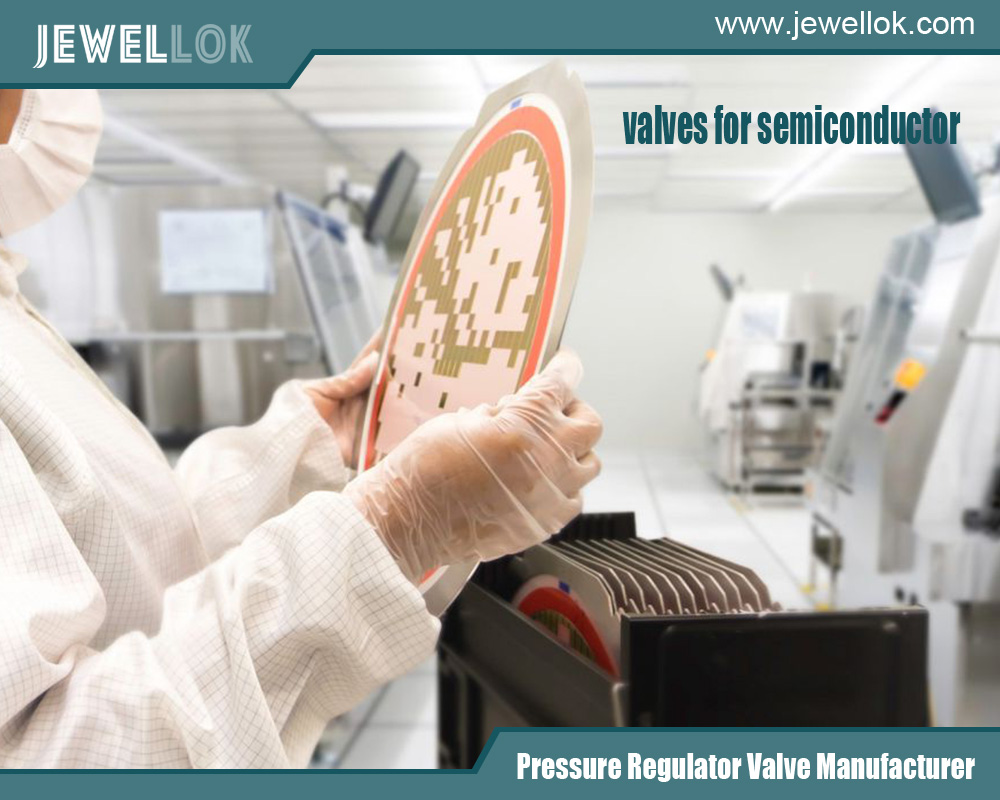
An Overview Of Centralized Gas Supply Control Systems In The Semiconductor Industry
- Pressure Regulator Valve Manufacturer
- Central Gas and Chemical Supply Systems, Central Gas Distribution Systems, Central Gas Installation Systems, Central Gas Supply System in Hospitals, Central Gas Supply Systems, Centralized Gas Pipeline System, Centralized gas supply control system china, Centralized gas supply control systems, Centralized gas supply control systems manufacturer, Centralized gas supply system in residential building, China central gas supply manufacturers, Custom solutions for central gas supply, Gas supply and control systems, Hospital Central Gas Supply Systems, Integrated Central Medical Gas Supply System, Laboratory Central Gas Supply System, LPG Central Gas Systems, LPG Pressure Control System, Pressure Regulators and Central Gas Supply Systems Vietnam
- No Comments
An Overview Of Centralized Gas Supply Control Systems In The Semiconductor Industry
Centralized gas supply control systems are the backbone of modern semiconductor manufacturing, ensuring the precise, safe, and efficient delivery of gases to various processes within a fabrication facility (fab). These systems manage the storage, purification, and distribution of gases from a central hub to multiple points of use, meeting the industry’s stringent requirements for purity, pressure stability, and safety. This article provides a comprehensive overview of centralized gas supply control systems in the semiconductor industry, exploring the types of gases used, system components, design considerations, advantages, challenges, real-world examples, and future trends. It aims to offer a detailed yet accessible insight into this critical technology.
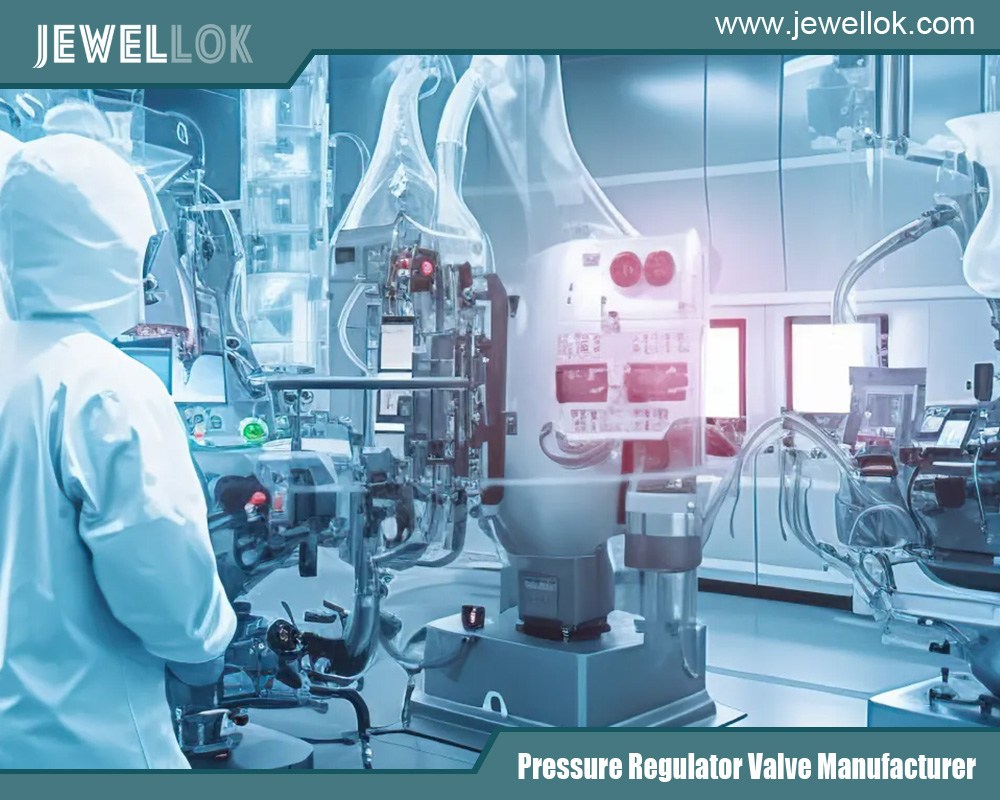
Introduction
The semiconductor industry relies heavily on advanced technologies to produce microchips that power everything from smartphones to medical devices. Among these technologies, centralized gas supply control systems play a pivotal role by delivering a consistent supply of ultra-pure gases to manufacturing processes such as etching, deposition, and cleaning. Unlike decentralized systems, where gas cylinders are placed near individual tools, centralized systems consolidate gas storage and control, distributing gases through a network of pipelines to multiple process stations. This centralization enhances safety, efficiency, and scalability—key priorities in an industry where even minor deviations can lead to costly defects. This article will cover the essential aspects of these systems, starting with the gases they handle, followed by their components, design principles, benefits, challenges, practical applications, and emerging innovations.
Types of Gases Used in Semiconductor Manufacturing
Semiconductor manufacturing employs a diverse array of gases, each tailored to specific stages of production. Understanding these gases and their roles is fundamental to appreciating the importance of centralized supply systems.
Nitrogen (N₂): The most widely used gas, nitrogen serves as an inert atmosphere for purging equipment and preventing oxidation during processes like wafer annealing.
Argon (Ar): Essential in physical vapor deposition (PVD) and sputtering, argon creates plasma to deposit thin films onto wafers.
Oxygen (O₂): Used in oxidation processes to grow silicon dioxide layers and in plasma cleaning to remove organic residues.
Hydrogen (H₂): Critical for annealing, where it reduces oxides on wafer surfaces, and as a carrier gas in some deposition processes.
Helium (He): Employed for leak detection due to its small atomic size and as a cooling gas in certain tools.
Specialty Gases: These include silane (SiH₄) for silicon deposition, ammonia (NH₃) for nitridation, and chlorine (Cl₂) or fluorine-based gases for etching intricate patterns into wafers.
The semiconductor industry demands ultra-high purity for these gases, often exceeding 99.9999% (six nines), as even trace contaminants—such as moisture or particulates—can introduce defects into microchip layers. For example, in chemical vapor deposition (CVD), impurities in silane can alter film properties, reducing device performance. Centralized systems are designed to maintain this purity from storage to delivery, ensuring consistent process outcomes across the fab.
Components of Centralized Gas Supply Systems
A centralized gas supply system integrates multiple components to store, purify, regulate, and distribute gases effectively. Here’s a breakdown of the key elements:
Gas Cylinders or Bulk Storage Tanks: High-volume gases like nitrogen and oxygen are stored in large cryogenic tanks, while specialty gases are kept in high-pressure cylinders. Bulk storage is preferred for cost efficiency and continuous supply in large fabs.
Pressure Regulators: These devices reduce the high pressure from storage units to a stable, usable level for process tools, preventing fluctuations that could disrupt manufacturing.
Filters and Purifiers: Positioned downstream of storage, these remove impurities such as water vapor, hydrocarbons, and particulates. Purifiers often use chemical or physical adsorption to achieve the required purity levels.
Distribution Manifolds: These systems of valves and piping direct gases from the central supply to various fab locations. Automated manifolds allow for precise control and isolation of gas flows.
Monitoring and Control Systems: Equipped with sensors for pressure, flow rate, and purity, these systems provide real-time data and trigger alarms or adjustments if parameters deviate from set points. Integration with fab automation software enhances oversight.
The system operates as a cohesive unit: gas is drawn from storage, purified, pressure-adjusted, and distributed through electropolished stainless-steel tubing—a material chosen for its resistance to corrosion and minimal outgassing. This setup ensures that gases reach process tools in the exact condition required, supporting the high precision of semiconductor manufacturing.
Design Considerations for Centralized Systems
Designing a centralized gas supply system involves balancing multiple factors to meet the semiconductor industry’s rigorous demands:
Safety: Handling toxic (e.g., ammonia), flammable (e.g., hydrogen), or asphyxiant (e.g., nitrogen) gases requires robust safety features. Leak detectors, emergency shut-off valves, and exhaust systems are standard, as is compliance with standards like SEMI S2 and local regulations.
Efficiency: Minimizing gas waste is a priority, achieved through optimized piping layouts and automated flow controls that match supply to demand.
Scalability: As fabs expand or adopt new processes, systems must accommodate additional gas types or higher volumes. Modular designs with extra capacity are often employed.
Reliability: Redundancy—such as backup cylinders or dual supply lines—ensures uninterrupted operation, critical in an industry where downtime can cost millions.
The physical layout must also minimize pressure drops over long distances and ensure uniform delivery to all tools. Engineers use computational modeling to optimize pipe diameters and routing, while regular audits verify compliance with safety and performance standards.
Advantages of Centralized Systems
Centralized gas supply systems offer significant benefits that make them indispensable in modern semiconductor fabs:
Improved Safety: Centralized monitoring reduces the risk of human error, and automated shut-offs mitigate hazards like leaks. Consolidating gas storage away from process areas further enhances safety.
Reduced Operational Costs: Bulk storage and efficient distribution lower gas procurement and handling costs compared to decentralized cylinder-based systems.
Enhanced Process Control: Consistent pressure and purity improve manufacturing repeatability, boosting yield and product quality.
Simplified Maintenance: Centralized systems streamline inventory tracking and servicing, reducing labor and downtime compared to managing numerous point-of-use cylinders.
These advantages translate into tangible gains for large-scale operations, where precision and cost-efficiency are critical drivers of success.
Challenges and Solutions
While centralized systems are highly effective, they face several challenges that require proactive management:
Gas Contamination: Impurities introduced during storage or distribution can ruin wafers. Advanced purifiers and rigorous quality checks at multiple stages prevent this issue.
Pressure Fluctuations: Variations in demand across the fab can destabilize pressure. Buffer tanks and high-precision regulators maintain consistency.
System Downtime: Component failures can halt production. Redundant designs and predictive maintenance—using sensors to anticipate issues—minimize disruptions.
Training personnel to handle complex systems and maintaining detailed standard operating procedures (SOPs) are also essential to address the diverse properties of gases like corrosiveness or reactivity.
Case Studies or Examples
Real-world applications illustrate the impact of centralized gas supply systems:
Taiwan Semiconductor Fab: A leading manufacturer implemented a centralized system to manage over 20 gases, including silane and nitrogen trifluoride (NF₃). With automated purity monitoring and pressure stabilization, the fab reduced gas-related defects by 15% and cut costs by 10% through optimized usage.
U.S. Fab with IoT Integration: A facility adopted a system with Internet of Things (IoT) sensors for real-time diagnostics. This enabled predictive maintenance, reducing unplanned downtime by 20% and extending component lifespans by identifying wear early.
These examples demonstrate how centralized systems enhance efficiency, reliability, and quality in semiconductor production.
Future Trends and Innovations
The evolution of centralized gas supply systems is shaped by technological advancements and industry needs:
Automation and AI: Machine learning algorithms are being integrated to predict maintenance needs and optimize gas flows, reducing waste and improving uptime.
Sustainability: Systems designed to recycle unused gases or reduce energy consumption align with the industry’s push for greener practices.
Modular Designs: Flexible, plug-and-play systems allow fabs to adapt quickly to new processes or gas requirements without extensive retrofitting.
These trends promise to make gas supply systems more efficient, cost-effective, and environmentally friendly, supporting the semiconductor industry’s growth and innovation.
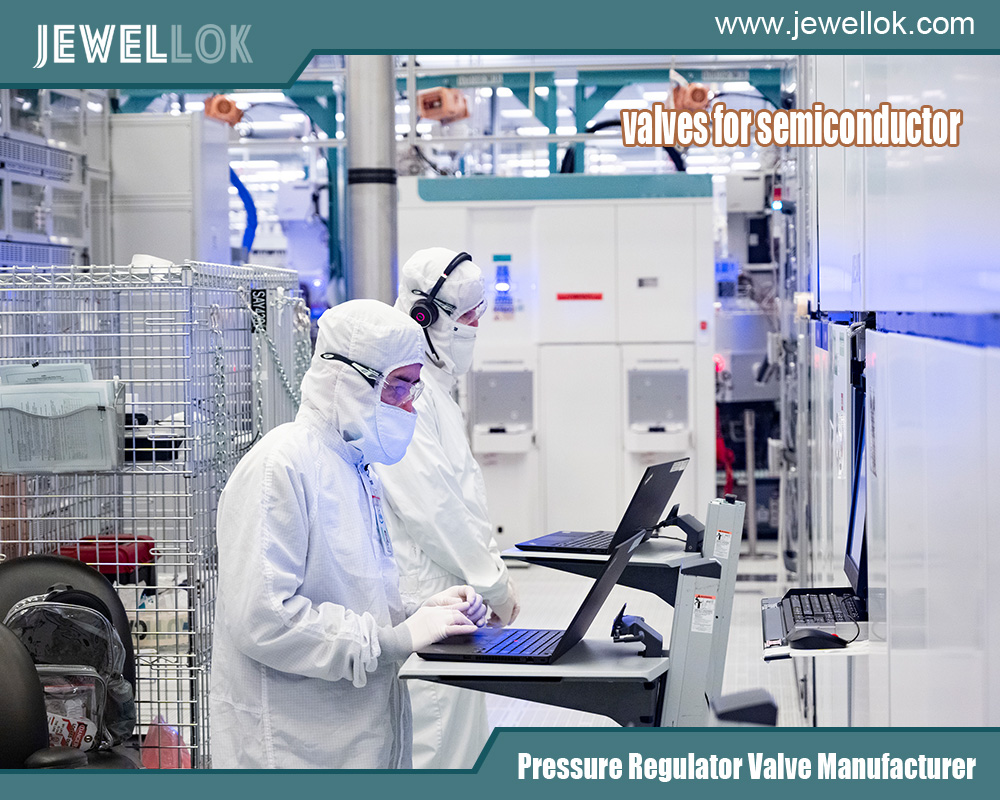
Conclusion
Centralized gas supply control systems are a cornerstone of semiconductor manufacturing, delivering the precision and reliability needed to produce cutting-edge microchips. By managing a complex array of gases through integrated components, these systems ensure safety, efficiency, and scalability while addressing challenges like contamination and downtime. Real-world successes underscore their value, and emerging innovations signal a future of even greater performance. As the semiconductor industry continues to advance, centralized gas supply systems will remain essential, underpinning the production of technologies that shape our world.
For more about an overview of centralized gas supply control systems in the semiconductor industry, you can pay a visit to Jewellok at https://www.jewellok.com/semiconductor/ for more info.
Recent Posts
The Applications, Principles and Types of Water Solenoid Valve
Medical Oxygen Regulator Manufacturers in France
How Does a Bulk Specialty Gas Delivery System (BSGS) Work?
Tags
Recommended Products
-
JR1300 Series Ultra High Purity Single Stage Regulator High Flow Line Regulator For Ultra High Purity Intermediate Flow
-
Hydrogen Manifold Argon Gas Manifold System Oxygen Manifold Propane Gas Manifold With Valves In Gas Manifold Changeover System
-
High Purity Semi-Auto Stainless Steel Changeover Manifold System, Nitrogen High Pressure Control Panel With Semiconductor Valve Manifold Box Diaphragm Valves
-
JR1000 Series UHP Ultra High Purity Single Stage Pressure Reducing Regulator And Low To Intermediate Flow
-
VMB Valve Manifold Panels And Boxes High Purity Configurable Systems JW-200-VMB & JW-100-VMB
-
High Purity High Pressure Specialty Gas Pressure Regulators Specialty Gases Pipeline Engineering Equipments Manufacturer And Supplier
-
Stainless Steel Single Stage Semiconductor Grade Pressure Control Module Pressure Control Panels JSP-6A Series
-
Integrated Gas System (IGS) Modular Integrated Gas Systems (TMS) Integrated Gas Supply System For Semiconductor And Laboratory