Blog
Jewellok is a professional pressure regulator and valve manufacturer and supplier.
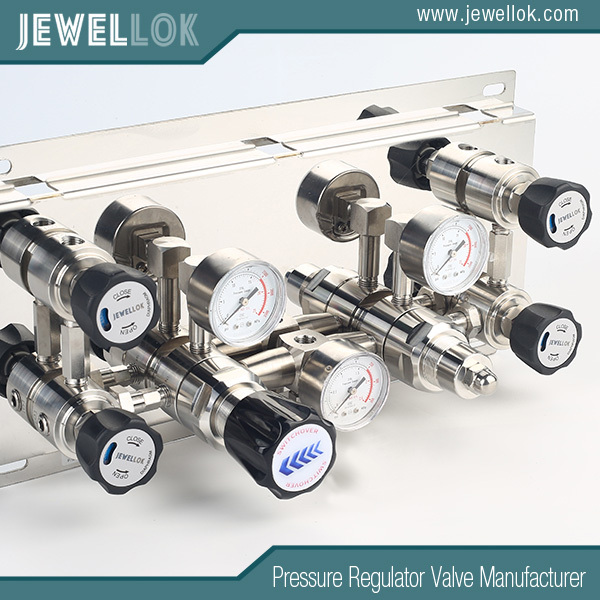
How Does A Specialty Gas Fully Automatic Changeover Manifold System Work?
- Pressure Regulator Valve Manufacturer
- auto changeover gas manifold, Automatic Gas Cylinder Changeover, automatic gas cylinder changeover unit, Automatic gas switchover system, Automatic Manifold Systems, Best Gas Switchover Manifolds for Gas Management, CO2 and Inert Auto changeover manifold, co2 cylinder auto changeover controller, Custom Non-Electric Automatic Gas Changeover Systems, fully automated manifold design, fully automatic changeover manifold systems, Fully Automatic Medical Gas Manifolds, gas arc auto changeover manifolds, gas changeover manifold, gas cylinder manifold systems, Industrial Automatic Changeover Manifolds, Liquid nitrogen switchover manifold, Manual Changeover Manifold Systems, Medicinal Gas Manifold Auto Switchover of Cylinder, Semi-Automatic Manifold Systems, Semi-Automatic Manifold Systems Malaysia, Semi-Automatic Manifold Systems Russia, Semi-Automatic Switchover Manifold, Specialty Gas Fully Automatic Changeover Manifolds, ultra high purity manifolds, vmb valve manifold box
- No Comments
How Does A Specialty Gas Fully Automatic Changeover Manifold System Work?
In industries where specialty gases are indispensable, maintaining a continuous and uninterrupted supply is critical. Specialty gases—high-purity gases or specific gas mixtures—are vital in applications ranging from semiconductor manufacturing to pharmaceutical production and research laboratories. Any interruption in their supply can lead to costly downtime, compromised results, or safety hazards. To address this challenge, fully automatic changeover manifold systems are employed. These systems are engineered to seamlessly switch from a depleted gas source to a reserve one, ensuring a constant flow of gas to the application without manual intervention. This article explores how these systems work, delving into their components, operation, types, advantages, applications, and key considerations for selection and installation.
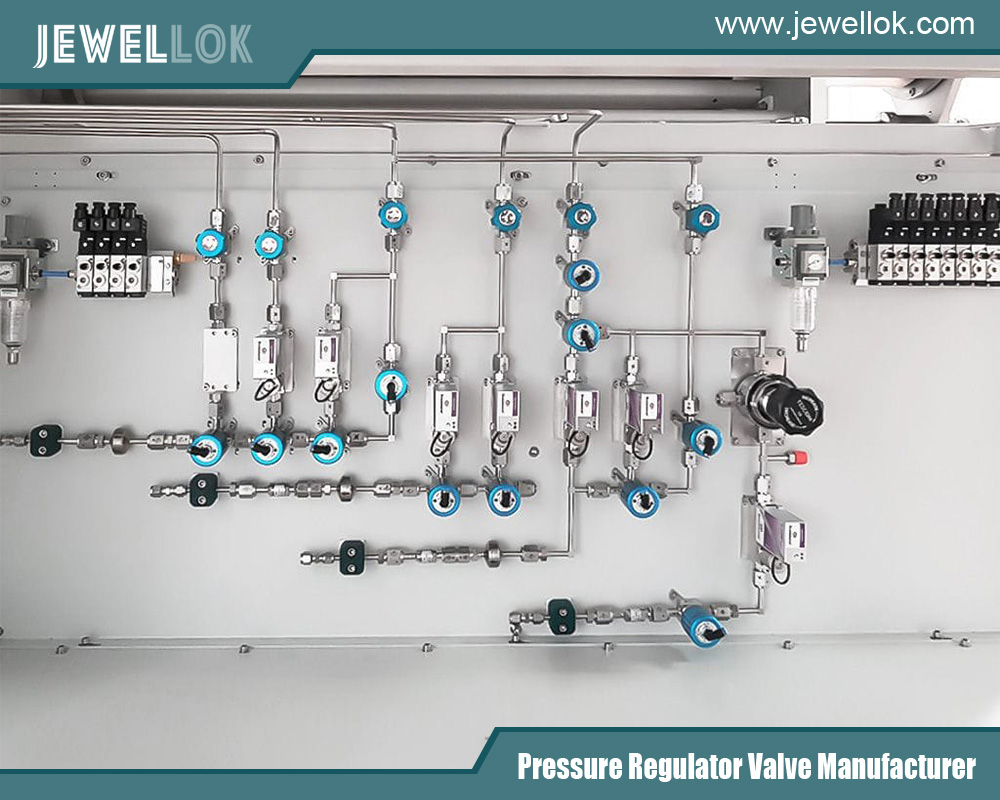
Introduction to Fully Automatic Changeover Manifold Systems
Specialty gases, such as nitrogen, argon, helium, or custom mixtures, are used in processes where purity and precision are non-negotiable. A fully automatic changeover manifold system is a sophisticated setup designed to manage the delivery of these gases from high-pressure cylinders to end-use applications. The “fully automatic” aspect refers to its ability to detect when the primary gas supply is running low and switch to a secondary (reserve) supply without human input, except for replacing empty cylinders. This automation is critical in environments where even a brief interruption could disrupt production or compromise safety.
At its core, the system comprises two banks of gas cylinders: a primary bank and a secondary bank. Gas is drawn from the primary bank until its pressure drops below a predetermined threshold, signaling depletion. The system then automatically shifts to the secondary bank, while an alert notifies operators to replenish the primary bank. Once replenished, the system can continue this cycle, alternating between banks to maintain an uninterrupted supply. This article will break down the components and operational sequence of these systems, offering a comprehensive understanding of their functionality.
Components of the System
To grasp how a fully automatic changeover manifold system operates, it’s essential to understand its key components:
- Gas Cylinders and Banks
Specialty gases are stored in high-pressure cylinders, typically made of steel or aluminum, designed to withstand the pressures of compressed gases (often exceeding 2000 psi). These cylinders are grouped into banks—each bank consisting of multiple cylinders connected via a manifold header. This setup increases the total gas volume available and simplifies cylinder management. For example, a bank might include four cylinders manifolded together, with one bank designated as primary and another as secondary. - Regulators
Pressure regulators reduce the high cylinder pressure to a lower, usable level suitable for the application (e.g., 50–150 psi). In a changeover system, regulators can be configured in different ways: each bank might have its own regulator, or a single regulator might be placed downstream of the changeover point. The choice depends on the system design and the precision required for pressure control. - Valves
Several types of valves play critical roles:
– Isolation Valves: Located at each cylinder, these allow individual cylinders to be shut off for replacement without interrupting the system.
– Check Valves: Prevent backflow of gas between banks or into depleted cylinders.
– Solenoid Valves: Electrically operated valves controlled by the automation system, these facilitate the switch between primary and secondary banks. - Pressure Sensors/Transducers
Pressure sensors or transducers monitor the pressure in each bank in real time. When the pressure in the primary bank falls below a preset threshold (e.g., 100 psi), the sensor sends a signal to initiate the switchover. These devices are critical for the system’s automation, ensuring timely transitions between gas sources. - Control Unit
The control unit is the brain of the system. It can be electronic—using a digital controller to process sensor signals and activate solenoid valves—or pneumatic, relying on pressure differentials to trigger the switch. Electronic control units often include additional features like alarm management and integration with facility monitoring systems. - Alarms and Indicators
Visual and audible alarms alert operators when a bank is depleted and requires cylinder replacement. Indicators, such as LED lights or digital displays, show which bank is currently in use, enhancing operational awareness.
These components work in concert to deliver a seamless gas supply, with each part contributing to the system’s reliability and automation.
How the System Works
The operation of a fully automatic changeover manifold system follows a logical sequence, ensuring continuous gas delivery:
- Normal Operation
Under normal conditions, gas is drawn from the primary bank. The manifold header connects the cylinders in the bank, feeding gas through the system’s piping to the regulator and onward to the application. Pressure sensors continuously monitor the pressure in both banks, providing real-time data to the control unit. - Detection of Low Pressure
As gas is consumed, the pressure in the primary bank decreases. When it drops below the preset threshold—indicating that the cylinders are nearly depleted—the pressure sensor detects this change and signals the control unit. - Automatic Switchover
Upon receiving the low-pressure signal, the control unit activates the solenoid valves. The valve on the primary bank closes, and the valve on the secondary bank opens, redirecting gas flow from the secondary bank. This transition occurs seamlessly, typically within milliseconds, ensuring no interruption to the application. - Alert for Cylinder Replacement
Simultaneously, an alarm (e.g., a buzzer or flashing light) and an indicator notify operators that the primary bank is depleted. Operators can then replace the empty cylinders in the primary bank without disrupting the gas supply, as the secondary bank is now active. - Continued Operation and Alternation
Once the primary bank’s cylinders are replaced and its pressure is restored, the system continues drawing from the secondary bank until it, too, reaches the low-pressure threshold. At that point, the control unit reverses the process, switching back to the replenished primary bank. This cycle repeats, alternating between banks to maintain a continuous supply.
This fully automatic alternation distinguishes these systems from semi-automatic versions, which may require manual resetting after each switchover. The design ensures minimal operator involvement beyond cylinder replacement, optimizing uptime and efficiency.
Types of Automatic Changeover Systems
Fully automatic changeover manifold systems vary based on their control mechanisms, tailored to different operational needs:
Electronic Control Systems
These systems use electronic pressure sensors and a digital control unit to manage the switchover. They offer high precision and can integrate with building management systems (BMS) for remote monitoring, data logging, and predictive maintenance alerts. Electronic systems are ideal for specialty gas applications requiring stringent purity and control, such as in semiconductor manufacturing.
Pneumatic Control Systems
Pneumatic systems rely on mechanical pressure differentials between the banks to trigger the switchover, eliminating the need for electrical components. They are simpler and more robust, making them suitable for environments where electronics might be impractical, such as in hazardous or explosive atmospheres. However, they may lack the advanced features of electronic systems.
For specialty gases, electronic systems are often preferred due to their accuracy and ability to maintain gas purity by optimizing the gas path and minimizing contamination risks.
Advantages of Fully Automatic Systems
These systems offer several compelling benefits:
Continuous Supply
The primary advantage is an uninterrupted gas flow, critical for processes where downtime could halt production or ruin experiments.
Reduced Downtime
Automation eliminates the need for constant monitoring and manual switching, freeing operators for other tasks and reducing response time during cylinder changes.
Safety Features
Built-in safety mechanisms, such as alarms, check valves, and optional purge systems (to remove air or moisture during cylinder changes), enhance operational safety and protect against contamination.
Efficiency in Gas Usage
By setting the switchover point at a lower pressure, the system maximizes the use of gas in each cylinder, reducing waste and operational costs.
These advantages make fully automatic changeover manifold systems a cornerstone of specialty gas management.
Applications
Fully automatic changeover manifold systems are widely used across industries reliant on specialty gases:
Semiconductor Manufacturing
High-purity gases like nitrogen and argon are used in processes such as chemical vapor deposition (CVD) and etching. Continuous supply prevents defects and maintains production yields.
Pharmaceutical Production
Specialty gases are employed for inerting, sparging, or synthesis reactions. An uninterrupted supply ensures consistent product quality and process efficiency.
Research Laboratories
Analytical instruments (e.g., gas chromatographs) and experiments often require precise gas mixtures. These systems ensure research continuity.
Healthcare
While medical gases like oxygen may overlap with specialty gases, automatic changeover systems ensure availability for critical patient care applications.
In each case, the system’s ability to maintain gas flow without interruption is paramount.
Considerations for Selection and Installation
Choosing and installing a fully automatic changeover manifold system requires careful planning:
Gas Type and Purity Requirements
The system must be compatible with the gas in use. Corrosive gases (e.g., chlorine) may require stainless steel components, while high-purity applications demand designs that minimize dead volumes and contamination.
Flow Rate Needs
The system’s capacity must match the application’s maximum flow rate, dictating the size of regulators, piping, and cylinder banks.
Space and Infrastructure
Facility layout influences the placement of cylinder banks and routing of gas lines. Compact designs may be necessary in constrained spaces.
Safety Regulations
Compliance with standards (e.g., NFPA, ISO) is essential, particularly in regulated industries like healthcare or food production.
Additional features, such as purge systems for ultra-high-purity gases or remote monitoring for large facilities, may also be considered to meet specific operational needs.
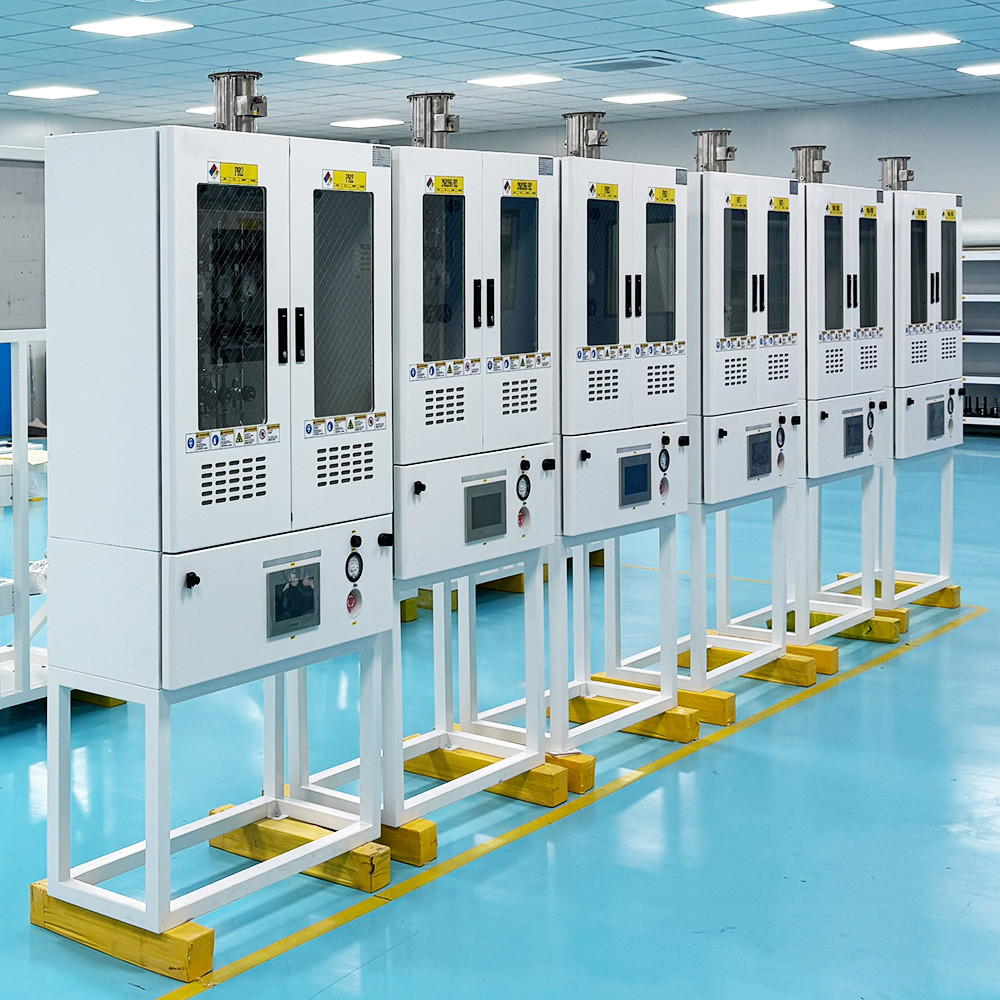
Conclusion
A fully automatic changeover manifold system is an advanced solution for delivering specialty gases with reliability and precision. By automatically switching between primary and secondary gas sources using regulators, valves, sensors, and control units, it eliminates the risk of supply interruptions. Its applications span critical industries, offering benefits in efficiency, safety, and uptime. As technology advances, these systems continue to evolve, integrating with modern industrial processes to meet the growing demands of specialty gas management. Understanding their components, operation, and selection criteria empowers industries to optimize their gas supply infrastructure effectively.
This comprehensive overview illustrates how fully automatic changeover manifold systems work, ensuring that specialty gases—vital to so many processes—are always available when needed.
For more about how does a specialty gas fully automatic changeover manifold system work, you can pay a visit to Jewellok at https://www.jewellok.com/what-is-fully-automatic-specialty-gas-cabinets-with-gas-panel-for-nf3-gas/ for more info.
Recent Posts
Pneumatic Pressure Control Valve Manufacturers in the UK
How To Choose The Right Stainless Steel Needle Valve
The Applications, Principles and Types of Water Solenoid Valve
Tags
Recommended Products
-
Ultra High Purity Pressure Gauge For Laboratory And Semiconductor JR Series
-
High Purity And Industria Gas Stick Assemblies Precise Pressure Control Gas Systems JSR-1ETG-BV Series
-
Specialty Gas Valves Ultra High Purity Gas Valves Ultra High Purity Gas Cylinder Valves UHP Cylinder Valve Ultra High Purity Gas Regulator
-
739LF High Purity Female Adapter Tube To Pipe Fittings And Connectors
-
771LF Female Run Tee | Stainless Steel Tube Fitting Compression Fittings 1/4 In 3-Way Tee Female Run Tee
-
DPR1 Ultra High Purity Two Stage Dual Stage Pressure Reducing Regulator Semiconductor Grade Regulators
-
Manual Gas Rack High Purity Gas Delivery Systems JW-100-GR
-
Line And Panel Mounting Adjustable Low Pressure Propane And Nitrogen Pressure Regulator JSR-3L & JSR-3LP Series