Blog
Jewellok is a professional pressure regulator and valve manufacturer and supplier.
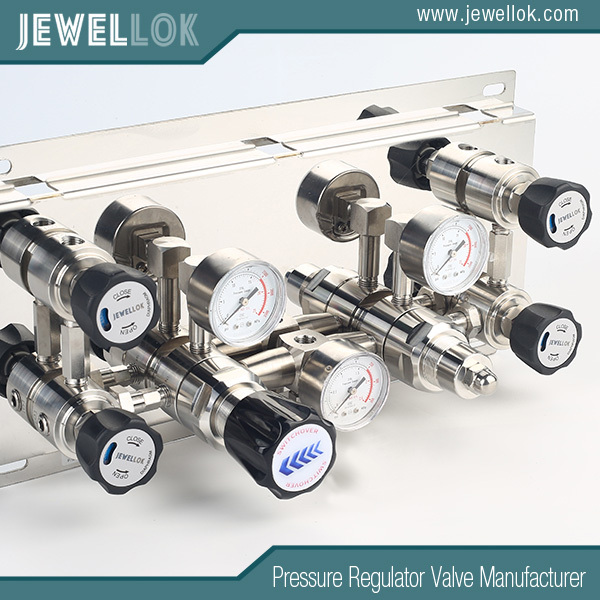
Ultra High Purity Diaphragm Valves: Guardians of Hygiene in Pharmaceutical Aseptic Production
- Pressure Regulator Valve Manufacturer
- 1inch of water, 2 inch irrigation valve, 6mm compression fitting, air compressor non return valve, argon hose connector, argon hose fittings, electric water valve 12v, ferrule connector, fire arrestor, gas semiconductor, high purity regulators, high purity valves, how a pressure regulator works, how do regulators work, how often should pressure relief valves be replaced, humming propane regulator, laboratory gas valves, male fitting for argon hose, pressure regulator valve leaking, propane adjustable pressure regulator, purpose of flame arrester, regulator valve alibaba international market, relief valve safety valve difference, safety relief valve vs safety valve, safety valve vs pressure relief valve, timed water valve, two stage pressure regulator, ultra high purity diaphragm valve, ultra high purity diaphragm valve manufacturer, Ultra High Purity Diaphragm Valves, ultra high purity diaphragm valves supplier
- No Comments
Ultra High Purity Diaphragm Valves: Guardians of Hygiene in Pharmaceutical Aseptic Production
In the aseptic production process of the pharmaceutical industry, the quality and safety of drugs are of vital importance. Any slight contamination may lead to serious consequences. Ultra high purity diaphragm valves, as key fluid control devices, play an indispensable role in ensuring the aseptic environment of production and the quality of drugs. This article will delve into how ultra high purity diaphragm valves meet the strict hygiene requirements of the pharmaceutical industry.
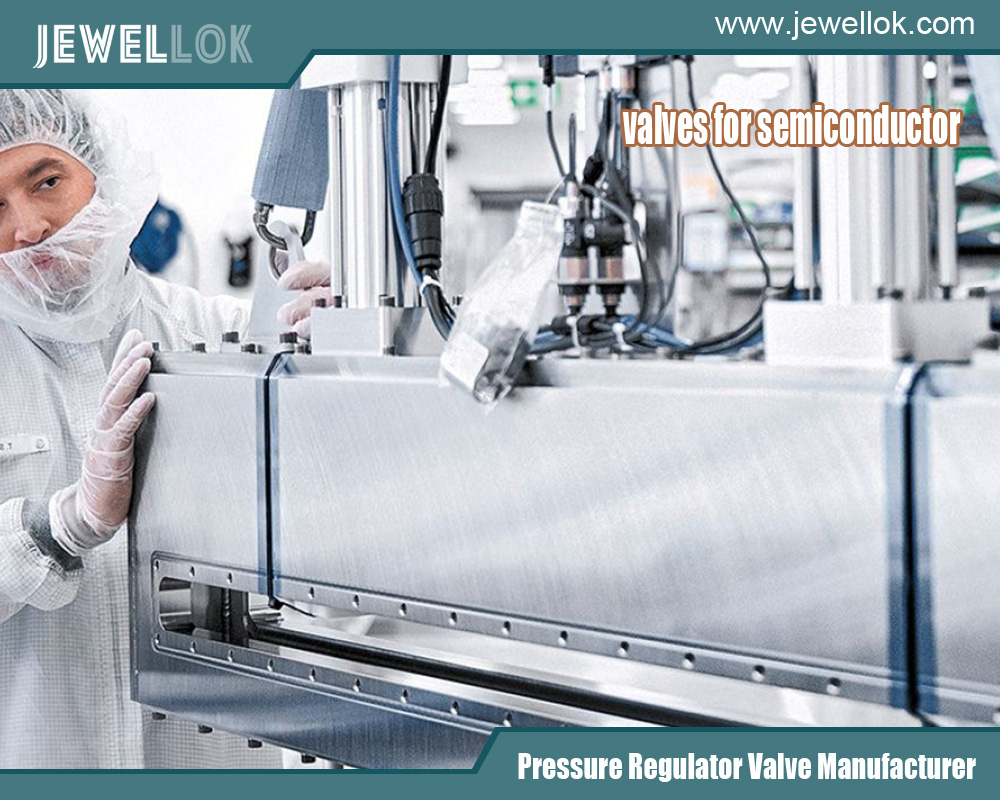
Material Selection – Laying the Foundation for Hygiene
The selection of materials for ultra high purity diaphragm valves is the primary key to meeting hygiene requirements. The valve body is usually made of 316L VIM – VAR stainless steel. The molybdenum element contained in this material enhances its resistance to corrosive media such as chloride ions, and it has excellent corrosion resistance. It can remain stable in complex environments commonly found in pharmaceutical production, such as humid and acidic or alkaline conditions. At the same time, it complies with the strict hygiene standards of industries such as food and pharmaceuticals. The surface can be polished with high precision, resulting in an extremely low roughness. There are no gaps, weld spots, or grooves where impurities and bacteria can adhere, eliminating the risk of contamination from the source.
The diaphragm, as the core component of the ultra high purity diaphragm valve, also requires careful material selection. Common materials include food-grade rubber and polytetrafluoroethylene (PTFE). Food-grade rubber has good elasticity and sealing performance, which can effectively isolate the medium. It is non-toxic and harmless and will not contaminate the drugs. PTFE has excellent chemical stability, low friction coefficient, and corrosion resistance, making it suitable for various complex medium environments. Even during long-term use, it can maintain stable performance, ensuring that the medium is effectively isolated from other parts of the valve body and preventing contamination.
Design Structure – Eliminating Hygiene Dead Zones
The design structure of ultra high purity diaphragm valves takes into full account the hygiene requirements and adopts unique designs to avoid the occurrence of hygiene dead zones. Its flow channel is designed as a straight-through type. This design not only reduces the fluid resistance but, more importantly, avoids the accumulation of sediments. The fluid can flow smoothly within the valve body without forming stagnant areas in the pipeline, thereby reducing the possibility of microbial growth and impurity adhesion.
The sealing structure of the valve is also a key point of the design. Ultra high purity diaphragm valves achieve sealing by the tight fit between the diaphragm and the valve seat. In the closed state, the diaphragm can be tightly pressed against the valve seat, forming a tight sealing barrier that effectively prevents fluid leakage. The elastic material of the diaphragm ensures that it can still maintain good sealing performance under frequent opening and closing operations and different pressure and temperature conditions, preventing external contaminants from entering the pipeline system and avoiding the pollution of the production environment caused by the leakage of internal media. In addition, the connection part between the valve stem and the diaphragm is specially designed to reduce friction and wear, further ensuring the reliability of the seal and avoiding the risk of contamination caused by component damage.
Cleaning and Disinfection – Maintaining an Aseptic State
In the aseptic production of pharmaceuticals, regular cleaning and disinfection are necessary measures to ensure the hygiene of the production environment and equipment. Ultra high purity diaphragm valves have good adaptability in this regard. Their simple structure and easy disassembly and assembly make it convenient for quick cleaning or replacement of the diaphragm, which greatly reduces the system downtime and improves production efficiency. During the cleaning process, each component of the valve can be disassembled, and special cleaning agents, compressed air, or clean water can be used for a comprehensive and in-depth cleaning to ensure the removal of surface dirt, residual materials, and possible microorganisms. For difficult-to-clean parts, such as the sealing surfaces of the valve seat and the diaphragm, special cleaning tools and methods can be adopted to ensure that there are no hygiene dead zones.
In terms of disinfection, the materials of ultra high purity diaphragm valves can withstand a variety of disinfection methods, such as steam-in-place (SIP) and clean-in-place (CIP). The 316L stainless steel valve body and the corrosion-resistant diaphragm material will not deform, corrode, or release harmful substances under the action of high temperature and chemical reagents and can maintain stable performance. During steam disinfection, the valve can withstand the impact of high-temperature steam to kill possible microorganisms. During chemical disinfection, the diaphragm and the valve body will not react chemically with the disinfectant, ensuring the effectiveness and safety of the disinfection process and thus maintaining the aseptic state of the entire production system.
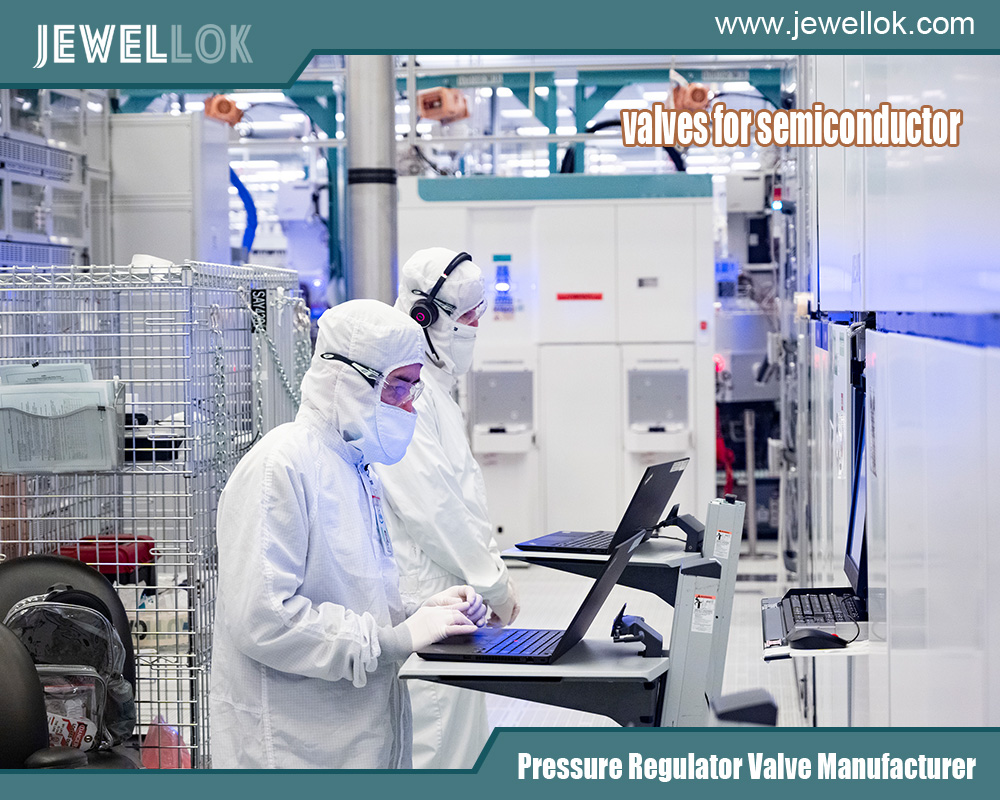
Regulatory Compliance – Strictly Adhering to the Quality Bottom Line
The pharmaceutical industry is strictly regulated by relevant laws and regulations. Ultra high purity diaphragm valves must comply with relevant regulatory standards, such as the Good Manufacturing Practice (GMP) and the requirements of the US Food and Drug Administration (FDA). These regulations have made detailed provisions on various aspects of valve selection, design, materials, cleaning validation, etc., for pharmaceutical water systems. During the design, manufacturing, installation, and use of ultra high purity diaphragm valves, these regulatory standards are strictly followed to ensure the quality and safety of drug production from all aspects. For example, in the selection of materials, it must meet the requirements of the regulations for materials in contact with drugs. In terms of cleaning validation, detailed validation reports need to be provided to prove that the valve can meet the specified hygiene standards after cleaning, thereby meeting the strict requirements of the pharmaceutical industry for product quality and safety and providing a reliable guarantee for pharmaceutical production.
Ultra high purity diaphragm valves, with their excellent performance in material selection, design structure, cleaning and disinfection, and regulatory compliance, perfectly meet the strict hygiene requirements in the aseptic production process of the pharmaceutical industry. They are key devices for ensuring the quality and safety of drugs, playing an irreplaceable and important role in pharmaceutical production, safeguarding the health of patients, and promoting the high-quality development of the pharmaceutical industry.
For more about ultra high purity diaphragm valves: guardians of hygiene in pharmaceutical aseptic production, you can pay a visit to Jewellok at https://www.jewellok.com/ for more info.
Recent Posts
Pneumatic Pressure Control Valve Manufacturers in the UK
How To Choose The Right Stainless Steel Needle Valve
The Applications, Principles and Types of Water Solenoid Valve
Tags
Recommended Products
-
High Purity High Flow Pressure Control Regulators & Valves Gas Stick Assemblies JSR-2TG Series
-
JR1000 Series UHP Ultra High Purity Single Stage Pressure Reducing Regulator And Low To Intermediate Flow
-
770L Female Elbow | Stainless Steel High Purity Weld Fittings Female Micro Elbow Fittings
-
Semi Automatic Gas Changeover Manifold System Manual Changeover Manifold Panel Single Stage Automatic Switchover Board
-
765L Stainless Steel Union Elbow Reducing High Purity Fitting Tubing Extension Tubing Connection
-
Stainless Steel Ultra High Purity (UHP) High Pressure Manual Diaphragm Valve
-
Ultra High Purity Stainless Steel Compressed Gas Changeover Manifold Panel System For Integrated Gas Supply System
-
High Pressure High-Purity Welded Check Valves And Low Cracking Pressure Check Valve JCV1 Series