Blog
Jewellok is a professional pressure regulator and valve manufacturer and supplier.
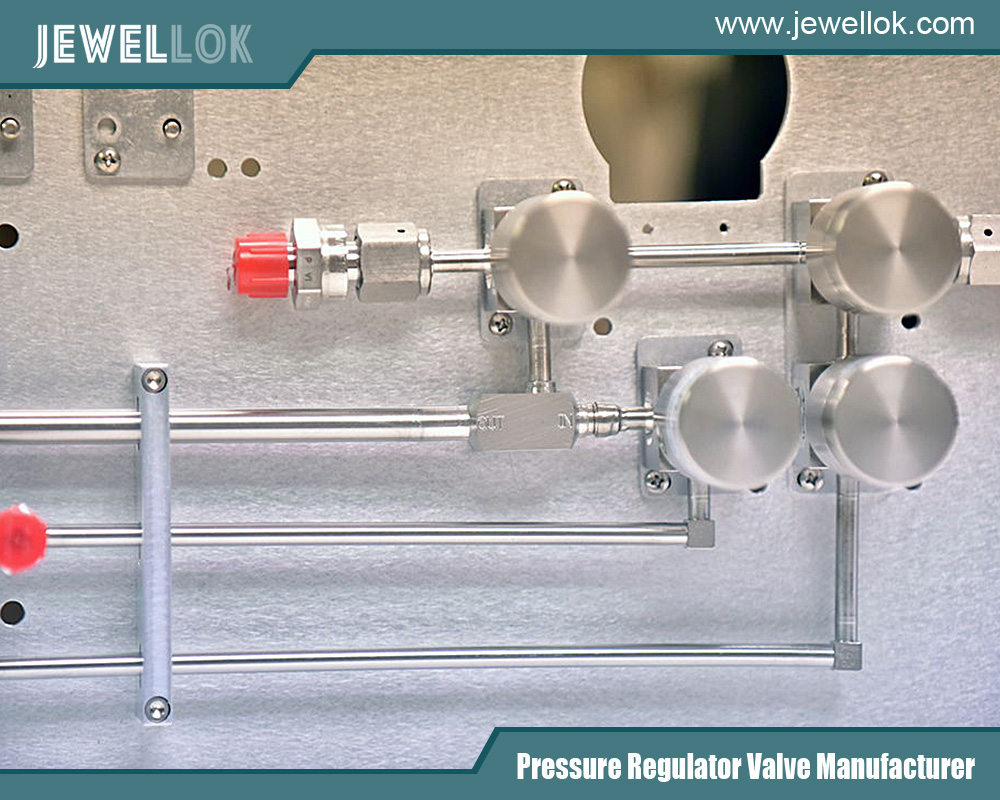
How Often Should Pressure Relief Valves Be Tested and Replaced?
- Pressure Regulator Valve Manufacturer
- 1 1 2 gas pressure regulator, 1 2 gas regulator, 1 2 propane regulator, 1/2 gas pressure regulator, 12v electric valve, 2 electric valve, 6mm compression union, adjustable propane pressure regulator, argon gas pressure regulator, Diaphragm Valve Manufacturers, electric water valve, gas cylinder, gas manifold system, gas pressure regulator how it works, gas regulator, gas used in semiconductor chip manufacturing, high pressure argon regulator, high pressure flexible hose pipe, high purity regulator, how a regulator works, how a solenoid works, how gas pressure regulator works, how pressure regulator works, industrial regulators, lab fittings exporter, oxygen regulator gauge, pressure regulator, pressure relief valves, pressure safety valve vs relief valve, propane pressure regulator valve, relief valve and safety valve difference, safety valve vs relief valve, semiconductor gas, valve manifold box, water valve timer, what is a flame arrestor
- No Comments
How Often Should Pressure Relief Valves Be Tested and Replaced?
Pressure relief valves (PRVs) are vital safety components in industrial systems, designed to protect equipment, personnel, and the environment by releasing excess pressure from pipelines, vessels, and other pressurized systems. Found in industries such as oil and gas, chemical processing, hydrogen energy, pharmaceuticals, power generation, and manufacturing, PRVs prevent catastrophic failures like explosions, leaks, or equipment damage caused by over-pressurization. However, to ensure their reliability, PRVs must be regularly tested to verify performance and replaced when they no longer meet safety standards. Determining the optimal frequency for testing and replacement is a complex task, influenced by factors like application, operating conditions, regulatory requirements, and valve design. This article explores the importance of PRVs, the factors affecting testing and replacement schedules, recommended practices, testing methods, regulatory guidelines, and emerging innovations to help organizations maintain safe and efficient operations.
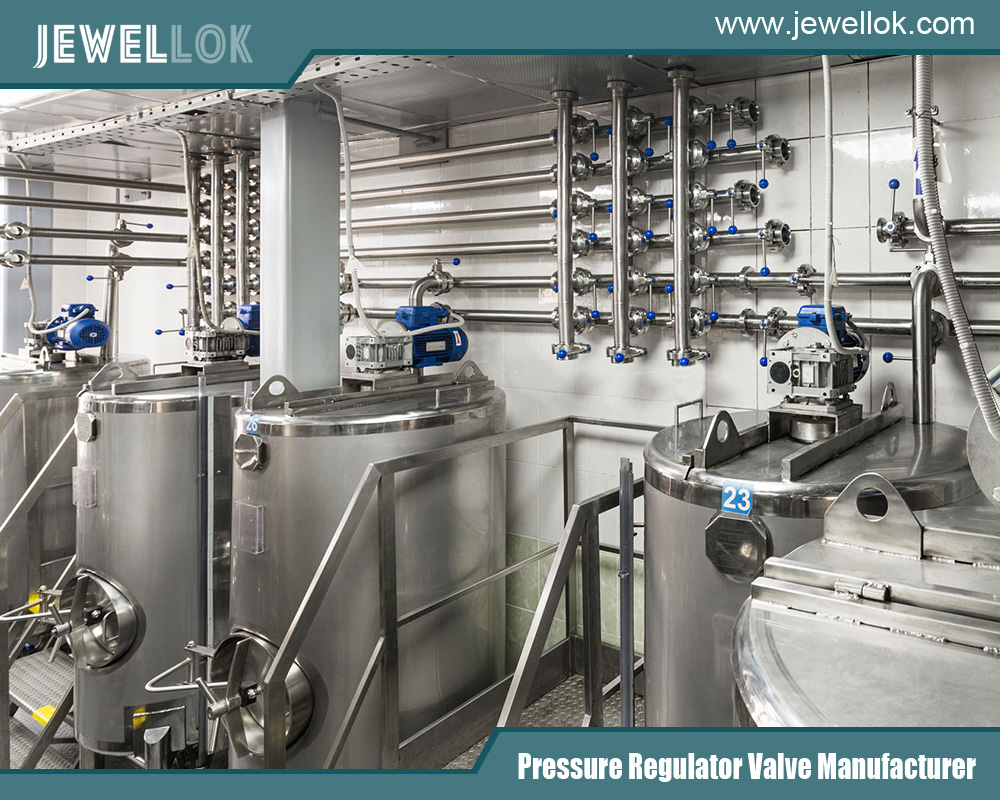
The Importance of Pressure Relief Valves
PRVs, also known as safety relief valves or pressure safety valves, are mechanical devices that automatically open to release excess pressure when a system exceeds its maximum allowable working pressure (MAWP). Once the pressure returns to a safe level, the valve closes, maintaining system integrity. PRVs are used in various applications:
- Oil and Gas: Protecting pipelines and storage tanks from over-pressure during transport or refining.
- Hydrogen Energy: Safeguarding high-pressure hydrogen systems in fuel cells, refueling stations, and electrolysis plants.
- Chemical Processing: Preventing reactor vessel failures when handling reactive gases like ammonia or chlorine.
- Pharmaceuticals: Ensuring safe pressure control in sterile processing systems.
- Power Generation: Protecting boilers and turbines from steam over-pressure.
A malfunctioning PRV can lead to severe consequences:
- Safety Hazards: Over-pressure can cause explosions, fires, or toxic gas releases, endangering workers and communities.
- Equipment Damage: Excessive pressure can rupture pipelines, vessels, or fittings, leading to costly repairs.
- Environmental Impact: Leaks or uncontrolled releases can pollute air, water, or soil, violating environmental regulations.
- Regulatory Non-Compliance: Failure to maintain PRVs can result in fines or shutdowns.
Regular testing and timely replacement are critical to ensuring PRVs function as intended, protecting systems and complying with industry standards.
Factors Influencing Testing and Replacement Frequency
The frequency of PRV testing and replacement depends on several factors, each requiring careful consideration to balance safety, cost, and operational efficiency.
- Application and Operating Conditions
The system’s application and operating environment significantly affect PRV performance:
- Fluid Type: Corrosive fluids (e.g., chlorine, sulfuric acid) or abrasive slurries accelerate valve wear, necessitating frequent testing.
- Pressure and Temperature: High-pressure (e.g., 700 bar in hydrogen systems) or extreme-temperature conditions (e.g., cryogenic hydrogen at -253°C) stress valve components, reducing lifespan.
- Duty Cycle: PRVs in systems with frequent pressure cycles (e.g., batch processing) wear faster than those in stable systems.
- Cleanliness: Dirty or particulate-laden fluids can clog or damage valve seats, requiring more frequent maintenance.
- Impact: Harsh conditions or demanding applications typically require more frequent testing and earlier replacement.
- Valve Design and Materials
PRV design and construction influence durability and maintenance needs:
- Spring-Loaded PRVs: Common in most applications, these valves rely on a spring to close after pressure release. Wear on the spring or seat can reduce reliability.
- Pilot-Operated PRVs: Used in high-pressure systems, these offer precise control but have more complex components, requiring specialized testing.
- Bellows-Sealed PRVs: Protect against backpressure or corrosive fluids, extending lifespan but requiring careful inspection of bellows integrity.
- Material Compatibility: Valves made of 316L stainless steel or Hastelloy resist corrosion better than carbon steel, affecting replacement intervals.
- Impact: Robust designs and materials may allow longer intervals between testing and replacement, but complex valves require specialized maintenance.
- Regulatory and Industry Standards
Regulations and standards mandate minimum testing and maintenance schedules:
- ASME Section VIII: Requires PRV testing for pressure vessels, typically annually or based on risk-based inspection (RBI) protocols.
- API 520/526: Provides guidelines for PRV sizing, testing, and maintenance in oil and gas, recommending testing every 1–5 years.
- NFPA 56: Specifies PRV requirements for hydrogen systems, emphasizing regular testing to prevent flammable gas risks.
- OSHA 1910.119: Mandates process safety management (PSM) for hazardous chemicals, including PRV maintenance.
- ISO 4126: Governs safety valves globally, recommending testing intervals based on application and risk.
- Impact: Compliance with standards often dictates minimum testing frequencies, but organizations may adopt stricter schedules for critical applications.
- Operational History and Failure Rates
Historical data on PRV performance and system incidents can guide maintenance schedules:
- Failure Frequency: Frequent failures or leaks indicate the need for more frequent testing or replacement.
- Near-Misses: Incidents like pressure spikes or valve sticking suggest underlying issues requiring immediate attention.
- Maintenance Records: Consistent performance may justify extended intervals, while recurring issues warrant shorter cycles.
- Impact: Data-driven insights help tailor testing and replacement schedules to specific systems.
- Risk and Consequence of Failure
The potential consequences of PRV failure influence maintenance frequency:
- High-Risk Systems: Systems handling flammable (e.g., hydrogen) or toxic (e.g., arsine) gases require frequent testing due to severe safety risks.
- Critical Processes: In pharmaceuticals or semiconductors, PRV failure can halt production, necessitating rigorous maintenance.
- Low-Risk Systems: Stable systems with non-hazardous fluids (e.g., water) may require less frequent testing.
- Impact: Higher risk or consequence justifies more frequent testing and proactive replacement.
Recommended Testing and Replacement Schedules
While schedules vary by application, industry, and regulation, general guidelines provide a starting point. Below are recommended frequencies based on common practices and standards, which should be adjusted based on the factors above.
Testing Frequency
Testing verifies that a PRV opens at the set pressure, releases adequately, and reseats properly. Common testing methods include bench testing, in-situ testing, and pop testing (described later).
- High-Risk or Critical Systems (e.g., hydrogen refueling, chemical reactors):
Test every 6–12 months to ensure reliability.
Example: API 510 recommends annual testing for pressure vessels in hazardous service.
- Moderate-Risk Systems (e.g., natural gas pipelines, boiler systems):
Test every 1–3 years, depending on operating conditions and historical performance.
Example: ASME BPVC suggests biennial testing for steam boilers.
- Low-Risk Systems (e.g., water treatment, non-hazardous gases):
Test every 3–5 years, assuming stable conditions and clean fluids.
Example: General industry practice for non-critical applications.
- Event-Based Testing: Test after incidents (e.g., pressure spikes, leaks) or major system changes (e.g., fluid type, operating pressure).
- Action: Develop a testing schedule based on risk assessments, regulatory requirements, and manufacturer recommendations, documenting results for compliance.
Replacement Frequency
PRVs are typically replaced when they fail tests, show significant wear, or reach the end of their service life. Replacement intervals depend on design, materials, and operating conditions:
- Spring-Loaded PRVs:
Replace every 5–10 years in moderate conditions, or 2–5 years in harsh environments (e.g., corrosive fluids, high cycles).
- Pilot-Operated PRVs:
Replace every 7–12 years, with more frequent component replacement (e.g., pilot seals) every 2–5 years.
- Bellows-Sealed PRVs:
Replace every 5–8 years, with bellows inspection every 1–2 years to detect fatigue.
- Event-Based Replacement: Replace immediately if the valve fails to open at set pressure, leaks, or shows corrosion, sticking, or seat damage.
- Action: Establish replacement criteria based on test results, visual inspections, and manufacturer service life estimates, maintaining spare valves for quick swaps.
Testing Methods for PRVs
Accurate testing is essential to assess PRV performance and determine maintenance or replacement needs. Common methods include:
- Bench Testing
- Description: Remove the PRV from the system and test it on a specialized bench with controlled pressure sources.
- Procedure: Apply increasing pressure to verify the valve opens at the set pressure (pop pressure), releases adequately, and reseats properly. Check for leaks and measure blowdown (pressure drop before reseating).
- Advantages: Highly accurate, allows thorough inspection, and enables repairs or adjustments.
- Disadvantages: Requires system shutdown, labor-intensive, and may not reflect in-situ conditions.
- Use Case: Ideal for high-risk systems or when detailed analysis is needed.
- Action: Use certified test benches compliant with ASME PTC 25 or API 527 standards.
- In-Situ Testing
- Description: Test the PRV without removing it, using portable devices to apply pressure or monitor performance.
- Procedure: Use a hydraulic or pneumatic lift-assist device to simulate pressure and measure pop pressure and reseat behavior.
- Advantages: Minimizes downtime, reflects real-world conditions, and is suitable for large or fixed valves.
- Disadvantages: Less precise than bench testing, limited by system constraints.
- Use Case: Suitable for moderate-risk systems or when shutdown is impractical.
- Action: Employ trained technicians and calibrated equipment to ensure accurate results.
- Pop Testing
- Description: Briefly increase system pressure to trigger the PRV and observe its response.
- Procedure: Gradually raise pressure until the valve opens, noting the pop pressure and reseat behavior.
- Advantages: Quick and simple, performed during normal operation.
- Disadvantages: Risky for hazardous systems, limited data on valve condition, and may cause wear.
- Use Case: Used for low-risk systems or as a preliminary check before detailed testing.
- Action: Conduct pop testing only with safety protocols in place and avoid overuse to prevent valve damage.
- Non-Destructive Testing (NDT)
- Description: Inspect PRV components for defects without disassembly, using methods like ultrasonic testing or radiography.
- Procedure: Check for corrosion, cracks, or material fatigue in valve bodies, springs, or bellows.
- Advantages: Non-invasive, extends valve life by identifying issues early.
- Disadvantages: Requires specialized equipment and expertise.
- Use Case: Complements bench or in-situ testing for critical applications.
- Action: Integrate NDT into maintenance schedules for high-value or high-risk PRVs.
Regulatory and Industry Guidelines
Compliance with regulations and standards is non-negotiable for PRV maintenance. Key guidelines include:
- ASME Boiler and Pressure Vessel Code (BPVC): Mandates testing and maintenance for pressure vessels, with intervals based on risk and inspection history.
- API Standards (520, 526, 510): Recommend testing every 1–5 years for oil and gas, with replacement based on condition.
- NFPA 56: Requires regular PRV testing for hydrogen systems, emphasizing leak prevention.
- OSHA 1910.119: Enforces PSM requirements, including documented PRV maintenance for hazardous processes.
- ISO 4126: Provides global standards for safety valves, recommending risk-based testing intervals.
- EPA Regulations: Govern emissions from PRV releases, requiring treatment for hazardous gases.
- Action: Review applicable standards, maintain compliance records, and consult with regulatory experts to ensure adherence.
Best Practices for Testing and Replacement
To optimize PRV performance and safety, follow these best practices:
- Conduct Risk Assessments: Use HAZOP or FMEA to identify critical PRVs and prioritize testing.
- Develop a Maintenance Plan: Create a schedule for testing, inspection, and replacement, tailored to system risk and conditions.
- Use Certified Technicians: Ensure personnel are trained in PRV testing and comply with standards like ASME or API.
- Document Everything: Record test results, maintenance actions, and replacements for compliance and trend analysis.
- Maintain Spare Valves: Keep calibrated spares to minimize downtime during testing or replacement.
- Monitor Performance Trends: Use data from tests and inspections to adjust schedules proactively.
- Partner with Suppliers: Work with reputable manufacturers for quality valves, technical support, and spare parts.
Challenges and Solutions
- Challenge: Downtime during testing.
- Solution: Use in-situ testing or redundant systems to minimize disruption
- Challenge: High maintenance costs. embora
- Solution: Focus on TCO, prioritizing durable valves and preventive maintenance.
- Challenge: Regulatory complexity.
- Solution: Engage compliance consultants and adopt risk-based inspection (RBI) strategies.
- Challenge: Lack of expertise.
- Solution: Provide training and leverage supplier expertise for testing and repairs.
Emerging Trends in PRV Maintenance
Innovations are enhancing PRV testing and replacement practices:
- Smart PRVs: IoT-enabled valves with sensors monitor pressure, temperature, and performance, enabling predictive maintenance.
- Digital Twins: Virtual models simulate PRV behavior, optimizing testing schedules and identifying failure modes.
- Automated Testing Systems: Portable, automated test rigs improve in-situ testing accuracy and reduce labor.
- Sustainable Materials: Eco-friendly alloys and coatings extend valve life and align with environmental goals.
- AI-Driven Analytics: Machine learning predicts valve failures based on historical data, refining maintenance schedules.
- Impact: These technologies improve accuracy, reduce costs, and enhance safety.
Case Studies
- Hydrogen Refueling Station (Norway): Annual bench testing and smart PRVs with IoT sensors ensured zero failures in a 700-bar hydrogen system, complying with NFPA 56 and saving $100,000 in potential downtime.
- Chemical Plant (USA): Biennial in-situ testing and Hastelloy PRVs for chlorine service extended valve life to 8 years, reducing replacement costs by 30% while meeting OSHA PSM requirements.
- Power Plant (India): Triennial testing with NDT and pilot-operated PRVs for steam boilers improved reliability, preventing outages and ensuring ASME compliance.
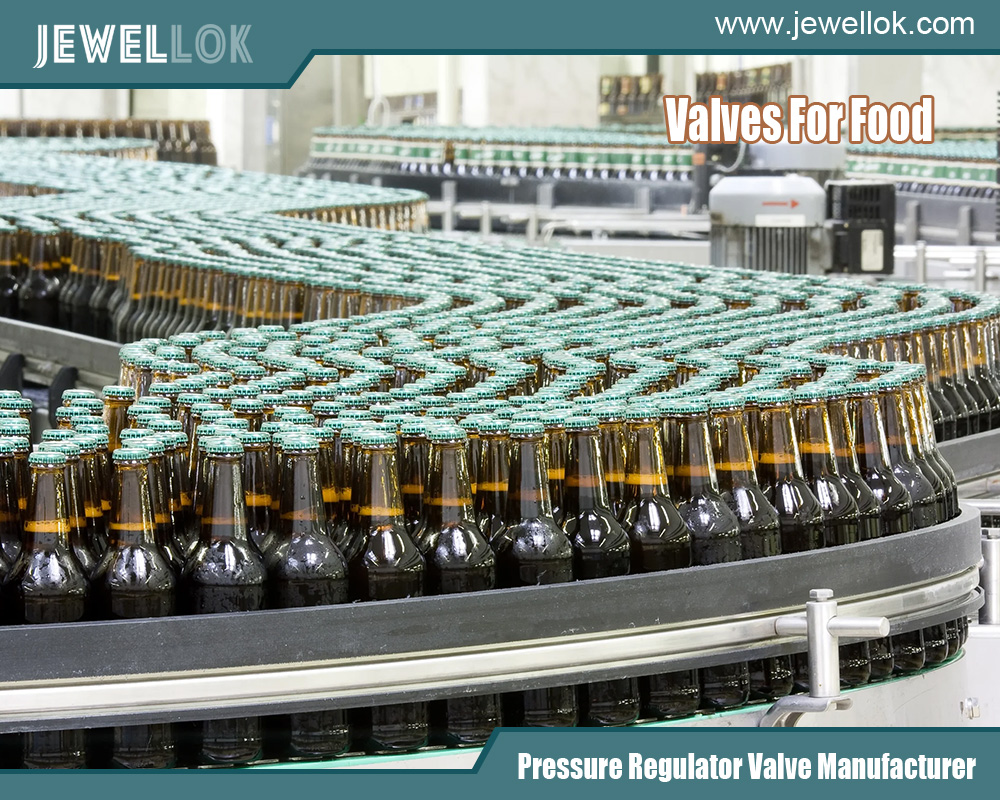
Conclusion
Determining how often pressure relief valves should be tested and replaced is a critical aspect of ensuring safety, compliance, and efficiency in industrial systems. Testing frequencies—ranging from 6 months to 5 years—depend on application, operating conditions, valve design, regulations, and risk levels, while replacement intervals typically span 2–12 years based on wear and performance. By implementing robust testing methods (bench, in-situ, pop, NDT), adhering to standards like ASME, API, and OSHA, and adopting best practices like risk assessments and documentation, organizations can maintain reliable PRVs. Emerging technologies, such as smart valves and AI analytics, are further enhancing maintenance strategies, reducing costs, and improving safety. Despite challenges like downtime and regulatory complexity, proactive testing and replacement schedules, supported by trained personnel and quality suppliers, ensure PRVs protect systems and personnel effectively. By prioritizing these practices, industries like hydrogen energy, chemical processing, and power generation can mitigate risks, comply with regulations, and drive operational excellence.
For more about how often should pressure relief valves be tested and replaced?, you can pay a visit to Jewellok at https://www.jewellok.com/ for more info.
Recent Posts
Best High-Pressure Gas Regulators For Industrial Use
Pressure Relief Valve Manufacturers
High Pressure Ball Valve Manufacturer
Application Of Ultra High Purity Gas Manifold Panels
Pressure Reducing Valve Manufacturers
Tags
Recommended Products
-
High Pressure High Temperature Pneumatic Ultrahigh Purity Stainless Steel Diaphragm Valves
-
JR1300 Series Ultra High Purity Single Stage Regulator High Flow Line Regulator For Ultra High Purity Intermediate Flow
-
766L High Purity Female Connector UHP Fitting Female Connector
-
T-BOX JW-TB-C Special Gas Delivery System Gas Valve Manifold Boxes
-
Fully Automated Gas Cabinet Gas Rack Gas Delivery Systems JW-300-GR
-
768LN Stainless Steel Male Pipe Tube Butt Weld Connector And Tube Fittings Supplier
-
Stainless Steel Single Stage Semiconductor Grade Pressure Control Module Pressure Control Panels JSP-6A Series
-
772L Male Branch Tee | Stainless Steel High-Purity Tube Fitting Male Branch Tee