Blog
Jewellok is a professional pressure regulator and valve manufacturer and supplier.
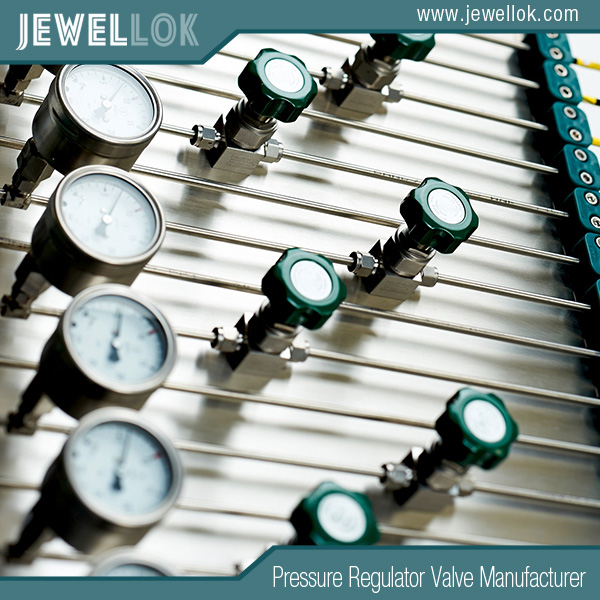
Auxiliary Gas Racks: Practical Equipment for Gas Management and Storage
- Pressure Regulator Valve Manufacturer
- adjusting propane regulator, argon hose fitting, Auxiliary Gas Racks, Auxiliary Gas Racks Manufacturer, Auxiliary Gas Racks Supplier, bcf connector, block & bleed valve, characteristics of pressure, chinese propane gas cylinder, diaphram valve, double block & bleed, double block and bleed valve, double block bleed valve, equipment for gas management and storage, excess flow valve, fusible plug, gas filter, gas regulator, gas used in semiconductor manufacturing, high pressure flexible hose, how a solenoid valve works, hydraulic regulator, industrial grade purity, low pressure regulator, o ring face seal fittings, pressure gauge fitting - 3/8 qc, pressure gauge manufacturers, pressure relief valve vs safety relief valve, quick connect, quick connect valve, relief vs safety valve, safety relief valve vs pressure relief valve, solenoid valve for ammonia gas 1 inch pipe, solenoid water valve, stainless pressure regulator, ultra high purity, water solenoid valve 24v
- No Comments
Auxiliary Gas Racks: Practical Equipment for Gas Management and Storage
Compressed gas cylinders are indispensable in industries such as oil and gas, chemical processing, hydro
gen energy, pharmaceuticals, semiconductors, welding, and laboratories, delivering gases like nitrogen, oxygen, hydrogen, helium, and acetylene for critical processes. However, managing and storing these cylinders poses significant challenges due to their high pressure, hazardous properties, and strict regulatory requirements. Auxiliary gas racks—specialized storage systems designed to hold, organize, and secure gas cylinders—are practical solutions that enhance safety, efficiency, and compliance in gas management. These racks prevent accidents, optimize space, and streamline operations, making them essential for facilities handling multiple cylinders. Selecting the right gas rack requires understanding their types, features, safety standards, and application-specific needs. This article provides a comprehensive guide to auxiliary gas racks, exploring their design, benefits, selection criteria, safety considerations, regulatory compliance, and emerging trends, offering practical insights to ensure safe and effective gas management and storage.
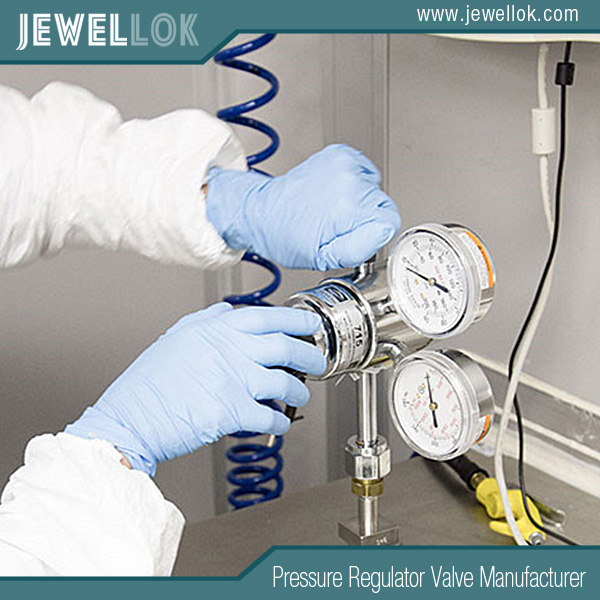
What Are Auxiliary Gas Racks?
Auxiliary gas racks are robust, purpose-built structures designed to store and organize compressed gas cylinders securely. They range from simple stands holding a single cylinder to large racks accommodating dozens, tailored to the needs of industrial, laboratory, or medical environments. Gas racks serve multiple purposes:
- Safety: Preventing cylinders from tipping, falling, or leaking, which could cause fires, explosions, or toxic exposures.
- Organization: Keeping cylinders orderly, accessible, and labeled for efficient inventory management.
- Space Optimization: Maximizing storage capacity in confined areas like labs or production floors.
- Compliance: Meeting regulatory standards for hazardous material storage (e.g., OSHA, NFPA).
Gas racks are used in:
- Industrial Settings: Storing welding gases (e.g., argon, acetylene) or process gases (e.g., nitrogen) in oil and gas or manufacturing.
- Laboratories: Managing analytical gases (e.g., helium, hydrogen) for gas chromatography or mass spectrometry.
- Pharmaceuticals: Securing medical gases (e.g., oxygen, nitrous oxide) in cleanroom environments.
- Hydrogen Energy: Storing high-pressure hydrogen cylinders for fuel cells or refueling stations.
- Semiconductors: Handling ultra-high-purity (UHP) gases (e.g., silane, arsine) with strict contamination controls.
Types of Auxiliary Gas Racks
Gas racks come in various designs, each suited to specific applications, cylinder sizes, and storage needs. Understanding these types helps in selecting the right rack.
- Single-Cylinder Stands
- Design: Hold one cylinder, often with a base, chain, or strap to secure it upright.
- Features: Compact, portable, ideal for small labs or welding stations.
- Applications: Temporary storage for a single gas (e.g., argon for welding, oxygen for medical use).
- Capacity: 1 cylinder (e.g., 9-inch diameter, 4–10 feet tall).
- Multi-Cylinder Racks
- Design: Hold 2–20+ cylinders in rows or grids, with chains, bars, or dividers to secure each cylinder.
- Features: Modular, stackable, or wall-mounted options; often include forklift pockets for mobility.
- Applications: Industrial facilities, warehouses, or labs with multiple gas types (e.g., nitrogen, helium, CO2).
- Capacity: 2–20 cylinders, depending on size.
- Palletized Gas Racks
- Design: Heavy-duty racks on pallets, designed for transport and storage of multiple cylinders.
- Features: Forklift-compatible, stackable, often with protective cages or frames.
- Applications: Gas distribution centers, oil and gas fields, or hydrogen refueling stations.
- Capacity: 6–24 cylinders, typically high-pressure (e.g., 3000–6000 psig).
- Specialty Gas Racks
- Design: Customized for specific needs, such as UHP gases, corrosive gases, or medical gases.
- Features: Electropolished stainless steel for UHP systems, fire-resistant materials for flammable gases, or sanitary finishes for pharmaceuticals.
- Applications: Semiconductor fabs, cleanrooms, or medical facilities.
- Capacity: Varies (1–10 cylinders), often smaller for high-value gases.
- Mobile Gas Racks
- Design: Equipped with wheels or casters for easy movement within a facility.
- Features: Locking mechanisms, compact designs, and ergonomic handles.
- Applications: Labs, hospitals, or workshops needing flexible cylinder placement.
- Capacity: 1–6 cylinders, depending on mobility needs.
Key Consideration: The choice of rack depends on the number of cylinders, gas types, space constraints, and mobility requirements. For example, a welding shop might use a multi-cylinder rack, while a semiconductor fab needs a specialty UHP rack.
Benefits of Auxiliary Gas Racks
Gas racks offer significant advantages for gas management and storage:
- Enhanced Safety: Secure cylinders to prevent tipping, which could damage valves or cause leaks (e.g., a falling oxygen cylinder can become a projectile).
- Regulatory Compliance: Meet standards like OSHA 1910.101, NFPA 55, and CGA P-1 for safe gas storage.
- Space Efficiency: Optimize floor space in crowded facilities, with stackable or wall-mounted designs.
- Improved Workflow: Organize cylinders by gas type or usage, reducing retrieval time and errors.
- Durability: Made from robust materials (e.g., steel, stainless steel) to withstand industrial environments.
- Versatility: Accommodate various cylinder sizes (e.g., 4–12 inches in diameter) and gas types.
Step-by-Step Guide to Selecting the Right Gas Rack
Choosing the right auxiliary gas rack involves assessing application needs, cylinder requirements, safety standards, and facility constraints. Follow these steps to make an informed decision.
Step 1: Assess Application and Gas Types
- Gas Types: Identify the gases being stored (e.g., inert like nitrogen, flammable like hydrogen, corrosive like chlorine, or medical like oxygen). This determines material and safety requirements.
- Inert Gases: Standard steel racks suffice.
- Flammable Gases: Need fire-resistant racks with grounding straps.
- Corrosive Gases: Require stainless steel or coated racks.
- UHP/Medical Gases: Demand electropolished stainless steel to prevent contamination.
- Application Context: Consider the industry and use case:
- Welding: Multi-cylinder racks for argon, acetylene, and oxygen.
- Laboratories: Single or mobile racks for helium or hydrogen.
- Pharmaceuticals: Specialty racks for sterile environments.
- Hydrogen Energy: Palletized racks for high-pressure hydrogen cylinders.
- Action: List the gases, their properties (e.g., flammable, corrosive), and the application (e.g., welding, lab, medical).
Step 2: Determine Cylinder Size and Quantity
- Cylinder Size: Standard cylinders range from 4–12 inches in diameter and 2–10 feet in height (e.g., K-size for industrial gases, D-size for medical oxygen). Ensure the rack accommodates your cylinder dimensions.
- Quantity: Estimate the number of cylinders to store (e.g., 1 for a small lab, 20 for a welding shop).
- Future Needs: Plan for scalability if gas usage increases.
- Example: A lab using 5 helium cylinders (9-inch diameter, 4 feet tall) needs a multi-cylinder rack with adjustable dividers.
- Action: Measure cylinder dimensions and count the number needed, considering future expansion.
Step 3: Evaluate Space and Mobility Needs
- Available Space: Measure the storage area’s dimensions (e.g., floor space, ceiling height). Wall-mounted or stackable racks save space in tight areas.
- Mobility: Decide if the rack needs to be moved:
- Stationary: Fixed racks for warehouses or production floors.
- Mobile: Wheeled racks for labs or hospitals.
- Access: Ensure racks allow easy cylinder retrieval and labeling visibility.
- Example: A hospital storing oxygen cylinders in a small room might use a mobile, 4-cylinder rack for flexibility.
- Action: Measure storage space, decide on mobility (fixed or mobile), and ensure accessibility.
Step 4: Select Materials and Construction
Materials:
- Steel: Durable, cost-effective for non-corrosive environments (e.g., welding shops).
- Stainless Steel: Corrosion-resistant for humid, coastal, or corrosive gas settings (e.g., chemical plants).
- Electropolished Stainless Steel: For UHP or medical applications to minimize contamination.
- Coated Steel: Powder-coated or galvanized for added corrosion resistance.
Construction Features:
- Securing Mechanisms: Chains, straps, or bars to hold cylinders upright.
- Dividers: Prevent cylinders from touching, reducing damage risk.
- Base Stability: Wide or weighted bases to prevent tipping.
- Forklift Pockets: For palletized racks in large facilities.
- Example: A semiconductor fab requires an electropolished stainless steel rack for silane cylinders, while a welding shop can use a powder-coated steel rack for argon.
- Action: Choose materials based on gas properties and environment (e.g., stainless steel for corrosive gases), and ensure robust construction.
Step 5: Prioritize Safety Features
Safety is paramount when storing compressed gas cylinders due to their high pressure (up to 6000 psig) and hazardous properties.
- Securing Systems: Chains or straps for each cylinder to prevent falls. Double chains or heavy-duty straps are ideal for high-pressure cylinders.
- Fire Resistance: For flammable gases (e.g., hydrogen, acetylene), use racks with fire-resistant coatings or store in fire-rated cabinets.
- Grounding: Grounding straps for flammable gas racks to prevent static sparks.
- Ventilation: Open or perforated designs to disperse gas leaks, especially for toxic or flammable gases.
- Labeling Areas: Space for clear labeling of gas types, pressures, and hazards (e.g., “Oxygen – No Smoking”).
- Locking Mechanisms: For mobile racks or medical gases to prevent unauthorized access.
- Example: A hydrogen refueling station uses a palletized rack with grounding straps and fire-resistant coating to store 700-bar hydrogen cylinders safely.
- Action: Select racks with safety features like chains, grounding, and ventilation, tailored to the gas’s hazards.
Step 6: Ensure Regulatory Compliance
Gas storage must comply with safety and industry standards to avoid fines or accidents.
- OSHA 1910.101: Requires secure cylinder storage, proper labeling, and segregation of incompatible gases (e.g., oxygen and acetylene).
- NFPA 55: Governs compressed gas storage, mandating ventilation, fire protection, and separation distances for flammable gases.
- CGA P-1: Provides guidelines for safe handling and storage of gas cylinders.
- ASME B31.3: Applies to gas piping systems, including storage areas.
- SEMI F19: Specifies UHP storage requirements for semiconductors.
- NFPA 56: Addresses hydrogen storage, emphasizing fire and explosion prevention.
Key Requirements:
- Store cylinders upright and secured.
- Segregate flammable, oxidizing, and toxic gases by at least 20 feet or a fire-rated barrier.
- Ensure ventilation to prevent gas accumulation.
- Label cylinders and racks clearly with gas names and hazards.
- Action: Verify that the rack meets OSHA, NFPA, and CGA standards, and request supplier documentation (e.g., compliance certificates).
Step 7: Consider Maintenance and Total Cost of Ownership (TCO)
Maintenance and cost considerations ensure the rack remains functional and cost-effective over time.
- Maintenance Needs:
- Inspection: Check chains, straps, and welds regularly (e.g., monthly) for wear or corrosion.
- Cleaning: UHP or medical racks require periodic cleaning to prevent contamination (e.g., per CGA G-4.1).
- Repairs: Replace damaged chains, straps, or dividers promptly.
TCO:
- Upfront Cost: Steel racks cost $100–$500, stainless steel $500–$2000, depending on size and features.
- Durability: Stainless steel lasts longer in corrosive environments, reducing replacement costs.
- Maintenance Costs: Simple steel racks require minimal upkeep, while UHP racks need cleaning.
- Action: Plan for regular inspections and cleaning, and calculate TCO by factoring in purchase price, maintenance, and lifespan.
Step 8: Partner with Reliable Suppliers
A trusted supplier ensures quality, compliance, and support.
- Reputation: Choose suppliers with experience in your industry (e.g., Airgas, Grainger, Gas Cylinder Source).
- Certifications: Ensure racks meet OSHA, NFPA, or CGA standards, with documentation provided.
- Customization: Some suppliers offer custom racks for unique cylinder sizes or applications.
- Support: Look for installation guides, safety training, or customer service for troubleshooting.
- Action: Request quotes from reputable suppliers, verify certifications, and ask for customization options if needed.
Practical Considerations and Best Practices
- Segregation: Store incompatible gases (e.g., oxygen and acetylene) in separate racks or areas to prevent reactions.
- Labeling: Use clear, durable labels on racks and cylinders (e.g., “Flammable Gas – Hydrogen”).
- Training: Train staff on safe cylinder handling, rack use, and emergency procedures (e.g., per OSHA 1910.101).
- Ventilation: Install racks in well-ventilated areas, away from ignition sources for flammable gases.
- Inventory Management: Rotate cylinders (first-in, first-out) to ensure fresh gas supply and track usage.
Challenges and Solutions
- Challenge: Limited space in small facilities.
- Solution: Use wall-mounted or stackable racks to maximize vertical space.
- Challenge: Ensuring compliance with complex regulations.
- Solution: Work with suppliers to select compliant racks and consult OSHA/NFPA guidelines.
- Challenge: Handling hazardous gases safely.
- Solution: Use fire-resistant, grounded racks with robust securing systems.
- Challenge: High costs for specialty racks
- Solution: Balance TCO by choosing durable materials for long-term savings.
Emerging Trends in Gas Rack Technology
- Smart Racks: IoT-enabled racks with sensors to monitor cylinder levels, leaks, or pressure, improving inventory and safety management.
- Modular Designs: Flexible racks that can be reconfigured for changing cylinder sizes or quantities.
- Sustainable Materials: Eco-friendly steel or recycled materials to align with green initiatives.
- UHP Compatibility: Electropolished stainless steel racks for semiconductors and hydrogen energy, meeting stricter purity standards.
- Automation Integration: Racks designed for automated cylinder handling in large facilities.
- Impact: These trends enhance safety, efficiency, and sustainability, supporting modern industrial demands.
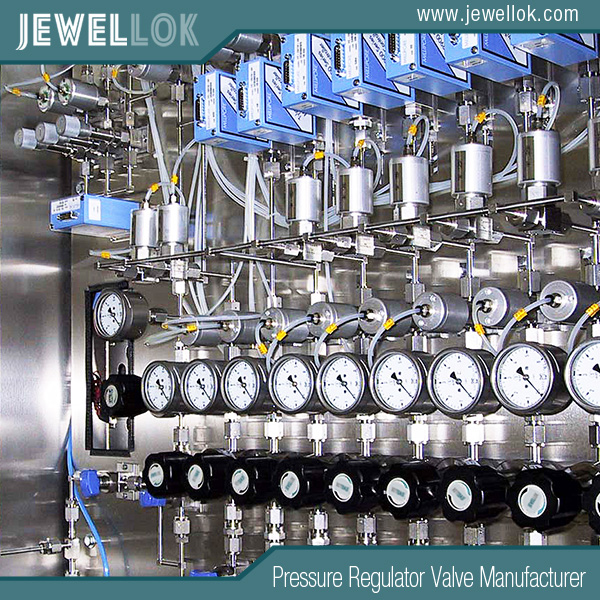
Conclusion
Auxiliary gas racks are practical, indispensable equipment for managing and storing compressed gas cylinders across industries like welding, semiconductors, pharmaceuticals, and hydrogen energy. By securing cylinders, optimizing space, and ensuring compliance with standards like OSHA, NFPA, and CGA, gas racks enhance safety, efficiency, and operational reliability. Selecting the right rack involves assessing gas types, cylinder sizes, space constraints, material needs, and safety features, while partnering with reputable suppliers ensures quality and support. From single-cylinder stands to palletized racks, the variety of designs caters to diverse applications, with emerging trends like smart racks and sustainable materials driving innovation. By following the step-by-step guide outlined in this article—evaluating application needs, prioritizing safety, and planning for maintenance—facility managers and safety officers can choose gas racks that streamline gas management, protect personnel, and comply with regulations. With the right gas rack, organizations can confidently handle compressed gases, ensuring safe and efficient operations in critical systems.
For more about auxiliary gas racks: practical equipment for gas management and storage, you can pay a visit to Jewellok at https://www.jewellok.com/ for more info.
Recent Posts
The Applications, Principles and Types of Water Solenoid Valve
Medical Oxygen Regulator Manufacturers in France
How Does a Bulk Specialty Gas Delivery System (BSGS) Work?
Tags
Recommended Products
-
High Purity High Pressure 316 Stainless Steel Ball Valves JBV1 Series From High Pressure Ball Valve Manufacturer And Supplier In China
-
762L Stainless Steel High Purity Union High-Purity Gas System Fittings
-
764L Stainless Steel Union Tee High Purity Fitting Union Tee Reducing Tubing Connection
-
Ultra High Purity Stainless Steel Compressed Gas Changeover Manifold Panel System For Integrated Gas Supply System
-
High Purity Configurable Systems VMB Valve Manifold Box JW-200-VMB-C & JW-100-VMB-C
-
Semi Automatic And Automatic Switching Speicialty Gas Changeover Manifold Panel With Semiconductor Valve Manifold Box Gas Pressure Regulators
-
High Purity High Pressure Specialty Gas Pressure Regulators Specialty Gases Pipeline Engineering Equipments Manufacturer And Supplier
-
Low Pressure High Flow Line Pressure Regulators And Control Valves JSR-4L Series For Laboratory Pressure Control