Blog
Jewellok is a professional pressure regulator and valve manufacturer and supplier.

What Are Ultra High Purity Gas Delivery Systems?
- Pressure Regulator Valve Manufacturer
- function of flow control valve in hydraulic system, Gas Delivery Cabinet Systems, gas delivery system in semiconductor, High Purity Gas Delivery Equipment, high purity gas delivery systems, high purity systems, Semiconductor fluid control systems, Semiconductor Fluid Control Systems And Components, ultra high purity gas delivery system, Ultra High Purity Gas Delivery System Manufacturer, Ultra High Purity Gas Delivery Systems in USA, Ultra High Purity Gas Delivery Systems Malaysia, Ultra high purity gas pipeline
- No Comments
What Are Ultra High Purity Gas Delivery Systems?
Introduction
In the realm of modern industry, where precision and quality are paramount, ultra high purity gas delivery systems play an indispensable role. These sophisticated systems are designed to transport gases—such as nitrogen, oxygen, hydrogen, and various specialty gases—with purity levels often exceeding 99.999%, ensuring that even the slightest impurities do not compromise critical processes. The evolution of these systems has been driven by technological advancements, particularly in industries like semiconductor manufacturing, where shrinking feature sizes on microchips have demanded increasingly stringent purity standards. Today, ultra high purity gas delivery systems are vital across multiple sectors, including pharmaceuticals, aerospace, research laboratories, and even food and beverage production.
The significance of these systems lies in their ability to maintain gas integrity from the source to the point of use. In semiconductor fabrication, for instance, impurities can lead to defects in microchips, resulting in substantial financial losses. In pharmaceuticals, the purity of gases used in production can directly affect the safety and efficacy of medications. This article explores the components, design considerations, applications, challenges, and future trends of ultra high purity gas delivery systems, providing a comprehensive overview of their role in modern industry.
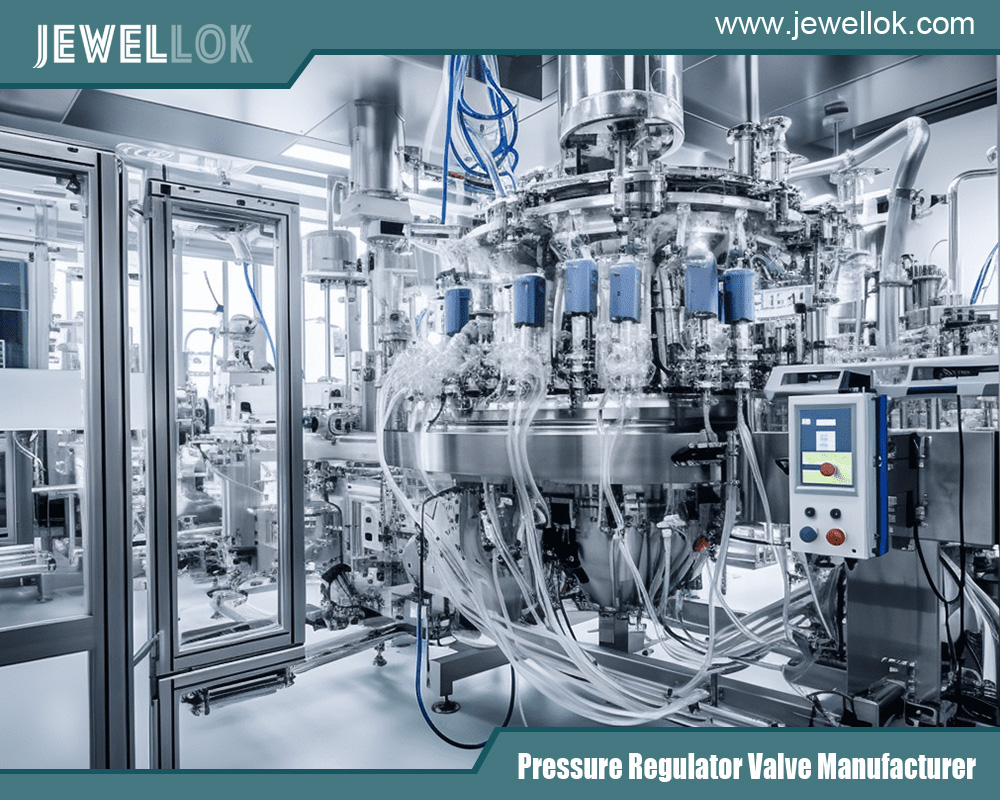
Components of Ultra High Purity Gas Delivery Systems
Ultra high purity gas delivery systems are composed of several key components, each meticulously engineered to preserve gas purity:
Gas Source: The system begins with the gas source, which can be high-purity gas cylinders, bulk storage tanks, or on-site gas generators. The choice depends on the volume required and the facility’s specific needs. For example, nitrogen might be generated on-site in large semiconductor plants, while specialty gases like silane are typically supplied in cylinders.
Regulators: These devices control the pressure of the gas as it moves from the source to the application. In ultra high purity systems, regulators are constructed with metal-to-metal seals and materials that prevent outgassing, ensuring no contaminants are introduced.
Valves: Various valves—shut-off, check, and relief—manage gas flow and enhance safety. Shut-off valves isolate sections for maintenance, check valves prevent backflow, and relief valves protect against overpressure. These must be made from inert materials to avoid contamination.
Tubing and Piping: The conduits for gas transport are typically made of stainless steel, often electropolished to a smooth finish to minimize particle entrapment. For highly reactive gases, specialized materials like Hastelloy may be used to enhance compatibility and purity.
Filters: Integrated into the system, filters remove particulates as small as 0.003 microns, depending on the application’s requirements. This ensures the gas stream remains free of solid contaminants.
Purifiers: Beyond filtration, purifiers eliminate trace gases or moisture that could compromise purity. For instance, a purifier might remove residual oxygen or water vapor from nitrogen before it reaches a semiconductor cleanroom.
Monitoring Equipment: Sensors and analyzers, such as oxygen analyzers, moisture detectors, and particle counters, continuously monitor gas quality. These instruments provide real-time data, enabling immediate corrective action if purity levels falter.
Each component is critical to the system’s overall performance, working together to deliver gas that meets exacting standards.
Design Considerations
Designing an ultra high purity gas delivery system requires careful attention to several factors to ensure gas purity is maintained:
Leak-Tightness: The system must be impervious to leaks, as even microscopic breaches can introduce atmospheric contaminants like oxygen or moisture. All connections, welds, and seals are rigorously tested to ensure integrity.
Material Selection: Materials must be inert and compatible with the gas being delivered. Stainless steel is a common choice, but for corrosive gases, alloys like Monel or Hastelloy may be necessary to prevent reactions that could introduce impurities.
Minimizing Dead Volumes: Areas where gas can stagnate—known as dead volumes—must be minimized. Smooth flow paths and the avoidance of unnecessary bends or pockets reduce the risk of contamination over time.
Pressure and Flow Compatibility: The system must deliver gas at the correct pressure and flow rate for the application, avoiding turbulence or pressure drops that could affect purity. This requires appropriately sized tubing and components.
Ease of Maintenance: Accessibility for replacing filters, calibrating sensors, and conducting repairs is essential. A well-designed system balances purity requirements with operational practicality.
These considerations ensure that the system performs reliably under the demanding conditions of high-purity applications.
Applications
Ultra high purity gas delivery systems are employed across a diverse range of industries, each with unique purity demands:
Semiconductor Manufacturing: In this sector, gases like nitrogen are used in photolithography to prevent oxidation, while hydrogen is employed in annealing processes to enhance crystal structures. Silane and ammonia, delivered at ultra high purity, are critical for chemical vapor deposition (CVD), where impurities can cause pinholes or contamination in thin films.
Pharmaceuticals: Nitrogen is used for blanketing to protect sensitive drugs from oxidation, while ultra high purity oxygen supports fermentation processes in bioreactor systems. In lyophilization (freeze-drying), nitrogen maintains a controlled environment to preserve product stability.
Aerospace: Ultra high purity argon is used in welding titanium components, such as turbine blades, to prevent oxidation and ensure weld integrity. High-purity gases also support the curing of composite materials in aerospace manufacturing.
Research Laboratories: In materials science, ultra high purity gases enable the synthesis of nanomaterials, where even trace impurities can alter properties. Chemistry labs use these systems for experiments requiring precise control over reaction conditions.
Food and Beverage: Carbon dioxide for beverage carbonation must be free of impurities to avoid off-flavors, while nitrogen in modified atmosphere packaging displaces oxygen to extend shelf life without introducing contaminants.
These applications demonstrate the versatility and critical importance of ultra high purity gas delivery systems.
Challenges in Maintaining Ultra High Purity
Despite their advanced design, these systems face several challenges:
Leak Prevention: The smallest leak can compromise purity, requiring regular testing with sensitive detectors like helium leak testers. High-quality seals and meticulous installation are essential.
Cost: The specialized materials, components, and maintenance requirements make these systems expensive. Filters, purifiers, and monitoring equipment add to operational costs, posing a challenge for budget-conscious facilities.
Maintenance: Servicing requires downtime, which can disrupt production. Personnel must be trained to avoid introducing contaminants during maintenance, adding complexity to operations.
Gas Source Purity: If the initial gas supply is substandard, the entire system is compromised. Sourcing from reputable suppliers and verifying purity upon delivery are critical steps.
These challenges highlight the need for rigorous design, operation, and oversight to maintain ultra high purity standards.
Case Study: Semiconductor Fabrication Plant
Consider a semiconductor fabrication plant as a practical example. The gas delivery system begins with a storage area containing high-purity nitrogen cylinders and an on-site generator for large-scale use. Electropolished stainless steel tubing transports the gas to cleanroom stations.
Pressure regulators adjust the gas to process-specific levels, while filters remove particulates. For critical applications like CVD, purifiers eliminate trace moisture or oxygen. At the point of use, a manifold controls flow rates, and oxygen and moisture analyzers monitor purity in real time, alerting operators to any deviations.
This setup ensures that gases meet the stringent requirements of semiconductor manufacturing, minimizing defects and maximizing yield.
Future Trends and Advancements
The field of ultra high purity gas delivery systems is evolving with technological advancements:
Enhanced Monitoring: New sensor technologies detect impurities at lower concentrations, improving system reliability.
Advanced Materials: Innovations in materials science are producing tubing and components with superior inertness and reduced outgassing.
Sustainability: Efforts to reduce gas waste and integrate renewable energy into gas generation are gaining traction, enhancing environmental performance.
Smart Systems: The integration of IoT enables remote monitoring, predictive maintenance, and data-driven optimization, ushering in a new era of efficiency.
These trends promise to make ultra high purity gas delivery systems more effective and sustainable.
Best Practices for Operation and Maintenance
To optimize performance, consider these best practices:
Regular Leak Testing: Use helium detectors to identify leaks promptly.
Filter Replacement: Follow a schedule based on usage to maintain purity.
Sensor Calibration: Regularly calibrate monitoring equipment for accuracy.
Cylinder Handling: Purge systems and use clean tools when changing cylinders.
Training: Educate personnel on purity protocols.
Record-Keeping: Document maintenance and purity tests for performance tracking.
These practices ensure long-term reliability and effectiveness.
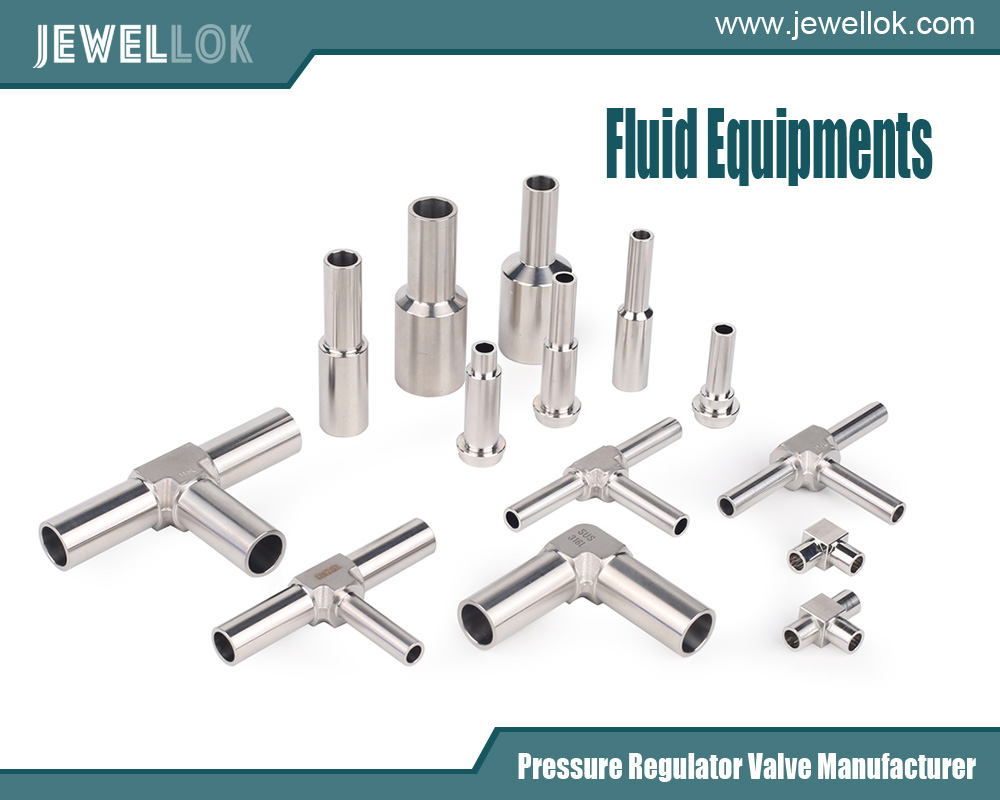
Conclusion
Ultra high purity gas delivery systems are critical enablers of modern industry, supporting processes where purity is non-negotiable. By understanding their components, design, applications, and challenges, stakeholders can harness their full potential. As innovations continue to emerge, these systems will remain at the forefront of technological progress, driving quality and efficiency across diverse sectors.
For more about what are ultra high purity gas delivery systems, you can pay a visit to Jewellok at https://www.jewellok.com/ for more info.
Recent Posts
Tags
Recommended Products
-
771LF Female Run Tee | Stainless Steel Tube Fitting Compression Fittings 1/4 In 3-Way Tee Female Run Tee
-
JF Series In-Line Gas Filters | High Purity High Precision High Flow Semiconductor Gas Filter Gas Filtration & Purification
-
Specialty Gas Valves Ultra High Purity Gas Valves Ultra High Purity Gas Cylinder Valves UHP Cylinder Valve Ultra High Purity Gas Regulator
-
Stainless Steel Ultra High Purity (UHP) High Pressure Manual Diaphragm Valve
-
Flow Control Stainless Steel Low Pressure Manual Diaphragm Valve For High Purity And Ultra High Purity Gases
-
DPR1 Ultra High Purity Two Stage Dual Stage Pressure Reducing Regulator Semiconductor Grade Regulators
-
765L Stainless Steel Union Elbow Reducing High Purity Fitting Tubing Extension Tubing Connection
-
Ultra High Purity Oxygen Pressure Gauge For Semiconductor Gases JG Series Pressure Instruments For Semiconductor Manufacturing