Blog
Jewellok is a professional pressure regulator and valve manufacturer and supplier.
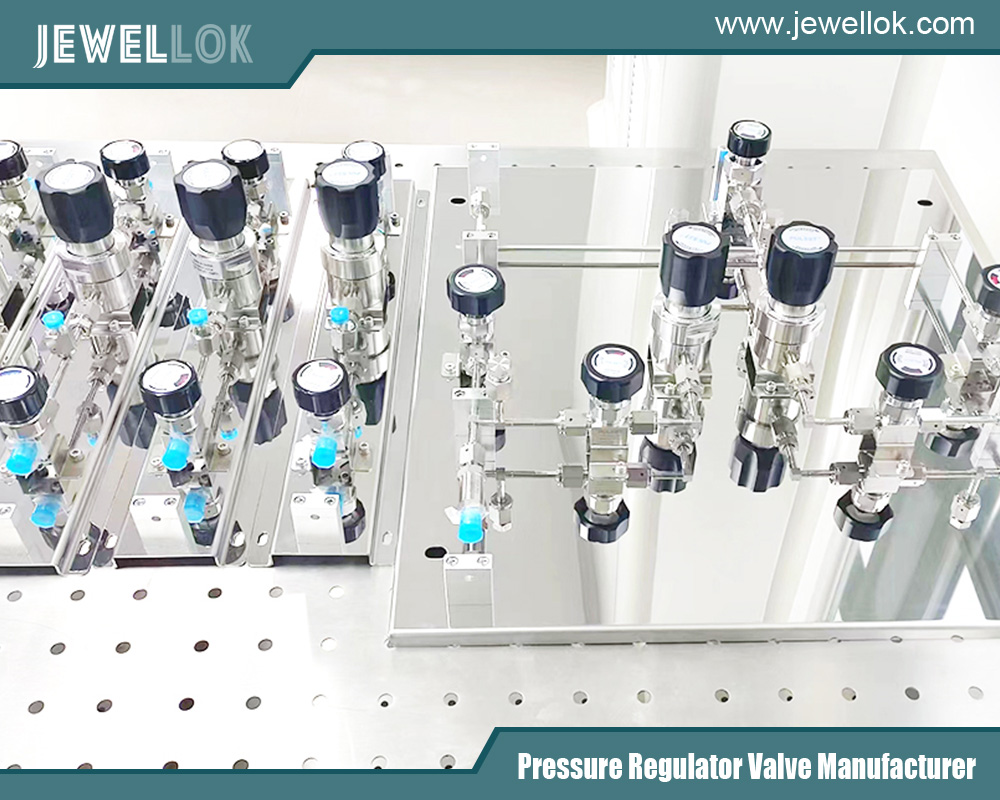
Analysis of Electrostatic Treatment Technology for Diaphragm Valves in Ultra-High Purity Environments
- Pressure Regulator Valve Manufacturer
- 1 2 gas regulator, 8mm compression fitting, china semiconductor diaphragm valves manufacturers, chinese propane gas cylinder, diaphragm valves, diaphragm valves factory, Diaphragm Valves for Ultra High-Purity Gas Systems, diaphragm valves manufacturer, Diaphragm Valves Manufacturer Mumbai, diaphragm valves supplier, excess flow valve, fluid systems components, gas manifold system, gas pipeline valve, gas pipeline valves, high purity diaphragm valves malaysia, hydraulic regulator, irrigation timer valve, pressure regulator, pressure relief valve vs safety relief valve, quick connect valve, safety valve and relief valve difference, semiconductor diaphragm valves, semiconductor diaphragm valves manufacturers, single stage pressure regulator, Two-Step Pneumatic Diaphragm Valves, ultra high purity, Ultra High Purity Diaphragm Valves, valve timer water
- No Comments
Analysis of Electrostatic Treatment Technology for Diaphragm Valves in Ultra-High Purity Environments
In ultra-high purity environments that are sensitive to static electricity, such as semiconductor manufacturing, high-end pharmaceutical production, and optical instrument manufacturing, any slight accumulation and discharge of static electricity can lead to serious consequences. For ultra-high purity diaphragm valves, dealing with static electricity issues, preventing static electricity accumulation and discharge is crucial to ensuring product quality, stable equipment operation, and personnel safety.
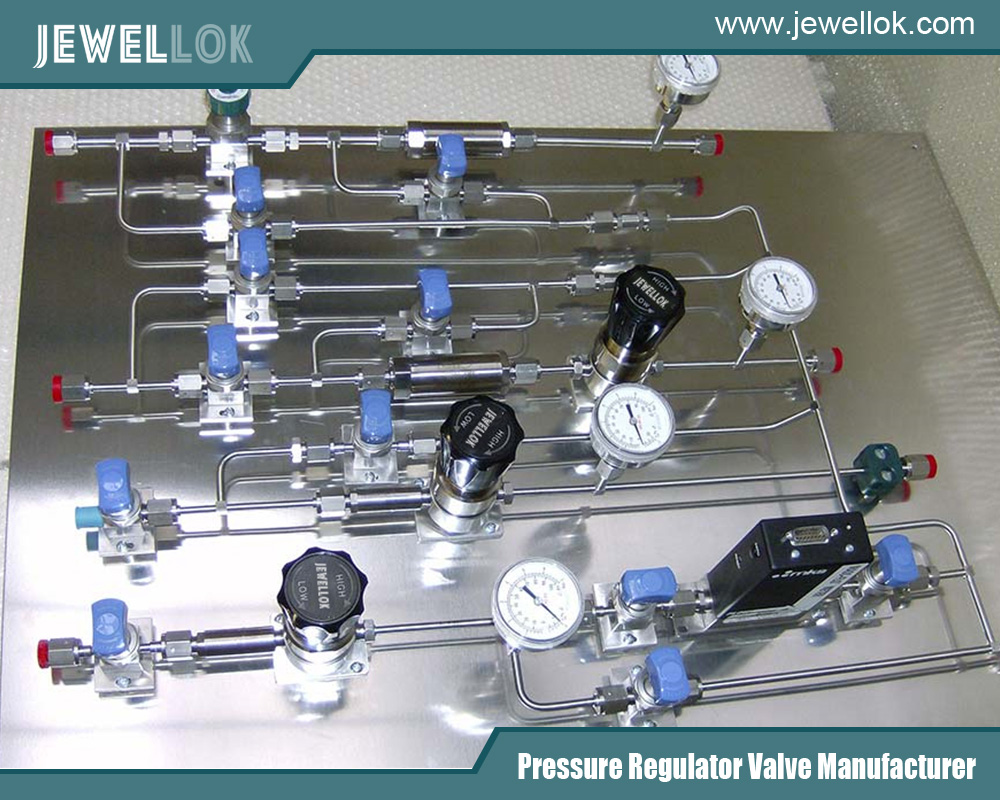
Hazards of Static Electricity in Ultra-High Purity Environments
In ultra-high purity environments, the hazards of static electricity are mainly reflected in the following aspects:
- Impact on product quality: In the semiconductor manufacturing process, the manufacturing precision of chips reaches the nanometer level. The instantaneous high voltage generated by static electricity discharge may break down the tiny circuit structures in the chips, causing short circuits or open circuits in the circuits and rendering the chips useless. In the pharmaceutical industry, static electricity may attract dust, microorganisms, and other impurities in the air, contaminating the drugs and affecting the purity and efficacy of the drugs.
- Interference with the normal operation of equipment: Static electricity accumulation may cause electronic components of the equipment to be interfered with, resulting in malfunctions, data transmission errors, and other problems in the equipment. For example, on an automated production line, static electricity may interfere with the signal transmission of sensors, causing the control system to make wrong judgments and affecting the stability of the production process.
- Triggering of safety accidents: In ultra-high purity environments where flammable and explosive gases or dust exist, the sparks generated by static electricity discharge may trigger explosions or fires, causing serious casualties and property losses.
Causes of Static Electricity Generation in Diaphragm Valves
- Friction during medium flow: When the ultra-high purity diaphragm valves medium flows inside the diaphragm valve, it will rub against components such as the diaphragm and the valve body. Due to the different abilities of the atomic nuclei of different substances to bind electrons, electrons will be transferred during the friction process, causing the diaphragm valve to become charged with static electricity. For example, when transporting high-purity chemical gases, the friction between the gas and the inner surface of the diaphragm valve is likely to generate static electricity.
- Mechanical movement: During the opening and closing process of the diaphragm valve, relative movements such as those between the valve stem and the seal, and between the diaphragm and the valve seat will also generate friction, thereby generating static electricity. In addition, mechanical actions such as the vibration and impact of the valve may also lead to the generation of static electricity.
- Environmental factors: The environmental humidity has a significant impact on the generation and accumulation of static electricity. In a dry environment, the charges on the surface of objects are not easy to dissipate, and it is easy to form static electricity accumulation. In a high-humidity environment, water molecules can form a thin water film on the surface of objects, making it easier for charges to conduct and dissipate, thereby reducing the generation of static electricity. Changes in temperature can also cause the expansion and contraction of materials, changing the contact and separation between different materials, and thus generating static electricity.
Special Designs and Measures for Diaphragm Valves to Deal with Static Electricity Issues
Grounding Design
- Direct grounding: Reliably connect the valve body of the diaphragm valve to the ground through a grounding wire, so that the static electricity on the valve body can be quickly conducted to the ground to avoid static electricity accumulation. The grounding wire should have sufficient cross-sectional area and good electrical conductivity to ensure the smooth discharge of static electricity. In some occasions with extremely high requirements for static electricity, special grounding systems such as multi-point grounding and independent grounding are also used to improve the reliability of grounding.
- Indirect grounding: For some diaphragm valves that cannot be directly grounded, static electricity dissipation devices such as static grounding clips and static grounding straps can be installed to indirectly conduct the static electricity to the ground. The static grounding clip is usually clamped on the metal part of the valve and conducts the static electricity through the internal conductive element; the static grounding strap is a conductive strap that is wound around the valve to achieve the dissipation of static electricity.
Material Selection
- Application of anti-static materials: Select anti-static materials to manufacture key components of the diaphragm valve, such as the valve body, diaphragm, valve stem, etc. Some special plastic materials, by adding conductive fillers (such as carbon fiber, metal powder, etc.), make them have good electrical conductivity and can effectively prevent the accumulation of static electricity. In some high-end diaphragm valves, anti-static rubber is used to make the diaphragm. This rubber not only has good sealing performance but also can conduct static electricity out in a timely manner.
- Compatibility of materials: When selecting anti-static materials, the compatibility between the materials and the ultra-high purity medium also needs to be considered to ensure that the materials will not affect the purity of the medium. For example, the materials selected for the diaphragm valves used in semiconductor manufacturing must meet the requirements of resistance to various chemical substances in the semiconductor process and will not undergo chemical reactions or release impurities.
Structural Optimization
- Reduce friction points: By optimizing the internal structure of the diaphragm valve, reduce the friction points during the flow of the medium and mechanical movement, thereby reducing the generation of static electricity. For example, adopt a smooth flow channel design, reduce the protrusions and sharp corners inside the valve, so that the medium can flow smoothly and reduce friction; improve the matching method between the valve stem and the seal, and use seal materials with a low friction coefficient to reduce the friction during mechanical movement.
- Increase static electricity dissipation channels: In the structural design of the diaphragm valve, add special static electricity dissipation channels to enable the static electricity to be quickly conducted from the generation site to the grounding site. For example, set up conductive channels inside the valve body to connect components such as the diaphragm and the valve stem to the grounding end to ensure that the static electricity can be dissipated in a timely manner.
Auxiliary Measures
- Install static eliminators: Install static eliminators such as ion air guns and static elimination rods on the inlet and outlet pipelines of the diaphragm valve. These devices can generate charges opposite to the static electricity to neutralize the static electricity on the medium inside the pipeline and the surface of the valve, thereby eliminating the hazards of static electricity. The ion air gun neutralizes the static electricity by blowing out an air flow with positive and negative ions; the static elimination rod uses the principle of tip discharge to ionize the molecules in the surrounding air, generating positive and negative ions to achieve the purpose of eliminating static electricity.
- Control environmental conditions: Strictly control the humidity and temperature of the ultra-high purity environment to maintain the stability of the environment. Generally, controlling the environmental humidity within the range of 40% – 60% can effectively reduce the generation of static electricity. At the same time, use equipment such as air conditioners and dehumidifiers to ensure that the environmental temperature is within an appropriate range and avoid static electricity problems caused by temperature changes.
- Regular maintenance and inspection: Regularly maintain and inspect the diaphragm valve, check whether the grounding connection is reliable, whether the anti-static materials are damaged, and whether the static eliminators are working properly. Discover and solve potential static electricity problems in a timely manner to ensure that the static electricity protection performance of the diaphragm valve is always in good condition.
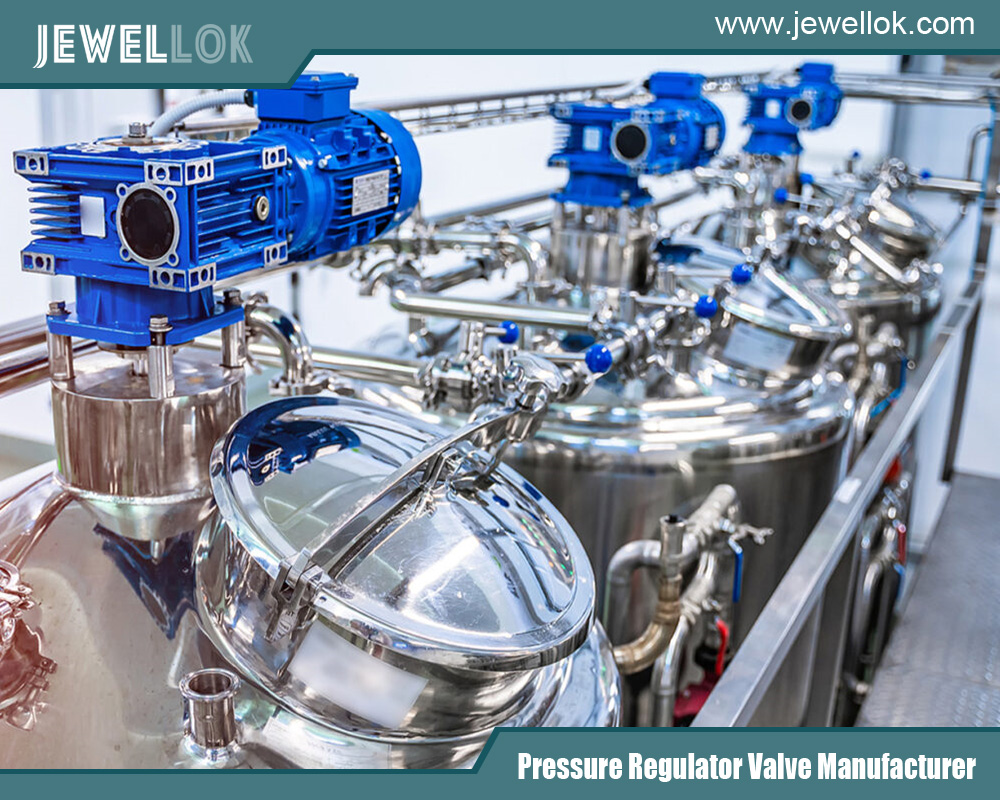
Common Industry Application Cases
- Semiconductor manufacturing industry: In the chip manufacturing process, the ultra-high purity diaphragm valves used need to have extremely high static electricity protection performance. A semiconductor manufacturing enterprise has adopted diaphragm valves with anti-static designs, and with a complete grounding system and environmental control measures, it has effectively reduced the impact of static electricity on the chip manufacturing process and improved the yield rate of chips. Through regular maintenance and inspection of the diaphragm valves, the stable operation of the valves is ensured, providing a reliable guarantee for the enterprise’s production.
- Pharmaceutical industry: In the drug production process, preventing the contamination of drugs by static electricity is of vital importance. A pharmaceutical enterprise installed diaphragm valves made of anti-static materials in the fluid conveying system of its aseptic production workshop and installed static eliminators in the workshop, and strictly controlled the environmental humidity and temperature. These measures effectively avoided the impact of static electricity on the quality of drugs and ensured the safety and effectiveness of the drugs.
In ultra-high purity environments that are sensitive to static electricity, through reasonable grounding design, material selection, structural optimization, and the application of auxiliary measures, ultra-high purity diaphragm valves can effectively deal with static electricity problems, prevent static electricity accumulation and discharge, and ensure product quality and the stable operation of equipment. With the continuous progress of science and technology, the static electricity treatment technology of ultra-high purity diaphragm valves will continue to develop and improve in the future to meet the strict requirements for static electricity protection in more high-end fields.
For more about analysis of electrostatic treatment technology for diaphragm valves in ultra-high purity environments, you can pay a visit to Jewellok at https://www.jewellok.com/ for more info.
Recent Posts
The Applications, Principles and Types of Water Solenoid Valve
Medical Oxygen Regulator Manufacturers in France
How Does a Bulk Specialty Gas Delivery System (BSGS) Work?
Tags
Recommended Products
-
Stainless Steel Ultra Clean Welding Joint Fittings TW Series TRW Series & CW Series
-
Single Stage Wall And Cabinet Mounting Pressure Control Panels JSP-2E Series For High Purity Gases
-
FT-BOX JW-FTB-C Valve Manifold Panels And Boxes With High Purity Configurable Systems
-
Semi Automatic Oxygen Nitrogen Helium Argon Gas Changeover Manifold Manual Gas Changeover Manifold Panel For Gas Cylinders
-
UHP Metal Gasket Face Seal Fittings Vacuum Coupling Metal Face Seal Join Long Gland And Short Gland
-
JR1300 Series Ultra High Purity Single Stage Regulator High Flow Line Regulator For Ultra High Purity Intermediate Flow
-
Flow Control Stainless Steel Low Pressure Manual Diaphragm Valve For High Purity And Ultra High Purity Gases
-
774L Stainless Steel UHP Fittings Butt Weld Bulkhead Union For High Flow Special Gas Fluid