Blog
Jewellok is a professional pressure regulator and valve manufacturer and supplier.
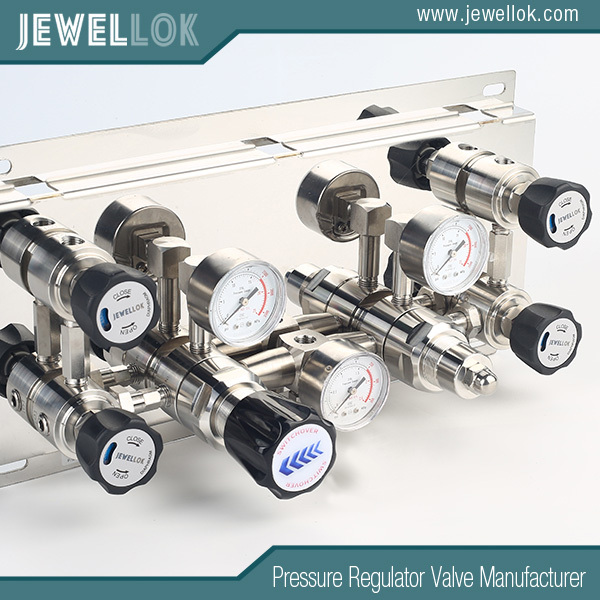
How To Choose The Right Pressure Regulator? A Professional Guide to Help You Make an Accurate Purchase
- Pressure Regulator Valve Manufacturer
- 1 1 2 gas pressure regulator, 1/2 gas pressure regulator, 12v electric valve, 2 electric valve, 3000PSI Nitrogen Panel Mount Pressure Regulator, 6mm compression union, adjustable air pressure regulator, adjustable hydraulic pressure regulator, Adjustable Pressure Regulators, adjustable propane pressure regulator, air compressor pressure regulator, air pressure regulator diagram, air pressure regulator electronic control, Air pressure Regulator for Pneumatic, air pressure regulator how it works, Air Pressure Regulator Manufacturer, air pressure regulator valve with gauge, air pressure regulator with gauge, air pressure regulator with relief valve, electric water valve, high pressure argon regulator, high pressure flexible hose pipe, high purity regulator, pressure regulator, relief valve and safety valve difference, safety valve vs relief valve, semiconductor gas, the right pressure regulator, valve manifold box
- No Comments
How To Choose The Right Pressure Regulator? A Professional Guide to Help You Make an Accurate Purchase
Pressure regulators are critical components in industrial systems, controlling and maintaining the pressure of gases or liquids to ensure safe, efficient, and reliable operation. Used in industries such as oil and gas, chemical processing, hydrogen energy, pharmaceuticals, semiconductors, water treatment, and manufacturing, pressure regulators protect equipment, optimize processes, and ensure compliance with safety standards. Selecting the right pressure regulator is a complex task that requires careful consideration of factors like application requirements, pressure and flow specifications, material compatibility, environmental conditions, regulatory compliance, and maintenance needs. An incorrect choice can lead to pressure instability, equipment damage, safety hazards, or costly downtime. This article provides a professional, step-by-step guide to choosing the right pressure regulator, exploring key criteria, practical considerations, and emerging trends to help stakeholders make informed purchasing decisions that enhance system performance and reliability.
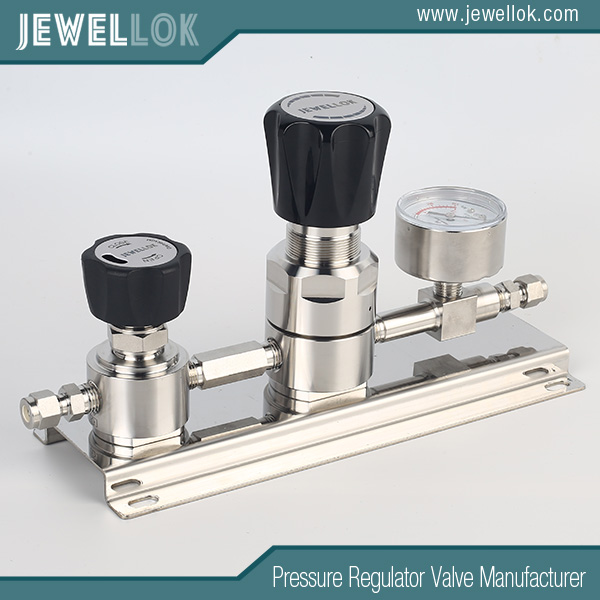
Understanding Pressure Regulators
A pressure regulator is a device that reduces or maintains the pressure of a fluid (gas or liquid) from a high-pressure source to a lower, controlled output pressure suitable for downstream equipment or processes. Regulators are used to:
- Stabilize pressure in pipelines, cylinders, or reactors.
- Protect sensitive equipment (e.g., gauges, sensors) from over-pressure.
- Ensure consistent flow in dynamic systems (e.g., gas chromatography).
- Maintain safety in hazardous fluid systems (e.g., hydrogen, chlorine).
Pressure regulators come in various types, including:
- Single-Stage Regulators: Reduce pressure in one step, ideal for stable inlet pressures.
- Two-Stage Regulators: Reduce pressure in two steps, offering better control for fluctuating inlet pressures.
- Back-Pressure Regulators: Maintain upstream pressure by releasing excess fluid.
- Differential Pressure Regulators: Control pressure relative to a reference pressure.
- Specialty Regulators: Designed for ultra-high-purity (UHP) gases, high-pressure systems, or corrosive fluids.
Choosing the right pressure regulator involves aligning its specifications with the application’s needs. Below, we outline a structured approach to guide this process.
Step 1: Define Application Requirements
The first step is to understand the specific requirements of your application, as these dictate the regulator’s design, materials, and performance.
1.1 Fluid Type and Compatibility
The fluid being regulated (gas, liquid, or mixed-phase) determines the regulator’s material and construction:
- Corrosive Fluids: Chemicals like ammonia, chlorine, or acids require corrosion-resistant materials such as 316L stainless steel, Hastelloy, or PTFE-lined components.
- Non-Corrosive Fluids: Water, air, or nitrogen may allow brass or 304 stainless steel, which are cost-effective but less resistant to corrosion.
- Ultra-High-Purity (UHP) Gases: Semiconductor or analytical applications (e.g., silane, nitrogen) demand electropolished 316L stainless steel to minimize contamination.
- Hazardous Gases: Flammable (e.g., hydrogen) or toxic (e.g., arsine) gases require regulators with leak-tight seals and safety features like tied diaphragms.
- Hygienic Fluids: Food-grade or pharmaceutical fluids need sanitary regulators with polished surfaces (e.g., Ra < 0.4 µm) and clean-in-place (CIP) compatibility.
- Action: Create a fluid profile specifying composition, corrosiveness, purity requirements, and state (gas/liquid), and ensure wetted parts are compatible.
1.2 Pressure and Flow Requirements
The system’s pressure and flow characteristics influence regulator selection:
- Inlet Pressure: Determine the maximum and minimum inlet pressure from the source (e.g., 3000 psi from a gas cylinder).
- Outlet Pressure: Specify the desired downstream pressure (e.g., 100 psi for a process line). Ensure the regulator’s outlet range covers this value.
- Flow Rate: Match the regulator’s flow capacity (e.g., Cv value) to the system’s flow requirements. High-flow systems (e.g., pipelines) need larger Cv values, while low-flow systems (e.g., instrumentation) require precise control.
- Pressure Stability: For applications with fluctuating inlet pressures (e.g., gas cylinders depleting over time), two-stage regulators provide better stability than single-stage models.
- Action: Compile a datasheet with inlet/outlet pressure ranges, flow rate, and stability needs, and verify the regulator’s Cv and pressure range.
1.3 Application Context
Consider the industry and specific use case:
- Oil and Gas: Requires high-pressure regulators (e.g., 6000 psi) for pipeline or wellhead control, often with 316L stainless steel for corrosion resistance.
- Hydrogen Energy: Needs regulators for ultra-high-pressure hydrogen (e.g., 700 bar) with materials resistant to embrittlement (e.g., austenitic stainless steel).
- Pharmaceuticals: Demands sanitary regulators for sterile water or gas systems, meeting FDA or 3-A standards.
- Semiconductors: Requires UHP regulators for precise gas delivery (e.g., nitrogen, silane) with minimal particle generation.
- Water Treatment: Uses regulators for moderate pressures and corrosion resistance against chlorinated water.
- Manufacturing: Employs regulators for compressed air or hydraulic systems, prioritizing durability and cost.
- Action: Define the industry, application (e.g., process control, cylinder regulation), and any regulatory or hygienic requirements.
Step 2: Select the Appropriate Regulator Type
The regulator type impacts performance, precision, and suitability for the application.
2.1 Single-Stage Regulators
- Design: Reduce inlet pressure to outlet pressure in one step using a diaphragm or piston.
- Advantages: Simple, compact, and cost-effective; ideal for stable inlet pressures.
- Disadvantages: Susceptible to outlet pressure drift as inlet pressure decreases (supply pressure effect).
- Applications: Gas cylinder regulation with consistent inlet pressure (e.g., nitrogen in manufacturing).
2.2 Two-Stage Regulators
- Design: Reduce pressure in two steps, using two diaphragms or pistons for enhanced stability.
- Advantages: Maintains consistent outlet pressure despite fluctuating inlet pressure; ideal for long-duration use.
- Disadvantages: More expensive and complex than single-stage models.
- Applications: Laboratory gas systems or depleting gas cylinders (e.g., helium in gas chromatography).
2.3 Back-Pressure Regulators
- Design: Maintain upstream pressure by releasing excess fluid when pressure exceeds the set point.
- Advantages: Protects upstream equipment from over-pressure; suitable for dynamic systems.
- Disadvantages: Not for downstream pressure control.
- Applications: Pump discharge lines or reactor pressure control.
2.4 Specialty Regulators
- Design: Tailored for specific needs, such as UHP, high-pressure, or corrosive fluids.
- Advantages: Meet stringent requirements (e.g., <10 ppb contamination, 10,000 psi).
- Disadvantages: Higher cost and limited availability.
- Applications: Semiconductor gas delivery, hydrogen refueling, or corrosive chemical processing.
- Action: Choose the regulator type based on pressure stability, flow control needs, and application specificity (e.g., two-stage for fluctuating inlet pressures).
Step 3: Choose the Right Materials
Material selection ensures compatibility, durability, and compliance.
3.1 Body and Wetted Parts
- 316L Stainless Steel: Ideal for corrosive fluids (e.g., chlorine, ammonia) and UHP applications (e.g., semiconductors).
- Brass: Cost-effective for non-corrosive gases (e.g., nitrogen, air) but unsuitable for aggressive media.
- Hastelloy/Monel: For extreme corrosion (e.g., hydrofluoric acid, seawater).
- PTFE/Polymer-Lined: For highly corrosive or hygienic applications (e.g., pharmaceuticals).
3.2 Diaphragm and Seal Materials
- PTFE: Chemical resistance for acids and solvents.
- Viton: Suitable for oils and hydrocarbons.
- EPDM: Ideal for water and steam.
- Stainless Steel: For high-pressure or high-temperature applications (e.g., steam).
- Action: Select body and seal materials based on fluid compatibility, temperature, and pressure, prioritizing 316L stainless steel for corrosive or UHP systems.
Step 4: Specify Performance Characteristics
Performance specifications ensure the regulator meets operational needs.
4.1 Pressure Control Accuracy
- Precision: High-precision regulators (e.g., ±0.1 psi) are required for applications like semiconductors or analytical instruments, while general-purpose regulators (e.g., ±1 psi) suit manufacturing.
- Droop: The decrease in outlet pressure as flow increases. Low-droop regulators maintain stability in high-flow systems.
- Supply Pressure Effect: The change in outlet pressure due to inlet pressure variations. Two-stage or high-quality single-stage regulators minimize this effect.
- Action: Specify required accuracy and select low-droop or two-stage regulators for precision applications.
4.2 Flow Capacity
- Cv Value: The flow coefficient (Cv) indicates the regulator’s flow capacity. High Cv values (e.g., >1.0) suit pipelines, while low Cv values (e.g., <0.1) are for instrumentation.
- Flow Curve: Review manufacturer flow curves to ensure the regulator maintains pressure across the required flow range.
- Action: Match the regulator’s Cv to the system’s flow rate, using manufacturer data for verification.
4.3 Safety Features
- Relief Valves: Integrated relief valves protect downstream equipment from over-pressure.
- Tied Diaphragms: Prevent diaphragm failure in hazardous gas systems.
- Gauge Ports: Allow pressure monitoring for troubleshooting.
- Locking Adjustments: Prevent unauthorized pressure changes.
- Action: Select regulators with safety features for hazardous or critical applications.
Step 5: Consider Environmental and Installation Factors
Environmental conditions and installation practices affect regulator performance and longevity.
5.1 Environmental Conditions
- Corrosive Atmospheres: Coastal or chemical plant environments require 316 stainless steel or coated regulators to resist salt or acid exposure.
- Temperature Extremes: Ensure materials withstand fluid and ambient temperatures (e.g., -40°C to 200°C for stainless steel). Use heated regulators for cryogenic fluids (e.g., liquid nitrogen).
- Ingress Protection: IP65 or IP67 ratings protect against dust and water in outdoor or washdown environments (e.g., food processing).
- Vibration: Robust designs or mounting brackets prevent drift in high-vibration areas (e.g., near compressors).
- Action: Specify materials and IP ratings to match environmental conditions, and use vibration-resistant designs where needed.
5.2 Installation Considerations
- Orientation: Most regulators work in any orientation, but verify manufacturer guidelines for optimal performance.
- Piping: Use filters or strainers upstream to protect the regulator from debris, and ensure proper piping size to avoid flow restrictions.
- Accessibility: Install regulators in accessible locations for adjustment, maintenance, and monitoring.
- Ventilation: For gas regulators, ensure adequate ventilation to prevent gas accumulation in case of leaks.
- Action: Follow manufacturer installation guidelines, using filters and ensuring accessibility.
Step 6: Ensure Regulatory and Safety Compliance
Compliance with industry standards and safety requirements is critical, especially in regulated industries.
6.1 Key Standards
- ASME B31.3: Governs process piping, including regulator materials and performance.
- API 520/526: Guides pressure control in oil and gas, emphasizing safety.
- CGA E-4: Specifies regulator design for compressed gas systems.
- FDA/3-A: Require hygienic designs for food and pharmaceutical regulators.
- NFPA 56: Mandates safe materials for hydrogen systems, including embrittlement resistance.
- SEMI F19: Defines UHP regulator requirements for semiconductors.
6.2 Safety Certifications
- ATEX/IECEx: Ensure regulators are intrinsically safe for explosive atmospheres (e.g., hydrogen refueling).
- ISO 9001: Confirms supplier quality management for consistent performance.
- Action: Verify compliance with relevant standards and request certifications from suppliers.
Step 7: Evaluate Maintenance and Total Cost of Ownership (TCO)
The regulator’s maintenance needs and TCO impact long-term reliability and cost.
7.1 Maintenance Requirements
- Inspection Frequency: High-precision regulators (e.g., UHP systems) require frequent checks, while general-purpose models need less maintenance.
- Repairability: Choose regulators with replaceable diaphragms, seats, or seals for easy repairs.
- Cleaning: Sanitary or UHP regulators may require periodic cleaning to maintain compliance.
- Action: Establish a maintenance schedule based on application criticality and manufacturer recommendations, and maintain spare parts.
7.2 Total Cost of Ownership
- Upfront Cost: Stainless steel regulators cost more than brass but offer durability.
- Maintenance Costs: Low-maintenance designs (e.g., two-stage) reduce long-term expenses.
- Lifespan: High-quality regulators (e.g., 316L stainless steel) last longer in corrosive environments.
- Action: Calculate TCO by factoring in purchase price, maintenance, and lifespan, prioritizing quality for critical systems.
Step 8: Partner with Reliable Suppliers
The supplier’s expertise, quality, and support are crucial for selecting the right regulator.
8.1 Supplier Evaluation
- Reputation: Choose suppliers with a track record in your industry (e.g., Swagelok, Tescom, or Emerson).
- Certifications: Ensure regulators meet ISO 9001, ASME, or industry-specific standards.
- Customization: Select suppliers offering tailored solutions (e.g., specific pressure ranges, materials).
8.2 Support Services
- Technical Support: Access to engineers for selection and troubleshooting.
- Testing/Calibration: Factory or on-site calibration to ensure accuracy.
- Warranty: Look for warranties covering defects or performance issues (e.g., 1–5 years).
- Action: Request supplier references, certifications, and service details, and negotiate terms for support and warranties.
Challenges and Solutions
- Challenge: Over-specifying regulators, increasing costs.
- Solution: Match specifications to needs (e.g., brass for non-corrosive fluids vs. stainless steel for UHP).
- Challenge: Pressure instability in dynamic systems.
- Solution: Use two-stage regulators or low-droop designs for fluctuating inlet pressures.
- Challenge: Regulatory compliance.
- Solution: Work with suppliers to ensure regulators meet standards like ASME or FDA.
- Challenge: Contamination in UHP systems.
- Solution: Use electropolished 316L stainless steel regulators with tied diaphragms.
Emerging Trends
- Smart Regulators: IoT-enabled regulators with sensors monitor pressure, flow, and leaks, enabling predictive maintenance.
- Sustainable Materials: Eco-friendly manufacturing and recyclable stainless steel align with green goals.
- Compact Designs: Miniaturized regulators for instrumentation or portable systems (e.g., medical devices).
- Advanced Diaphragms: Hastelloy or graphene-based diaphragms for extreme conditions.
- Impact: These trends enhance precision, sustainability, and automation, supporting modern industrial needs.
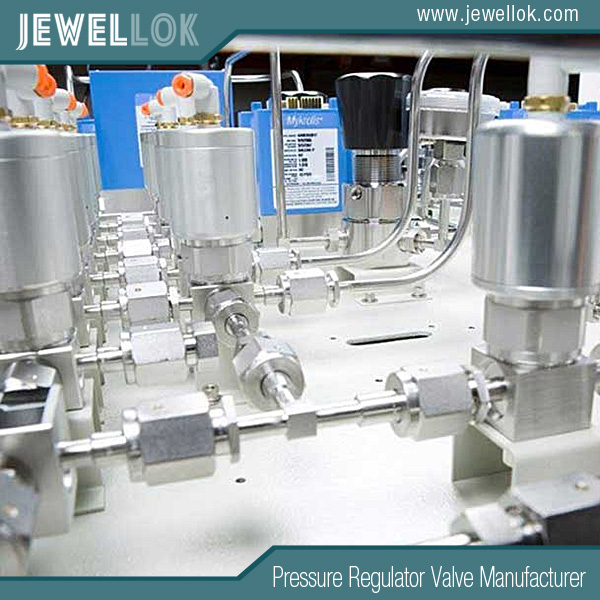
Conclusion
Choosing the right pressure regulator requires a systematic approach, considering fluid compatibility, pressure and flow requirements, regulator type, materials, environmental conditions, regulatory compliance, and maintenance needs. By defining application requirements, selecting the appropriate regulator type, ensuring material compatibility, and partnering with reliable suppliers, organizations can optimize pressure control, enhance safety, and reduce costs. Pressure regulators, from single-stage to UHP specialty models, offer versatile solutions for industries like semiconductors, hydrogen energy, and pharmaceuticals. Emerging trends like smart regulators and sustainable materials further enhance their value, supporting precision and innovation. By following the steps outlined in this professional guide, stakeholders can make accurate purchasing decisions, ensuring reliable pressure regulation and operational success in critical industrial systems.
For more about how to choose the right pressure regulator? a professional guide to help you make an accurate purchase, you can pay a visit to Jewellok at https://www.jewellok.com/ for more info.
Recent Posts
The Applications, Principles and Types of Water Solenoid Valve
Medical Oxygen Regulator Manufacturers in France
How Does a Bulk Specialty Gas Delivery System (BSGS) Work?
What is a Gas Pressure Relief Valve?
Tags
Recommended Products
-
High Pressure High Temperature Pneumatic Ultrahigh Purity Stainless Steel Diaphragm Valves
-
Ultra High Purity Trimethylaluminum TMA Gas Cabinet Liquid Delivering Cabinet Used For Specialty Gas Delivery System In Semiconductor
-
High Pressure High Flow Specialty Gas Control Panel With Diaphragm Valve , 3000Psig Oxygen Control Medical Changeover Manifold Panel
-
FT-BOX JW-FTB-C Valve Manifold Panels And Boxes With High Purity Configurable Systems
-
High Purity High Pressure Gas Cylinder Pressure Regulators Pressure Reducing Valve JSR-1E Series
-
739LF High Purity Female Adapter Tube To Pipe Fittings And Connectors
-
Single Stage Wall And Cabinet Mounting Pressure Control Panels JSP-2E Series For High Purity Gases
-
Hydrogen Manifold Argon Gas Manifold System Oxygen Manifold Propane Gas Manifold With Valves In Gas Manifold Changeover System