Blog
Jewellok is a professional pressure regulator and valve manufacturer and supplier.
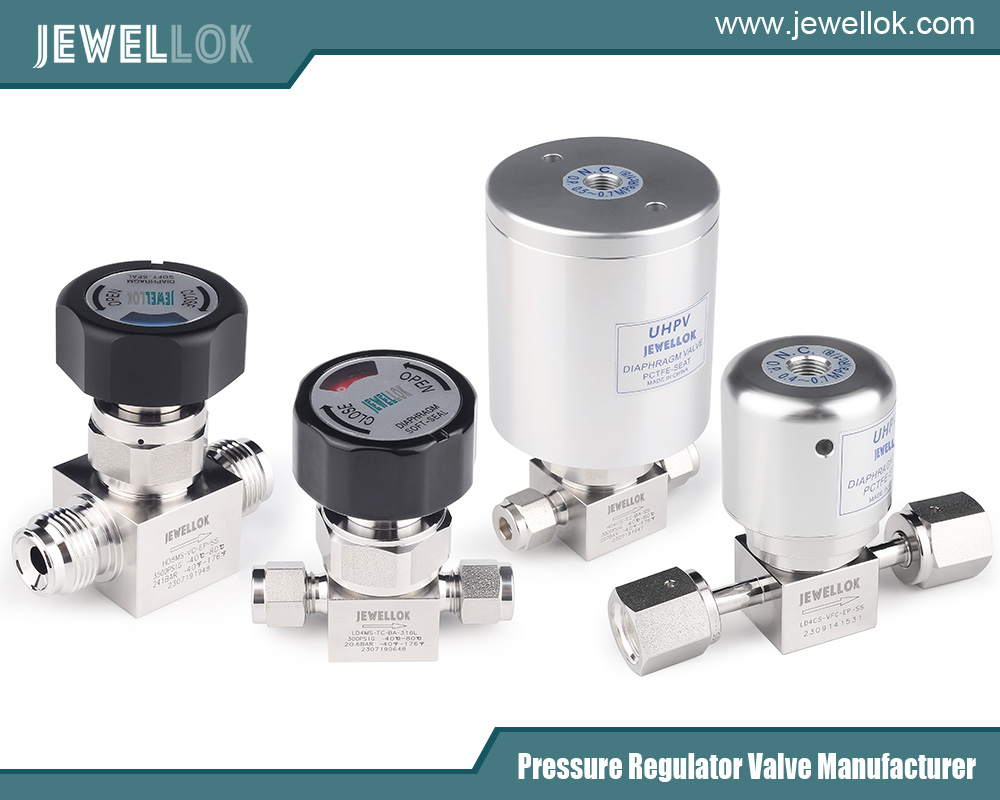
Single-stage ultra-high purity line gas regulator from natural gas regulator manufacturer
- Pressure Regulator Valve Manufacturer
- 3/4 natural gas regulator, adjustable natural gas regulator, china ultra high purity gas regulator manufacturer, difference between dual and single-stage regulator, Dual stage ultra high purity gas regulators, natural gas pressure reducing valve, natural gas regulator high pressure, natural gas regulator manufacturer, single stage propane regulator, Single-Stage Ultra-High Purity Line Gas Regulator, Stainless Steel Ultra High Purity Gas Regulator, ultra high purity gas regulator china, ultra high purity gas regulator in Mumbai, ultra high purity gas regulator malaysia, Ultra high purity gas regulator manual, ultra high purity gas regulator thailand, Ultra High Purity Gas Regulators Malaysia
- No Comments
Single-stage ultra-high purity line gas regulator from natural gas regulator manufacturer
Introduction
In industries where precision and cleanliness are non-negotiable, the delivery of gases at controlled pressures with impeccable purity is a cornerstone of operational success. Enter the Single-Stage Ultra-High Purity Line Gas Regulator, a vital tool designed to ensure that gases are delivered safely, consistently, and free from contaminants. From semiconductor manufacturing to pharmaceutical production, this device plays an indispensable role in processes where even the tiniest impurity can lead to catastrophic failures or compromised safety.
A Single-Stage Ultra-High Purity Line Gas Regulator is a device that reduces the high pressure of a gas from a source, such as a cylinder or pipeline, to a lower, usable level in a single step. Unlike dual-stage regulators, which perform pressure reduction in two phases for enhanced stability, single-stage regulators are simpler, cost-effective, and well-suited for applications with stable inlet pressures. The “ultra-high purity” designation highlights its ability to maintain gas cleanliness, achieved through specialized materials and design features that prevent contamination. This article will explore the regulator’s components, operational principles, applications, advantages, maintenance needs, and real-world significance, offering a thorough understanding of its role in modern industry.
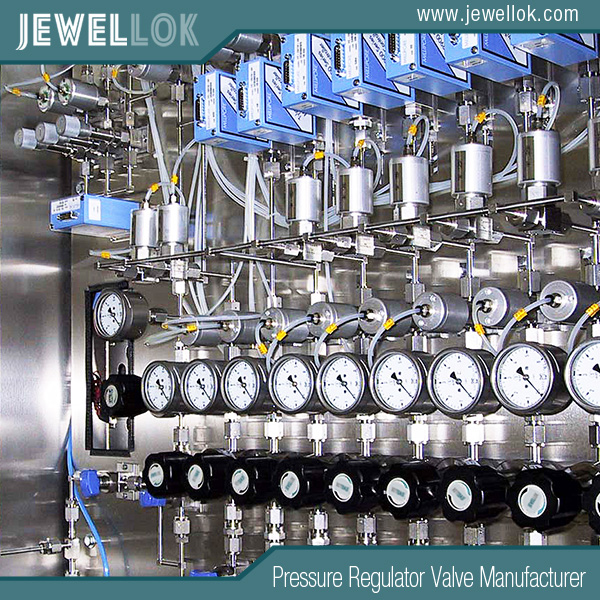
Components and Design
The effectiveness of a Single-Stage Ultra-High Purity Line Gas Regulator lies in its meticulously engineered components, each tailored to balance pressure control with gas purity. Here’s a breakdown of its key parts:
Inlet and Outlet Ports: These are the entry and exit points for the gas. In ultra-high purity models, these ports often feature specialized fittings, such as VCR (Vacuum Coupling Radiation) connections, to minimize leaks and contamination risks.
Diaphragm: The diaphragm senses downstream pressure and adjusts the valve to maintain the desired output. Made from materials like stainless steel or Hastelloy, it avoids outgassing—releasing trapped gases that could contaminate the flow.
Valve Assembly: Comprising a seat and poppet, this controls gas flow. The materials (often stainless steel or fluoropolymers like PTFE) are chosen for their compatibility with the gas and ability to form a tight, leak-proof seal.
Body and Bonnet: The regulator’s main structure is typically constructed from 316L stainless steel, a low-carbon alloy prized for its corrosion resistance and purity. Internal surfaces are electropolished to a mirror-like finish, reducing particle generation and adhesion.
Filters: Some models include inline filters to capture microscopic particles, further ensuring gas purity.
The design emphasizes minimal dead volume—areas where gas could stagnate and introduce impurities—and smooth internal surfaces to prevent particle buildup. These regulators are often assembled in cleanroom environments, adhering to stringent standards like those set by SEMI (Semiconductor Equipment and Materials International), ensuring they meet the purity demands of critical applications.
How It Works
The operation of a Single-Stage Ultra-High Purity Line Gas Regulator is both elegant and efficient. Gas enters the regulator at high pressure through the inlet port and encounters the valve assembly. The diaphragm, linked to the valve via a stem, senses the pressure on the outlet side and adjusts the valve accordingly. If the outlet pressure falls below the set point, the diaphragm opens the valve wider, increasing gas flow to raise the pressure. If the pressure exceeds the set point, the diaphragm closes the valve, reducing flow to lower the pressure.
This single-stage process means pressure reduction occurs in one step, making the regulator sensitive to inlet pressure fluctuations. For instance, as a gas cylinder depletes, the inlet pressure drops, which may cause slight variations in outlet pressure. However, in applications with stable inlet pressure—such as a full cylinder or a piped gas supply—this limitation is negligible, and the regulator performs admirably.
The “ultra-high purity” feature is achieved through non-reactive materials, tight seals, and designs that eliminate contamination risks. For example, the absence of elastomeric seals (which can degrade and release particles) and the use of metal-to-metal seals ensure that the gas remains pristine as it passes through the regulator.
Applications
The Single-Stage Ultra-High Purity Line Gas Regulator shines in industries where gas purity is critical. Here are some key applications:
Semiconductor Manufacturing: Processes like chemical vapor deposition (CVD) and plasma etching rely on ultra-pure gases (e.g., nitrogen, argon, or silane) to create microchips. A single impurity can cause defects, rendering chips unusable.
Pharmaceutical Production: Gases like oxygen or nitrogen are used in synthesis or as carriers. Contamination could compromise drug safety, making ultra-high purity regulators essential.
Research Laboratories: In chemistry, physics, or materials science, experiments demand gases free of impurities to ensure accurate results. For instance, gas chromatography relies on pure carrier gases like helium.
Aerospace and Defense: Applications such as environmental testing or propulsion system calibration require precise, uncontaminated gas delivery.
A practical example is a semiconductor fab using nitrogen to purge equipment. A Single-Stage Ultra-High Purity Line Gas Regulator ensures the gas is free of moisture or oxygen, preventing oxidation that could damage delicate wafers.
Benefits
The advantages of this regulator make it a standout choice for many applications:
Precision: While less stable than dual-stage models, it offers reliable pressure control for stable inlet conditions.
Purity: Its primary strength is maintaining gas cleanliness, critical for sensitive processes.
Cost-Effectiveness: Simpler than dual-stage regulators, it provides a budget-friendly option without sacrificing purity.
Simplicity: Fewer components mean easier maintenance and lower failure risk.
Reliability: Built for harsh environments, it delivers consistent performance over time.
These benefits make it ideal for users needing ultra-pure gas delivery without the complexity or cost of dual-stage systems.
Comparison with Other Regulators
To choose the right regulator, it’s helpful to compare the Single-Stage Ultra-High Purity Line Gas Regulator with alternatives:
Single-Stage vs. Dual-Stage: Dual-stage regulators reduce pressure in two steps, offering superior stability when inlet pressure varies (e.g., as a cylinder empties). However, they’re more complex and costly. Single-stage models suffice when inlet pressure is consistent.
Ultra-High Purity vs. Standard Regulators: Standard regulators work for less demanding tasks, like welding, where purity isn’t critical. Ultra-high purity models are mandatory for applications requiring contaminant-free gas.
This regulator is best for scenarios prioritizing purity over extreme pressure stability, such as short-duration processes or stable gas supplies.
Maintenance and Safety
Maintaining a Single-Stage Ultra-High Purity Line Gas Regulator ensures its longevity and performance. Key practices include:
Inspection: Regularly check for leaks (using leak detection fluid), worn seals, or diaphragm damage.
Cleaning: Periodic cleaning in a cleanroom removes contaminants, preserving purity.
Calibration: Verify the regulator delivers the set pressure accurately.
Safety is critical when handling high-pressure gases:
PPE: Wear safety glasses and gloves.
Ventilation: Ensure proper airflow, especially with toxic or flammable gases.
Lockout/Tagout: Isolate the system during maintenance.
Common issues include leaks (from loose fittings) or pressure creep (from a damaged seat), both fixable with proper troubleshooting.
Case Studies
Semiconductor Fab: A chip manufacturer faced high defect rates due to moisture in nitrogen gas. Switching to a Single-Stage Ultra-High Purity Line Gas Regulator with enhanced sealing reduced moisture levels, cutting defects and saving millions.
Pharmaceutical Lab: During API synthesis, trace impurities in oxygen gas threatened product safety. An ultra-high purity regulator ensured compliance with purity standards, safeguarding the process.
These examples highlight the regulator’s real-world impact on quality and efficiency.
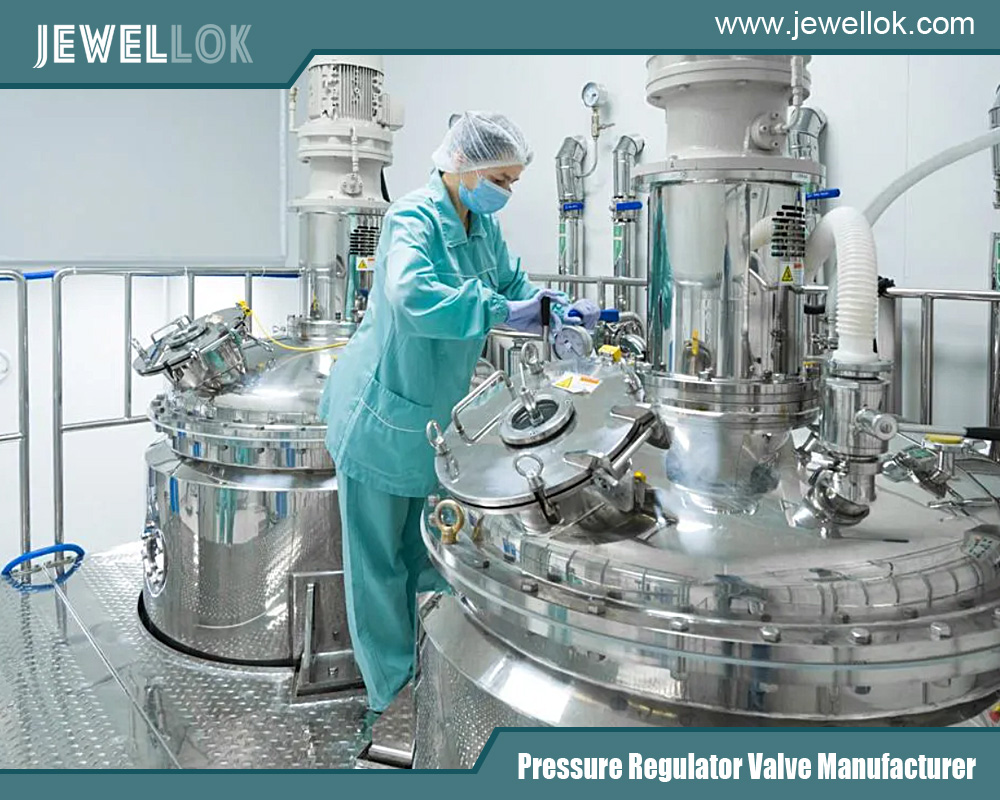
Conclusion
The Single-Stage Ultra-High Purity Line Gas Regulator is a cornerstone of industries requiring precise, contaminant-free gas delivery. Its simplicity, cost-effectiveness, and purity-focused design make it invaluable for applications from semiconductor fabs to research labs. While it may lack the pressure stability of dual-stage models, its reliability and performance in stable conditions are unmatched for the price. As industries demand ever-higher standards, this regulator will remain a key player, with future innovations likely enhancing its capabilities through smarter materials and technology.
For more about the single-stage ultra-high purity line gas regulator from natural gas regulator manufacturer, you can pay a visit to Jewellok at https://www.jewellok.com/product-category/ultra-high-purity-regulators/ for more info.
Recent Posts
What Is A High Purity Gas Regulator?
What Is An Integrated Gas Supply System?
Stainless Steel Diaphragm Valve Manufacturer
Tags
Recommended Products
-
Stainless Steel Ultra High Purity (UHP) High Pressure Manual Diaphragm Valve
-
T-BOX JW-TB-C Special Gas Delivery System Gas Valve Manifold Boxes
-
High Purity High Flow Pressure Control Regulators & Valves Gas Stick Assemblies JSR-2TG Series
-
Fully Automated Gas Cabinet Gas Rack Gas Delivery Systems JW-300-GR
-
767LT Reducer Pressure Reducing Valve Adjustment High purity Pressure Reducing Union Fittings And Tubing
-
Semi Automatic Gas Cabinet Gas Panels High Purity Gas Delivery Systems JW-200-GC
-
765L Stainless Steel Union Elbow Reducing High Purity Fitting Tubing Extension Tubing Connection
-
Manual Gas Rack High Purity Gas Delivery Systems JW-100-GR