Blog
Jewellok is a professional pressure regulator and valve manufacturer and supplier.
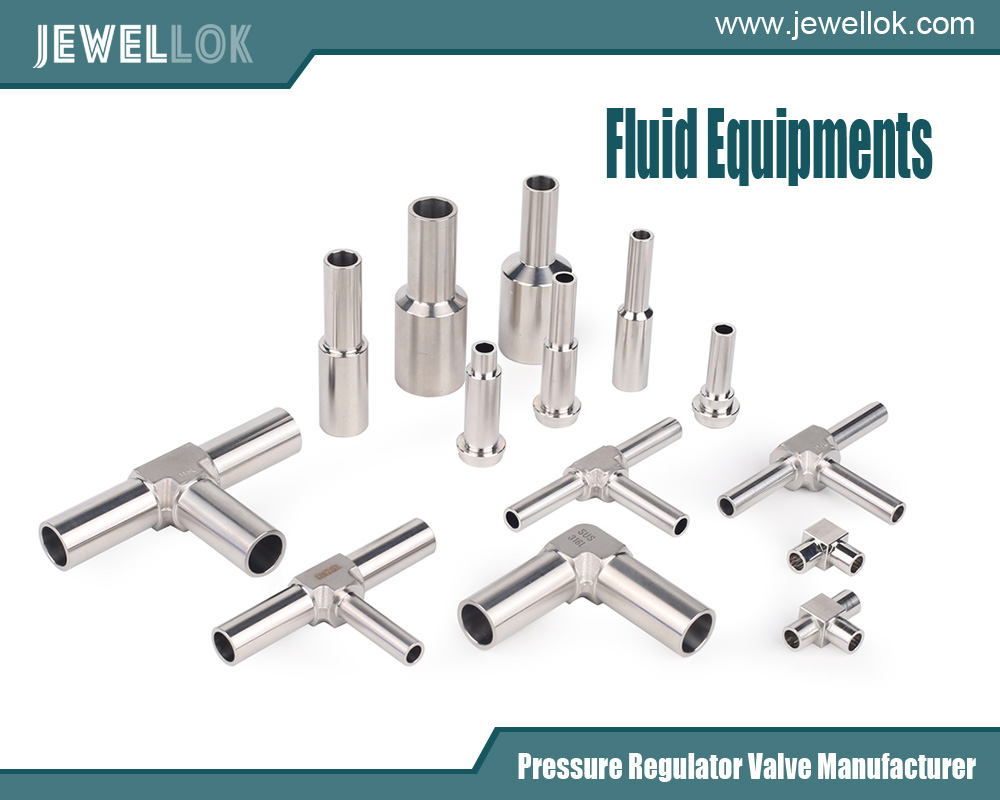
Gas Industry in the Semiconductor Industry
- Pressure Regulator Valve Manufacturer
- 1 1 2 gas pressure regulator, 1 2 gas regulator, 1/2 gas pressure regulator, 1/4 VCR Stainless Steel Ultra High Purity Gas Regulator, 2 inch irrigation solenoid valve, 3/4 natural gas regulator, Adjustable Helium Single Stage High Pressure Gas Regulator, adjustable natural gas regulator, Argon Gas Flow Gauge Regulator And Valves, argon gas pressure regulator, argon gas pressure regulator manufacturer, Argon Gas Regulators, best gas regulator in philippines, China Gas Valve Manufacturers, China high purity gas valve manufacturer, China Industrial Gas Valve Manufacturer, gas filter, gas industry, gas industry in the semiconductor industry, gas used in semiconductor manufacturing, gas valve, High Purity Gas Valves, High purity gas valves manufacturers, industrial grade purity, laboratory gas valves, low pressure regulator, oil and gas valves suppliers in uae, pressure gauge manufacturers, relief vs safety valve, safety relief valve vs pressure relief valve, semiconductor industry, Specialty Gas Valves, Specialty Gas Valves and Regulators, stainless pressure regulator
- No Comments
Gas Industry in the Semiconductor Industry
The semiconductor industry is a cornerstone of modern technology, powering devices from smartphones and computers to electric vehicles, medical equipment, and advanced systems like artificial intelligence (AI) and 5G networks. At the heart of semiconductor manufacturing lies the gas industry, which supplies ultra-high-purity (UHP) gases and specialty gases essential for creating the intricate circuitry of microchips. These gases, ranging from nitrogen and hydrogen to exotic fluorinated compounds, enable critical processes like deposition, etching, and doping, ensuring the precision and reliability required for advanced semiconductor nodes (e.g., 5nm and below). As the semiconductor industry grows—projected to reach a $1 trillion market by 2030—the demand for high-purity gases is surging, driven by digitalization, electric mobility, and emerging technologies. This article examines the pivotal role of the gas industry in semiconductor manufacturing, exploring the types of gases used, their applications, supply chain dynamics, challenges, innovations, and future trends shaping this critical sector.
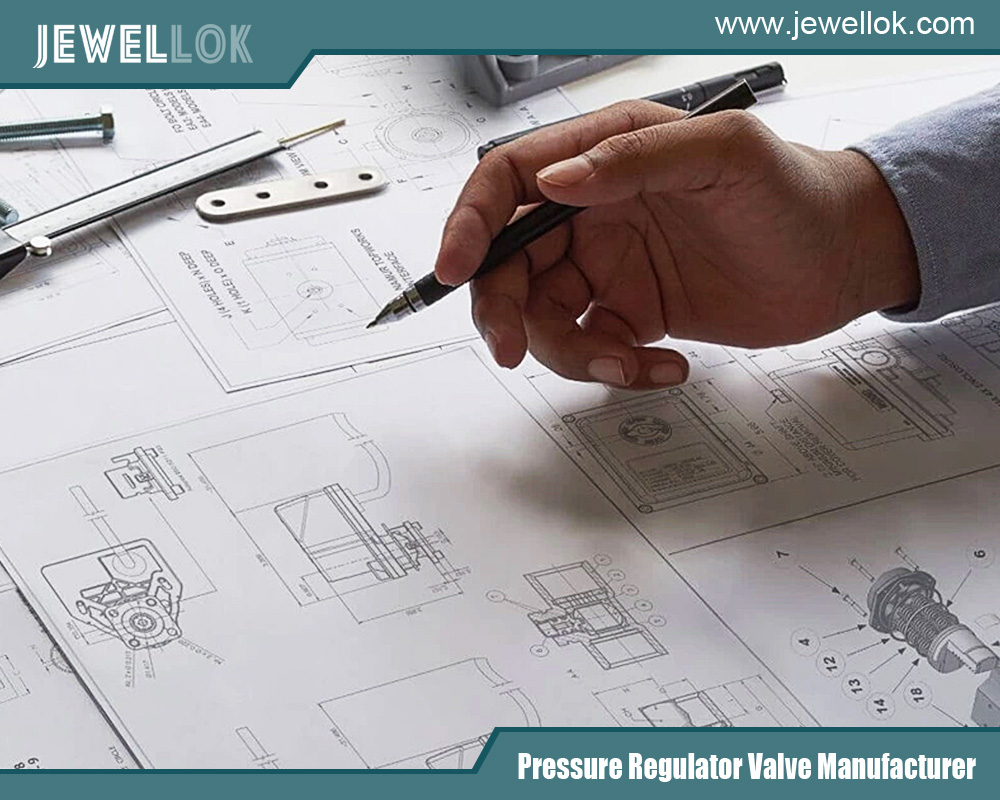
The Role of Gases in Semiconductor Manufacturing
Semiconductor manufacturing, or wafer fabrication, is a complex, multi-step process that transforms silicon into integrated circuits (ICs) and other microelectronic devices. Gases are indispensable at nearly every stage, facilitating chemical reactions that shape the electrical properties of semiconductors. Over 30 different gases are used in processes such as crystal growth, deposition, etching, doping, lithography, and chamber cleaning, with purity levels often exceeding 99.9999% (6N) to prevent contamination.
The gas industry supplies two main categories of gases for semiconductors:
- Bulk Gases: High-volume, high-purity gases like nitrogen, helium, hydrogen, argon, and oxygen, used for inerting, purging, and thermal management.
- Specialty Gases: Electronic specialty gases (ESGs), including silane, phosphine, nitrogen trifluoride, and fluorocarbons, designed for specific chemical reactions in semiconductor processes.
According to the China Semiconductor Industry Association, the global market for electronic specialty gases reached $4.51 billion in 2018 and is projected to grow significantly, with China’s market alone expected to reach 23 billion yuan by 2024. These gases account for 14% of raw material demand in semiconductor manufacturing, second only to silicon wafers, underscoring their critical role.
Types of Gases and Their Applications
Bulk Gases:Bulk gases are used in large quantities to create controlled environments or support general processes:
Nitrogen: The most widely used gas, nitrogen (78% of Earth’s atmosphere) is abundant, inert, and cost-effective. In semiconductor fabs, it purges pipelines and chambers to remove oxygen and moisture, protecting sensitive wafers. A modern fab can consume 50,000 cubic meters of nitrogen per hour.
Helium: A noble gas with high thermal conductivity, helium cools silicon wafers during high-temperature processes like annealing, preventing thermal damage. Its inert nature makes it ideal for plasma processes.
Hydrogen: Used in annealing to repair crystal structures, epitaxial deposition of silicon or germanium, and plasma cleaning to remove contaminants like tin in photolithography. Hydrogen also stabilizes toxic gases like diborane during doping.
Argon: An inert gas with low ionization energy, argon is used as a primary plasma for deposition and etching, in UV lithography lasers, and to protect silicon crystals from oxygen reactions during wafer growth.
Oxygen: Essential for silicon oxidation, a critical process that forms insulating layers on wafers.
Specialty Gases
Specialty gases are highly reactive or exotic compounds tailored for specific semiconductor processes:
Silane (SiH4): Used in chemical vapor deposition (CVD) to deposit silicon films. Highly flammable and pyrophoric, silane requires careful handling.
Phosphine (PH3) and Diborane (B2H6): Dopants that introduce phosphorus or boron to alter semiconductor electrical properties. These toxic gases demand stringent safety measures.
Fluorinated Gases: Perfluorocarbons (e.g., CF4, C2F6), hydrofluorocarbons (e.g., CHF3), nitrogen trifluoride (NF3), and sulfur hexafluoride (SF6) are used for etching and chamber cleaning. These high global warming potential (GWP) gases pose environmental challenges.
Rare Gases: Neon, xenon, and krypton are used in extreme ultraviolet (EUV) lithography to create precise patterns on wafers. Neon, for example, serves as a buffer gas in UV lasers.
Ammonia (NH3): Used in deposition (e.g., CVD, ALD) and doping for nitride-based semiconductors.
Applications:
Deposition (CVD, ALD): Gases like silane and ammonia deposit thin films of silicon, nitrides, or oxides.
Etching: Fluorinated gases selectively remove material to create circuit patterns.
Doping: Phosphine and diborane introduce impurities to modify electrical conductivity.
Lithography: Rare gases enable precise patterning in EUV systems.
Chamber Cleaning: Nitrogen trifluoride and fluorocarbons remove residues from deposition chambers.
Annealing and Epitaxy: Hydrogen and argon support crystal growth and defect repair.
These applications highlight the gas industry’s role in enabling the precision and scalability of semiconductor manufacturing.
Supply Chain Dynamics
The gas industry’s supply chain for semiconductors is complex, involving production, purification, delivery, and on-site management. Key players like Air Liquide, Linde, Air Products, and Merck dominate the global market, forming an oligopoly due to technological expertise and economies of scale.
Production and Purification
Bulk Gases: Nitrogen, oxygen, and argon are produced via air separation units (ASUs) on-site or delivered as cryogenic liquids. Hydrogen is supplied as compressed gas or produced on-site.
Specialty Gases: Produced through synthesis, distillation, or adsorption, specialty gases require advanced purification to achieve sub-ppb impurity levels. For example, Air Products’ BIP® technology guarantees oxygen levels below 10 ppb and moisture below 20 ppb.
On-Site Generation: Large fabs use nitrogen generators (e.g., Linde’s SPECTRA® series) and electrolyzers for green hydrogen to reduce reliance on external supplies.
Delivery Systems
Gas delivery systems are critical for maintaining purity and precision:
Components: Valves, regulators, mass flow controllers, and gas sticks (compact units with UHP components) ensure accurate flow and pressure control. Materials like 316L stainless steel and Teflon resist corrosion from reactive gases.
Piping: Electropolished 316L stainless steel tubing, welded with orbital gas tungsten arc welding (GTAW), minimizes contamination. Double-wall piping and VCR fittings prevent leaks.
Safety: Hazardous gases like silane (pyrophoric) and hydrogen fluoride (corrosive) require specialized containment, leak detectors, and pressure regulators.
Global Supply Challenges
The semiconductor gas supply chain faces several challenges:
Import Dependency: In regions like China, specialty gases are heavily imported (e.g., $2.451 billion in imports vs. $146 million in exports in 2018), creating vulnerability to sanctions or supply disruptions.
COVID-19 Disruptions: The pandemic caused raw material shortages and logistics delays, exacerbating chip shortages and impacting dependent industries like automotive.
Geopolitical Risks: Trade restrictions or sanctions can limit access to critical gases, as seen in China’s reliance on foreign suppliers.
Sustainability: High-GWP gases like SF6 and CF4 contribute to greenhouse gas emissions, prompting regulatory scrutiny and emission reduction efforts.
Action: Diversify supply chains, invest in local production, and adopt recycling systems to mitigate risks.
Challenges in the Gas Industry for Semiconductors
The gas industry faces several challenges in meeting semiconductor demands:
- Purity Requirements: Advanced nodes (<5nm) require gases with impurities below parts-per-trillion (ppt) levels. Even 1 ppm of contamination can ruin a chip by affecting etching or deposition.
- Safety Risks: Gases like silane, phosphine, and hydrogen fluoride are flammable, toxic, or corrosive, requiring rigorous safety protocols, including gas detectors, protective gear, and leak-proof systems.
- Environmental Impact: Fluorinated gases have high GWP, contributing to climate change. The EPA’s Greenhouse Gas Reporting Program tracks emissions, and companies are optimizing processes or switching to lower-GWP alternatives like NF3.
- Supply Chain Complexity: Delivering UHP gases globally while maintaining purity and reliability is logistically challenging, especially for hazardous gases.
- Cost Pressures: High-purity gases are the second-largest material expenditure after silicon, driving demand for cost-effective solutions like on-site generation.
- Solutions:
Invest in advanced purification technologies (e.g., adsorption, chemisorption).
Implement safety systems like gas leak detectors and automated shutdowns.
Adopt recycling systems (e.g., EFC’s Neon Gas Recycling System) to reduce emissions and costs.
Develop local production to reduce import reliance.
Innovations Driving the Gas Industry
The gas industry is evolving to meet the semiconductor sector’s growing demands through technological and sustainable innovations:
- Ultra-High-Purity Technologies
Advanced Purification: Companies like EFC Gases use distillation and adsorption to achieve 6N+ purity levels, critical for sub-7nm nodes.
Point-of-Use Filtration: Technologies like Air Products’ BIP® cylinders provide additional filtration at the point of use, ensuring sub-ppb impurity levels.
Analytical Capabilities: Mass spectrometry and laser-based analyzers monitor gas purity in real time, ensuring process repeatability.
- Smart Gas Delivery Systems
IoT-Enabled Systems: Sensors and mass flow controllers monitor pressure, flow, and purity, integrating with SCADA systems for real-time control.
Predictive Maintenance: AI algorithms predict equipment failures, reducing downtime and ensuring consistent gas supply.
Custom Gas Sticks: Compact, UHP gas delivery units optimize flow control for specific processes.
- Sustainable Practices
Neon Recycling: EFC’s Neon Gas Recycling System captures and reconditions spent neon from laser exhausts, reducing CO2 emissions by over 1 million metric tons per fab over 20 years.
Green Hydrogen: Linde’s on-site electrolyzers produce green hydrogen using renewable energy, supporting sustainability goals.
Low-GWP Alternatives: Switching to NF3 or optimizing processes reduces emissions of high-GWP gases like SF6.
- On-Site Generation
Nitrogen Generators: Linde’s SPECTRA® N series scales with fab needs, delivering UHP nitrogen efficiently.
Argon Plants: Linde’s SPECTRA argon plants meet rising demand with improved energy efficiency.
Hydrogen Electrolyzers: On-site green hydrogen production reduces transport emissions.
Impact: These innovations enhance purity, safety, and sustainability while reducing costs and supply chain risks.
Future Trends
The gas industry in semiconductors is poised for transformation, driven by technological and market trends:
Advanced Nodes: Sub-3nm processes will demand even higher purity and precision, spurring innovations in purification and delivery systems.
Digitalization and AI: IoT and AI will enable fully automated gas delivery systems, optimizing flow and predicting maintenance needs.
Sustainability: Recycling, green hydrogen, and low-GWP gases will align with net-zero goals, driven by regulations like the EPA’s HFC Phasedown.
Regional Expansion: Investments in the U.S. (e.g., CHIPS Act) and Asia (e.g., China, Taiwan) will increase demand for local gas production and ASUs.
Emerging Applications: Quantum computing, OLEDs, and electric vehicles will require new gas mixtures and delivery systems.
Action: Invest in R&D for purification, recycling, and smart systems to stay competitive in a growing market.
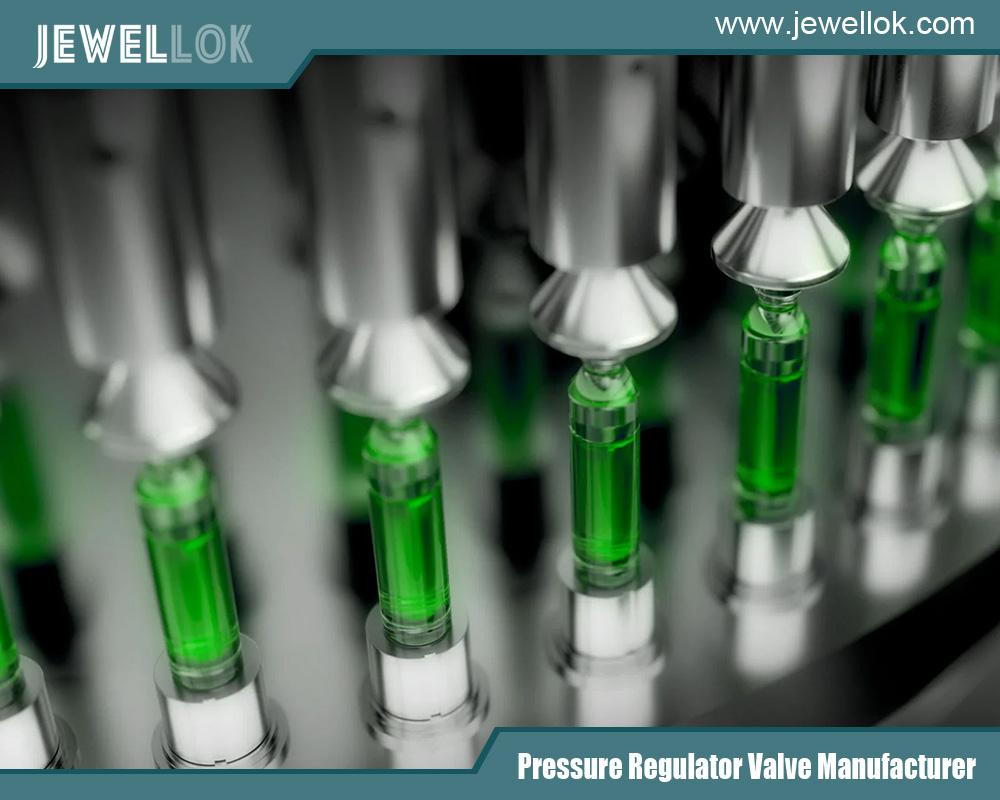
Conclusion
The gas industry is a linchpin of the semiconductor industry, supplying the ultra-high-purity and specialty gases that enable the production of advanced microchips. From nitrogen and hydrogen to silane and fluorocarbons, these gases facilitate critical processes like deposition, etching, and lithography, ensuring the precision and reliability required for modern technologies. Despite challenges like supply chain vulnerabilities, safety risks, and environmental concerns, the gas industry is innovating through advanced purification, smart delivery systems, and sustainable practices like neon recycling and green hydrogen. As the semiconductor market grows, driven by digitalization, AI, and electric mobility, the demand for high-purity gases will continue to rise, presenting opportunities for suppliers to enhance purity, safety, and sustainability. By addressing challenges and embracing innovations, the gas industry will remain a vital force in powering the semiconductor revolution, enabling the technologies that shape our digital world.
For more about gas industry in the semiconductor industry, you can pay a visit to Jewellok at https://www.jewellok.com/ for more info.
Recent Posts
Best High-Pressure Gas Regulators For Industrial Use
Pressure Relief Valve Manufacturers
High Pressure Ball Valve Manufacturer
Application Of Ultra High Purity Gas Manifold Panels
Pressure Reducing Valve Manufacturers
China High Pressure Air Regulator Valve Manufacturer
Tags
Recommended Products
-
Stainless Steel Low Pressure Seal Pneumatic Diaphragm Control Valve For For HP & UHP Gases
-
High Purity Stainless Steel Mini Tube Butt Weld Fittings For Semiconductor
-
772L Male Branch Tee | Stainless Steel High-Purity Tube Fitting Male Branch Tee
-
771L Male Run Tee | Stainless Steel High Quality High Purity Male Run Tee Branch Tee Pipe Fittings
-
767LP Port Connector Ultra High Purity VCR Metal Gasket Face Seal Tube Fittings
-
VMB Valve Manifold Panels And Boxes High Purity Configurable Systems JW-200-VMB & JW-100-VMB
-
JF Series In-Line Gas Filters | High Purity High Precision High Flow Semiconductor Gas Filter Gas Filtration & Purification
-
Semi Automatic Gas Cabinet Gas Panels High Purity Gas Delivery Systems JW-200-GC